

For many scrap companies, sustainability always has been part of their visions. For example, in 1905, Louis Padnos started Holland, Michigan-based Padnos by trading furs and rags with the hope he could extend the life of materials people had discarded.
Sustainability has become even more important in the 117-year-old company’s recent history. Today, Padnos takes a closer look at its carbon footprint; environmental, social and governance (ESG) reporting; and the sustainability of its customers’ facilities, too. Kari Bliss, principal of sustainability at Padnos, has influenced many of the company’s efforts around sustainability in the past decade.
Bliss first joined Padnos as an account executive for the company’s paper and plastics division in 2010 after spending the first part of her career in real estate construction. Although Bliss didn’t have any scrap industry experience when she joined Padnos, she says the company wanted to hire someone with an outside perspective to grow its plastics division.
“Sometimes fresh eyes are a good way to grow,” Bliss says. “I didn’t have any preconceived notions coming in.”
Bliss says she spent many nights studying the paper and plastics markets in the early years of her career at Padnos.
“Those first few years, I made a lot of mistakes trying to understand who is a good customer for us,” she says.
Bliss says she was part of a great team that was willing to go the extra mile for its customers. She adds that the hard work and research she did paid off because she helped grow the plastics division to where it needed to split from the company’s paper division. The plastics division even added compounding services to aid customers, and she says they are two fast-growing areas for Padnos.
In her career at Padnos, Bliss says she always considers ways the company can improve its sustainability performance. About three years ago, she became Padnos’ first sustainability leader. Last year, Bliss was promoted to the role of principal of sustainability.
She shares some of the company’s most recent efforts around sustainability in the interview that follows, including Padnos’ work on Sustainability City and recycling plastics from auto shredder residue (ASR), or fluff.

Recycling Today (RT): Early in your career at Padnos, you helped the company get into compounding. What was it was like working in Padnos’ plastics division and starting to offer compounding services?
Kari Bliss (KB): The biggest challenge was getting everyone to see my vision. In the early days, I didn’t know what I didn’t know. We were doing the hard work of collection and downsizing the plastic, selling it to compounders. To me, it was obvious that compounding was the next logical step to vertically integrate our services. It took a lot of trial and error to create a narrative that others could get behind.
Ultimately, it took Jonathan Padnos, our president and CEO, joining the plastics division. He saw the possibility and set out to find a partner to get us up to speed fast. That partner, Gary Barnett, is still with us today [as vice president of plastics].
RT: How have its compounding business and plastics division become among the fastest-growing areas for Padnos?
KB: The narrative quickly changed from just being a recycler to offering closed-loop programs. We can take material from the customer, improve the mechanical properties and give it back to the customer, building a closed-loop system. This was the precursor to the work we do today to further the circular economy. As zero waste became the goal of every OEM [original equipment manufacturer], our services were in high demand. We aren’t the largest recycler; we do have more diverse processing capabilities than our peers, and it gave us a competitive edge.
RT: Since joining Padnos, you have transitioned into a role overseeing sustainability efforts. What do you do on a day-to-day basis at Padnos as its principal of sustainability?
KB: I still spend time researching every day. Our customers depend on us to bring them the latest innovations for handling their materials. My team tracks our Scope 1, 2 and 3 emissions, and we provide carbon scores for our products. We believe in the value of private-public partnerships to build a circular economy. To that end, I study pending legislation, sit on various boards and speak at conferences.
RT: What has it been like coaching Padnos’ customers on sustainability?
KB: Some of the best success stories we’ve had is in full collaboration with our customers. I’ll go into a plant and see that they’re trying to do the right thing. They may not realize how much waste is happening with how they handle their scrap materials.
For example, I might go to a customer that has 10 buildings, and they’re hauling all their loose corrugated and film to one baler. The lightweight nature of the material could take one person all day to transport the material around. If we can put a piece of equipment in to help densify the material at the source of generation, it has a big impact on handling time and frees up valuable floor space. A traditional [return on investment, or ROI] calculation may miss some of the savings available.
RT: In recent years, Padnos also launched Sustainability City. Could you tell me more about that effort?
KB: Sustainability City is an 18,000-square-foot innovation space where we can take our time solving some of our customers’ toughest challenges. We have room to lay out a full load of materials and gather enough data to develop better solutions. We regularly get in new equipment that can help densify material, so our customers can reduce their freight costs and lower carbon emissions.
Hundreds of customers have visited with the teams to participate in trials. This shared learning develops more solutions and helps with change management when improvements are implemented.
RT: In your role, you have also researched the recyclability of ASR. What got you interested in this, and what were your findings?
KB: Over 98 percent of the metal from cars and durable goods is captured in our shredder and downstream operation. What is left appears to be a hopeless mix of fabric, wood, foam, plastic, dirt and rubber. About eight years ago, a team member asked me what could be done with all the ASR that ends up as landfill cover. It piqued my interest, and I started to research what efforts had been made to solve the challenges. I discovered the obstacles were more financial than technical.
In 2020, consumers started to demand producers address climate change. Lots of companies were making bold commitments to reduce their carbon footprint and increase postconsumer content. I knew those goals would be hard to reach based on existing feedstocks. I dusted off my research and started to discuss the possibilities with other team members.
Eventually, I got enough team members interested that the project took off. My main contribution was to see the possible and not give up.
It took collaboration between our different business units to produce a product with a desirable ROI. For decades, manufacturers have used recycled content because it costs less than prime. Now, they need to use recycled content to honor their commitments and meet the demands of consumers.
To the best of my knowledge, we are the only ones in the United States mechanically recycling ASR. We’re not using solvents; we’re not using pyrolysis; we’re not using any kind of molecular or chemical process, which means that our ASR is created with a much lower carbon footprint than plastic recovered from one of those other processes.
RT: How else is Padnos using its ASR?
KB: Polypropylene is a versatile material that is likely to increase in use over the next decade. Today, we are producing a 20-percent-talc-filled polypropylene from the ASR. It is one of the most widely used materials in automobile and durable goods manufacturing. As we move from internal combustion engine (ICE) to electric vehicles (EV), materials will change. An EV weighs about 1,000 pounds more than an ICE. That needs to change to improve the range, and plastics are one of the best ways to achieve lightweighting goals.
We’re in negotiations with multiple OEMs who have expressed interest in our material. ASR plastic will be in products next year.
RT: What are the biggest challenges to recovering plastics from ASR?
KB: The mix of materials is staggering and inconsistent. Every material has different properties that need different sortation technologies. The development of these technologies will continue to be the challenge over the next few years.
Regarding the financial viability of [plastic recycled from] ASR, it really isn’t going to be a cost savings. This material is not going to be cheaper than prime material. The savings come more about that it is a large source of postconsumer end-of-life content. It would be difficult for the OEMs to meet claims that they’ve made of having recycled content and reducing their carbon footprint without it.
RT: What are your hopes for the future regarding how the scrap industry will handle ASR overall?
KB: I would like to see our technology spread across the U.S., so all ASR becomes part of the circular economy.
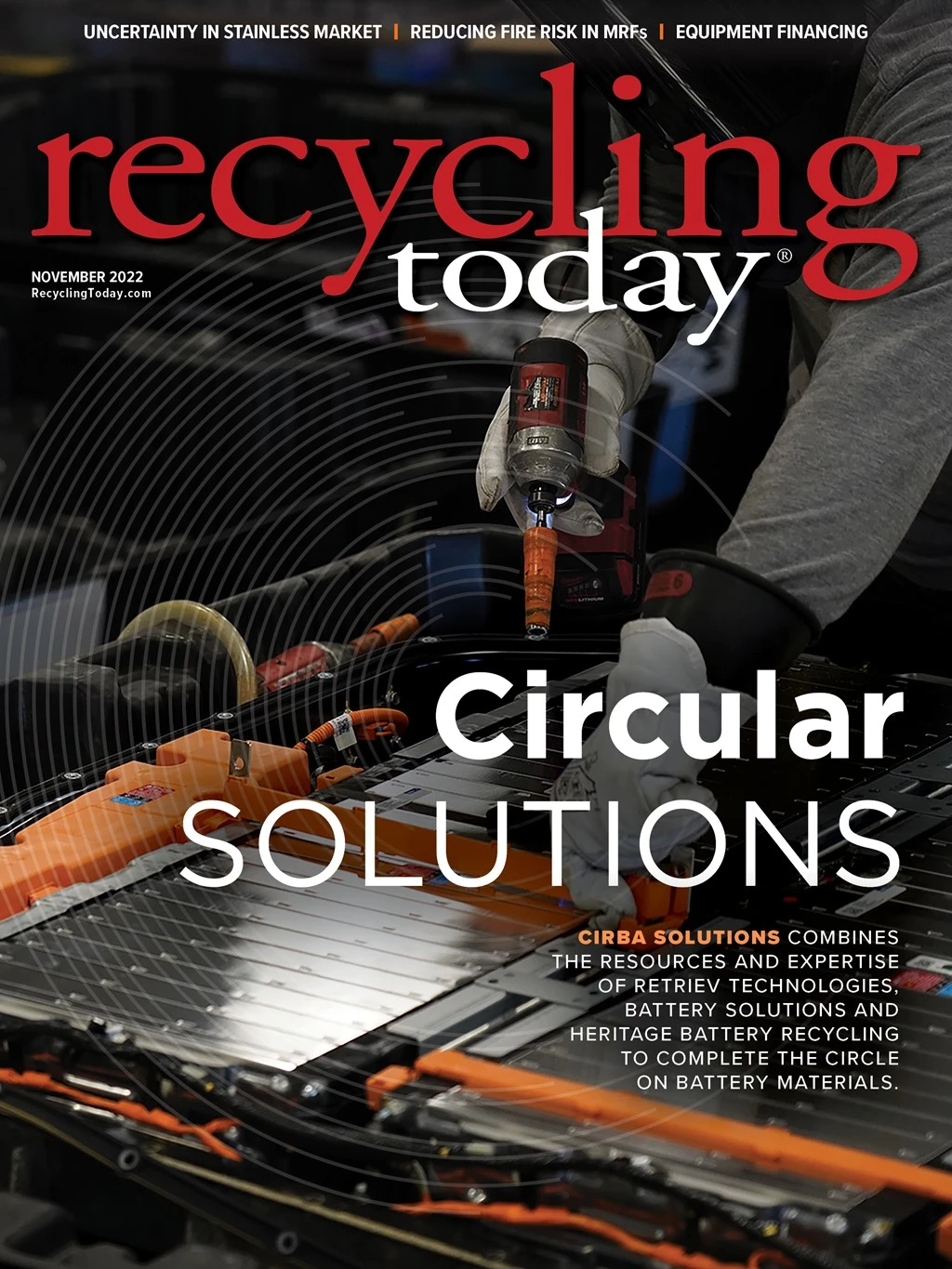
Explore the November 2022 Issue
Check out more from this issue and find your next story to read.
Latest from Recycling Today
- Athens Services terminates contract with San Marino, California
- Partners develop specialty response vehicles for LIB fires
- Sonoco cites OCC shortage for price hike in Europe
- British Steel mill’s future up in the air
- Tomra applies GAINnext AI technology to upgrade wrought aluminum scrap
- Redwood Materials partners with Isuzu Commercial Truck
- The push for more supply
- ReMA PSI Chapter adds 7 members