
Prevention of employee injuries should be a primary goal of all employers. One fundamental aspect of employee safety is guarding moving parts on machinery. Injuries related to a lack of machine guarding usually are severe and result in amputations or similar serious injuries. The manufacturing, recycling and food industries all share the need to have appropriate machine guards in place to adequately protect workers.
The Occupational Safety and Health Administration (OSHA) has a standard for machine guarding: 1910.212. This OSHA standard states that moving parts on machinery must be guarded from accidental contact from “over, around or under.”
Common types of guarding
A variety of guarding types are available:
- barrier guards – These are the most common types of guards, providing a physical barrier around moving parts to prevent accidental contact.
- distance guarding – This is a guarding method that usually uses a barrier to prevent employee access to a general area where moving parts are present.
- light curtains – A more sophisticated method of guarding, they electronically shut down the equipment if an employee or other object breaks the plane of protection near the point of operation.
- pullback devices or restraining straps – These are typically used for punch press and press brake machines. This type of protection relies heavily on proper setup and use by employees, so it is considered by most to be the least favorable method of protection.
- machine function guarding – This type of guarding consists of machine functionality, such as two hand controls, foot treadle operation and other methods that prevent an employee from inserting hands or body parts into danger zones during machine operation.
A machine guarding program
Any company that has equipment requiring guarding should have an effective machine guarding program. This program should consist of a variety of components:
- initial assessment – Each piece of equipment should be formally inspected for proper machine guarding and related safeguarding. Any pieces noted to have exposed parts or outdated guarding methods would be upgraded or otherwise safeguarded.
- employee training – Employees require specific training about how to identify proper (or improper) machine guarding. Rules related to disabling machine safeguards, reporting unsafe conditions and other similar topics should be covered in this training. Lockout training also is required for those performing lockout procedures and employees working near that equipment.
- on-going inspections of guarding – Virtually every manufacturing, recycling or food facility is required by OSHA to have frequent and regular inspections. Machine guarding should be part of that inspection process. Several pieces of equipment that use an emergency stop function as part of the machine safety should be tested at the beginning of each shift.
A common mistake many employers make is assuming that new equipment they purchased for their facilities will have the necessary machine guarding that meets all of OSHA’s requirements. Don’t make this mistake! Proactive employers keep machine guarding as a regular safety focus item and, as a result, have a safer workplace as well as a stronger safety culture.
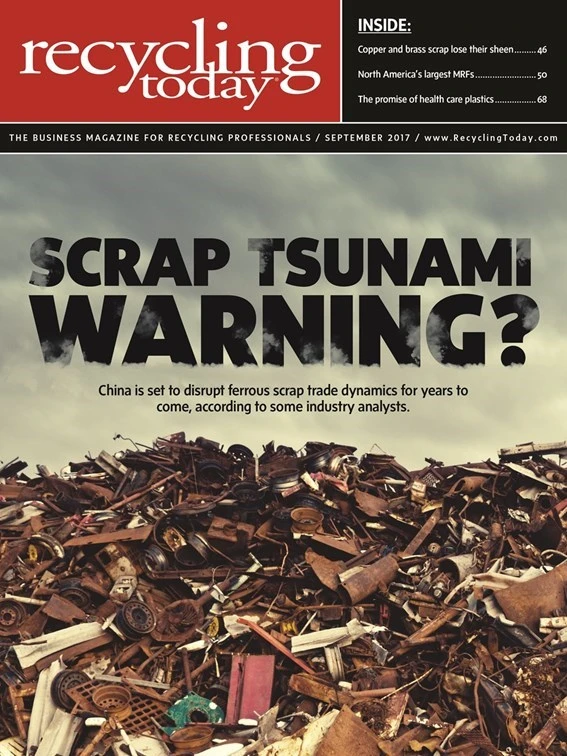
Explore the September 2017 Issue
Check out more from this issue and find your next story to read.
Latest from Recycling Today
- Athens Services terminates contract with San Marino, California
- Partners develop specialty response vehicles for LIB fires
- Sonoco cites OCC shortage for price hike in Europe
- British Steel mill’s future up in the air
- Tomra applies GAINnext AI technology to upgrade wrought aluminum scrap
- Redwood Materials partners with Isuzu Commercial Truck
- The push for more supply
- ReMA PSI Chapter adds 7 members