
In late 2020, computer peripherals manufacturer Logitech International announced its plans to use postconsumer resin (PCR) in more than 50 percent of its mice and keyboards by the end of this year. The company also pledged to provide full transparency regarding the carbon value of its products and its use of PCR by using third-party validation.
Logitech, with headquarters in Newark, California, and Lausanne, Switzerland, has focused on increasing PCR in its popular product lines as part of its design for sustainability efforts since 2017. Its K120 and K400 keyboards, C390 webcam, M100 and M190 mice and the UE Hyperboom speakers are among the products that incorporate PCR. The company’s ERGO M575 mouse started with a design goal of maximizing PCR in the black, graphite and off-white models. It also is Logitech’s first product to have its PCR content validated by an independent third party.
In late 2020 when the company announced its expanded use of PCR, Prakash Arunkundrum, global head of operations and sustainability at Logitech, said, “Since plastic is one of the most-used materials at Logitech, we’re investing in the circular economy by recycling and reusing consumer products to push the limits of what is currently possible for recycled plastic.”
Engineered solutions
“What we did is take an uncompromising approach,” says Robert O’Mahony, head of sustainability, global operations, at Logitech regarding the company’s use of PCR. He says Logitech worked with its PCR suppliers to engineer a virgin plastic replacement that would offer a drop-in solution. “Default, off-the-shelf PCR is not a drop-in replacement.”
He says the company sought to create PCR that offers integrity and repeatability. “It took time and a lot of effort. We did it on a partnership basis.”

Logitech kept its performance specifications at the forefront during this process, O’Mahony says. “We honed the supply chain to allow us to get the grade of PCR we needed to compound.
“We will not compromise around the user experience. It’s taken some time to get where we are, but we’ve figured it out for the most part,” he adds.
Logitech also consolidated its color palette to maximize its PCR use. “Initially, we said we would focus on a limited palette to help us understand our capabilities. We are now broadening that palette” to include pinks and whites in addition to black and gray, O’Mahony says.
According to its website, Logitech has developed 12 colors using PCR, with more coming soon. These colors and resins also are available to other companies in an effort to reduce the industry’s carbon impact.
Among the resins Logitech uses are high-impact polystyrene (HIPS), polycarbonate (PC) and acrylonitrile butadiene styrene (ABS). O’Mahony says recycled ABS has been the easiest of the plastics to work with and represents the majority of the company’s PCR use. Logitech devices made with ABS contain as much as 85 percent recycled content.
“HIPS and PC are more challenging; that is not to say that it’s not possible.”
O’Mahony adds, “As we continue to double down on the repeatability of our supply chain, it makes it easier to increase the percentage of PCR we are using. If we are using good raw material, we get a good final material.”
Logitech has a closed-loop recycling system in place at its factories. Additionally, the company has worked “hand in glove” with its resin suppliers, he says. O’Mahony says he has personally spoken with all of Logitech’s resin suppliers as well.
“We have our engineers doing the work on the ground at the molding machines until we get to the point that we get the grade we need.
“We couldn’t have made the progress we’ve made without that approach,” he adds.

The company’s “uncompromising rigor” has enabled Logitech to help its suppliers improve their PCR, which has led to better results at Logitech, O’Mahony says.
While Logitech had to modify its molding conditions to use PCR, he says using the material “hasn’t been a hindrance” and has not resulted in yield loss thanks to the “integrity” of its PCR supply.
The next step for the company is figuring out how it can use PCR to achieve different finishes and colors. “We are confident that we will,” he says.
Cut the carbon
Logitech is committed to increasing its use of PCR because the consumer technology industry uses significant volumes of plastic in its products. Such a change also will reduce the company’s overall carbon footprint, O’Mahony says.
By the end of 2021, Logitech says it will have shipped more than 50 million devices made with PCR. More than half of the mice and keyboards in its Creativity and Productivity portfolio, the company’s largest, will contain PCR. This will eliminate what Logitech estimates is 7,100 tons of virgin plastic and 11,000 tons of carbon annually.
The PCR used in Logitech products will range from 20 percent in its technically complex lighter colored products to 80 percent. Its suppliers must provide third-party certification for the PCR they provide, O’Mahony says. That information is available on the Logitech website at www.logitech.com/en-us/sustainability/post-consumer-recycled-plastic.html.
Emeryville, California-based SCS Global Services is providing the recycled-content verifications for Logitech’s products using mass-balance calculations.
Logitech’s transparency efforts also include committing to printing the carbon value of its products on their packaging across its portfolio. “Carbon is the new calorie,” O’Mahony says.

He adds that Logitech hopes that by offering this level of transparency, it can spur change within the electronics industry. “We’ve said from the outset that we are not using this as a competitive advantage but to activate the industry to do the right thing. We are using transparency to activate positive change.”
Logitech is committed to the Paris Agreement, he says, having pledged to cut its carbon footprint in half by 2030 to support the goal of limiting global warming to below 2 degrees Celsius. To this end, the company plans to use renewable electricity exclusively by 2030. O’Mahony says developing circular supply chains also will play an important role in achieving its carbon-reduction goal.
To assist with that effort, Logitech is designing for recyclability in part by reducing the number of resin types used in its products. “We are now designing differently. We have been for quite some time,” O’Mahony says.
According to Logitech’s sustainability report for its 2020 fiscal year, “Our goal is to design products that deliver great user experiences while minimizing our environmental footprint and enhancing our positive social handprint. For us, a truly sustainable design considers environmental and social impacts from the moment raw materials are sourced right through to end of life.”
The company adds, “We realize that the biggest opportunities to reduce environmental impact arise early in the design process, when key decisions about a product are made. So, we have integrated environmental impact assessment processes at the front end of product development.”
In addition to its use of recycled plastics, Logitech is working with external partners to develop a road map of sustainable materials for the future, as well as sustainable packaging advancements. The company promises ongoing innovation that will allow it to make lower impact electronic devices.
Logitech’s employees are excited about the progress the company has made in the area of PCR use, O’Mahony says. “It’s a catalyst for us to look elsewhere and do more. All our colleagues are fully bought into this.”
Get curated news on YOUR industry.
Enter your email to receive our newsletters.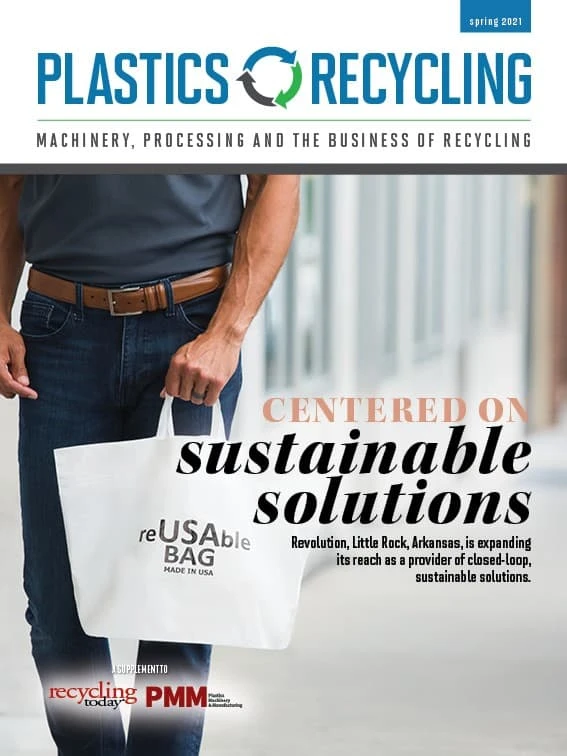
Explore the Spring 2021 Plastics Recycling Issue
Check out more from this issue and find your next story to read.
Latest from Recycling Today
- LumiCup offers single-use plastic alternative
- European project yields recycled-content ABS
- ICM to host colocated events in Shanghai
- Astera runs into NIMBY concerns in Colorado
- ReMA opposes European efforts seeking export restrictions for recyclables
- Fresh Perspective: Raj Bagaria
- Saica announces plans for second US site
- Update: Novelis produces first aluminum coil made fully from recycled end-of-life automotive scrap