Over the past 25 years, the number of environmental regulations in the United States has increased exponentially. Today, the Environmental Protection Agency, Washington, administers about 14 major and hundreds of minor statutes, covering more than 10,000 regulations. Each regulation requires some form of corrective action, such as pollution control or abatement, which affects the bottom line of thousands of companies. The cost of environmental compliance by U.S. industry has been estimated by the EPA to be $122 billion per year.
Now there are international environmental standards, as well. The International Organization for Standardization, Geneva, mostly confined itself to issuing technical and safety standards until about a decade ago when it began branching out. First, it developed the ISO 9000 standards – international quality control standards for products and services. Then in 1993, the organization turned its attention to environmental management systems. Besides improving environmental protection and performance, the resulting EMS standards – known as ISO 14000 – are expected to provide a credible alternative to traditional command and control regulation. They address systems and continuous improvement tools for all types of organizations, including companies in the manufacturing and service industries.
Although they have been approved, the standards have not yet been officially released except in draft form. When final, ISO 14000 standards could give companies easier access to markets in other countries by eliminating trade barriers imposed by conflicting national and regional EMS standards.
The goal of ISO 14000 is to improve global environmental conditions by motivating greater environmental compliance by businesses, government departments and nonprofit organizations. Two key objectives are to integrate environmental management systems and product life-cycle thinking with economic priorities, and to establish environmental standards that rely on market competition among organizations that each wish to be seen as having the best environmental compliance.
The standards are being developed by ISO Technical Committee 207, which consists of representatives from 41 participating and 14 observing national delegations. The ISO Tag Group currently has approximately 477 members, including representatives from industry, government, trade associations, environmental groups, law firms, and consulting firms, as well as private individuals. In early 1996, representatives from 102 countries voted to adopt the ISO 14000 – ISO 14001, the EMS guideline and standard, respectively. Forward-looking companies, recognizing the reality of ISO 14000 (as the generic series of documents is commonly known) are planning for the advent of the new global environmental standard.
Although U.S. scrap processors have not yet implemented the standards, many companies in the Pacific Rim are proceeding under the draft standards, and the German government has already mandated that any company that wants a German government contract must be ISO 14000 certified.
COMPETITIVE ADVANTAGE
Many companies are already elevating environmental management to critical business status, considering it an avenue to competitive advantage. Competitive advantage can be described as a mixture of attributes, both perceived and substantive, that make an enterprise unique and give it an edge over others. New business areas, total customer involvement, research and development, marketing activities, sales campaigns, re-engineering and cost-cutting are tactics that can help a company achieve competitive advantage. Strategic environmental management integrates these tactics with environmental management policies, achieving a competitive advantage while improving aggregate environmental impact.
Sustaining competitive environmental advantage requires a continual cycle of impact, evaluation and improvement. Market forces can achieve environmental improvements independent of regulation in three ways. First, organizations having market power and subscribing to the tenets of ISO 14000 will influence suppliers to adopt ISO 14000 as well. Secondly, large organizations will add value for their small and medium-size customers by conforming to ISO 14000. Finally, companies in particularly competitive industries will seek stakeholder and customer good will, resulting in market advantage, by publicly declaring environmental goals and objectives and periodically disclosing environmental audit results.
DEVELOPING STRATEGIES
Just as companies have developed standards for everything from nuts and bolts to accounting practices, international standards for environmental management and protection systems will eventually be commonplace. But in the short term, what is the best strategy for determining if ISO 14000 is a good idea for your company to adopt?
The first major consideration is the relevance of ISO 14000 to your particular industry and market. In addition, cost – and the value received for that cost – will be a factor in determining whether or not to seek ISO 14000 certification at all or for just a few of your company’s facilities or plants. Often, the best place to begin estimating potential cost is with your company’s ISO 9000 program.
For small to medium sized businesses, the cost for complying with ISO 9000 is about $30,000 to $40,000 to get started. Annual maintenance costs are significantly less. The cost of implementing ISO 14000 standards would probably be about the same. A company that has gone through the process of documenting its operations to comply with the ISO 9000 standards will have a base to start from when looking to comply with ISO 14000. Costs would include documenting current operating practices, the audit at the end of the year, and then continual improvements each year after that.
Although slow to adopt ISO 9000 quality control standards at first, members of U.S. industry have realized that compliance with these standards, albeit voluntary, has become a de facto requirement for conducting business outside the United States, especially in Europe. Moreover, a trickle-down effect has occurred as various multinational companies have required all of their suppliers to become ISO certified as well. In the metals business, auto manufacturers are gradually forcing steel mills to become ISO 9000 certified to supply them. In turn, steel mills will eventually require their suppliers – scrap processors – to be ISO 9000 certified. ISO 14000 certification will follow in the same way, although it may take a decade.
Having an ISO-certified environmental management system will help a company gain market share for a number of reasons. For one, ISO 14000 induces compliance with all applicable environmental laws and regulations, so companies that adhere to the ISO guidelines may see a decrease in future liability costs and possibly some regulatory relief in the form of reduced inspections and permitting flexibility from the EPA.
Also, proactive environmental management encourages the use of process controls and other methods to minimize waste and prevent pollution, which eventually makes the facility more efficient. Following set standards of excellence may reduce the need for comprehensive facility audits and in some cases reduces compliance costs further – for example, if a company has a program to minimize spills, there won’t be the cost to clean up spills later. And a combination of operational efficiency, reduced environmental liability and regulatory relief favorably impacts the bottom line, allowing companies to become more competitive in both the domestic and global marketplaces.
BUILDING A TEAM
Since complying with ISO 14000 will involve input from multiple departments throughout your company, your first order of business should be to tap the right talent in your firm. Your chance of success without multi-disciplinary support is remote. Furthermore, to singlehandedly build a business case for ISO 14000 without interdisciplinary input could potentially alienate others at the company.
In evaluating the ISO 14000 issue, think of yourself as a coach who must build and lead a team to complete this task successfully. You need to amass support from people in key areas who can provide valuable input as you try to determine the potential risks and rewards for implementing ISO 14000. Marketing and operations experience will be critical to estimate the potential costs associated with the standardization of environmental procedures to gain ISO certification.
Start by considering all of the stakeholders in this important matter. On the production side, this includes business unit managers, line executives, and facility management. Other stakeholders include regional and divisional staff, quality program managers, and site environmental health and safety coordinators. It is particularly important to consider downstream or post-production stakeholders such as marketing and public relation managers, along with customers, vendors, stockholders, and the community.
For your facility, operations people will play a key role. However, it is important that you enlist a project champion, someone high up in the organization, who can take ownership of the ISO 14000 effort. Following the sports team analogy, this person is akin to the ball club owner and will be a vital resource in giving your case the attention it deserves throughout the company. The project champion should have the power and visibility to marshal the substantial resources needed to gain ISO 14000 certification.
With your team assembled, you can begin to ask fundamental questions about your company’s operations. The first question you must ask is: what would be the advantage of implementing an EMS such as ISO 14001 for my company? The answer is that having an EMS can help an organization provide confidence to its interested parties by ensuring that policies, objectives, and targets are met; that emphasis is placed on prevention rather than corrective action; that evidence, reasonable care, and regulatory compliance can be provided; and that the system design can incorporate the concept of continual improvement as evidenced by the proliferation of "green" advertisements and corporate environmental report cards.
With a team formed, the goal identified and the possible rewards laid out before you, the next step is to direct your team into the actual creation of an environmental management system.
CREATING AN EMS
The components of an environmental management system are policy, self examination, implementation, measurement and evaluation, and improvement. Policy entails the issuance of a directive from the highest level of management identifying improved environmental performance and establishing an EMS as a commitment of the organization. The policy should articulate, in general terms, the organization’s commitments and goals. For example, the policy may be to achieve compliance with existing regulations, improve energy efficiency, conserve raw materials, reduce the volume and toxicity of waste streams, and alter procurement protocols. The policy may be in the form of a public document – spelled out clearly in annual reports of publicly owned companies or an advertising campaign – as well as being circulated internally.
Then, to accomplish the policy commitments, an organization will need to perform a rigorous self-examination. This will entail cataloguing environmental regulations and standards that apply to the organizations’ operations, products, and services. The company will need to identify how and to what extent activities, products, and services may have either beneficial or detrimental impacts on the environment; compare the organization’s present environmental performance with the applicable standards and regulations; and review its procurement and contracting policies. Then, with a baseline of information in hand, the organization should establish specific performance targets and objectives and a schedule for achievement and review.
For example, one of the goals in the EMS for a company that shreds cars could be to reduce waste leaving the auto shredder. This company might develop a program to do secondary recovery and recover more of the nonferrous from the auto shredder residue.
To implement the plan and achieve its target, it will be necessary to allocate or acquire additional, adequate resources. These would include, for example, personnel, materials, equipment and funding. In addition, it will be necessary to conduct training for raising awareness about the targets and ensuring competency as far as attaining them, to establish procedures and protocols for documenting implementation, to create compliance maintenance records and to establish procedures for response to potential emergencies.
Periodically, the organization will need to measure its progress in achieving the target objectives. In addition to monitoring and measuring performance, a system will be needed to ensure that deficiencies are corrected and performance is documented. The EMS itself should be subject to a periodic audit.
Finally, the organization must have a plan and a budget in place for correcting deficiencies identified during the self-audit process and for ensuring continual improvement of its environmental performance.
Consistent with usual ISO practices, an organization will be able to self-declare conformance with ISO 14000. However, in practice, third-party certification may be necessary to satisfy customers, stakeholders, or regulatory requirements. For the ISO 14000 families, certification is contemplated only for the EMS specification document. Thus, environmental performance, evaluation and auditing would be mandatory components of an effective EMS for an ISO 14000 organization, but it would not be required to follow ISO documentation on audits to relieve third party certification.
Furthermore, an organization could be certified without requiring its suppliers to conform to ISO 14000 (although some entities can be expected to take the extra step of requiring their suppliers to be certified). The U.S. has developed a certification infrastructure which will be available when the ISO 14000 standard is released to the public. Organizations that will set the standards auditors will use to conduct third-party certification include the American Society of Testing and Materials, Philadelphia, and the American National Standards Institute, New York.
REDUCED LIABILITY
Whether or not management systems yield improved environmental conditions, compliance with ISO 14000 EMS standards soon may be a condition of doing business. When top management commits an organization to improve environmental compliance and allocates resources to achieve that commitment, exposure to liability is reduced. By controlling waste streams and considering all the issues in your organization that have an environmental impact, your exposure to both U.S. and international regulatory and
compliance requirements will be minimized. The U.S. EPA has said if a company has an EMS in place, they can do more of the policing themselves, and the EPA is less likely to do an audit.
The environmental regulatory climate in the U.S. has forced companies to focus on managing their environmental obligations in a systematic manner. Failure to do so increases the company’s exposure to significant penalties, potential criminal action, or burdensome cleanup costs. Therefore, many companies in the U.S. have had environmental management systems in place for many years. Initially, these systems were not based on any formal standards or requirements. Rather, companies applied normal management practices to environmental issues and thereby developed an EMS that was integrated into and consistent with their existing management systems.
The U.S. government has taken notice of the relationship between the ISO 14000 EMS and compliance. The result has been several documents outlining what the U.S. government believes are key elements of a compliance assurance program. Taken as a group, these documents indicate that if a company has in good faith implemented a satisfactory EMS, the U.S. government will take less severe enforcement action in the case of environmental problems, and the resulting penalties will be lower. In some cases, a good EMS can assist a company in avoiding criminal prosecution and contribute to penalty reductions of more than 75 percent.
The ISO 14000 international standards are the wave of the future. It is not too early to get your corporate "house" in order. Compliance with these standards represents an opportunity to identify and correct weaknesses in compliance, heighten internal awareness and responsibility, and reduce the potential for penalties. With careful integration of environmental planning and other management functions, an effective EMS can reduce your overall cost of doing business.
The author is department head-engineering for Versar Inc., Lombard, Ill.
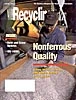
Explore the August 1996 Issue
Check out more from this issue and find your next story to read.
Latest from Recycling Today
- ReMA opposes European efforts seeking export restrictions for recyclables
- Fresh Perspective: Raj Bagaria
- Saica announces plans for second US site
- Update: Novelis produces first aluminum coil made fully from recycled end-of-life automotive scrap
- Aimplas doubles online course offerings
- Radius to be acquired by Toyota subsidiary
- Algoma EAF to start in April
- Erema sees strong demand for high-volume PET systems