
Scrap metal sorting is changing. As any recycler will report, traditional scrap metal sorting techniques are becoming outdated. At the same time, the volume of scrap received from a variety of sources has increased, fueling the demand for better tools to maximize scrap metal identification and profits. With fluctuating metals prices, precise scrap metal sorting is more important than ever and could mean the difference between reselling materials for dollars rather than cents on the pound.
Older generation metals identification instruments can be cumbersome and difficult to use in the typical yard environment. Hand-held analyzers are now the instrument of choice to meet the rigorous demands of modern scrap recycling. They can provide accurate alloy grade separations for fast identification. However, these instruments can be fragile and can have technological limitations that often result in a failure to rapidly identify all alloying elements, which can mean a missed opportunity for profit gain.
William F. Sullivan & Co. Inc., Holyoke, Massachusetts, a scrap metal recycler serving some of the area’s largest manufacturers, was looking for a way to improve the efficiency of its sorting process by reducing the time and costs associated with
Founded in 1953, Sullivan has made a business out of taking care of the environment by recycling scrap metal purchased from some of the area’s largest manufacturers as well as from individuals in and around New England. The company has created a business that focuses on providing customers with the fairest pricing for their scrap, in addition to offering the most effective options for handling scrap metal challenges.
Sullivan processes about 70,000 tons of material each year, 25 percent of which is nonferrous. To stay competitive, the company uses different hand-held analyzer technologies to identify
Overcoming the light-metal challenge
Sullivan has been using hand-held X-ray fluorescence (XRF) units for many years, typically for the analysis of nickel alloys, brasses and other metals made up of heavier elements. However, the company says it found a gap when using this technique to analyze lighter alloys, such as aluminum.
Sullivan discovered LIBS technology about two years ago and says it was pleased with how well it performed for light element analysis, particularly
Brian Powell, the company’s vice president, managed the implementation of the hand-held LIBS analyzer. Regarding the company’s initial reaction to this new technology, he says, “We have been very impressed with Rigaku’s LIBS capabilities of separating Al 6061 alloys from Al 5052, which can be very difficult to process so quickly. The speed of obtaining those results was something we had not previously experienced and, therefore, allowed us to sort specific alloys out so we’re not making a mixed package.”
Using the LIBS technology, Sullivan says it was able to upgrade the material it was preparing, increasing profitability on every pound.
The LIBS elemental analytical technique has the ability to detect and quantify the elemental composition of heavy and light elements in a solid, liquid or gas state.
LIBS is more sensitive and better suited to the detection of light elements, such as aluminum (Al), magnesium (Mg) and beryllium (Be). However, prior to 2015, LIBS analysis previously was confined to a laboratory environment. Recent technological advancements—such as miniature, solid-state microlasers
Because the KT-100 LIBS analyzer uses laser technology, there is no radiation exposure and minimal to no regulatory restrictions or registration and licensing fees.
Offering versatility and simplicity
Sullivan primarily uses the LIBS analyzer to sort aluminum alloys but also will use it to sort heavier metals when the company’s hand-held XRF unit is not available. “We know we can rely on the KT-100 for other alloys and it will do a consistent job, just like it does with the aluminum alloys,” Powell says.
The analyzer offers more than six hours of battery life and can hold more than 4,000 measurements. It includes a docking station cradle that charges the analyzer and a spare battery at the same time.
“It’s very quick and easy and is just right there, ready to go whenever you need it,” Powell says. Furthermore, the unit’s GPS and Wi-Fi capabilities allow for instrument tracking to protect the owner’s investment. Its

With an influx of various metals, Sullivan needed a tool that would be easy to introduce to any of its yard employees. Users have the ability to select which information is available on the results screen, and Powell determined what he would like to see—the spectra, the chemistry breakdown or just the alloy name.
Powell says he usually will have the instrument run in “Alloy Match” mode, so his workers do not need to make any determinations on their own. For more complicated metals, the company’s employees have the ability to view the
Another feature that appeals to the company is the keyboard, which consists of hard, raised buttons. This makes it easier for people who wear work gloves to operate compared with touch-screen devices.
In addition, the buttons of the KT-100 are assignable. “We can go right from the ‘Alloy Match’ result over to an in-depth alloy analysis that shows the element breakdown and then back again to the ‘Alloy Match’ very quickly,” Powell says of that feature.
Sponsored Content
Labor that Works
With 25 years of experience, Leadpoint delivers cost-effective workforce solutions tailored to your needs. We handle the recruiting, hiring, training, and onboarding to deliver stable, productive, and safety-focused teams. Our commitment to safety and quality ensures peace of mind with a reliable workforce that helps you achieve your goals.
Meeting the rigors of the scrap yard
The environment of a scrap metal processing facility is not ideal for analytical technology instruments. Therefore, any tool used to sort metal needs to be able to withstand the toughest use.
Another challenge Sullivan encountered when using the company’s hand-held XRF analyzer was that the analysis window would regularly jam when analyzing small pieces of scrap, such as turnings, and the instrument would need to be returned to the factory to be repaired. This resulted in downtime for the scrap company and associated costs.
To guarantee protection against all work environments, the KT-100 underwent strict testing to the United States Military Standard
In addition, its ingress protection (IP-54) rating and safety window composed of fused silica are designed to protect against dusty and wet environments.
“It’s very efficient [and] very
Get curated news on YOUR industry.
Enter your email to receive our newsletters.
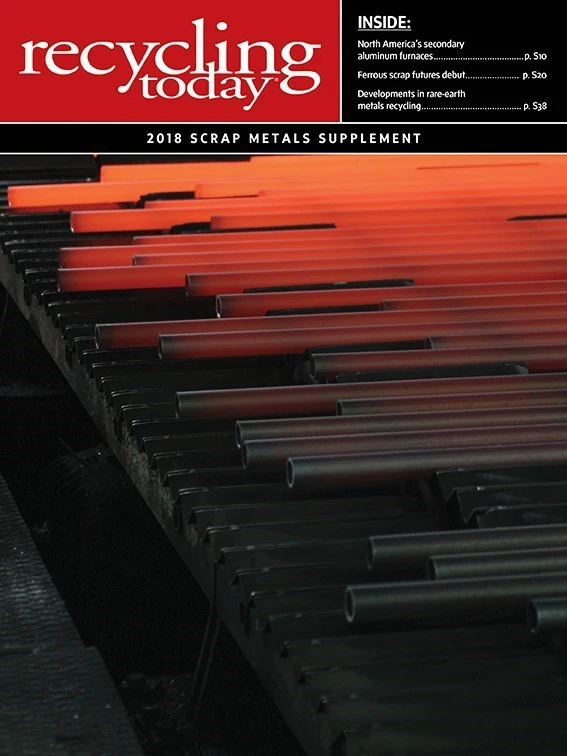
Explore the January 2018 Scrap Metals Supplement Issue
Check out more from this issue and find your next story to read.
Latest from Recycling Today
- Athens Services terminates contract with San Marino, California
- Partners develop specialty response vehicles for LIB fires
- Sonoco cites OCC shortage for price hike in Europe
- British Steel mill’s future up in the air
- Tomra applies GAINnext AI technology to upgrade wrought aluminum scrap
- Redwood Materials partners with Isuzu Commercial Truck
- The push for more supply
- ReMA PSI Chapter adds 7 members