
One of the best ways to stay ahead in the recycling ball game is to be sure a team has the best and most productive equipment. Joe Krentzman & Son, headquartered in Lewistown, Pennsylvania, is among those atop the standings of recycling companies and aims to maintain its position in the Mid-Atlantic region. It is a full-service scrap company that provides container service and scrap processing to the industrial sector and the general public.
Today, brothers David and Michael Krentzman are at the helm of the operation. They have three central-Pennsylvania locations: the main operation in Lewistown, a second yard in Hollidaysburg and the newest one in DuBois, formerly the H. Shakespeare & Sons business. The Lewistown yard is nearly 100 acres. “We could store more scrap than you could shake a stick at,” Michael says.
The brothers agree that, in the recycling game, hitting a regular stream of singles is more important than hitting a home run. That includes rounding the bases in their operation and stealing opportunities that present themselves.
“Big deals arise here and there, and they are great,” Michael says. “We love the extra-base hits. But our business is built on continuous relationships … ongoing, repeatable deal flow … and that stems from relationships.
“I’d rather have four steady customers I see a little from every month than the one very big deal,” Michael says. If one of the four goes away, the company still has the other three. Call it a mindset of risk mitigation by diversification.
The company also sells various grades of new and secondary structural, tubular and plate/sheet steel products.
Krentzman Metals Corp., a wholly owned subsidiary of Joe Krentzman & Son, trades scrap among other scrap processors and consuming mills and foundries in the Mid-Atlantic region as well as material processed by its parent company.
“The challenges of the past couple years have taught us a good bit about marketing scrap, which we do for scrap sellers and consumers in the Mid-Atlantic, Pittsburgh and Ohio Valley regions,” Michael says.
The Krentzmans also own Krentzman Supply company, which sells pipes, valves and fittings and plumbing, heating, cooling and mechanical products, as well as various industrial supplies.
Processing improvements
Joe Krentzman & Son keeps improving, too, as well as diversifying. As part of a recent upgrade, the company added a new Sierra 750 portable shear/baler/logger to its main processing yard in Lewistown.
“It augments our industrial baling capability and largely replaces excavator-based mobile shears,” Michael says.
The goal was to significantly increase throughput and to lower the company’s cost per ton
The 186,000-pound Sierra 750 features 750 tons of shearing force derived from a 230-horsepower turbo diesel engine. The shear can handle 16 to 22 tons per hour.
“Given the abundance of shredding capacity in our geography and given the type of scrap we see, this was a logical choice,” Michael says of the company’s decision to purchase the portable shear/baler/logger. (Pennsylvania is home to 15 auto shredders, according to the most recent version of Recycling Today’s auto shredder list, which was published in October 2016.)
The new machine is hitting for average. “We will hit the typical tonnage ranges Sierra quotes,” David says. “It does depend on the type of material we are running. Some material adds up faster,” he says.
Joe Krentzman & Son has some obsolete material it is processing alongside new material, as it creates the optimal flow pattern through its yard to the machine.
The Lewistown yard has a Fuchs material handler from Terex with an elevated cab feeding the machine from the charge box side. “We placed the pad for our
While the shear/baler/logger can be operated via remote control, Joe Krentzman & Son currently has an operator stationed in the cab of the machine. “As we run more material over the next several months, we may re-evaluate this process and run via remote control,” David says, adding that for
The Krentzmans chose Sierra equipment because they like the idea that Sierra believes in doing things the way they do—fundamentally, building a relationship and being there
“That was something that quietly drove the process as we decided not just what piece of machinery we wanted but whose piece of machinery we wanted as the basis of a relationship,” Michael says.
Additional capabilities
Joe Krentzman & Son has several streams of scrap that go to the most appropriate processing equipment for that stream. “We dismantle railroad cars, and our mobile shears are great for that,” Michael says.
Even though the mobile shears are not nearly as efficient at preparing most scrap as the Sierra machine, they are great tools for other jobs. They also leave no equipment stranded on base. One of the company’s mobile shears went to Joe Krentzman & Son’s second yard in Hollidaysburg to boost production there.
Anything under ¼-inch in thickness and basically in sheet form is baled in the three-ram ferrous baler. “This makes the most sense, given the premium for baled scrap,” Michael says.
The bulk of the yard’s clean, obsolete material will now be
The company also has an active nonferrous operation that handles all grades of nonferrous scrap.
While the brothers know their company is not the biggest, they say they strive to make Joe Krentzman & Son an efficient, well-run and well-focused company.
“Frankly, we strive to build relationships with good companies led by good people who are honest, honorable and dependable,” Michael says. “Profitable deals make business continue, but dealing with good people is what makes life worth living and makes business even more worth doing.”
Get curated news on YOUR industry.
Enter your email to receive our newsletters.
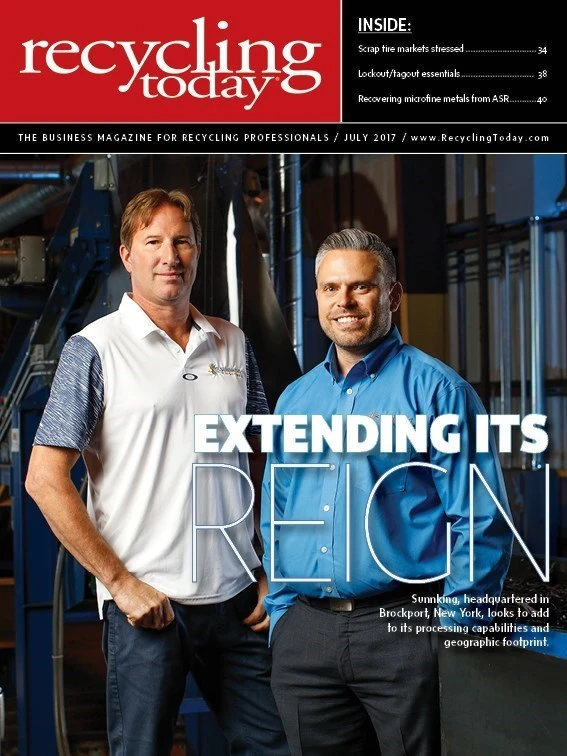
Explore the July 2017 Issue
Check out more from this issue and find your next story to read.
Latest from Recycling Today
- ReMA opposes European efforts seeking export restrictions for recyclables
- Fresh Perspective: Raj Bagaria
- Saica announces plans for second US site
- Update: Novelis produces first aluminum coil made fully from recycled end-of-life automotive scrap
- Aimplas doubles online course offerings
- Radius to be acquired by Toyota subsidiary
- Algoma EAF to start in April
- Erema sees strong demand for high-volume PET systems