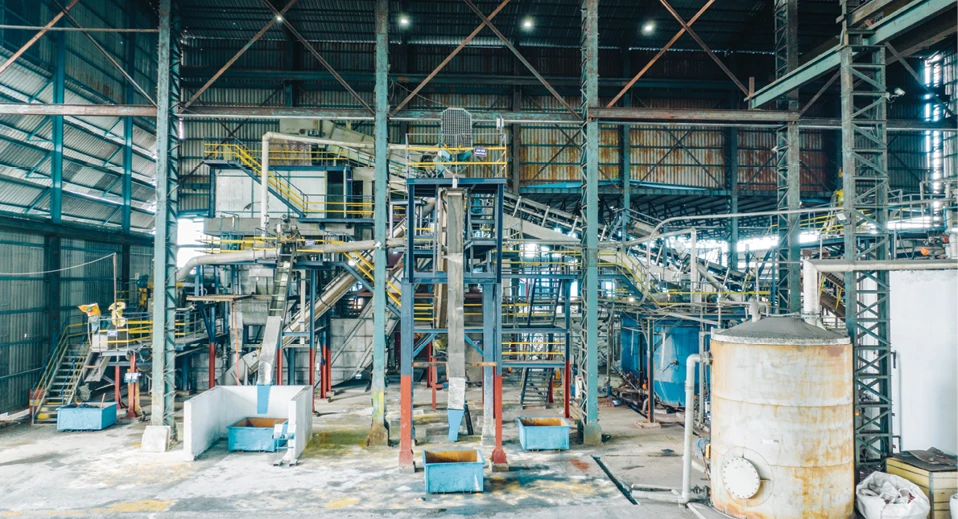

The Jain Metal Group has its roots in the 1950s, when the company’s founding family installed its first copper and copper alloy rolling mill in the south of India.
The Chennai, India-based company continues to be a leading player in the red metals sector and has followed up on that success in many ways. A critical one that has been important to North American nonferrous metals processors, members of the Jain family say, was establishing a lead plant with two 5-ton-capacity rotary furnaces in 2013.
Now, slightly more than one decade after that step was taken, the Jain Resource Recycling Pvt. Ltd. (JRR) business unit is the largest lead recycler in India, having raised its production capacity to around 180,000 tons annually. Additionally, JRR was named as The Best Performer in Non-Ferrous for 2022-23 by the Indian Institute of Metals.
“The mission is to provide efficient and environmentally responsible lead recycling solutions, contributing to a cleaner and healthier planet,” says Kamlesh Jain, managing director of Jain Metal Group.
The JRR factory-produced refined lead ingot is “unquestioned on a global level,” says Mayank Pareek, another of the firm’s managing directors. He notes the JRR 9997 lead ingot brand has been London Metal Exchange (LME) registered since 2023.
As well, JRR and its facility hold ISO 9001, ISO 14001 and ISO 18001 certifications, attesting to its adherence to quality standards, environmental standards and compliance with industrial health and safety regulations.
Jain and Pareek say JRR also is actively engaged in community outreach, with contributions to the Chennai community including efforts to educate and encourage individuals and businesses to participate in responsible battery disposal and recycling.

“Jain Resource Recycling Pvt. Ltd. practices aim to minimize environmental impact, preventing soil and water pollution and reducing carbon emissions associated with lead-acid battery disposal,” according to the company.
At the same time the company is focused on its home community, JRR reaches out to the world in its raw material sourcing activities.The company interacts with traders and processors around the world in its quest for scrap grades that include lead acid battery scrap (ReMA, or Recycling Materials Association, formerly the Institute of Scrap Recycling Industries, grades rains and rink), lead-copper cable scrap (relay), automotive wheel weight scrap (ropes), lead parts obtained from various end-of-the-life items (radio) and lead dross (rents).
Initially, JRR focused on sourcing lead scrap within India. Recognizing the JRR’s environmentally friendly way of recycling, in 2015 the government of India allowed the company to import lead scrap and lead-acid battery scrap.
Subsequently, JRR has tapped into the extensive network of Jain Metal Group internally recognized scrap suppliers, and it quickly developed sources of lead scrap and end-of-life lead-acid batteries from processors and traders the world over.
Initially, JRR focused on sourcing end-of-life lead-acid batteries and battery plate scrap. After adding the procurement of wheel weights, range, radio, rent and other grades, the company developed processes for processing lead copper cables. Now, JRR is India’s largest importer of lead copper cables, including relay.
Thanks to its ability to innovate and diversify, by 2019 JRR attained the capacity to produce 3,000 tons of lead ingots per month. After 2019, it accelerated its pace of growth and successively planned multiple expansion of smelting and refining capacities to reach its current production of 13,000 tons per month.

Along with the company’s rapid production growth throughout the past five years came the challenge of sourcing scrap to keep pace. During that time, JRR increased its sourcing base to 80 countries in North America, East Asia, the Middle East, the Pacific, Africa, Europe and the Caribbean.
Currently, JRR is procuring more than 15,000 tons of various types of lead and lead-acid battery scrap each month. That volume includes wet lead acid-battery scrap (rink), which was not allowed to be imported into India for many years. “JRR recently has become the first company in India to get permission to import rink,” Pareek says.
On the finished product side, JRR started its lead operations by making refined lead ingot with 99.97 percent purity. Later, the company evolved its raw materials and refining technologies and started making refined lead ingots with purity of up to 99.99 percent.
In 2018, JRR started making alloys and currently makes lead-tin alloys, lead-antimonial alloys, lead-calcium alloys and others. The expansion and diversification projects in lead and aluminum alloys have allowed the company to enjoy robust sales growth, with a 40 percent compound annual growth rate (CAGR) over the past five years.
With a global network of quality suppliers and attention to the quality of its metals and alloys, JRR says it has expanded its refined metals customer base to include buyers in more than 10 countries, including Korea, Japan, Malaysia, Europe, Turkey and the United States.

The rapid establishment and growth of JRR in the lead sector is emblematic of the focus on quality production and trustworthy trading that has made Jain Metal Group a preferred trading partner for recyclers around the world.
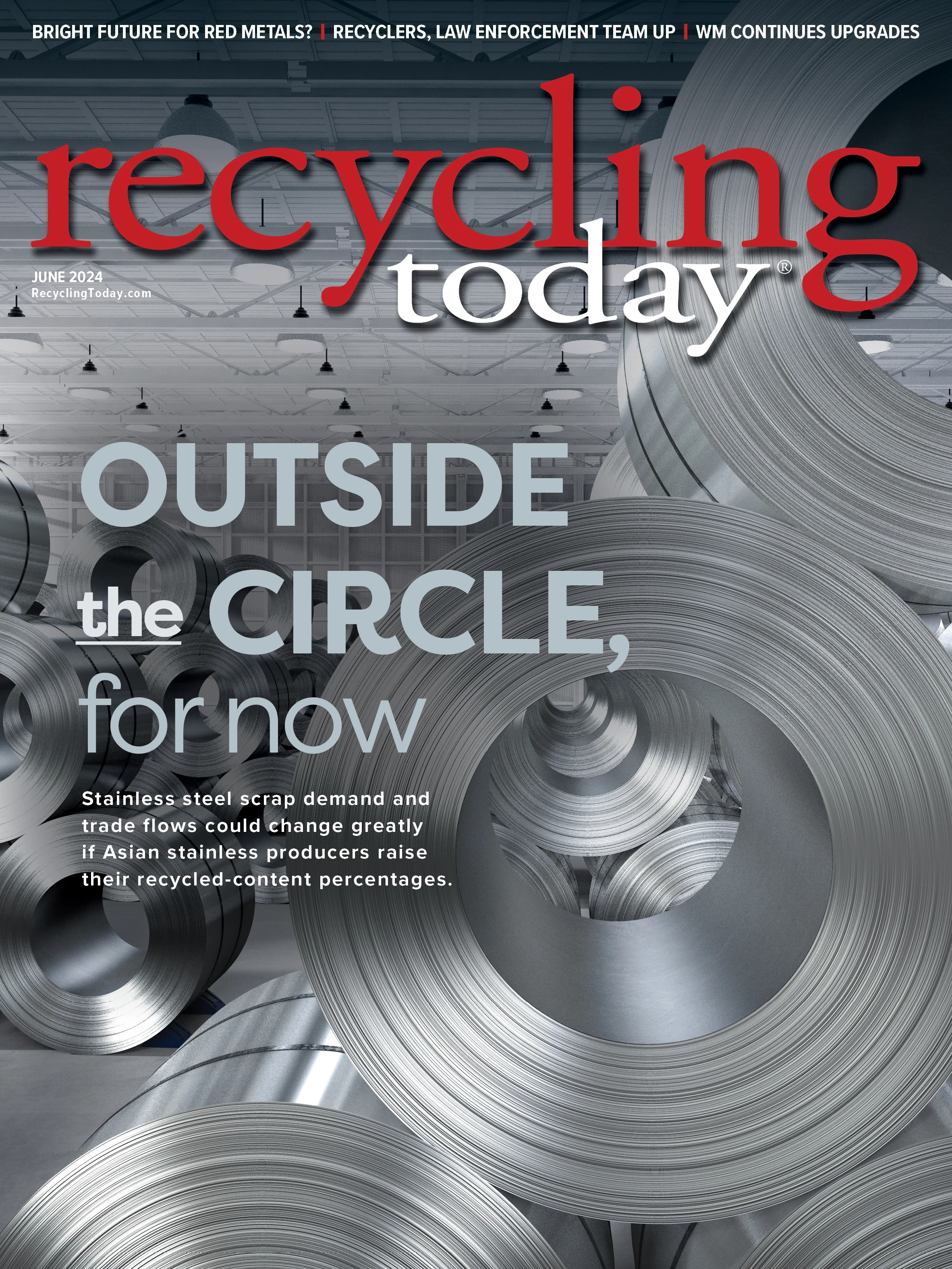
Explore the June 2024 Issue
Check out more from this issue and find your next story to read.