
CP Group’s commitment to innovative design and durable construction has set the industry standard for nearly 50 years. As an OEM, our ongoing investments in research and development coupled with our practical experience as material recovery facility (MRF) operators drive MRF design.
Unlike other systems suppliers, we’ve stood in your shoes and know the challenges you encounter daily. We have more than 25 years of experience as a MRF owner and operator where we processed half of the city of San Diego’s curbside recycling, and we still process material today. The CP team collectively has decades of experience working for and with private and public recyclers—some of the largest in the industry. Our team’s practical experience in MRF operations means we truly understand the importance of controlling operating expenses, and that is reflected in our approach to the systems we design and the equipment we supply.
Our mission is to maximize the value of the material stream by identifying crucial stages in the recovery process, using precise equipment at each point. Our MRF design principles result in better recovery rates and high-quality commodities.
At CP, we focus on fractionating incoming material for size and density differentiation, liberating material for streamlined downstream processing and separating commodities through highly precise selective sorting.
We appreciate the elegance of simplicity, and our approach to equipment and MRF design reflects that philosophy.
Take our Auger Screen™ as an example. This machine has led to an evolution in the front end of sorting systems, contributing to the effectiveness of the equipment on the back end.
“We appreciate the elegance of simplicity, and our approach to equipment and MRF design reflects that philosophy.”
Evolving the Front-End
CP introduced Auger Screens™ to the U.S. market in 2017 with our “fractionate” principle. Some European companies have sold splitter screens in other markets, but they take a one-size-fits-all approach and don’t use them for sizing. CP correctly applies the technology to sizing. Rather than take a one-size-fits-all approach, we have developed more than five Auger Screen™ sizes as well as a patented screen to segregate old corrugated containers (OCC). The OCC Auger Screen™ is engineered specifically to target midsize to large OCC, producing a clean end product. We use patented high-agitation, tri-lobe augers to achieve these results.
Our Auger Screens™ use a series of cantilevered augers made from abrasion-resistant steel that require little to no maintenance. They do not wrap or jam because of the augers’ corkscrewing motion.
In our industry, people always have protected the machines. Industrial automation should allow machines to protect the people. That’s what we have done. The CP Auger Screen™ eliminates the presort and dramatically decreases the volume on the postsort, thereby decreasing the number of manual sorters needed and increasing their safety by removing the small hazardous fraction.
Next, we mechanically prepare material for downstream sorting by liberating 2D material from 3D material with our high-capacity, low-maintenance CPScreen™ and Anti-Wrap Screen™. This process increases purity as commodities continue to the next phase, separation, where we deploy our near-infrared (NIR) and artificial intelligence- (AI-) enabled optical sorters.
Using the CP Auger Screen™ upfront in combination with our other screening technology allows us to maximize the effectiveness of optical sorters. The material is fractionated effectively, creating more homogeneous streams that enable the efficiency of downstream sorting.
Reduced OPEX
It’s no secret that MRFs are becoming increasingly complex as automation is added to improve material recovery and purity and to address labor issues. We also know that this automation comes at a higher price than MRF operators saw even a few years ago in part because of inflated prices for everything from steel to conveyor belts.
Given the investment new technology represents, CP Group has prioritized reducing operating expenses for our customers to help them realize a return on investment more quickly.
Additionally, our technology allows MRF operators to reduce headcount in their plants. In the past, for every ton of material processed per hour, a hand sorter was required. We’ve reduced that personnel requirement by 80 percent, meaning a 50-ton-per-hour system requires only 10 sorters or less, depending on the degree of automation, with the future goal of no manual sorters. That is the kind of impact CP is striving for with the systems we design and build.
Our equipment is more durable and requires less maintenance and cleaning, further reducing OPEX for our customers. By using CP Group augers and non-wrapping screens, MRF operators have less maintenance and downtime to contend with compared with other sorting solutions.
This reduction in maintenance also means our systems experience less downtime. Our customers say uptime for CP systems is greater than 95 percent.

High-performing optical sorters
With the ability to sort over a width of nearly 11 feet, CP was the first company to offer wider belts for the optical sorters manufactured by our MSS Inc. division. The FiberMax™ sorters also run at the fastest belt speeds (up to 1,200 feet per minute), which, when combined with our wide belts, equates to belt coverage that facilitates the sorting process, enabling more tonnage to be processed and more picks per minute on a single unit with less collateral damage.
We also employ a proprietary air-assist and material-handling system that keeps paper moving through the sensing zone in a laminar flow without turbulence, while our patented PrecisionFlow Hood™ ensures accurate ejection of ultra-light materials in fiber and film applications.
Our MSS FiberMax™ machines effectively remove small OCC from mixed paper, enabling MRF operators to improve their yield on OCC and the quality of their mixed paper, realizing the highest values for both these commodities.
AI integration
CP Group has integrated AI with our MSS NIR optical sorters, launching Vivid AI™ in 2023.
The technology leverages the proven efficacy of our air jets with AI’s real-time data to enhance MRF efficiency and profitability. This powerful combination enables the finer separation of materials with similar signatures as interpreted by conventional sorters. For example, we can sort cat food cans from used beverage cans and polyethylene terephthalate (PET) thermoforms from PET bottles.
Investing in innovation
We’ve gotten where we are by continually investing in research and development and introducing new concepts to the industry over the decades. We have a dedicated research and development team and also involve team members from throughout the company, including those in sales and project management.
We’re constantly asking ourselves, “What is the next thing we can do to make things better?”
Our R&D investment shows in our equipment and our approach to system design.
For example, Auger Silos were a CP innovation that we introduced three years ago, along with leveling augers nearly 10 years ago. We have taken out traditional silos and replaced them with two rotating augers at the bottom of the silo and a leveling auger at the top. The bottom augers act as a material metering system that eliminates half and quarter bales by emptying the correct amount of material to be baled.
The CP Group focuses on innovative efforts to simplify operations for our customers because we appreciate that operating a MRF is difficult, and your equipment should work for you, not against you.

Terry Schneider
President/CEO
CP Group

CP Group
6795 Calle de Linea, San Diego, CA 92154
619-477-3175 | 800-462-5311 | www.cpgrp.com
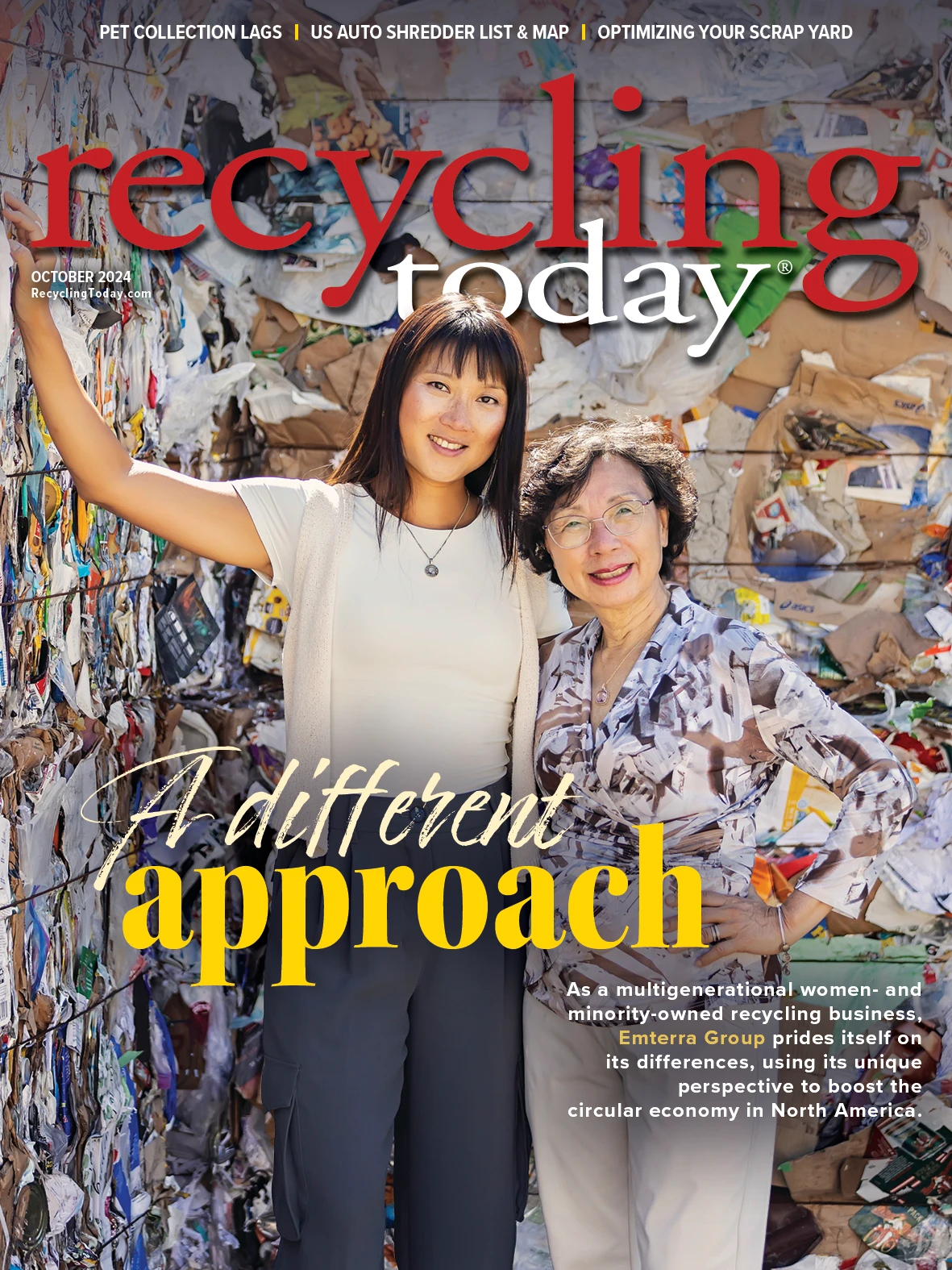
Explore the October 2024 Issue
Check out more from this issue and find your next story to read.