

A fictional story posed an all-too-real scenario for attendees at Scrap Expo in Louisville, Kentucky: A poorly maintained scrap yard with lax safety standards could spell trouble.
During a presentation Sept. 12, “How your equipment is a mirror into your company culture,” John Sacco, president and co-owner of Bakersfield, California-based Sierra International Machinery, used a story about a journalist touring two scrap yards—one filled with potential hazards and another focused on a high standard of cleanliness and safety—to illustrate the importance of a well-maintained yard’s effect on the perception of not just a company, but the overall industry.
Sacco used real photos taken at scrap yards, including his own in Bakersfield, California, to drive the message home. The story of Tony, a fictional journalist for the New York Times, was presented along with images that included employees not wearing the proper personal protective equipment (PPE) while torching, forklifts with torn seats and impact marks on their rear and piles of scrap surrounding a material handler. At the other yard, roads were kept clean with a sweeper truck, employees were decked out with the proper PPE and equipment that was years old appeared brand new.
“So, are you going to write anything?” Sacco said of Tony’s dilemma after his two scrap yard tours. “You might focus on the negative. And what’s the negative? Yard No. 1. Is the journalist going to think our industry is a junk industry, or professionally kept? He’s going to be conflicted. … Yard No. 1 and yard No. 2 have completely different cultures.”

Trouble spots
Sacco said it is important for yard owners to understand everyone in their company plays a part in what outsiders see.
“It’s incumbent on everybody who owns a yard to understand that every day you’re open, you’re open to the possibility of getting an OSHA [Occupational Safety and Health Administration] inspection, an EPA [Environmental Protection Agency] inspection, Air Pollution Control Board inspection, or, for that matter, one of your important clients,” he said. “You’re trying to buy their material, and they want to do an audit of your facility. They want to see who they’re doing business with. That’s real.”
He pointed to images of scrap yard employees standing near piles without wearing hard hats and torchmen working with exposed skin and no face or eye protection, noting that he found the pictures online. “When OSHA [looks for] the next yard they’re going to call on and fine, you’ve posted, ‘Come fine the heck out of me,’” he said.
Citing photos of Sierra torchmen fully outfitted with PPE, including facemasks and respirators, he said employees are fitness-tested for the gas that emits from the torching process. “Let’s protect our people,” he said.
Next, Sacco highlighted forklifts. Three photos showed operators drinking coffee while driving, wearing the incorrect hat and not wearing a seatbelt. “If OSHA comes into your yard and sees guys driving your forklift this way and this is what you’re presenting, get ready to cut a big check to OSHA,” he said.
A photo Sacco personally took at a yard featured a forklift with scrapes along the back. “I took these, and [I] think to myself, as an industry, we’ve got to change,” he said. “What are we telling people in our business, our companies, when we have equipment with all these scrapes on the back? We’re telling them it’s OK to run into things, it’s OK to hit a person. That’s what your equipment is saying about your company culture right there. It’s OK, I’m going to hit someone someday, because I’m hitting everything else. It’s only a matter of time.”
Finding a better way

Sacco noted that Sierra’s journey to operating a clean and safe yard wasn’t a quick one, taking 10 years to make necessary improvements. There was a time when the company’s Bakersfield yard posed its fair share of hazards.
“You’re not going to go home, snap your fingers and this is what you’ll be,” he said, using a current photo of the Bakersfield site with clean, new-looking forklifts and material handlers that actually were several years old. “It takes time to develop the culture within. Every single day, and I kid you not, before a forklift is ever put into service, they have to [clean and inspect it]. When I see a ding on a forklift, it’s immediately taken out of service. It has to be taken to the shop. "If you’re cleaning like this every morning, I guarantee you those forklifts are going to last a lot longer,” he added. “Sierra was not this way before. Yes, we let people run into things all the time. We thought it was normal. We thought being rough and tough was OK. But when you have an OSHA inspector come visit you and you’re scared to death of what fine they’re going to give you, it changed our lives at Sierra. … It’s taken a long time to get where we’re going. I encourage you, it doesn’t happen overnight, but it’ll happen in time.”
Two-ram balers were his next example. In a problem yard, a baler had a faulty wire tie unit and wires that appeared discombobulated, as well as oil leaks, while pictures of a similar, 10-year-old unit at the Bakersfield yard showed employees cleaning out the wire tie unit and cleaning the area around the baler at the end of a shift.
“Again, we can clean up,” Sacco said. “Leaks happen. There isn’t a hydraulic piece of equipment I’ve ever been associated with in my facility that hasn’t leaked at one time or another. That will happen. But let’s clean it up, because if they come in and inspect you and they see something like this, they’re just going to stay because they know they’ve got you.”
He noted his preference is to use material handlers to feed conveyors for efficiency and safety, using a photo example of a front-end wheel loader that had toppled over onto its side in a yard and was left unattended.
“All of our nonferrous conveyors, people who feed copper, aluminum, stainless, cardboard, we can do all that. Why? Because this is what we’re going to prevent,” Sacco said. “Bobcats, wheel loaders, those things are zooming back and forth and back and forth. They don’t care what’s in front of them or in back of them. … We’ve got to take safety into consideration.
“How can we prevent injury? Let’s provide our employees with tools so they can prevent it. Not to say a front-end loader isn’t great. But a material handler on stabilizers isn’t going to drive into the pit if it’s in one place and it knows to drive away from the pit if it’s moving.”

Personnel plays
A company’s culture and its ability to attract talent are linked, said Sacco, who acknowledged many scrap yard owners across the industry are struggling to find new employees.
One way to drive interest from prospective talent is to place emphasis on a trucking fleet.
“Our trucks are our billboards,” he said, using the fleet deployed by Brett Ekart, CEO of Boise, Idaho-based United Metals Recycling, as an example. “[Brett] just thinks, ‘Hey, I can attract talent because people see my trucks and think those are [nice] trucks, I want to work for a company that provides [nice] equipment for their employees, their drivers.’ … Every day in your city, your community, your trucks are running around, picking up recyclables and moving them. Think about your fleet.”
Ekart added, “I like clean trucks because I need truck drivers, and the only way to get truck drivers is to get good equipment.”
For staff already in place, Sacco recommended leading by example and being thorough in enforcing rules for safety and cleanliness to build a desirable culture, even if it means having to let some solid employees go in the process.
“It takes time [to build culture],” Sacco said. “It just doesn’t happen overnight. I’m not standing here because I just did this and, boom, there it is. It took time. But once [employees] know you’re following up … You’ll never see me in my yard without my PPE ever, because if I’m going to project safety and require my people to work safely, if you’re not, they don’t care. They go, ‘Look at him, he doesn’t have to wear it, why should I?’
“We can’t say profit or safety,” he added. “We cannot say profit or maintenance. We cannot say profit or environmental stewardship. We have to say the word ‘and.’ Profit and safety. Profit and environmental stewardship. Profit and maintenance. You can’t have one without the other. … I encourage you to think about how you can have profit and better roads, profit and better-maintained equipment. How can we have profit and do something environmentally that really is good for the community.”

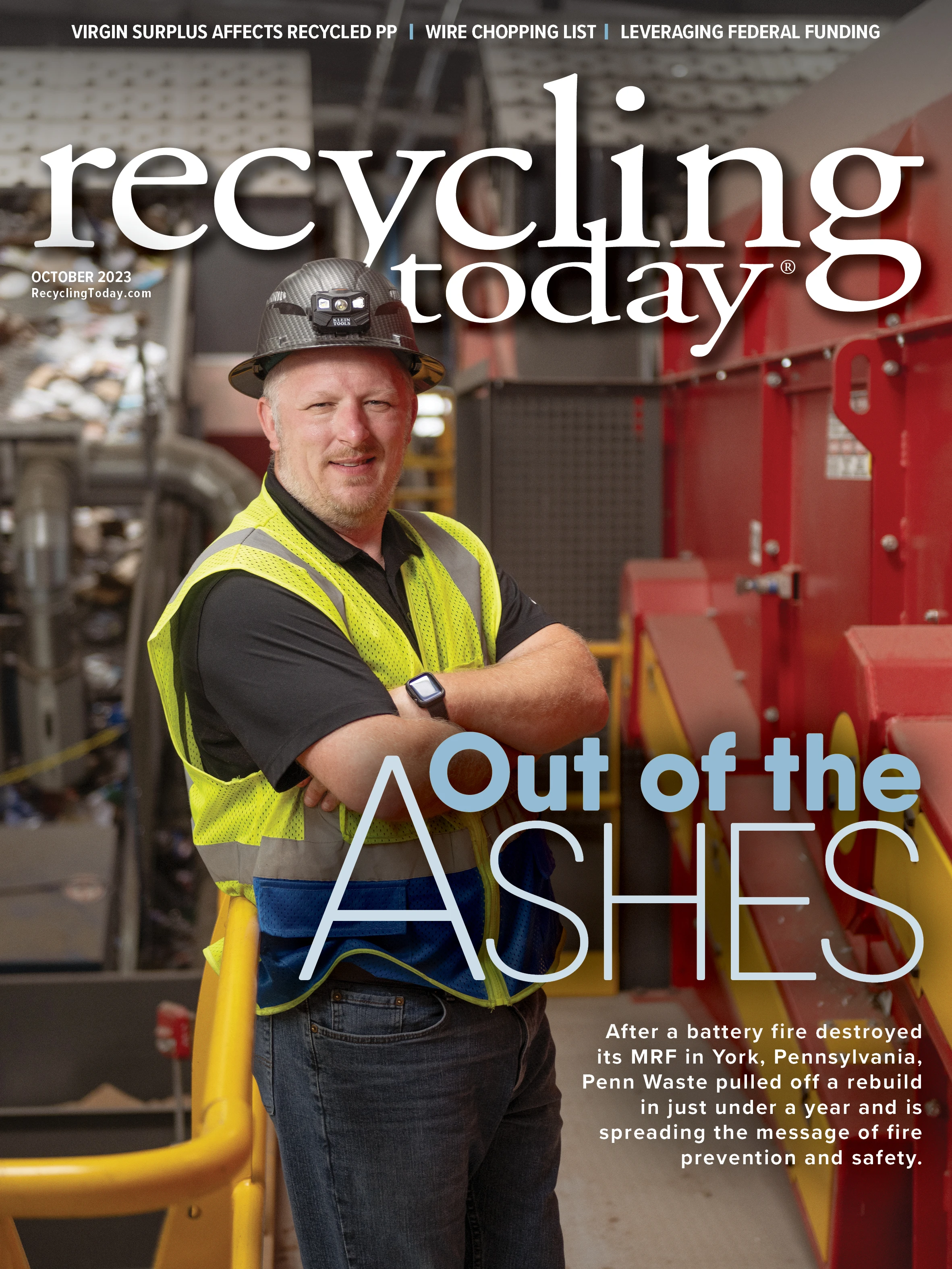
Explore the October 2023 Issue
Check out more from this issue and find your next story to read.
Latest from Recycling Today
- ReMA PSI Chapter adds 7 members
- Joe Ursuy elected to NWRA Hall of Fame
- RRS adds to ownership team
- S3 Recycling Solutions acquires Electronics Recycling Solutions
- Nextek, Coveris to recycle food-grade plastic film
- Recyclekaro expands recycling capacity
- USTR hears comments on port fee proposal
- C&D World 2025 hits record attendance and exhibitor numbers