Choose a nonferrous metal or a plastic resin material, and chances are there is a trade group claiming it is gaining favor with automakers as a material of choice for tomorrow’s cars and trucks.
Separating the claims from the facts is important for participants in several industries, however, including scrap processors and their suppliers. While iron and steel have long driven the automobile recycling industry, other materials have increased their presence in the yards of auto recyclers.
STEEL STAYS NUMBER ONE
Steel’s long-time status as a recyclable commodity has traditionally allowed the auto industry to claim a high recycling success rate. USCar, Southfield, Mich., a trade association funded largely by the Big Three automakers, claims that 75 percent of vehicle weight is currently recycled. And according to the Steel Recycling Institute, Pittsburgh, nearly 98 percent of all iron and steel used to make vehicles finds its way back to the mill as reusable scrap.
In addition, steel’s affordability and ability to meet crash test standards makes it seemingly irreplaceable for a number of applications. The industry’s research and development departments are also aware of the intense competition, and continue to produce new alloys and formulas to keep steel attractive to the automakers.
“Now and in the foreseeable future, steel is the material of choice. It’s the least expensive and has improved dramatically,” a materials specialist from Ford Motor Co., Dearborn, Mich., said in a recent Los Angeles Times story.
At least one comprehensive study, however, indicates that steel as a percentage of total vehicle weight is on a downward trend. According to American Metal Market, steel and iron now account for 67 percent of average vehicle weight, down from just less than 74 percent in 1978. The biggest gainers in content during that same time span have been aluminum (up to 6 percent from 3.2 percent) and plastics and plastic composites (up to 7.6 percent from 5 percent).
The changing nature of what goes into a vehicle is starting to affect what comes out of auto shredders.
“We're seeing a decrease in the ferrous content,” says Roger Ruminski, general manager, United Metal Recyclers, Kernersville, N.C. United Metal operates an auto shredder and conducts periodic samplings of the shredded content, according to Ruminski.
But if the content of vehicles is indeed changing to include more nonferrous and nonmetallic materials, will the change have a significant impact on scrap processors and automobile shredders?
ALUMINUM ADJUSTMENTS MADE
According to The Aluminum Association, Washington, automakers consumed 3,607 million pounds of aluminum in 1996, up 7.9 percent over the previous year. On average, passenger cars manufactured in 1996 contained more than 250 pounds of aluminum. According to the association, that figure represents a rather significant 32 percent increase over the 191 pounds used per vehicle just five years earlier.
Similarly, the light truck segment has also increased its use of aluminum during the past five years. While light trucks built in 1991 contained an average 161 pounds of aluminum, those built in 1996 had 241 pounds of aluminum – an impressive 45 percent increase in per vehicle content. Chrysler Corp. has indicated that it will soon be building aluminum front axle assemblies for the four-wheel-drive versions of its Dodge Durango sports utility vehicle and its Dodge Dakota pickup truck.
Operators of automobile shredders are not necessarily seeing that aluminum content at their sites. “Part of what is happening is that some aluminum parts are disappearing from the cars before they even get to the shredders,” says Stephen Wulff of the David J. Joseph Co., Cincinnati. Wulff, who is vice president-planning of the company’s ferrous division, notes that large aluminum castings and parts such as wheel rims are generally removed by dismantlers and salvage yard operators.
Eddy current separators are utilized at virtually all of the Joseph Co.’s sites, says Wulff, to make sure the company takes full advantage of any nonferrous opportunities. “We’re working very hard to capture that market. We’re spending more time and more energy, and we’re investing a lot of money.”
“The recycling infrastructure is getting better established to recover those nonferrous materials,” agrees Terry Cullum, a GM environmental engineer who also works with the Vehicle Recycling Development Center (VRDC), a joint research project of GM, Ford and Chrysler. According to Cullum, the VRDC works closely with scrap processors and their trade associations to ensure that “the total picture” (i.e., dismantling and recycling implications of material choices as well as performance characteristics) is seen when considering what materials will go into new vehicles.
If aluminum continues to gain, who benefits and who stands to lose? Right now, auto dismantlers seem to be reaping some of the benefits of strong aluminum scrap markets. As Wulf indicated, larger aluminum parts are often spotted by dismantlers and sold not as parts, but as aluminum scrap.
Scrap processors have not remained on the sidelines of the aluminum game. Most have also entered the nonferrous arena, partly due to the realization that aluminum has gained a prominent place in the vehicle composition picture. Owners of auto shredders have had little difficulty finding markets for the aluminum that is sorted out by eddy currents.
And end markets for secondary aluminum are strong. According to Roger Scott-Taggart, an industry analyst with Alcan Aluminum Ltd., Montreal, five straight years of global aluminum inventory reduction should mean that an oversupply of scrap is unlikely. He spoke at a recent Aluminum Roundtable sponsored by the Institute of Scrap Recycling Industries Inc. (ISRI), Washington.
The aluminum industry remains confident that its products will continue to gain ground as auto makers strive to create lighter, fuel-efficient vehicles. “Lightweighting vehicles without downsizing or sacrificing safety is a critical goal for automakers today,” says Jane Patty Lichter, director of transportation of The Aluminum Association. “Aluminum has demonstrated its ability to meet these demands, as the increased growth shows.”
PLASTIC COMPOSITES
Aluminum is not alone in claiming it is the material of the future for auto makers.
Plastic auto body panels have been looked at by vehicle manufacturers as a way to lighten auto weights and eliminate corrosion problems.
At the Frankfurt Auto Show this September, Chrysler introduced its Composite Concept Vehicle (CCV), which it billed as featuring “an innovative automotive application of affordable, lightweight, recyclable composites that has the potential to revolutionize how cars and trucks are made.”
It is unclear how far the trip from concept to mass production will be for the CCV, according to Chrysler spokesperson Scott Fosgard. He says that Chrysler is initially looking at developing nations – such as China, India and Mexico – as the primary market for the subcompact composite vehicle.
Fosgard claims that it makes more sense to introduce composite cars in these countries in part because they do not have the same metals recycling infrastructure in place that exists in the United States. “We’ve got the model recycling infrastructure for the world,” says Fosgard. “There isn’t necessarily that same infrastructure for steel and metals in other parts of the world.”
The composite material being used for Chrysler in the concept and test vehicles is a form of polyethylene terephthalate (PET). It was chosen in part, according to Fosgard, because of its track record for recyclability. But whether U.S. scrap processors could easily cultivate the ability to recycle PET auto panels is unclear.
At Sims Bros., Marion, Ohio, there is a procedure in place for the plastic bumpers that have become standard in the auto industry. At one time, the company shredded plastic bumpers and shipped the resulting material directly to nearby Honda of America, Marysville, Ohio. Now, according to vice president Larry Sims, the bumpers are still removed by his company but are shipped to another firm that processes them for Honda.
In mid-September a facility came online that adds another building block to the automotive plastics infrastructure. Philip Services Corp., Hamilton, Ontario, and BASF Corp.’s Polymers Division, Mount Olive, N.J., opened what it is billing as the first rigid polyurethane recycling facility in North America.
Rigid polyurethanes – found in automotive steering wheels, dashboards, bumpers and spoilers – have not been widely recycled, although they account for up to 20 percent of the plastic found in the average vehicle.
The recycled polyurethane, or polyols, will be marketed by BASF to the automotive industry.
The new facility, located in Detroit, will initially accept scrap polyurethane from auto companies and automotive suppliers. “Our hope is that by mid-1998 we’ll be in a position to accept post-consumer scrap,” says Tom Randazzo, senior vice president, Philip Services. Corp. The company will be installing a mega-shredder at its Hamilton, Ontario facility, and would initially remove bumpers from vehicles brought there and send them to the Detroit plant.
The new facility is a first step for auto plastics to approach the recycling percentages of steel and aluminum.
AUTO SHREDDER RESIDUE
After a car is shredded and all the easily marketed steel and nonferrous metals are removed, a lot of nonmetallic material – such as foam, plastics and rubber – remains. This material, called automobile shredder residue (ASR) or shredder “fluff”, is not very recyclable because it’s difficult to separate the material into pure streams. Recently, auto manufacturers and other researchers have begun looking at ways that fluff can be diverted from its traditional home in landfills.
USCar recently asked researchers at Argonne National Laboratory, Argonne, Ill., to look into ways to reuse one common fluff material: polyurethane foam (PUF) used in auto seats. Argonne researchers have built a prototype system that cleans scrap seat foam quickly and readies it for reuse.
According to Ed Daniels, a section leader at Argonne, the vehicle seating project addressed ways to separate and reclaim the PUF from the general ASR stream. However, PUF only makes up 5 to 6 percent of a typical ASR stream. “It is clearly a technical challenge to try to extract material from that stream,” says Daniels.
The laboratory has also conducted research for the appliance industry that may have applications for auto shredder operators. Tests conducted by Argonne have looked at ways to separate marketable resins such as acryclonitile-butadiene-styrene (ABS) and high-impact polystyrene (HIPS) from shredded appliance residue.
North America may wish to look to Europe for techniques on ASR reuse. Two European companies are trying to overcome the barriers that have stood in the way of ASR being used as fuel in steel manufacturing blast furnaces. According to Automotive Recycling magazine, the two firms – Arbed Group, Luxembourg, and Krupp Hoesch Stahl AG, Dortmund, Germany – have already developed a technique to substitute ground-up plastic packaging waste for heavy oil in blast furnace operations. Now they are turning their attention to ASR in the hopes that it can be used in the same capacity.
And many shredder operators are anxious for developments to occur soon. More than one shredder operator referred to an industry-wide scramble to maintain auto shredder feedstock, making a maximum dollar return per vehicle critical.
W. Z. Baumgartner Jr., an environmental engineer and scrap industry consultant with W. Z. Baumgartner & Associates Inc., Brentwood, Tenn., believes ASR can provide an ideal daily landfill cover. “It’s one of the wisest environmental moves we could make,” he says. Use as landfill cover would require no further processing by the auto shredder operator and – while it may not generate any income – could at least lessen ASR disposal costs. However, ASR is considered a hazardous material in some states, so this would not be a valid solution in all regions.
But Baumgartner also says that as long as recycled plastic resins are not in great demand, there may not be any technological breakthroughs for fluff sorting and reprocessing.
“As soon as the economic driving force is there, I’m sure the equipment will follow,” he says of any future ASR sorting technology.
“Research” and “future” remain the most commonly used terms, however, when the subject of recycling and reuse of ASR is discussed. For now, as one auto shredder operator told Recycling Today, the only destination for fluff is “straight to the landfill.”
MAXIMIZING REUSE
Even before the shredding or crushing process begins, auto dismantlers are looking at ways to market individual parts that may still be in demand. Advances in computer technology may help operators of salvage and dismantling yards maximize the value of parts and components that some consumers might consider junk.
United Recyclers Group (URG), Florence, Ala. – a consortium of more than 200 auto dismantling companies – is developing an information management system that is designed to help its members take full advantage of this secondary market.
According to URG, much of the research is being driven by the insurance industry, which is seeking to reduce vehicle repair costs through the increased use of salvaged auto parts. The dismantlers/salvage yard operators, through URG, want to consolidate their inventories and have the Recycler Information Management System (RIMS) database available to insurers and collision repair shops. The database is being designed to allow for Internet access and digital images of parts being inspected or ordered.
Of note to auto shredder operators is the organization’s belief that the new system could help insurers favor repairing cars as opposed to declaring them as totaled.
PLASTICS STILL THE WILDCARD
Scrap yards and shredder operators seem to have adjusted to the increased presence of aluminum in vehicles. The existence of end markets for aluminum – and the value that creates – brought about the widespread use of eddy currents.
But to achieve that level of adjustment to plastic components, work will have to be done on developing end markets.
The author is managing editor of Recycling Today.
Get curated news on YOUR industry.
Enter your email to receive our newsletters.
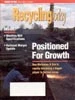
Explore the October 1997 Issue
Check out more from this issue and find your next story to read.
Latest from Recycling Today
- NWRA announces 2025 Driver of the Year, Operator of the Year winners
- The Scrap Show: Nanci Schuld of FE Trading Group LLC
- Call2Recycle Canada partners with RLG to advance battery collection
- Report delves into recovery opportunities for food-grade polypropylene
- Reimagining Supplier Payments in Metal Recycling: A Digital Leap Forward
- STEINERT Lithium Battery Detection and Removal from Waste Streams
- Driving the Future: Innovations in Waste & Recycling Technology
- Robin Wiener recognized for recycling leadership