One of the significant challenges facing recyclers today is the suppression of jobsite dust that typically accompanies any number of activities, including sorting, loading, hauling, abrasive blasting, concrete and masonry demolition and crushing.
Depending on the source, airborne dust can create several concerns, such as the potential for environmental, health or safety risks; higher equipment maintenance costs; reduced visibility; poor community relations; and, in some cases, even the danger of explosion.
The trend toward tighter regulation of all emissions provides additional motivation for the industry to find efficient, cost-effective methods of dust control.
The most common techniques for controlling dust generated at recycling sites are surface suppression and airborne capture. Surface dust suppression is an attempt to prevent dust from migrating by wetting the source before particles become airborne. This can be achieved through static spreading (while the debris source is stationary) or dynamic wetting (such as spraying down the material on a moving conveyor).
Some methods can be quite sophisticated. The dynamic surface wetting systems built into crushing or screening equipment, for example, generally feature good effectiveness with minimal water usage. While integrated suppression technology can be very efficient, it’s limited to the equipment on which it is installed, leaving recyclers to improvise their own ways of handling dust from their many other dust-generating activities.
SPRAY ON
Most companies use very basic static spraying techniques, such as sprinklers or handheld hoses. While these methods can help reduce the amount of surface dust that can become airborne, they tend to saturate target surfaces, often resulting in standing water that can create additional hazards. Their reach also tends to be quite limited, and the approach frequently requires significant staff time to operate the hoses or to reposition sprinkler heads.
A far more effective option is an atomized spray, which relies on the principle of creating very small water droplets, delivering them at relatively high velocity over a wide coverage area to produce collisions with dust particles and drive them to the ground. The method has proven well suited to C&D applications in particular, one of the few technologies capable of delivering dust control via airborne capture and surface wetting.
When selecting any dust suppression system, the most obvious criteria is its performance: How effectively does it knock down solid particles and prevent ground-level dust from becoming airborne? One way to compare equipment designs is to look at their power, including motor rating, air velocity, air volume and water pressure, all of which are directly related to range and coverage area. The water source is also a factor: It’s very unlikely that a machine supplied by a garden hose will be able to equal the performance of equipment fed by a 1.5-inch fire hose.
But the equation is far more complex than reviewing the specifications. As dust particles and water droplets approach each other, the best chance for a collision is created when they are roughly the same size, avoiding a slipstream effect that can carry them past one another. Unfortunately, there is a tradeoff—larger droplets will travel farther before losing their momentum, while smaller droplets are more effective at suppressing airborne dust.
Because of inter-related factors like these, all of the components in dust control equipment must be designed to achieve an optimum balance, including pump, nozzles, fan and other elements. The most effective models are likely to be those designed specifically for dust suppression, as opposed to equipment intended for other purposes that has been modified.
EXERCISING OPTIONS
When shopping for dust suppression equipment, consider seeing a specialist. A manufacturer that adopts dust control as one of many product lines must divide its resources to support all of those lines, whether it be in R&D, technical service or repair. In contrast, a supplier whose sole business is dust control will have a very focused approach, with every employee concentrating on functions related to that single objective.
Be sure to review the standard features and available options. Will the manufacturer deliver the unit on a carriage mount so it can be easily moved wherever it’s needed on a given day? Is it available with a skid mount so it can be easily moved with a fork lift? Can it be ordered with a dosing pump to add surfactants for superior particle agglomeration or additives for odor control?
Beyond options and accessories, look for the ability to customize. Some equipment brands are sold with an established set of options, with little room to accommodate specialized needs. For example, in some applications, the ability to tailor droplet size to suppress specific particles can be a significant advantage. That kind of versatility typically means a change in nozzles and possibly other features, requiring a certain amount of flexibility that not all manufacturers will offer.
It may also be a good idea to find out if the equipment is suitable for automatic operation, even if that ability isn’t needed now. In future years, it may become desirable to install solenoid-activated controls or other automation, allowing users to activate suppression equipment at specific times to conserve water and energy.
As with many types of equipment, good indicators of overall quality are the supplier’s warranty and guarantee. A manufacturer willing to warranty its products for significantly longer than its competitors is probably building a durable and reliable piece of equipment. Likewise, if a supplier ensures customer satisfaction with a money-back guarantee, it’s a good indication that the products have been field-proven.
With any large purchase, it makes sense to request references and success stories in the specific industry niche where the equipment will be used. Finally, keep an eye out for manufacturers whose success depends on customers like you.
The author is CEO of Dust Control Technology, Peoria, Ill.
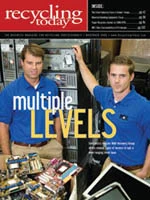
Explore the November 2008 Issue
Check out more from this issue and find your next story to read.
Latest from Recycling Today
- NWRA announces 2025 Driver of the Year, Operator of the Year winners
- The Scrap Show: Nanci Schuld of FE Trading Group LLC
- Call2Recycle Canada partners with RLG to advance battery collection
- Report delves into recovery opportunities for food-grade polypropylene
- Reimagining Supplier Payments in Metal Recycling: A Digital Leap Forward
- STEINERT Lithium Battery Detection and Removal from Waste Streams
- Driving the Future: Innovations in Waste & Recycling Technology
- Robin Wiener recognized for recycling leadership