
The polyethylene terephthalate (PET) bottle recycling market added another large consumer when the textile company Unifi Inc., headquartered in Greensboro, North Carolina, opened its Repreve Bottle Processing Center at its textile dye house in Reidsville, North Carolina.
The center’s opening allows Unifi to fully control the process of converting bales of plastic bottles into postconsumer recycled flake for its Repreve brand fiber. With a growing customer base of apparel producers seeking to increase their sustainability efforts by using recycled material, the new plant provides the control that the company determined was essential to meet these needs.
Introducing Repreve
Unifi has been in the textile business for more than 45 years. It is one of the world’s largest producers of synthetic nylon and polyester products.
Prior to introducing Repreve, its line of 100 percent recycled content fiber, in 2007, Unifi blended industrial fiber scrap into its product line to provide a recycled-content option. While Repreve fiber is made completely from recycled material, it can contain a mix of postindustrial and postconsumer content or be made solely from postconsumer material, depending on customers’ preferences.
Since introducing its Repreve line, Unifi has seen a growing number of top apparel firms, such as Levi’s, Haggar, The North Face and Patagonia, use its recycled fiber in their products. Many of these customers want to use fiber that contains as much as 100 percent postconsumer plastic.
Tim Cole, Unifi vice president of manufacturing, says the company’s goal is to “use as much recycled content as possible, although there are some applications where it is more challenging.”
While the apparel sector is a key end market for Repreve, the brand also is making inroads with the upholstery and automotive sectors. On the automotive side, Unifi notes that since 2012 Ford Motor Co., Dearborn, Michigan, has used Repreve recycled fiber in five of its car and truck models, including in its F-150 pickup truck.
In total, Unifi estimates that since it started using recycled PET to manufacture Repreve, it has recycled more than 5 billion plastic bottles.
The flake is converted into recycled fiber at Unifi’s Recycling Center in Yadkinville, North Carolina. Previously, relying on outside sources for flake created some challenges for the operation, Cole says.
Going vertical
For years Unifi purchased recycled PET flake on the open market for manufactureing Repreve, Cole says.
However, inconsistency in the quality of the available recycled flake led Unifi to explore producing its own raw material. “What we found is that we had to invest in our own assets if we wanted to improve the flake quality going into our fiber,” he says.
That goal came to fruition when Unifi opened its Repreve Bottle Processing Center in Reidsville last August. The $28 million facility allowed the company to achieve its goal of vertical integration for its Repreve brand. By opening its own facility to convert plastic bottles into flake, Unifi could add flexibility, expand its production capabilities and support Repreve’s growth, Cole says.
Operating its own bottle processing facility allows Unifi to better control the quality of its raw material, Cole says. “You get better results when you can control your supply.”
He adds that the move “has improved our performance in Yadkinville.”
Additionally, Cole says, the investment “demonstrates our commitment and validates our story. Because of that, we are getting more interest from other retailers and from other companies. We can show the bottles-to-fiber process, and we can establish what they can get from us.”
The Repreve Bottle Processing Center was built using available square footage at Unifi’s dye house, where the processing center and dyeing operation operate simultaneously. Unifi wanted the bottle processing center to be close to its Yadkinville facility to keep its overall costs down, he says. “We put the plant in North Carolina because we already had a vibrant dying operation at the site. With the existing infrastructure in place, we could reduce our capital costs. We already had a modern wastewater treatment plant, steam boilers and significant electrical infrastructure that we could build on.”
The arrangement enables some of the wastewater used in the dying operation to be reused to clean and convert the postconsumer PET bottles into flake. “We are using the treated wastewater from our dyeing operation as a prewashing operation for our bottle washing operation,” Cole says. “It was a nice fit to reduce our environmental footprint.”
The Bottle Processing Center takes up more than 150,000 square feet at the facility. “Eventually, we will produce around 75 million pounds a year of flake. That is our goal,” Cole says.
After the PET bottles are cleaned and flaked, the flakes are shipped to Repreve’s recycling center in Yadkinville, where Repreve fiber is created.
From bottle to flake
Unifi purchases baled PET bottles from material recovery facilities (MRFs) throughout the eastern United States as raw material for its Bottle Processing Center. The company uses clear and green PET bottles in its process.
Incoming bottles are sorted and filtered using multiple processes to ensure that only high-quality PET bottles are used to create flake.
Labels, debris and caps are removed from the bottles, which then are shredded into flake, washed, dried and bagged to be used to produce Repreve fiber.
The company sells excess flake on the open market. The material is used to make products that include thermoformed food-grade packaging, strapping and film.
At the center’s official grand opening last year, Tom Caudle, Unifi president, said, “The vertical integration of our Repreve manufacturing process highlights an important next step in Unifi’s continued path toward sustainability and producing high-quality, value-added products. The Repreve Bottle Processing Center uses custom-designed, cutting-edge technology and provides increased flexibility that will allow us to better serve our customers, as well as create a new channel of revenue.”
Because Repreve is taking in PET bottles from a broad range of sources, the company says it has invested significant capital into equipment that will allow it to meet its quality specifications.
While it has very specific requirements, Cole says it can be a challenge to get the right material coming through the door. The processing center buys material from more than 50 different suppliers through the eastern half of the country. “[Quality] varies by region quite a bit,” he says. “If it is a curbside program or a recycling facility that has a deposit bill in place, the quality can be quite different. We knew going in that we would be handling a wide range of plastics, so we spent more money with the sorting technology in case some stuff was not high quality.”
Cole continues, “We have worked with two major equipment suppliers to develop our process.
“On the front end, we worked with Bulk Handling Systems (BHS),” he says. “They helped us with the bale handling and bottle sorting. We used a lot of their NRT (National Recovery Technologies) sorting technology in our bottle sorting area.”
Unifi incorporated nine optical sorting units from NRT, Nashville, Tennessee, into the system. They remove non-PET plastics from the incoming material stream.
Sponsored Content
Labor that Works
With 25 years of experience, Leadpoint delivers cost-effective workforce solutions tailored to your needs. We handle the recruiting, hiring, training, and onboarding to deliver stable, productive, and safety-focused teams. Our commitment to safety and quality ensures peace of mind with a reliable workforce that helps you achieve your goals.
The BHS system also includes screen and air separation technologies.
While the facility produces flake only from clear and green PET bottles, Cole acknowledges that a range of other plastics are being delivered to the facility in the PET bales that it purchases. The non-PET material is sorted out, baled and marketed to other consumers.
He says there is a learning curve for suppliers, though he would not reveal the percentage of outthrows the operation averages.
To further ensure quality, Unifi installed sorting and cleaning equipment from the Italian equipment company Amut SpA, which is used on the back end to clean the recycled flake. Amut designed, built and assembled a new PET washing plant for the facility, including equipment for prewashing bottles and removing shrink sleeve wraps, ensuring Unifi achieved the total vertical integration it sought.
Even with “state-of-the-art” technology installed, quality remains an issue. While demurring on the relative quality of its feedstock, Cole says he hopes to see it improve, if for no other reason than because the company offers a financial incentive to quality suppliers. “I would state the obvious: If a reclaimer can provide Unifi with a purer PET strain, Unifi can afford to pay them more for their material,” he says. “The higher percentage of PET a reclaimer can send me in that bale of bottles, the more Unifi can afford to pay them.”
Cole says that after opening with one shift per day the middle of August 2016, the facility quickly ramped up. By Oct. 1, it was operating around the clock.
As of early February, Unifi says the plant had processed more than 350 million bottles. By the middle of this year, the company says it expects to reach a weekly run rate of 42 million bottles.
Ongoing challenges
Along with bale quality, another challenge Unifi is confronting is the changing nature of the bottles themselves. Thinner PET bottles, Cole says, have had a major impact on the design of the plant’s equipment. “We did try to design a plant where we would have less loss with the lighter bottles.” However, he continues, “It did make designing the plant more challenging.”
With demand for its line of Repreve fabric growing, Cole says the biggest challenge is boosting the overall PET recovery rate in the United States. He points out that many European and Asian countries have PET recovery rates in excess of 50 percent, while recovery in the United States has languished in the 35 percent range. “We would like to see much higher rates.”
Get curated news on YOUR industry.
Enter your email to receive our newsletters.
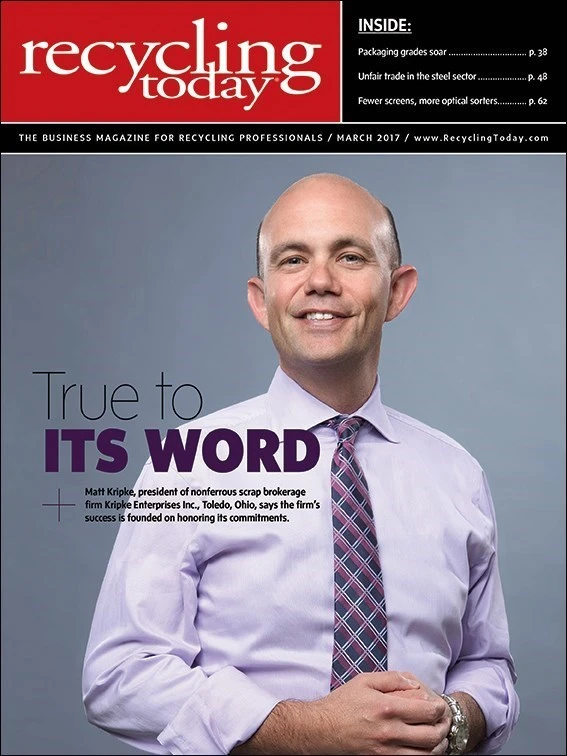
Explore the March 2017 Issue
Check out more from this issue and find your next story to read.
Latest from Recycling Today
- Returpack reports increased DRS activity in Sweden
- Trade groups align against European export restrictions
- Construction, auto sectors show mixed signals
- Politics in Turkey threaten recycled steel outlet
- Toppoint Holdings expands chassis fleet
- Lego creates miniature tire recycling market
- Lux Research webinar examines chemical recycling timetables
- Plastics producer tracks pulse of wire recycling market