
In February of last year, Johnson Controls, the world’s largest manufacturer of automotive batteries, finalized an agreement covering North America, China
At the time of the announcement, Joe Walicki, president of Johnson Controls Power Solutions, said, “Agreements like this are a part of our continuing strategy to invest in clean technologies, building on our commitment to
That sentiment is echoed by Tom Parmenter, global vice president of procurement, components and sourcing, Johnson Controls Power Solutions, who says, “Investments like this are a part of our strategy to invest in new technologies.”
Aqua Metals drew Johnson Control’s attention because it was the first company in the industry to demonstrate real-world implementation of new recycling technology, Parmenter says.
The technology
Aqua Metals’ AquaRefining technology extracts lead from lead-acid batteries with a room temperature, closed-loop, water-based process that results in less hazardous waste and reduces direct human contact with lead, according to the company. The process produces lead that does not require further refining to increase its purity.
Aqua Metals opened its first battery recycling plant in McCarran, Nevada, in August of 2016.
In a Recycling Today article that ran in the January 2017 Scrap Metals Supplement, available at www.RecyclingToday.com/article/disruptive-technology, Steve Cotton, chief commercial officer for the company, explains that in the AquaRefining process, the lead paste that is removed from lead-acid batteries is not dried as it is in the traditional recycling process that involves smelting and refining. Instead, the paste is pumped into digestion tanks that are filled with a
Aqua Metals claims its water-based modular AquaRefining process is cleaner, more cost-effective and more energy-efficient than smelting.

The AquaRefining process generates primary lead ingots, lead-acid-battery-grade lead alloy ingots, clean plastic chips that are recovered from the battery casings and sulfuric acid.
In late 2016, Cotton told Recycling Today he envisions AquaRefineries being located next to lead-acid battery manufacturers, allowing the manufacturers to verticalize their operations.
The partnership
“Our partnership with Johnson Controls is a tremendous step forward and is an opportunity for us to work with the global leader in automotive battery manufacturing and responsible recycling,” Stephen Clarke, chairman
Johnson Controls, which already has vertically integrated its operations to include recycling, is the first company to license AquaRefining technology. Under the terms of the agreement, Johnson Controls will supply Aqua Metals with batteries to recycle as a service as part of the Johnson Controls closed-loop network and will purchase AquaRefined metals produced from Aqua Metals’ facilities. The battery manufacturer also has acquired 4.9 percent of Aqua Metals’ outstanding shares.
Regarding Johnson Controls’ stake in Aqua Metals, Parmenter says, “We expect this to grow over time as Aqua Metals’ capacity increases.”
“Our partnership with Johnson Controls is a tremendous step forward and is an opportunity for us to work with the global leader in automotive battery manufacturing and responsible recycling.” – Stephen Clarke, Aqua Metals
The two companies are working to develop the blueprint for how and where Johnson Controls will use the technology going forward, he says. “The initial focus will be in North America, but the agreement also includes Europe and China. As Aqua Metals continues to prove out this technology in its own plants and we develop the blueprint, we will explore these questions.”
Parmenter says the AquaRefining process will supply less than 5 percent of the company’s recycled lead needs initially. “We expect this to grow over time as Aqua Metals’ capacity increases.”
He continues, “The lead will be used in a portfolio of Johnson Controls’ products and will be initially sent to facilities on the West Coast with
Recycling’s role
In fiscal 2016, Johnson Controls supplied nearly 152 million automotive batteries. “You can say 1 in every 3 vehicles is powered by Johnson Controls,” Parmenter says.
He adds that the company’s batteries are made from more than 80 percent recycled content.
“Johnson Controls’ recycling system has helped make automotive batteries the most recycled consumer product in the world,” Parmenter says. “[In 2016], our system recycled 8,000 batteries every hour—making us the world’s largest recycler.
“We are proud of our current recycling footprint and continue to invest to ensure we are leading in this space,” he says.
Up to 99 percent of conventional lead-acid automotive batteries can be recycled, Parmenter says. “The plastic can be recycled into new battery cases. The electrolytes can be reused or made into detergents. Metals can be used to make new batteries. In fact, the metals in conventional batteries are the most recycled materials in the world—more than paper, glass
He continues, “Working with companies like Aqua Metals is part of our broader strategy to invest in new technologies, building our commitment to
Get curated news on YOUR industry.
Enter your email to receive our newsletters.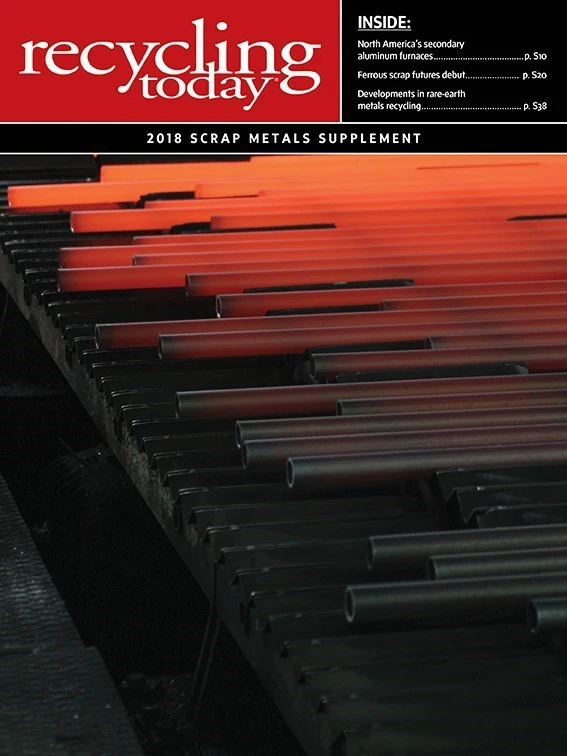
Explore the January 2018 Scrap Metals Supplement Issue
Check out more from this issue and find your next story to read.
Latest from Recycling Today
- Athens Services terminates contract with San Marino, California
- Partners develop specialty response vehicles for LIB fires
- Sonoco cites OCC shortage for price hike in Europe
- British Steel mill’s future up in the air
- Tomra applies GAINnext AI technology to upgrade wrought aluminum scrap
- Redwood Materials partners with Isuzu Commercial Truck
- The push for more supply
- ReMA PSI Chapter adds 7 members