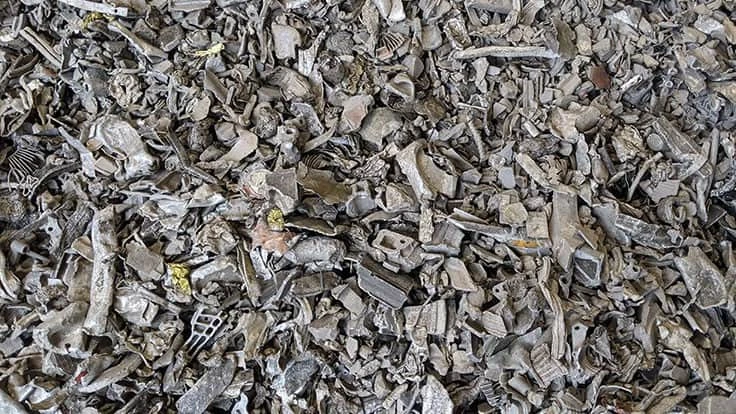
Photo courtesy of Levitated Metals

Ronak Shah, president of Levitated Metals, says his company may be something of a “one-trick pony,” but that singular focus is allowing Levitated Metals to meet its primary objective of supplying aluminum smelters with high-quality, low-magnesium twitch.
The company broke ground at its 10-acre site in New Caney, Texas, just outside Houston, in early 2020. While the original plan was to begin operating in September of last year, the pandemic delayed startup until earlier this year.
“Our supply partners worked tirelessly to ensure a safe and healthy startup,” Shah said in early April when the company announced that it had begun operating. “We navigated equipment supply chain disruptions and the difficulties of international travel for overseas technical experts.”
The heavy media plant operator purchases zorba and zorba fines from auto shredding operations and produces twitch (aluminum), zebra heavies (a mixture of brass, copper, zinc, nonmagnetic stainless steel and copper wire) and zeppelin (a mixture of magnesium and aluminum) that it is marketing to smelters and processors in the U.S., Mexico and overseas, the company says. Levitated will be able to produce 10 million pounds per month when operating at full scale, though Shah says, “We are not anywhere near that capacity today.”
He adds that the company is operating a single shift as it navigates the “growing pains” typical of a startup.
Operating at full scale will come with time and as the automotive industry rebounds from the semiconductor chip shortage, which is affecting demand for twitch, Shah says.
Going online

Aside from launching during the pandemic, Shah says Levitated faced other challenges. Some were unique to a new heavy media plant operation, while others likely are familiar to new companies more generally.
“It’s hard to start a business up from scratch,” Shah says. “Even getting the street address was more difficult than you might have thought. And then how do you get it on Google Maps so that every truck driver is not calling when they are trying to figure out how to get to you?”
As a new heavy media plant, Levitated also faced the challenge of securing supply, he says.
“Most zorba producers have been producing zorba and selling zorba for decades and decades and have a suite of consumers they consistently sell to,” Shah says. “To break into that takes work. In the space of taking trial loads and building a relationship, they are recognizing that we, Levitated, will pay on time [and] that we are going to be fair around the inevitable quality issues that might occur as sometimes we get a richer mix of zorba than we expected to receive and sometimes we get a mix of zorba that is not quite as good.”
He adds, “We make sure to work with them in a manner they are comfortable with to grow that relationship.”
While starting up any manufacturing business presents challenges, Shah says starting up and running a heavy media flotation plant is “especially challenging.” These operations are similar to wire chopping lines in that constant adjustments are necessary to produce the highest quality product, he says.
Levitated also is starting up at the same time its primary consumers are seeing demand for their products decrease related to the semiconductor shortage. “The standard consumers of twitch are buying far less of it now because demand for their finished product is far less as well.”
Strategically located
When Shah first decided to start Levitated in May of 2019, the market looked different than it does today. “At the time of the envisioning of Levitated Metals, there was enormous demand, and still is large demand, for aluminum twitch—for cast, recycled, direct-melt feedstock—in especially the Mexico market,” he says. “Relatively few players shipped high volumes of aluminum twitch into Mexico.”
Additionally, he says, twitch production in the U.S. has declined as some plants shut down and others produced less of the grade.
Levitated intends to address what Shah describes as the “discontinuity between supply and demand.”
The Houston area offered an ideal location for the company as it is close to suppliers and consumers and offers a busy container port and strong workforce, Shah said when construction on the facility was announced. Interstate Highway 10, I-45 and I-69 are main thoroughfares for aluminum shipments into the Southeast U.S.
“We are centrally located to a number of large auto shredders,” he told Recycling Today at that time, “and on the main thoroughfare that feeds the automotive industry in the Southeast with aluminum from Monterrey, Mexico.”
Levitated purchases zorba from as far away as Florida to the east, Kansas to the north and New Mexico to the west. Shah says, “We buy from relatively far away and are forever increasing that radius.”
The company says it picks up material in end-dumps, saving suppliers the additional expense of loading and transporting overseas containers.
Despite that flexibility, trucking still is presenting a challenge for Levitated and its suppliers and consumers. “It’s a complete mess,” Shah says. “Even in the last eight months that we’ve been buying material, we’ve been able to see the challenges of trucking get harder and harder both for inbound and outbound transportation.”
He adds that Levitated does a certain amount of inbound shipping using rail, which makes buying from farther away more viable. “But the majority of our material is brought in by truck.”
Levitated supplies twitch to consumers in Mexico but does not buy zorba from out of that country because Shah says transportation is not economical.
Levitated supplies its twitch to consumers in the United States and Mexico, with Shah noting that the Southeast U.S. and northern Mexico are home to dozens of melting operations.
Also uneconomical is supplying U.S. consumers outside of its region. “Our consuming base was always meant to be Mexico,” Shah says.
In addition to these North American markets, some of the twitch as well as the majority of the zebra the company produces are shipped to overseas consumers through the Port of Houston.

Prioritizing quality
In addition to Shah, the Levitated Metals executive team includes Director of Marketing David Burlison and Director of Operations Glenn Gunter. Prior to his role at Levitated, Burlison was a senior metals trader at Real Alloy. He also has worked for Custom Alloys in California and has been in the scrap industry for more than 25 years.
Shah says Gunter has been providing operations leadership at Levitated since the first piece of equipment was installed. He previously was operations manager for Upstate Shredding and general manager for SA Recycling’s Mobile, Alabama, facility, overseeing auto shredder operations.
“Every equipment design decision and operational choice is driven by our primary goal: to provide our customers the superior aluminum twitch that only a dual-stage heavy media flotation plant can generate,” Gunter said when Levitated announced that operations had started.
The company uses a dual-density heavy media flotation process to produce its end products, which means incoming material is separated in two stages, Shah says. In the first stage, the magnesium and low-value aluminum, such as Alucobond (an aluminum composite), are removed by using ferrosilicon or magnetite to create a water bath with a specific gravity in the range of 1.9. Magnesium is a contaminant to some cast aluminum alloy grades, and the media plant’s ability to remove it is one of its biggest advantages, Shah says.
“Recyclers buy that stuff,” he says of zeppelin, the mixture of aluminum and magnesium, “but they are not trying to buy it as a twitch product.”
The material that sinks in that first processing stage goes to a second stage that separates the aluminum alloys from the heavies. This water bath has a specific gravity of 3.2.
Shah says a final quality control process ensures the accuracy of the company’s sorting processes.
“We work really hard to try to make the best possible product for consumers to buy. We have been pretty successful in that we are supplanting material they had previously been buying.”
Shah continues, “We may be a one-trick pony, but we also are a team of really smart people focused exclusively on making the best product for our melting consumers. We are always trying to find ways to make it better.”
WANT MORE?
Enter your email to receive our newsletters.
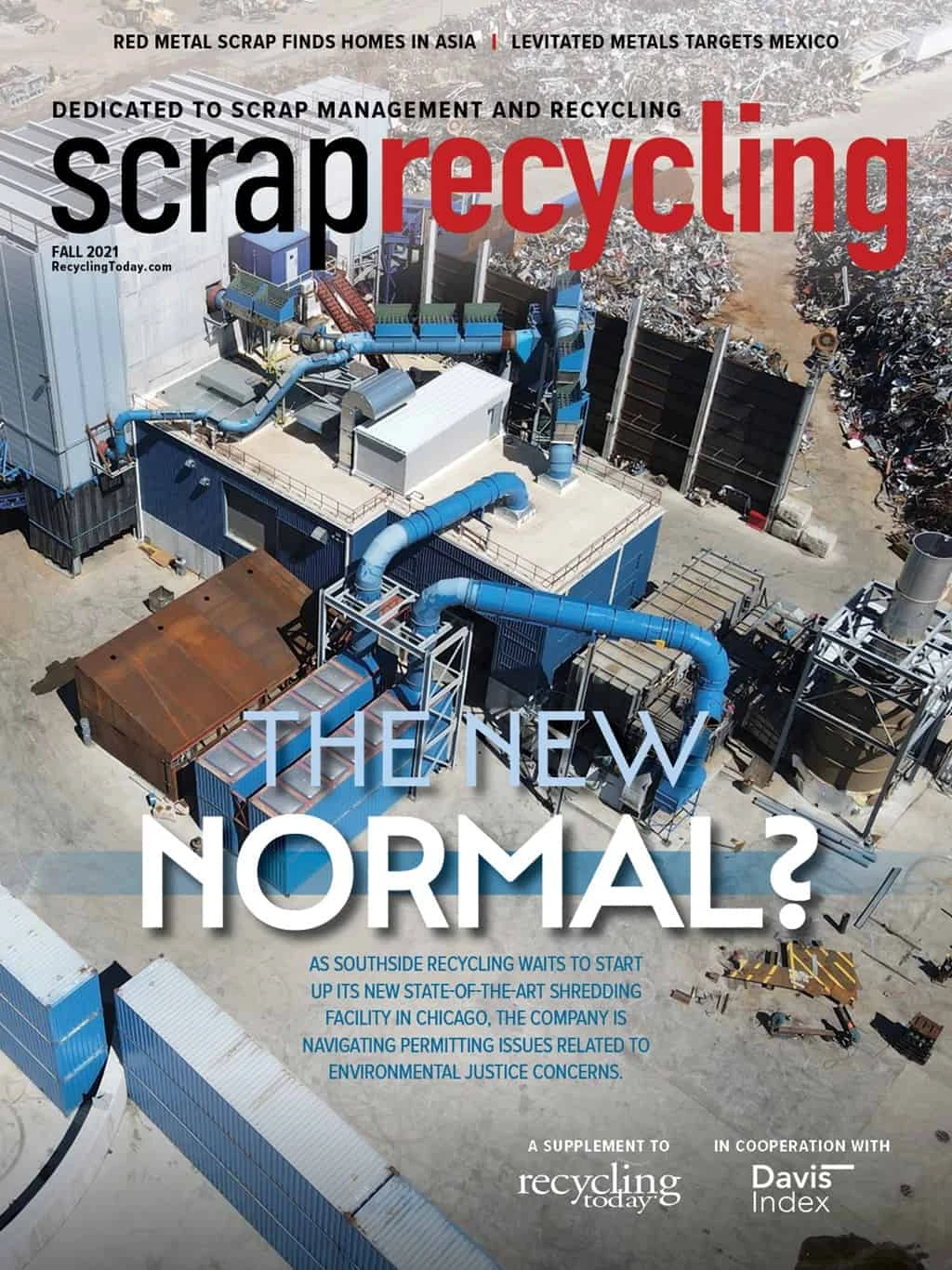
Explore the Fall 2021 Scrap Recycling Issue
Check out more from this issue and find your next story to read.
Latest from Recycling Today
- Republic Services, Blue Polymers open Indianapolis recycling complex
- Altilium produces EV battery cells using recycled materials
- Brightmark enters subsidiaries of Indiana recycling facility into Chapter 11
- Freepoint Eco-Systems receives $50M loan for plastics recycling facility
- PET thermoform recycling the focus of new NAPCOR white paper
- Steel Dynamics cites favorable conditions in Q1
- Hydro starts up construction in Spain
- Green Cubes unveils forklift battery line