Owners of secure document destruction businesses share many things in common with paper recyclers, including reliance on some of the same kinds of equipment. Balers are standard fixtures in both industries; however, baling shredded paper comes with its own unique set of conditions and challenges.
Choosing the right baler for a secure shredding operation doesn’t have to be a difficult process. "It’s an easy application, so you don’t need a complex baler," says Joe Szany, director of Nexgen Baling Systems, a division of Vernon, Ala.-based Marathon Equipment Co.
With some consideration and planning, as well as attention to the specific baling needs for shredded paper, secure document destruction companies can easily match a baler to their operations.
MATCH GAMEManufacturers recommend secure shredding firms consider substance over baler style when choosing baling equipment. "Shredded paper, if it’s mixed office paper, old newspapers or hard white paper, will usually bale well in any kind of baler," says Michael P. Stenson, international sales manager for Waste Processing Equipment Inc./Max-Pak Balers of Rainsville, Ala.
Angelos Androutsopoulos of Vangel Paper, a Baltimore company that offers secure destruction and recycling services, says a more important factor in baler selection is matching the baler’s output with an operation’s volume and allowing for growth.
Roger Williams of American Baler, Bellevue, Ohio, says, "Style has little effect on the integrity of bales." Instead, he said the critical factor when deciding among baling equipment is compression force.
Szany adds that a typical guideline in the industry is to use auto-tie models for production rates of more than 100 tons per month and manual-tie models if a company is processing fewer than 100 tons per month. He adds that the 100-ton-per-month target is more of a suggestion than a hard-and-fast rule.
While all balers can handle shredded paper effectively, a horizontal style baler might edge out a vertical downstroke baler as the best choice, according to Jeffrey Dietterich, president of Advanced Equipment Sales, Franconia, Pa. "A vertical downstroke baler doesn’t necessarily apply the most force," he says, adding that the amount of pressure is a critical factor in determining the best baler for an application.
Another major factor for secure shredders to consider is density, Szany says. "Density saves money, saves time, saves wire costs and saves shipping costs."
Production rates also vary by baler style, which is another factor to keep in mind when shopping for a baler, says Stenson. "One vertical [baler] typically can produce up to 50 tons per month of bales. A horizontal closed-end, manual-tie baler can carry you to 200 tons per month of bales, and an open-end auto-tie, depending on its horsepower, infeed opening and cylinder diameter, can take you from 200 tons per month to 2,000 tons per month. So volume throughput is going to dictate the size of the machine," he says.
Williams also advises shredding companies to look at the various details of their daily operations to help them determine which baler style and size will fit best. For instance, shredding firms should consider the capacity of their trucks as a determining factor as well as how they will operate their balers. Some companies choose to bale throughout the day, a half hour here and there, while others choose to bale for three hours straight, Williams says.
Williams adds that shredding companies should consider the physical space they operate in when sizing a baler—not just the square footage of their physical location. He says traffic around the baler is just as important to consider as the size of physical footprint. "You have to think about how you’re going to bring in trucks," he says. "It’s not just a matter of square footage—you have to account for how you use the space you have."
Dietterich adds that secure shredding companies should consider where their material is going to be marketed. Shredding companies that are looking to export material will have different needs when it comes to bale size to maximize the loading of export containers, which are smaller than those containers used to ship material domestically. "If you’re shipping domestically, you’re filling a 53-foot container with 20 tons of material," he says. "Conversely, [when shipping] overseas, you have to get that same 20 tons of material into a 40-foot oversea container, so you need greater density."
Once a baler has been selected, operators can do a number of things to address the challenges involved in baling shredded paper.
DENSITY MATTERSSome fall-off is inevitable when baling shredded paper, but manufacturers say secure shredding operations can take steps to minimize the effect.
Stenson says fall-off can be lessened by using balers that produce higher-density bales, "which usually means a larger cylinder for greater pounds per square inch on the press head at compaction." He adds, "Or you can use a slip of cardboard to cap the ends of the bale, which will reduce the shredding."
Szany agrees that higher-density bales lead to less fall-off. "When we look at 150,000 pounds of force, with a good tension system, your fall-off will be minimal," he says.
A larger particle size also improves bale integrity, but carries the negative aspect of reducing bale density, says Williams. It could also create security concerns for some customers of secure destruction companies.
Shredders also have the option of bagging or wrapping shredded paper bales to reduce fall-off, but Szany doesn’t recommend the practice. "If you buy the right baler, it’s not necessary," he says.
Williams agrees, adding that wrapping bales adds a great deal of cost that secure shredding companies are unlikely to recoup.
Stenson echoes his sentiments, "The process is time consuming and expensive," he says. "It would be better to invest in a baler with a larger cylinder first." A larger cylinder paired with a smaller packing cavity helps to increase bale density, he says.
Mills also prefer to receive unwrapped bales, Dietterich says. "Mills really frown on wrapping bales," he says. "It’s not something they want to handle."
Other factors, like charge box size, don’t figure in as much, says Stenson. "The charge box does not have an impact on density and integrity," he says. "Size is relative."
In fact, Szany says operators of secure shredding plants can typically go with the smallest charge box because the material has already been taken down to a size that makes it easy to get into the baler.
Dietterich cautions against using a charge box that is too large. Depending on the density of the shredded paper being baled, he says operators run the risk of stalling the ram by attempting to "take too big a bite."
Once a machine is up and running, shredders can take many steps to ensure the most efficient operation.
RUNNING SMOOTHOne way to ensure a baler is producing the densest bales possible is to maintain a consistent feed.
"Just match conveyor throughput speed to baler throughput and stage your materials well to maintain an even feed," advises Stenson.
"Rather than having peaks and valleys, a consistent, steady feed is much better," agrees Szany. "It will help get material into the top as well as the bottom of the baler."
Excessive dust can also be a challenge when processing shredded paper. While some in the industry recommend using water during the baling process, Williams says to do so with caution. "There are positives and negatives," he says regarding water usage. "On one hand, it helps keep dust down. On the other, it increases maintenance."
Stenson also cautions against water usage. "It’s not necessary, and the moisture content can be construed by the paper mill as an attempt to falsely increase bale weight, for which there are price reductions," he says.
When it comes to using water when baling, Androutsopoulos says, "I wouldn’t recommend it unless you’ve discussed it with your buyer of the mill to which you’re shipping. It could be a problem for them."
When it comes to maintenance, shredder operators should be mindful of excess dust and keep equipment clean, Szany says.
Williams agrees, saying hydraulic tanks should be kept especially clean. "Cleanliness and housekeeping—these will eliminate 80 to 85 percent of issues with the baler."
The author is associate editor of
SDB and can be contacted at jgubeno@gie.net.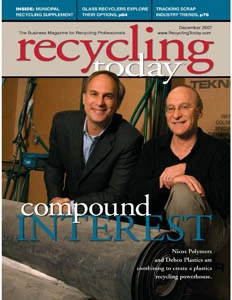
Explore the December 2007 Issue
Check out more from this issue and find your next story to read.
Latest from Recycling Today
- Sortera Technologies ‘owning and operating’ aluminum sorting solutions
- IDTechEx sees electric-powered construction equipment growth
- Global steel output recedes in November
- Fitch Ratings sees reasons for steel optimism in 2025
- P+PB adds new board members
- BlueScope, BHP & Rio Tinto select site for electric smelting furnace pilot plant
- Magnomer joins Canada Plastics Pact
- Out of touch with reality