
Buyers of shredded metal grades expect a tightly specified product that can meet their melt shop chemistry requirements. Shredding plant operators know the daily changes to their infeed make meeting those specifications an ongoing challenge.
Separation technology provider Eriez regularly works with its customers to solve singular, identified sorting challenges. The company’s Recycling Market Manager Mike Shattuck says those same customers can benefit greatly when they engage with Eriez in a start-to-finish review of their infeed, shredding and downstream systems.
“As with many processes, where a problem shows up is rarely where it originated from,” Shattuck says. “It is always good to look at the entire process and rectify an issue or problem where it originates. To do this, as a technical sales engineer, you must understand the complete shredding and metals sorting process.”
In the shredding process, while Eriez does not provide equipment specifically for feeding a shredder, Shattuck says, “The old saying ‘garbage in, garbage out’ stands true with car shredding. If operators have a poor mix of feedstock, they may overload the magnetic drums downstream with an abundance of fluff that will cause frag to be too dirty or have an adverse effect on the recovery.”
When it comes to their ferrous shred, shredding plant operators are open to advice and solutions that can lower the copper content of that end product. “It has become quite common that steel mills will pay a premium for low-copper shred. To reduce copper in shredded steel, Eriez relies on scrap drums, specifically our high-strength PRex drums, and a ballistic separator,” Shattuck says.
“In the recycling market alone, Eriez has developed 12 new products in the last 10 years.” – Mike Shattuck
The Eriez Shred1 ballistic separator can be configured into a wider downstream sorting process. “Material is presented to the high-speed ballistic separator after the scrap drums,” Shattuck says. “The less magnetic material, (copper-bearing, debris, irony aluminum) is affected more by the ballistics of the high-speed belt than the attraction of the magnetic in the head pulley of the conveyor and are thrown over a splitter.”
Investments in nonferrous shredded metals also have intensified in the auto shredding sector, and Eriez has been involved from the beginning. In recent years, upgrading zurik to zorba has been a key process improvement offered by Eriez.
“In working through this development, it was determined that if zurik is shredded on a small ring mill, further downstream separation can take place, leaving the processor with a more saleable product,” Shattuck says. “The process has proven to provide an attractive and quick ROI for the customer.”
The zurik-to-zorba upgrade technology is emblematic of the Eriez approach. “In the recycling market alone, Eriez has developed 12 new products in the last 10 years that are changing the way shredder plants are producing their product,” Shattuck says. “With these new products and processes, we are able to develop increasing revenue for the customer.”
Descriptions of the Eriez product line for metal recyclers can be found at www.eriez.com/Recycling.
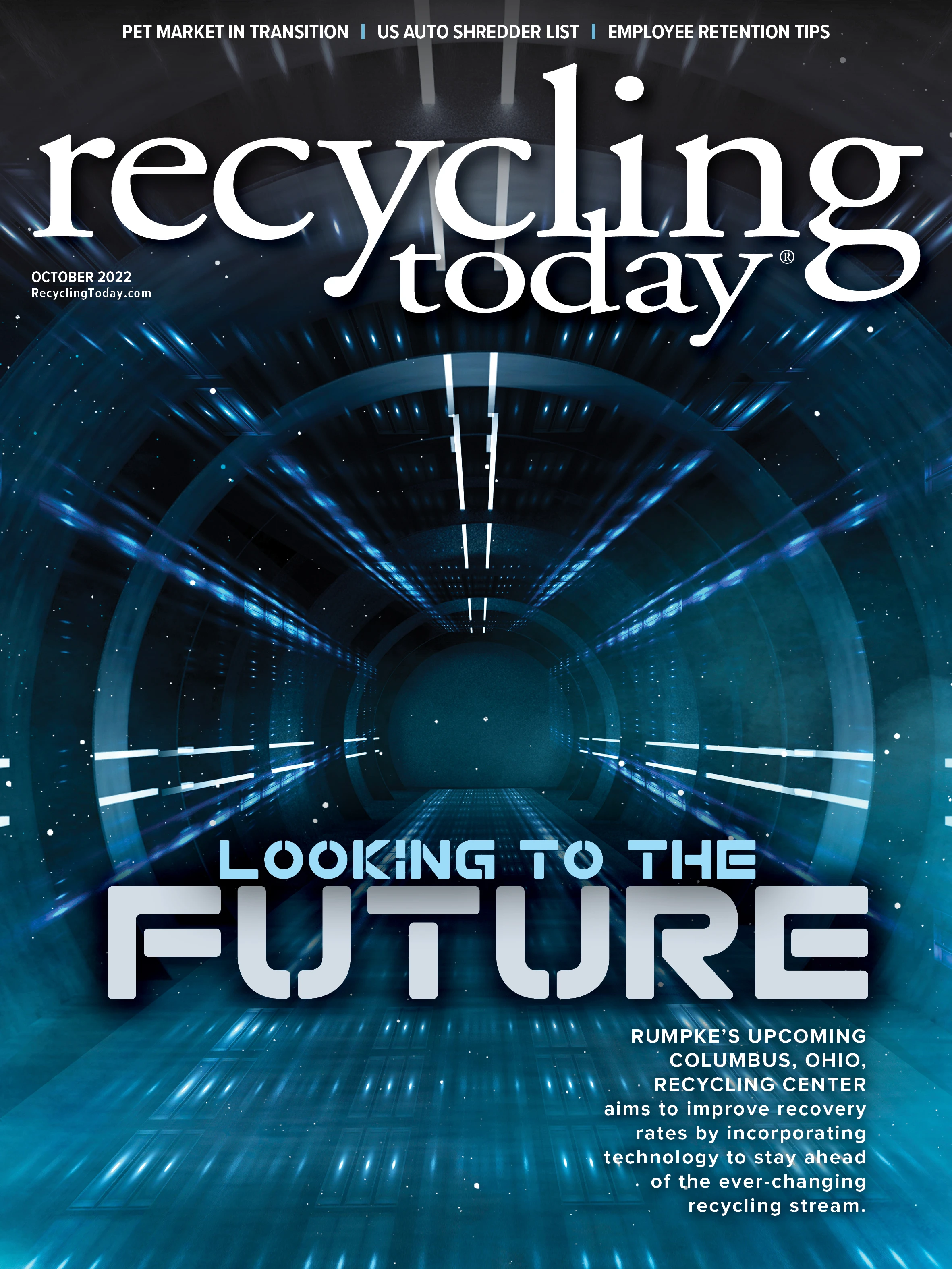
Explore the October 2022 Issue
Check out more from this issue and find your next story to read.