
Photo courtesy of Nucor Corp.

The electric arc furnace (EAF) steel sector in the United States grew rapidly in the final quarter of the 20th century thanks in part to the country’s deep ferrous scrap reservoir. Early investors in the technology might not have paid close attention to greenhouse gas (GHG) emissions aspects of EAF production, but EAF steelmakers are keenly aware of them as of this year.
The London-based consultancy Deloitte defines decarbonization as the “term used for removal or reduction of carbon dioxide (CO2) output into the atmosphere.” Blast furnace/basic oxygen furnace (BOF) steel production has placed the sector historically at the highest levels of CO2 output, so reduction (rather than outright removal) has become the initial target.
In that effort, U.S.-based EAF steelmakers point to GHG emissions figures they say put them ahead of the game on a global basis.
Taking credit
The resource conservation aspect of using scrap metal as feedstock is a message that EAF producers have been communicating for several decades. In his letter that opens the 2003 Nucor Corp. annual report, then-CEO Daniel R. DiMicco writes, “We solidified our position as the nation’s largest steel manufacturer and the largest recycler.”
Among the largest EAF steel producers in the U.S., Texas-based Commercial Metals Co. (CMC) had scrap recycling origins before entering the steel sector, and North Carolina-based Nucor Corp. and Indiana-based Steel Dynamics Inc. (SDI) acquired large scrap companies in 2007 and 2008, respectively.
The 2015 Paris Agreement moved the GHG emissions aspects of environmental protection to the forefront. The focus on emissions ran the risk of elbowing recycling out of the conversation—at the very least, it caused EAF producers to elaborate on the relationship between recycling and reduced emissions.
Several years on, most steelmakers seem to have amplified the volume of their low-carbon messages. Quite a few also have invested to pursue lower GHG emissions.
The three large U.S.-based EAF producers, as well as one of North America’s remaining blast furnace/BOF mill operators, all have demonstrated a willingness to track their decarbonization efforts and broadcast their scores.
CMC, which produces long products predominantly used in the construction sector, touts its low-carbon production methods to potential steel products buyers. In its Net Zero Steel campaign, the company positions itself as being able to supply customers that need to reach net zero emissions targets.
“Using innovative EAF technology, all CMC steel is produced with 63 percent less greenhouse gas emissions intensity than the industry average,” CMC says.
SDI’s top executives, meanwhile, regularly emphasize that the company’s GHG emissions are lower than the industry average. Regarding its low-carbon credentials, SDI Chief Financial Officer Theresa Wagler told Recycling Today last year, “We’re the decarbonization story already—today.”
In a set of investor presentation slides released earlier this year, SDI claims a GHG Scope 1 and Scope 2 emissions rating of 0.42 for its six EAF mills. That compares with one as the steel industry average in the U.S. and an average global rating of 1.7.
“Our steelmaking operations already meet the 2050 intensity targets under the Paris Agreement and its 2 degrees Celsius scenario,” SDI says.
Cleveland-Cliffs, one of two remaining blast furnace/BOF operators in the U.S., along with Pittsburgh-based United States Steel Corp., also has made itself part of the decarbonization discussion.
The Cleveland-based company has roots in iron mining and ore processing but has expanded into steel under the leadership of current CEO Lourenco Goncalves. As with its EAF brethren, the firm also staked a claim in the scrap processing sector in 2021 when it acquired Detroit-based Ferrous Processing & Trading (FPT).
In 2021, Goncalves, whose company also operates some EAF capacity, said U.S. producers are meeting their reduced GHG emissions obligations while producers in China and elsewhere are not.
Goncalves said the steel sector in the U.S. is responsible for 2 percent of global steel industry GHG output compared with 64 percent for China. Paris Agreement noncompliance in the steel sector “doesn’t reside in the United States, it resides in China,” he added.
“China feeds off Australia, which has lots of iron ore, but Australia does not have a lot of water [needed to produce pellets],” Goncalves said. “In the U.S., our taconite mines are located on the edge of the Great Lakes, so we can produce pellets, and we do produce pellets.”
Beyond messaging, measuring with the yardstick of capital expenditures seems to demonstrate that numerous steel producers are doing more than just talking about lowering their emissions.

Changes to the north
At the start of this century, nearly 60 percent of steel output in Canada consisted of blast furnace/BOF output. The two largest mills were operated by Algoma Steel Inc. in Sault Ste. Marie, Ontario, and by the former Dofasco in Hamilton, Ontario.
In the past two years, the current owners of each of those complexes have embarked on projects to retire their blast furnaces and install EAF technology, citing decarbonization efforts in both cases.
The Algoma conversion project received an important push in May 2021 when the company was acquired by New York-based Legato Merger Corp., a special purpose acquisition company (SPAC) listed on the NASDAQ exchange.
“We continue to evaluate our strategic options, including the potential for a substantial investment in electric arc furnace steelmaking,” Michael McQuade, who was then CEO of Algoma, said as part of the acquisition announcement.
“We believe Algoma’s transformation and potential investments will allow Legato stockholders to participate in a significant value-creation opportunity,” Legato Chief SPAC Officer Eric Rosenfeld added.
Subsequently, the firm has committed to an EAF conversion project that involves installing 3.7 million tons of liquid steel capacity annually with two 250-ton EAFs at its core, according to Italy-based Danieli & C. Officine Meccaniche S.p.A., with whom Algoma signed a technology supply agreement in late 2021. The project carries an estimated $550 million price tag.
The Dofasco complex, owned and operated by Luxembourg-based ArcelorMittal, also is joining in EAF conversion. Two months after the Algoma merger announcement, ArcelorMittal announced plans to invest about $1 billion at the Hamilton complex to transition away from blast furnace/BOF steelmaking to EAF production.
While Algoma has shown a commitment to melt scrap via a joint venture with Ontario-based scrap processor Triple M Metal, ArcelorMittal intends to produce direct-reduced iron (DRI) in Hamilton.
Although recyclers might end up having a higher-volume connection to the Algoma effort, ArcelorMittal says DRI nonetheless will provide emissions benefits. In its 2021 announcement, the steelmaker says using DRI in EAF production “carries a significantly lower carbon footprint.”
Steelmakers in Mexico also are investing in EAF production to offer lower-carbon steel. In February, Luxembourg-based steelmaker Ternium SA (which makes most of its steel in the Americas) announced plans to build a 2.6 million tons-per-year EAF steel slab production facility in Mexico.
If following the money is the true path to understanding how an industry sector is trending, the EAF production method and GHG emissions-reduction goals seem to be on solid ground.
A council with heft
In addition to the statements of individual steelmakers, EAF producers are demonstrating their ability to act in concert via the Washington-based Global Steel Climate Council (GSCC), established late last year.
Nucor, SDI, CMC and the Institute of Scrap Recycling Industries, Washington, comprise four of the six founding members of the GSCC, and the council is upfront in saying scrap-fed EAF steelmaking is critical to steel sector decarbonization. The news release announcing the GSCC’s creation says much of world’s steel production is carbon-intensive because it relies on mined and processed coal, iron ore and limestone. Other steelmakers, including GSCC members, use EAFs with a principal input of recycled scrap to produce steel with “significantly lower carbon emissions.”
Nucor CEO Leon Topalian says an overriding GSCC message is that not all steel labeled as “green” is equal and policymakers should not be led to believe so.
“We have the technology to reduce carbon emissions in steel production by 70 percent today,” Topalian says of scrap-fed EAF mills. “The global industry needs to build on the innovation that has already led to cleaner steel production in the U.S., because the green and digital economies around the world are going to be built with steel, and the steel they are built with matters.”
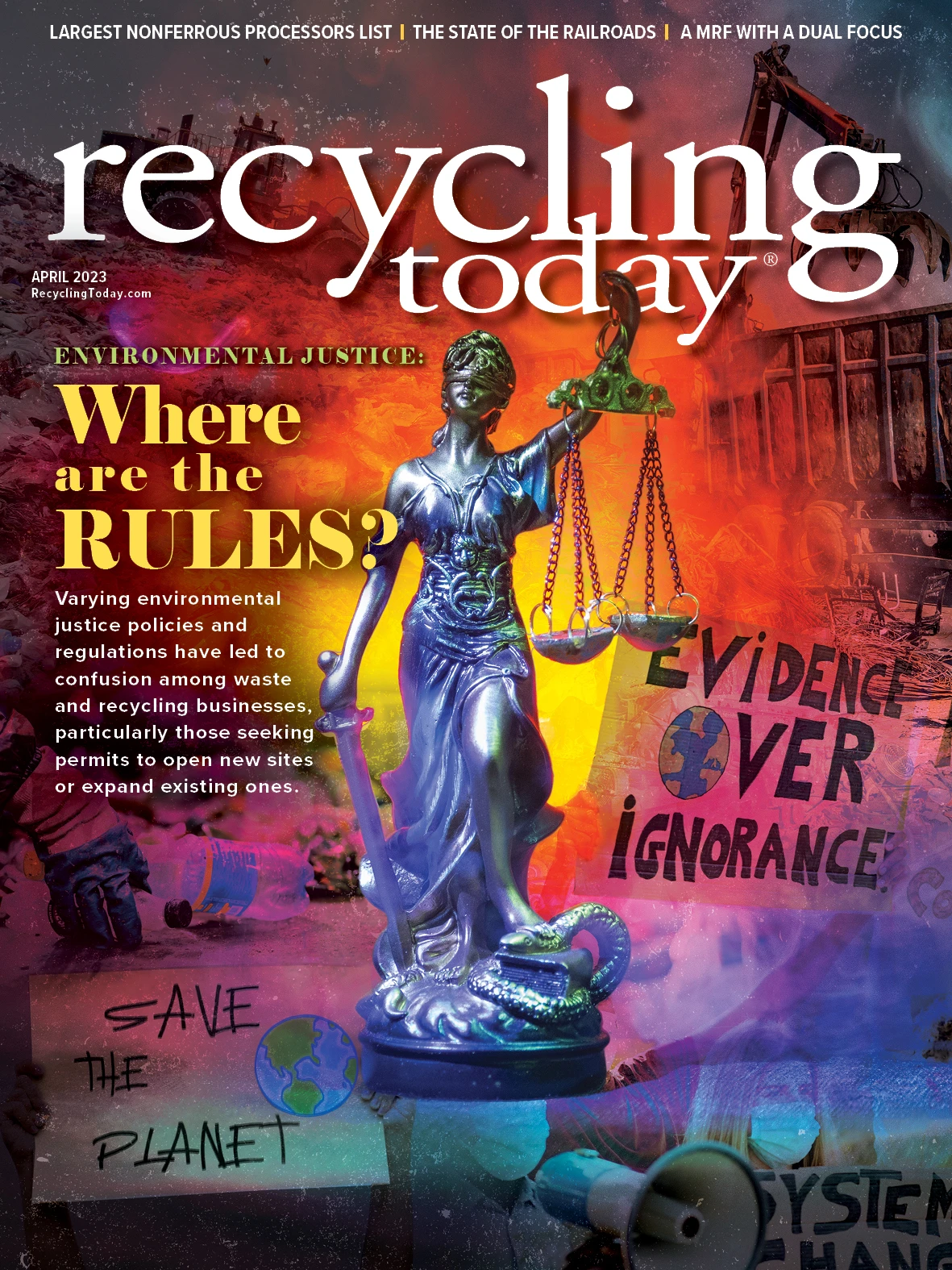
Explore the April 2023 Issue
Check out more from this issue and find your next story to read.
Latest from Recycling Today
- Athens Services terminates contract with San Marino, California
- Partners develop specialty response vehicles for LIB fires
- Sonoco cites OCC shortage for price hike in Europe
- British Steel mill’s future up in the air
- Tomra applies GAINnext AI technology to upgrade wrought aluminum scrap
- Redwood Materials partners with Isuzu Commercial Truck
- The push for more supply
- ReMA PSI Chapter adds 7 members