
KW Plastics Recycling is among the world’s largest recyclers of high-density polyethylene (HDPE) and polypropylene (PP), with processing capacity of more than 1 billion pounds per year and silo capacity in excess of 100 million pounds. But the Troy, Alabama, firm, which transforms plastic scrap into recycled resin pellets, hasn’t gotten there alone.
Shortly after KW opened its recycling division near its headquarters in the early 1990s, the company began working with SSI Shredding Systems, Wilsonville, Oregon, to meet its size-reduction needs as KW’s plastic feedstock evolved.
As KW’s scrap intake grew, it acquired three SSI shredders: a 100-horsepower (hp) 1600E system, as well as two 200-hp systems. SSI says the two-shaft, rotary-shear shredders, which operate at slow speeds and high torque, are designed to efficiently process difficult materials, such as contaminated bales of plastic scrap, using a series of counter- rotating knives. The original 1600E model still operates on one of KW’s main production lines.
Along with the 1600E, KW runs two larger, 200-hp Dual-Shear systems. Recently, KW installed two Dual-Shear M140-EDSD shredders, each with a 75-inch-by-45-inch cutting chamber, infeed hopper rams and SSI’s SmartFeed technology. That technology allows KW to process difficult materials at high volumes with efficient electric drives, SSI says.
The equipment KW has ordered from SSI has evolved over the years. “We have changed configurations and models over the years as KW Plastics’ needs and preferences changed,” says David Wilson, technical sales at SSI. “As the company has expanded into some new applications, they added additional shredders as they’ve gone along.”
Kenny Campbell, who co-founded KW along with Wiley Sanders, says the versatility and adaptability of SSI’s machines are their biggest strengths.
“Our wash lines are able to run very high-volume rates, very efficiently, and that’s how we’re able to keep our costs down, and our SSI equipment plays a very big role in helping us do that,” Campbell says. “They also were very open to working with us to develop the shredder that best fit our particular applications, whereas the other companies had their shredders, but they were one-size-fits-all, and they weren’t capable or willing to change or modify their offerings to better meet our needs.”
Wilson adds that it’s important for both companies to work to adapt to changing markets. “The people at KW Plastics are always thinking about ways to improve their process, and the SSI shredders by design are very configurable. KW Plastics takes advantage of this. For example, the cutter design they started with is nothing like the cutter configurations they use today.”
One equipment feature that helped KW meet its evolving needs is the optional ram hopper. Light, bulky scrap that could float above cutters or form bridges is forced by the ram directly into the cutter blades. This helped the plastics recycling company improve production capacity, SSI says.
KW views the equipment’s durability as yet another asset. “I like our shredders because they can handle contamination that other shredders aren’t able to handle,” says Scott Saunders, general manager at KW Plastics Recycling. “With recycling, you expect to buy a segregated bale; but, many times, there are contaminants, such as metal or big pieces of wood and other things, in the bale that aren’t supposed to be there. The SSI shredder doesn’t self-destruct, for lack of a better term, when those things hit the machine. It will reverse itself and allow us to continue our processes.”
These shredders’ ability to withstand foreign materials is born out of SSI shredders’ heavy-duty design, Wilson adds. “All the SSI slow-speed Dual-Shear shredders are built like a tank. The M140 models, for example, are over 20 tons each. Plus, all the KW Plastics’ SSI shredders have a patented shock-protection system that is designed to protect the system from damage when the bad stuff drops into the shredder.”
Campbell says even with this type of abuse, the company’s shredders require minimal maintenance. “Our shredders routinely see all types of foreign materials, even metal of all different shapes and sizes, including solid metal shafts; but the shredders are very robust and the cutter blades are very tough,” he explains. “They can take extreme abuse and still function normally.”
And that has meant reduced production downtime for KW. Campbell says the shredders’ uptime is greater than 99 percent.
The SSI machines also are designed to reduce fires and dust exposure, resulting in a cleaner, safer workplace. The slow-speed rotation of the cutters results in low friction and low heat when processing most materials. Between each cutter is a cleaning finger designed to keep material from wrapping around the shaft, keeping the cutting chamber clean and reducing material buildup, Wilson says. In addition, the system produces minimal dust and fines.
Get curated news on YOUR industry.
Enter your email to receive our newsletters.
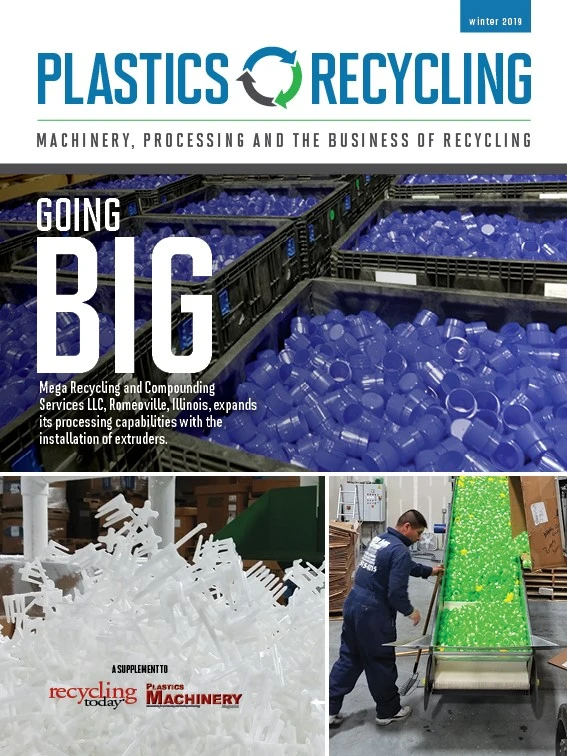
Explore the February 2019 Plastics Recycling Issue
Check out more from this issue and find your next story to read.
Latest from Recycling Today
- Toppoint Holdings expands chassis fleet
- Lego creates miniature tire recycling market
- Lux Research webinar examines chemical recycling timetables
- Plastics producer tracks pulse of wire recycling market
- Republic Services, Blue Polymers open Indianapolis recycling complex
- Altilium produces EV battery cells using recycled materials
- Brightmark enters subsidiaries of Indiana recycling facility into Chapter 11
- Freepoint Eco-Systems receives $50M loan for plastics recycling facility