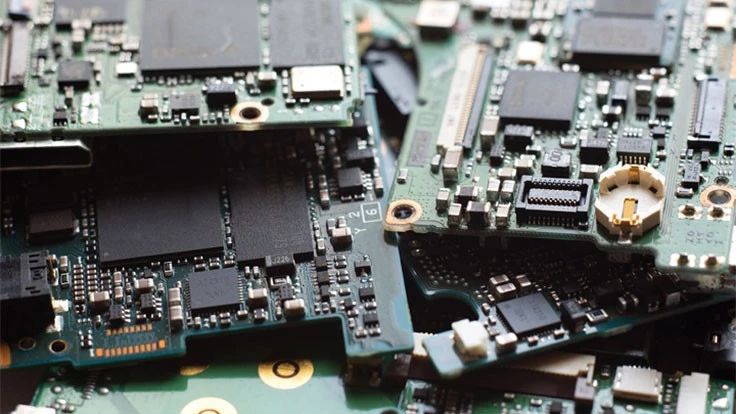

Itronics Inc. and its President John Whitney have always envisioned a clean, waste-free planet. Over the years, they’ve translated that vision into innovative, practical and money-making applications.
Whitney is best known for inventing a method for separating silver and other precious metals from spent photographic liquid. Itronics uses the demetallized fluid to make micronutrient-rich fertilizers at its Reno, Nevada, plant, while the metals are turned into bullion and sold to refineries. Additionally, the glass slag produced in Itronics’ refining process can be used to manufacture commercial products, such as decorative tile.
Expanding into e-scrap
Itronics is not standing still. Within the last four years, the company has developed a way to reclaim precious metals—including gold, silver and palladium—as well as copper and tin—from discarded computer circuit boards. It has simply added the e-scrap as infeed material for its refinery process.
In that process, silver is not only recovered from photographic waste, but its chemical makeup allows it to soak up metals from circuit boards during furnace refining. The metals then become ingredients in the company’s bullion.
Because of this e-scrap breakthrough, Itronics is buying more furnaces to ramp up bullion production and will eventually bring in larger furnaces. Whitney has even modified a furnace so that it burns latent heat energy from copper in circuit boards, reducing outside energy needed to power the furnace by more than 50 percent.
For that furnace innovation, Whitney and Itronics won an award from NV Energy, a Nevada public power company, in 2016.
“Our company will never be the same again because the amount of e-scrap is unlimited,” Whitney says. “It’s a nonseasonal business, and it can be expanded in small steps continually. It’s a new revenue source for us, and we can grow it at a rate we can manage.”
Capturing metals from e-scrap is part of Itronics’ overall mission to reclaim 100 percent of all materials it processes, converting everything into salable goods. Itronics calls itself a “zero-waste green technology company.”
“Dr. Whitney imagines a world without waste, and he’s been able to do that through zero-waste technology,” says Jeff Baclet, Itronics spokesman. “The only discharge from our factory is if someone uses the restroom.”
Whitney says other businesses, and even the government of China, have tried to replicate his processes, to no avail.
Itronics is moving forward on other fronts, as well. This year the company purchased a centrifuge, which uses centrifugal force to separate solids from liquids in a spinning container. The machine, which the company first tested in November 2018, will decrease the time it takes to separate liquids from solids from about five months to two or three weeks.
Meanwhile, Itronics is buying a 54,000-square-foot building on 48 acres in Wabuska, Nevada, where it plans to expand operations. The company’s existing Reno plant is 35,000 square feet in comparison. Whitney says it will take about two to three years to get the plant up and running.
“What we’re doing hasn’t been done before in this manner,” Whitney says. “It’s all pioneering.”
Silver separation
It was in the 1970s that Whitney, who holds a doctorate in mineral economics and a master’s degree in mineralogy, invented a proprietary chemical process that could separate silver from a silver-and-gold-bearing cyanide solution. It was done through his company Whitney & Whitney Inc. in Nevada.
It was no surprise when, in 1986, Reno and its neighboring city, Sparks, turned to Whitney for help with a silver problem. Spent photographic liquids from one-hour photo shops and from X-rays taken at dentist offices and hospitals were ending up in the Truckee River and Pyramid Lake, both prominent fisheries.
The photographic liquids contained silver, which is toxic to fish, and nitrogen, which in large quantities is unhealthy for them. The local wastewater treatment plant was unable to remove all the silver and nitrogen from the liquids.
Whitney, using the proprietary chemical process he invented years earlier, was able to filter out nearly 100 percent of the silver, along with iron and sulfur, from the photographic liquids. By doing so, he saved Reno and Sparks millions of dollars the cities would have had to spend on a new treatment plant.
For that accomplishment, Whitney won an inventor-of-the-year award from the University of Nevada. He also placed second in the 2005 Worldwide Environmental Awards, presented by the Institution of Chemical Engineers, based in the U.K.
But Whitney wasn’t finished. He wanted to find a commercial use for the silver, iron and sulfur that, in sludge form, would be separated from the photographic liquid. He dried the sludge, placed it in a furnace reaching 2,100 degrees F and produced nearly 100 percent pure silver bullion. The iron and sulfur made up glass slag, a byproduct in the process.
In 1988, Whitney established Itronics to buy Whitney & Whitney and take the firm public. Itronics initially specialized in collecting and treating photographic waste. The timing was right, because in the early 1990s, the U.S. Environmental Protection Agency said spent photographic liquid containing silver was the country’s largest hazardous waste stream.
Focused on fertilizer
In 1990, Itronics started developing its Gold’n Gro liquid fertilizers, using the liquid that was almost entirely demetallized in photographic waste. Trace metals, along with sulfur and nitrogen, remaining in the liquid are nutrients that are good for people, plants and soil, Whitney says.
“It was trial and error, failure after failure. In the process you become specialized in failure analysis. You have to have a tremendous amount of patience.” – John Whitney, Itronics Inc.
“People need micronutrients like zinc, copper and iron in tiny supplements in their diets,” Whitney says. “Animals and plants have the same needs. So, we are supplying zinc, iron and manganese to the plants. Many other fertilizers in the market are phosphate-based with non-nutrient metals, like cadmium and arsenic. Non-nutrient metal content is very low in our fertilizers.”
Whitney adds that Itronics’ fertilizers deliver chemicals more efficiently to plant roots, so less product is needed, which in turn means less risk for groundwater contamination.
Also, Itronics’ fertilizers improve crop yields, especially for almond-tree farmers. Whitney says when California experienced droughts in recent years, and the state rationed water to farmers, the production of one almond-tree grower using Gold’n Gro was comparable to prewater-rationing days.
Whitney says it took Itronics about 15 years to develop, test and market 11 fertilizers. Today, the company’s fertilizers account for between 85 and 90 percent of its sales.
Some like it hot
About five years ago, Baclet, who co-owns a computer business, was hearing from his customers that computers contain a significant amount of gold—if there was only a way to remove it.
_fmt.png)
One day in June 2014, Baclet lined up a few discarded computer towers on a conference table and asked Whitney if it’s possible to reclaim the gold inside them. Whitney believed temperatures were high enough in Itronics’ furnaces to conduct a test with the circuit boards.
A long series of tests followed, with Whitney trying to determine if it was technically and financially feasible to add e-scrap as an infeed material.
“It was trial and error, failure after failure,” Whitney says. “In the process you become specialized in failure analysis. You have to have a tremendous amount of patience. You have to be psychologically able to cope with failure.”
After two-and-half years, Itronics reclaimed 1.5-ounce button-size pieces of metal from the e-scrap.
“Once we got that, I said it looks like we can make it work,” Whitney says.
The e-scrap recycling works like this: Itronics takes the silver-iron-sulfur sludge that, during Whitney’s proprietary chemical treatment, is separated from photographic waste. Instead of placing the sludge directly into the furnace to create bullion, Itronics separates the silver from the iron and sulfur through leaching, a slow process that involves dissolving the metals in liquid. A filter press then separates the powdered silver from the liquid.
Meanwhile, circuit boards are dropped into a shredder and then into a grinder so the pieces are small enough for the furnace. When the silver is finally separated from the iron and sulfur, the silver powder and e-scrap are slid into the furnace, where they are heated for about 20 hours.
Inside the furnace, the silver soaks up metals like gold, palladium, copper and tin in the e-scrap. The molten-metal mix is poured into a mold and cooled, and the metals sink to the bottom of the mold, forming a bullion puck. The mold is cracked open with a sledgehammer, and the multimetal puck is removed.
Itronics then re-melts four metal pucks to create one 4-pound bullion bar, ready for sale and shipping to a refiner, which separates the valuable metals. The iron and sulfur separated from the silver during leaching are used to make Itronics’ fertilizers, and glass slag produced in the furnace refining is sold to a copper smelter, which uses it as a flux or purifying agent.
The recovery of tin from solder in circuit boards is significant. Whitney says tin is three times the cost of copper and that the U.S. Department of Defense keeps a supply on hand because of its preciousness.
According to a December 2017 United States Geological Survey report, a 2013 Department of Defense study found that tin was in shorter supply than any other mineral. The article also reports that the United States imported 75 percent of its tin in 2015. Thanks to Itronics, the country will have a domestic tin supplier.
Of course, gold reclaimed from e-scrap is nothing to sneeze at. Baclet says that according to the “2016 Global E-waste Monitor” report, $22 billion in gold are tossed away in e-scrap every year.
“You no longer have to dig into the side of a mountain to get gold,” Baclet says.
Whitney says Itronics’ e-scrap operation is small but growing. “We’re trying to do it at a large-enough scale to make it profitable,” he says.
Endless e-scrap
Whitney says the new centrifuge will shorten Itronics’ process for separating silver from the leaching liquid containing iron and sulfur. After leaching, instead of placing the dissolved material in a filter press, the company will separate the silver, iron and sulfur from the liquid in the centrifuge, which will cut the time it takes to process e-scrap by 85 percent.
Meanwhile, Itronics is exploring adding spent silver-bearing batteries and alkaline batteries as infeed materials. The company also is testing whether it can liquefy copper for direct injection into its fertilizers so it doesn’t have to buy liquid copper.
As for photographic waste, Baclet says it’s here to stay, despite growth in digital photography. Some applications, such as X-rays, still demand conventional photography, while some people believe digital photos lose quality and clarity over time.
If true, the future looks picture-perfect, in a silver and gold frame, for Itronics.
Get curated news on YOUR industry.
Enter your email to receive our newsletters.
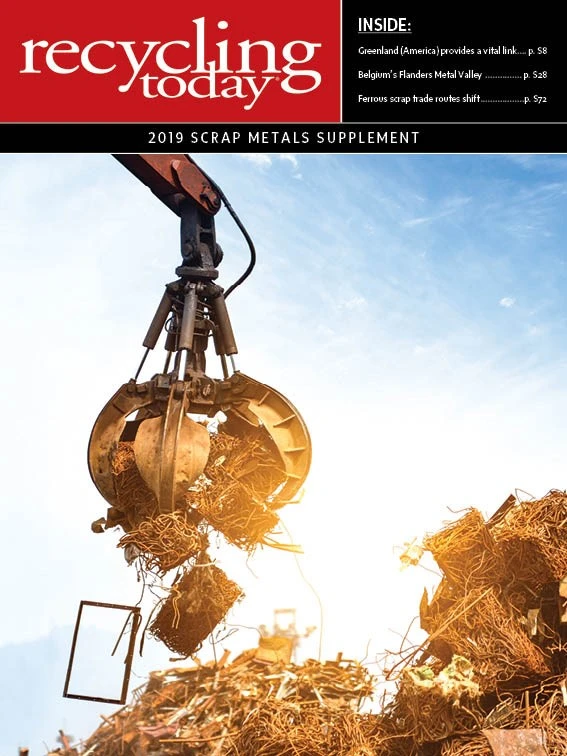
Explore the January 2019 Scrap Metals Supplement Issue
Check out more from this issue and find your next story to read.
Latest from Recycling Today
- AF&PA report shows decrease in packaging paper shipments
- GreenMantra names new CEO
- Agilyx says Styrenyx technology reduces carbon footprint in styrene production
- SABIC’s Trucircle PE used for greenhouse roofing
- Hydro to add wire rod casthouse in Norway
- Hindalco to invest in copper, aluminum business in India
- Recycled steel price crosses $500 per ton threshold
- Smithers report looks at PCR plastic’s near-term prospects