Material handling is essential to C&D recycling and demolition applications. Whether sorting through debris on a demolition site, loading crushers and shredders or filling trucks with processed materials for transport, the goal is efficiency and productivity. But how can recyclers or demolition contractors be sure they’ve selected the right machinery for their unique operations?
|
With a few basic considerations in mind and a willingness to share the details of their operations with their equipment dealers, demolition contractors and C&D recyclers can be certain they’ve selected the proper combination of material handling equipment for their operations.
SIZING THINGS UP
Material type, size and density are among the primary considerations when selecting material handling equipment such as skid steers and wheel loaders.
"We start backwards from the material you’re handling and its density," says Doyle Long, senior work tool manager for Caterpillar Inc., Peoria, Ill. "What you have to get down to is how much material you have to move per bucket load. Then when you know material density, that gives you an idea of the size of bucket that you need."
"You want a bucket that is going to be able to load in two to four passes," Andrew Bonde, product marketing manager for John Deere Construction & Forestry Co., Moline, Ill., says. "Two is ideal. You don’t want to spend too much time loading."
ON GAURD |
On Guard Material handling machines destined for the C&D recycling and demolition markets are often equipped with guarding packages that serve to protect the machines and their operators from the harsh environments. "I think we as manufacturers are getting better at customizing guarding solutions for demolition customers," Andrew Bonde, product marketing manager for John Deere Construction & Forestry Co., Moline, Ill., says. "It can range from protecting the cooling package from airborne debris to providing cylinder guards so that the cylinders don’t get scored or damaged to providing guards around the glass portions of the cab to protect the operator." Bonde adds that John Deere has focused on providing guarding solutions that will fit the customer’s application, as some are more rigorous and demanding than others. David Morice, wheel loader product marketing manager for JCB Inc., Savannah, Ga., says belly plating, or heavily plating the underside of loaders, is popular within the demolition and recycling industries. "Depending on some applications, they might want to have what they call wire braiding on the hydraulic hoses that are exposed in the boom or bucket area," he adds. |
The bucket size then determines the size of the loader and its lifting capacity. "If you want to look at it very basically, a wheel loader is a teeter-totter, and the Society of Automotive Engineers has defined what percent of the tipping load of a loader you can use as a payload and still be considered safe." Long says.
"It’s good to understand the specs of the machine: The breakout force, the lift capacity, the maximum material density per cubic yard," David Wolf, marketing manager for Case Construction Equipment, Racine, Wis., says. "Those are all restrictions you need to understand.
"Most people have a good feel for what they need to have, for how much material they need to move. I’d say that’s the most important thing," Wolf continues. "But they also have to consider the application." Application constraints include dump height and the size of the job site or recycling yard.
Bonde adds that loaders have to be able to lift the required material density to the required height; therefore, the height of the vehicles used to transport the material should be taken into account, as should the height of the hoppers and conveyors on size-reduction equipment.
David Morice, wheel loader product marketing manager for JCB Inc., Savannah, Ga., says lift height requirements will help recyclers or demolition contractors determine whether they need a standard wheel loader or one with an extended boom option.
The same consideration applies when selecting skid steers. George Chaney, JCB’s compact equipment product marketing manager, says this is the second consideration for skid steer selection following the particulars relating to the materials handled. "If in fact they need to raise the material up to a certain height to dump or to discharge, the machine obviously has to clear the minimum height requirement. Also, sometimes there are height restrictions inside of buildings where too large of a machine might interfere with overhead water utilities, sprinkling systems, door jambs, etc.," Chaney says.
The space constraints of the recycling yard or demolition site also affect loader sizing. Compact loaders or skid steers may be more attractive to recyclers or demolition contractors working in tight spaces, while larger wheel loaders or excavators may be more suitable for those without space restrictions.
BANTAM-WEIGHT VERSATILITY
"The skid steer is notorious for maneuverability," Lance Schulz, loader product specialist for Bobcat, West Fargo, N.D., says. "The size of a machine offers so many advantages vs. other construction equipment."
"The first and foremost thing about skid steers is that they are maneuverable, and they are very versatile," Chaney says, adding that the machines provide high-duty cycle times and considerable output. He says that the C&D recycling and demolition industries welcome skid steers because of their versatility, productivity, speed and power. "They are quick, they are nimble, and they are also very powerful," he says.
Schulz says horsepower is important; however, it is not the sole indicator of a loader’s performance. Instead, he suggests considering a balanced system. "One metric worth investigating is a machine’s axle-torque rating." This rating is the direct measure of the power available at the wheels, Schulz says. "If axle torque is not adequate, it’s going to be difficult to be productive."
JCB identified that some attachments require more hydraulic flow or pressure than others in order to obtain optimum productivity, Chaney says. "That sometimes becomes the requirement that they try to satisfy. The primary requirement of the application, dictates what size, type or spec of machine they operate," he says.
The advent of quick-hitches also lends to the versatility of these compact material handlers, enabling operators to quickly change out attachments depending on the task.
"Skid steer loaders can be outfitted with countless tools, whether it’s buckets or forks or hammers or shears to be used in demolition applications," Neil LeBlanc of Caterpillar says. "The skid steer is basically a highly mobile tool carrier and a loader or processor of bulk materials."
Caterpillar’s Long adds, "There are places where you just can’t put an excavator or a wheel loader. If you need mobility, and you’ve got tight quarters, or if you need mobility and at a lower production rate than a wheel loader requires, then a skid steer is obviously a more efficient way to do it."
Skid steers are typically available with either a radial-lift or a vertical-lift (also known as parallel-lift) arm. Long explains that radial-lift arms swing through an arc, meaning that the arm has little forward reach when fully extended. Parallel- or vertical-lift arms, however, maintain forward reach by rotating the attachment forward as the arm rises.
Compact wheel loaders compete with skid steers for customers within these markets. Keith Rohrbacker, construction equipment product manager for Kubota Tractor Corp., Torrance, Calif., says some of the features that give compact wheel loaders an advantage are better visibility because the operator sits higher; maneuverability without surface damage; lower sound levels at the operator’s ear; and more comfort in part because of less vibration.
Wolf says, "If you’ve got the room and long load and carries, then I would say definitely go with the wheel loader. It’s going to be a little more comfortable for the operator. Ride control always helps: less wear and tear on the machine, less wear and tear on the operators."
ON THE MOVE
Wheel loaders are employed in C&D recycling and demolition applications because of their strength and mobility.
"If you have to carry over long distances, then a wheel loader is going to be more suitable for that," Wolf says. Excavators are better suited to situations where they can sit in one place and pick through material, thanks to their long reach. "But excavators are not very quick to move. I would say if you can get all the material within reach of an excavator, it’s going to be more efficient than a wheel loader. But if you have to carry a long distance, a wheel loader is going to be better," he adds.
Long agrees. "The rule of thumb that I apply is, if you can do it with an excavator without moving, then that’s a better tool. The exceptions would be when you’ve got to move or when you’ve got a space constraint," he says.
Adding a grapple or a bucket with a thumb to an excavator enables it to handle material of inconsistent size and type, while wheel loaders are most often used for handling bulk material of a consistent size.
LeBlanc says, "Generally I would use an excavator if I had bulk material that was long and stringy, because I’ve got a variety of different work tools or attachments that are best suited to pick up those long, stringy pieces, whereas the wheel loader, because of the fixed bucket, would not be best suited to do that."
Excavators are best suited to primary demolition and size reduction and to cleaning larger debris from sites, while wheel loaders are used for load and carry applications.
JCB’s Morice says, "The other advantage that excavators provide is that of having a high-rise cab for improved visibility. The advantage for wheel loaders is that of mobility and being able to move from place to place in a fairly quick amount of time. Productivity is better with a wheel loader when you are dealing with a very wide area.
"The demolition role for a wheel loader is more of a support role," Morice says. "Basically the role of the wheel loader is more in terms of clean up around the excavator and loading the material that has been cycled by the excavator."
Bonde also finds the wheel loader best suited to cleaning up demolition sites. "For the most part, I think wheel loaders have a purpose to serve in demolition. I haven’t seen any other product type or machine form come in and offer a better solution than a wheel loader can offer."
However, Long finds that the trend in the demolition industry is toward the excavator. "If you can set the job up to where you can use it, it’s just a more versatile tool than a wheel loader."
Versatility is key when selecting material handling equipment, Long says. "If they’ve got a broad cross section of material types and sizes, I would definitely recommend that they equip the loader with a coupler, so they can go back and forth between a couple of different bucket sizes or to a fork and top clamp."
Long continues, "We’re selling a very high percentage of our loaders with couplers on them today anyway, regardless of the application." The trend toward versatility is influencing manufactures. "It is much easier to get an operator to take advantage of the versatility if you make it easy for him to switch tools. On a wheel loader, if he has to pull a pin-on tool off and replace it with something else, he just won’t do it. It takes him an hour to get it done. You might even consider a multi-purpose bucket, one that you could grab things with."
Working with an equipment dealer or manufacturer can help recyclers and demolition contractors choose the right material handling equipment for their operations.
Long says, "Sit down with the equipment manufacturer and show him the job, show him what you are trying to do. Whether it’s a wheel loader or an excavator, you need to build as much versatility into it as you can," because of the variance among demolition jobs. "I would recommend couplers on both wheel loaders and excavators to give you the ability to switch tools when the job conditions change," he adds.
The author is assistant editor of C&D Recycler and can be contacted via e-mail at dtoto@cdrecycler.com.
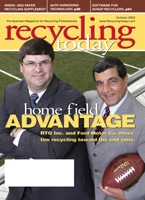
Explore the October 2003 Issue
Check out more from this issue and find your next story to read.
Latest from Recycling Today
- Nucor receives West Virginia funding assist
- Ferrous market ends 2024 in familiar rut
- Aqua Metals secures $1.5M loan, reports operational strides
- AF&PA urges veto of NY bill
- Aluminum Association includes recycling among 2025 policy priorities
- AISI applauds waterways spending bill
- Lux Research questions hydrogen’s transportation role
- Sonoco selling thermoformed, flexible packaging business to Toppan for $1.8B