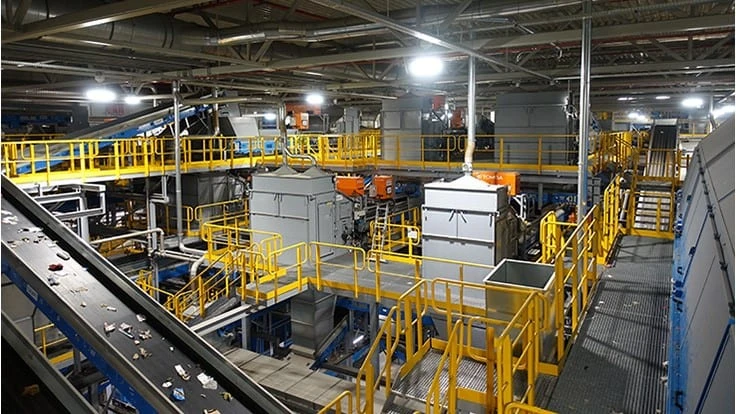
Photo supplied by Tomra Systems ASA.
The Tomra Recycling business unit of Norway-based Tomra Systems ASA says a system it has supplied to a Norwegian sorting plant has demonstrated that mixed waste sorting prior to disposal can be “a superior solution to separate collection.”
According to Tomra, since the district in Norway served by the plant stopped the separate collection of plastic in its region and deployed a mixed waste sorting system, the facility increased material recovery rates from 28 percent to 82 percent and achieved a recycling rate of 56.4 percent, “thus meeting the EU’s 2025 recycling targets ahead of time.”
Tomra says the IVAR district now “ranks first in processing MSW [municipal solid waste] by volume.”
Situated in Forus in southwest Norway, IVAR manages all residue and waste collection from 10 municipalities with an approximate population of 325,000. With its MSW sorting plant, IVAR now recovers high volumes of recyclable materials before incineration, “reducing CO2 emissions and global dependency on virgin material by supplying high-quality recycled content for new products and packaging,” states technology supplier Tomra.
When local and international recycling targets became increasingly stringent, IVAR recognized the need to improve its waste management and recycling methods. The company sought the advice of Tomra to identify opportunities in mixed waste sorting the plant sent MSW samples from the region to Tomra’s test facility in Germany.
There, analysis showed that whereas paper recovery from its MSW streams performed reasonably well, plastics recovery offered room for improvement. Test analysis unveiled that the household waste contained high volumes of plastic recyclables, even though they were meant to be collected separately.
Based on that analysis, Tomra recommended the construction of a new fully automated mixed waste sorting plant consisting of new facilities for plastics reprocessing and paper sorting, as well as the elimination of separate plastics collection in the region.
Previously collected separately, plastics are now also disposed of in the curbside collection system gray bin and recovered in the new facility. As a result, only the plant’s residues are transported to a waste-to-energy plant, says Tomra.
In late 2014, the plant building project began with Bergisch Gladbach, Germany-based Sutco Recycling Technik chosen as the supplier for IVAR’s combined residual waste and paper sorting plant. Sutco, in turn, selected Tomra Recycling as project partner for sorting equipment. Since the new facility started operation in January 2019, 22 of Tomra’s Autosort sorting units now sort plastics (PET, PS, LDPE, HDPE, PP) and paper (mixed paper, cardboard, beverage cartons) out of what is collected in the region’s gray bins. In addition, metals (aluminum, steel) are recovered.
In the system, collected material larger than 350 millimeters, or mm, (13.75 inches) are sorted by a finger screen and shredded into smaller pieces before two drum screens separate the material into three target sizes: less than 60 mm (less than 2.35 inches); 60 to 150 mm (2.35 to 5.9 inches); and 150 to 320 mm (5.9 to 12.6 inches).
In the next step, Tomra’s Autosort machines recover 90 percent of the mid-sized (2.35 to 5.9 inches) and the large (5.9 to 12.6 inches) plastic fractions before they extract mixed paper. Finally, magnets and eddy currents remove both the nonferrous and ferrous metals, says Tomra.
After plastics have been presorted, they are further sorted by material type. First, ballistic separators separate plastic film and rigid plastics. Afterward, 14 Autosort machines undertake the separation of rigid plastics into PP, HDPE, PS, PET and create a clean fraction of LDPE plastic film.
To further increase purity levels, the clean material fractions undergo a second sorting step, also carried out by Autosort machines, to remove the remaining contaminants. PS and PET considered high-quality end fractions are baled and sent to different mechanical recycling plants in Europe. LDPE, HDPE and PP are washed, dried and pelletized in the IVAR Forus plant and sold as pellets.
Sponsored Content
Redefining Wire Processing Standards
In nonferrous wire and cable processing, SWEED balances proven performance with ongoing innovation. From standard systems to tailored solutions, we focus on efficient recovery and practical design. By continually refining our equipment and introducing new technology, we quietly shape the industry—one advancement at a time.
The mixed paper fraction, as well as mixed paper and cardboard infeed coming from separate collection, is processed in a separate sorting line. From the more than 23,000 metric tons of paper sorted per shift, 95.7 percent of the infeed material is turned into four salable paper products, including a de-inking grade, OCC, Tetra Pak and other cartons.
“We have been delighted to be given the opportunity to consult with IVAR in the planning of e new plant, provide our latest sensor-based sorting equipment and accompany such an exciting and game-changing project,”, says Oliver Lambertz, a Tomra Recycling vice president. He says the following targets have been met: sort nearly all PE, PP, PS or PET plastics suited for (mechanical) recycling; sort 95 percent of the fractions identified; and realize purity rates of 95 to 98 percent.
Comments Rudolf Meissner, a supervisor at IVAR, “Tomra’s sorters and consultancy convinced us right from the beginning. As we have experienced first-hand, they are an essential tool for automated waste sorting, running high throughput and generating high yield and purity levels alike – the goal all sorting plants are pursuing and the reason why these machines definitely belong in any modern sorting and recycling facility. Combined with their reliable service, we could turn our waste sorting process into a cost-effective and competitive activity.”
Get curated news on YOUR industry.
Enter your email to receive our newsletters.
Latest from Recycling Today
- USTR announces phased measures designed to address China’s shipbuilding dominance
- APR, RecyClass release partnership progress report
- Clearpoint Recycling, Enviroo sign PET supply contract
- Invista expanding ISCC Plus certification program
- Redwood partnership targets recycling of medium-format batteries
- Enfinite forms Hazardous & Specialty Waste Management Council
- Combined DRS, EPR legislation introduced in Rhode Island
- Eureka Recycling starts up newly upgraded MRF