
The mega batch feeder
When Medford, New York, based Gershow Recycling set out to build its new eddy current plant, one of the issues the company needed to overcome was consistently feeding the system.
“We did a lot of work to understand the production rate we needed to ensure our eddy current plant no longer held us hostage,” Gershow Recycling President Kevin Gershowitz says. “We identified that none of the available feeding systems could do it.”
Gershow needed a batch feeder that could maintain the material flow. The company created an initial idea for a massive feeder it believed would work. “We shared this idea with several industry suppliers," Gershowitz says. "They told us it would not work and were unwilling to build it."
“When we shared the idea with the team at U.S. Conveyor, it was a different story. They were sure they could build it and confident it would work as desired. ... U.S. Conveyor went beyond being confident they could build the batch feeder. They guaranteed it would work and said if it did not, they would give us our money back. That was more than we expected.”
“We’ve built hundreds of feeders, but nothing of this scale,” says Troy Graves. President of U.S. Conveyor Technologies, Mackinaw, Illinois.
“To get the job done, our engineering team set out understanding the customer expectations, modeling the power requirements and understanding the forces it would take to move this huge amount of material at a very precise rate” Graves adds.
The feeder is 70 feet long and 8 feet wide. Fully loaded, it allows for approximately 115 tons of material (or 240 cubic yards of ASR) to be loaded. It then seamlessly meters the material into the plant’s elaborate screening system.
Counting zorba

The zorba produced by the Gershow plant enters a sophisticated counting regimen. Each of the eight lines drops onto a designated scale conveyor. That scale conveyor incrementally moves until it reaches a predetermined weight, then it clears itself and begins counting again.
This highly controlled process allows the plant’s control system to continually record precise production levels for each zorba fraction as well as the plant’s overall production.
Traditional belt scales do not work when weighing low volume products like zorba, especially when the total flow is sliced into eight fraction sizes. The system has proven to be very accurate and this approach holds great potential for a wide variety of applications in the industry.
Value from the ferrous

Many operators let the ferrous recovered from their DSRPs drop into their residual lines. U.S.C. offers a way to recover that material.
By running the residuals through a Spaleck Cassette screen and U.S. Conveyor Polisher, the ferrous fraction is both reclaimed and cleaned up. This allows that fraction to be added back into outbound ferrous material, turning it into revenue while avoiding landfill fees. It’s a great use of the cassette screen and polisher.
Going bananas

Keeping nonferrous plants open and airy while maintaining lines of sight and working around obstacles is challenging. U.S. Conveyor’s proprietary banana conveyors can help to get the job done. The banana conveyors allow for slopes not possible with traditional conveyors.
The unique banana conveyors can be integrated into plant designs in numerous ways. They provide perfect material flow from one processing phase to the next but also help to deliver the open access.
Get curated news on YOUR industry.
Enter your email to receive our newsletters.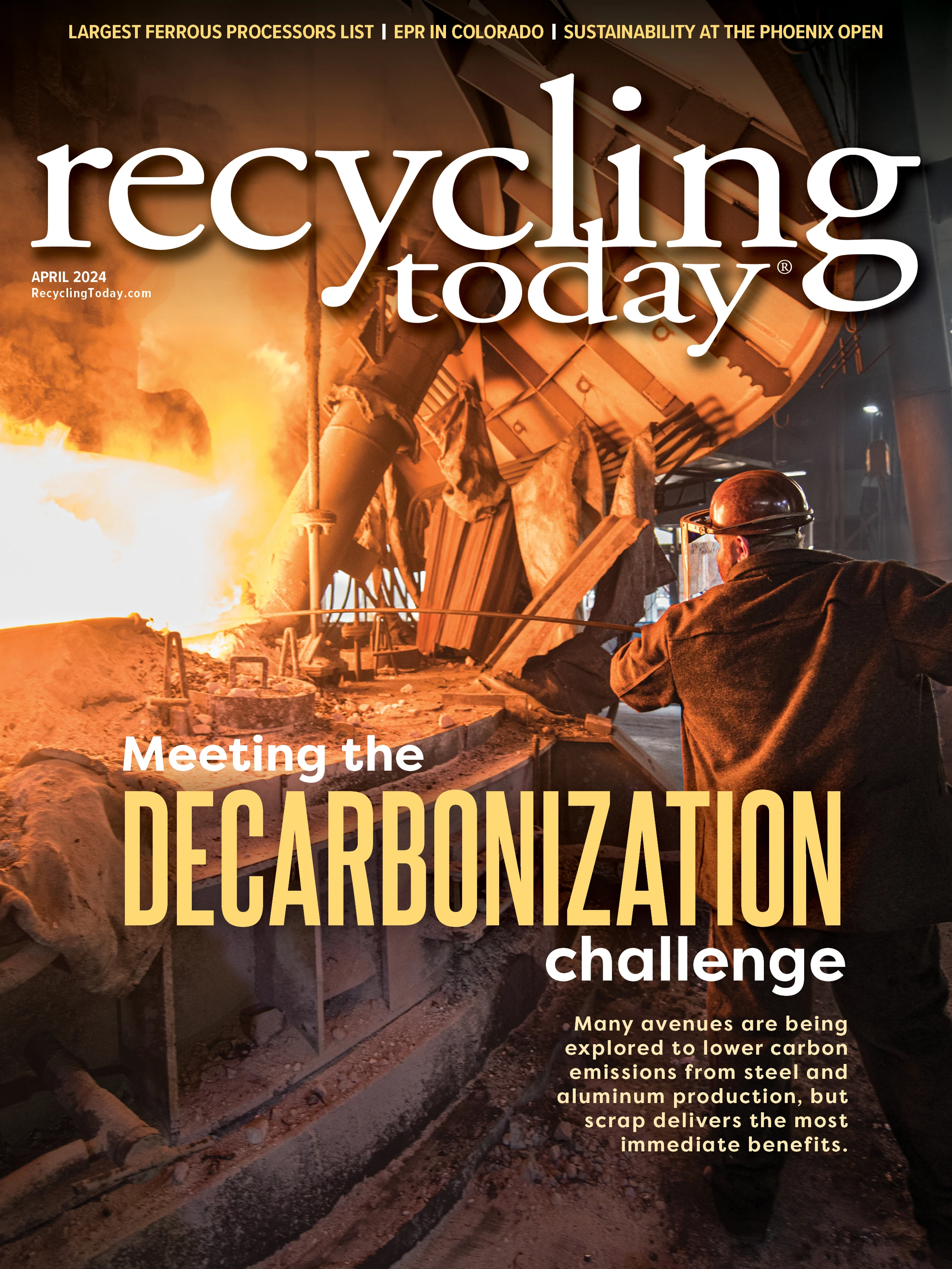
Explore the April 2024 Issue
Check out more from this issue and find your next story to read.