Sorting. Maybe recyclers should prefer their scrap materials to be shaken, not stirred.
That’s one of the conclusions of a patent granted to Impact Laboratories Ltd., Grangemouth, Scotland, which has invented a new way to separate scrap plastics based on their differing densities. Unlike traditional methods, which use mechanically agitated impellers within stir tank reactors to separate the materials, the new method employs a centrally located oscillating baffle within a vessel that shakes the materials. In preferred embodiments, a segregation fluid, such as water, flows through the vessel.
“Preferably, the baffle structure comprises a central shaft upon which are located a plurality of discs, the discs including one or more pathways therethrough for the passage of vessel contents,” according to the patent.
The discs, which are spaced at equal distances along a shaft according to the size of particles being separated, create movement throughout the segregation fluid.
The system can be used to separate polyethylene (PE) and polypropylene (PP); it also works with nonplastic materials, including minerals and metals. The material can be film or thin flakes—materials that typically are difficult to separate because of static friction. Heavier materials sink, while lighter materials float. By using multiple vessels, arranged either horizontally or vertically, users can zero in on the materials they wish to process.
“Such cascaded arrangements can also be used to separate a mixture of more than two materials using water as the segregation media and controlling its flow through the series of vessels,” the patent states. “Therefore, we can separate a complex mixture of materials, for example, a mixture of PP (polypropylene) / LLDPE (linear-low-density polyethylene) / HDPE (high-density polyethylene) / ABS (acrylonitrile butadiene styrene) / HIPS (high-impact polystyrene) / PVC (polyvinyl chloride).”
Patent 10,093,036; issued Oct. 9, 2018

Pyrolysis. A company in Swindon, England, patented equipment and a method for converting mixed plastics into liquid fuel via pyrolysis that could be useful for plastics recycling operations. According to the patent granted to Recycling Technologies Ltd., the invention and process are “particularly suited to use in small- to moderate-sized recycling facilities, where they complement the facilities already present. For example, the electricity and heat generated by the process … can be used to power recycling operations.”
The invention would use the lower-value, mixed plastics that remain after more valuable materials have been sorted out.
The process involves feeding the mixed plastics into a fluidized bed reactor and passing the resulting product through a condenser to form a liquid byproduct and a gas byproduct.
The liquid is stored in a tank and used as fuel to run a generator to produce electricity. Unlike prior technologies for pyrolyzing mixed plastic scrap, the invention produces a uniform, high-quality fuel, the patent states.
Patent 10,093,860; issued Oct. 9, 2018
Depolymerization. A process for chemically recycling polyethylene terephthalate (PET) by using microwaves and a special catalyst could provide energy savings over previously used methods, according to a patent application that has been filed by the University of North Carolina at Chapel Hill.
The method breaks down PET scrap by combining the material with ethylene glycol and a catalytic system that consists of a catalyst and a microwave absorber. The mixture is heated via microwave irradiation. The resulting monomer can be purified and repolymerized into virgin PET resin.
According to the patent application, current methods for recycling PET via glycolysis require exotic catalysts and large amounts of heat. Existing glycolysis processes that use microwave irradiation have higher energy-to-heat conversion ratios than other methods but still are too expensive because of the amount of energy they require.
“By utilizing a mixed catalytic system that features a microwave absorber, glycolytic depolymerization of PET via microwave irradiation can be optimized to provide a process that is significantly more energy efficient than current chemical recycling techniques,” the application states.
Patent application 20180319950; published Nov. 8, 2018
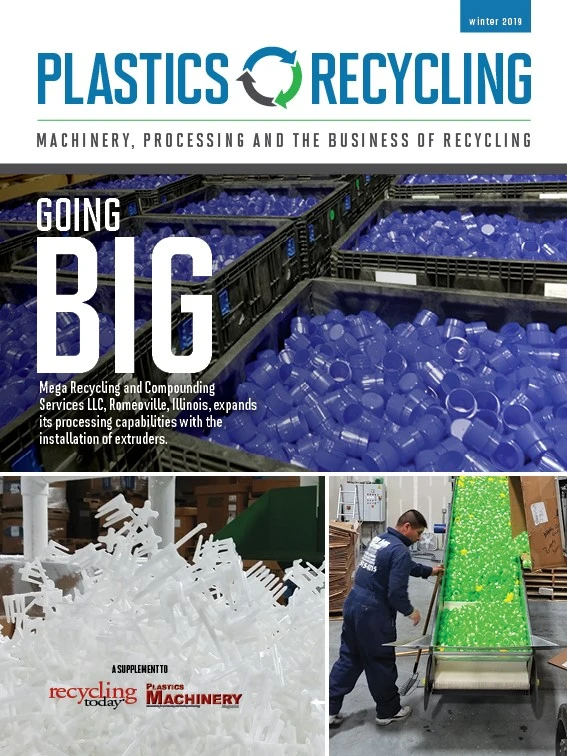
Explore the February 2019 Plastics Recycling Issue
Check out more from this issue and find your next story to read.
Latest from Recycling Today
- LumiCup offers single-use plastic alternative
- European project yields recycled-content ABS
- ICM to host colocated events in Shanghai
- Astera runs into NIMBY concerns in Colorado
- ReMA opposes European efforts seeking export restrictions for recyclables
- Fresh Perspective: Raj Bagaria
- Saica announces plans for second US site
- Update: Novelis produces first aluminum coil made fully from recycled end-of-life automotive scrap