WTC Materials Processing Continues
The focus after the recent terrorist attacks at the Pentagon and the World Trade Center has rightly been on the loss of human life and the U.S. military and diplomatic response.
But at the WTC site in lower Manhattan, sits probably the world’s largest debris pile from buildings taken down incorrectly, and the ultimate fate of some of the material is still being decided.
Currently, Turner Construction, New York, along with Bovis Lend Lease, London, and AMEC, London, are general contractors on the clean up and any re-building being done. Several subcontractors have been hired to help finish tearing down the buildings and remove the material.
THE EARLY SCRAMBLE
After the buildings collapsed, several demolition contractors moved in to help—some called by FEMA and some not— and some perhaps cynically to be in position to receive contracts when the debris removal started.
FEMA went through a process of weeding out contractors who won’t be needed. Separate contracts have been awarded for the various quadrants of the 16-acre site. Now that the focus is on debris removal and not search and rescue, a lot of the cranes are moving out and are being replaced by demolition excavators, although one huge crane is being erected on the site for removal of extra-large pieces.
Early on, the search for survivors took prominence over debris removal, although that has now changed. Not that it would have made much difference as far as removing the towers’ debris any quicker, according to John Yannuzzi, Yannuzzi & Sons, Orange, N.J. Even without the search for survivors it will be slow going because of the nature of the material.
Instead of nice, neat beams cut properly and mixed with mostly heterogeneous concrete like on a normal demolition job, the site consists of an unsorted tangle of twisted metal and pulverized concrete, along with miscellaneous office furniture, paper, etc. The debris also contains or contained the remains of more than 4,000 people.
At the site, an equipment operator can grab a piece of metal and think it is a small piece when in reality it is a 50-ton chunk covered by rubble. This can put unexpected stress on the boom.
Or, the movement of one piece can expose a cavern 40 feet down, making it highly unsafe for machines and workers. For that reason, companies are holding safety meetings daily to remind the workers how to be extra careful in this environment.
This all can take a toll on the operators. Besides being tough duty over long hours, it can be emotional for some as they operate through the rubble, realizing what happened there. All contractors are rotating out personnel in order to help alleviate the stress.
AN UNWELCOME SITE
The work on collapsed Building Seven of the WTC has been on full-scale removal for some time now. That job has been awarded to Nacirema Environmental of Bayonne, N.J., with assistance from Seasons Contracting Corp., North Bergen, N.J. MCM Management Corp., Detroit, and Brandenburg Industrial Services, Chicago, are subcontractors on that job, as well.
A demolition contracting company that has been there from the afternoon of Sept. 11 is East Hanover, N.J.-based Mazzocchi Wrecking. Its excavators and employees could often be seen in live television coverage of the search and rescue. (News crews were only allowed one view into the site, that of the North Tower area where Mazzocchi was working.)
According to Nick Mazzocchi, the company has nine excavators working at the site now, and has purchased two more excavators that will be assembled at the site in the next few weeks. The company also has 20 trucks per day working. Like all the contractors at the site, the equipment is manned around the clock as everyone is working two, 12-hour shifts. He estimated that his trucks are moving out 4,000 tons per day.
Yannuzzi & Sons is another company that has been there from early on. John Yannuzzi reported that his company has six pieces of mobile equipment on site, and will have four more there shortly. The company has been involved with several implosions over the years, and is used to seeing piles of debris. But this is different, Yannuzzi said, beyond the obvious human tragedy. "It is a building taken down wrong," he said.
Equipment operators did not know what to do at first when they showed up. "We have already broken the boom off of one excavator, and that has never happened before. Usually you can see the crack coming and fix it. And we broke two grapples so far. Not just the tip, but the whole grapple, and those were good ones."
The rubble of the two towers extends as high as 90 feet in the air. The procedure is to put two large excavators at the tops of those piles, process the material down to a manageable size and push it down to smaller excavators that will further process the material into sizes that can be handled by the trucks.
Besides the two towers and Building Seven, several surrounding buildings around the site are damaged and will have extensive work done on them before they are used again, or they could be taken down. This includes the other buildings in the WTC complex. Other buildings around the site that remain still look like they have been through a battle.
The material is all going to the closed Fresh Kills landfill on Staten Island, where FBI agents are sorting through it looking for clues.
Fresh Kills has been closed for close to a year, but the technicalities of securing permits to open it back up were bypassed.
RECYCLING CONSIDERATIONS
Grace Mazzocchi, whose company owns a new C&D recycling center across the river at the Meadowlands complex in New Jersey, says there are no plans now to recycle any of the material beyond the metal. She is not sure if anything else is salvageable.
Early on in the clean-up stages, John Yannuzzi agreed: "Recycling is the furthest thing from their mind, but I suspect they will just stack it there and then put a bid out later to recycle it. The only way to recycle that material is to use a high-tech plant that can float apart the debris." Observers also point out the squeamishness of handling the material, as there could still be residue from the unfortunate victims of the tragedy.
By late September, though, New York City had issued the first of what is expected to be a number of bids to handle the steel beams pulled from the rubble.
The first bid, issued by the New York City Department of Design and Construction, came out on Sept. 21, with a contract awarded early the next week. That contact went to two companies, each slated to handle half of the 50,000 tons of steel that is being barged from the WTC site.
The two winning bids went to Hugo Neu Schnitzer, New York, and Metal Management Inc., Chicago, who both are taking in 25,000 tons of the material via barge.
Hugo Neu’s Claremont facility in Jersey City, N.J., will be taking in its portion of the steel beams being generated. Metal Management will bring the barge shipments to its Port Newark facility in Newark, N.J.
Due to the size of the material that is being shipped, the number of scrap processors who would be able to handle the material is limited.
Alan Ratner, president of Metal Management Northeast, says his company is using torch cutters, as well as mobile shears and fixed shears, to reduce the large steel beams into manageable sizes.
Bob Kelman, vice president of Hugo Neu, agrees that the size and weight of the beams makes the process of converting the metal into a more easy-to-handle format very difficult.
There are likely to be a number of additional bids issued by the city as more steel beams are pulled from the wreckage.
Mark Sprouls, a freelance writer/photographer working on behalf of Caterpillar Inc., contributed to this article.
Contractors Sift Through Debris at Fresh Kills
While the first stage of clean-up efforts takes place at Ground Zero in Manhattan, a second phase is underway at the Fresh Kills landfill on Staten Island.
Fresh Kills had stopped accepting waste for burial earlier in 2001. After the attack, however, it was the logical place to haul debris for processing.
Contractors and subcontractors at the site have been accepting mixed loads and running them through screening equipment. At the screening lines, homicide investigators sift through the material for personal artifacts, body parts and other evidence that can confirm victims were at the scene.
One of the contractors on site, Taylor Recycling, Montgomery, N.Y., is running debris through fingerscreens made by Erin Systems Inc., Portland, Maine.
According to Hans Taylor, the efforts are non-stop, with the crews and machinery running "24 hours a day, seven days a week."
Doug Logan, national recycling specialist with Erin Systems, says crews are doing a pre-sort of material at Fresh Kills, pulling out larger pieces of steel for recycling. Material is then sent to the screening machines where investigators look for evidence to be pulled from the stream of material.
Logan describes the mixture of materials as "a high concentration of steel, including rebar and conduit, and wet aggregate dirt." The wet aggregate comes from the constant hosing down of material at ground zero, which is being done to bring down the temperature at the core of the still smoldering wreckage. "At the core, as of early November, it was still 1000 degrees Fahrenheit," notes Logan.
Taylor and other contractors have been able to keep up with the flow of material that arrives, avoiding a stockpiling situation at the landfill, according to Howard Fiedler of Erin Systems.
Logan estimates the clean up efforts will continue into spring of 2002, probably into April and May.
Should Steel Beams Make a Memorial?
Is it wrong for the scrap industry to reclaim the scrap metal generated from the attack on the World Trade Center?
In a letter to several media outlets, at least one scrap recycler says that it is, and proposes making an underwater barrier reef offshore from Manhattan.
Harry Kletter, chairman of Industrial Services of America (ISA), Louisville, Ky., says "this sacred rubble and scrap should not be buried in a landfill with ordinary trash or consumed in a steel mill’s furnace, since it contains pieces of books and records, pieces of tile and carpet, pieces of computers and lighting, pieces of glass and marble, and pieces of someone’s son, someone’s daughter, someone’s mother, someone’s father, someone’s friend, someone’s neighbor."
In his letter, Kletter also makes reference to the economic condition of the ferrous scrap industry, saying, "We need to recycle everything from Ground Zero in a manner that will not present a burden to an already overwhelmed infrastructure."
Kletter proposes creating a barrier reef of the material 17 miles offshore from the southern tip of Manhattan where the World Trade Center used to stand. "A barrier reef is a living and growing tribute that would be an economical and ecological choice for a lasting memorial capped by a stainless steel buoy fashioned from scrap and fitted with a solar and wind-powered beacon to serve as an everlasting light."
It is unclear how much support Kletter will be able to garner for his project. Two scrap companies have already bid on steel beams being reclaimed from the site, and much of the concrete at the site may not be in large enough chunks to build a reef.
Kletter was in Manhattan at the time of the attack and witnessed the towers collapse from the balcony of an office building. He says he "would also like to be a witness at the dedication of the World Trade Center reef."
BUFFALO PLANT WILL SEEK RECYCLABLE WOOD
A fiberboard manufacturing plant being constructed near Buffalo, N.Y., by Ligna Recycling Technologies is planning to hire 64 workers and accept waste wood from throughout the region.
A report in the Buffalo News quotes Ligna Technologies president Steve I. Simon of Toronto as saying the company and seven other Canadian investors are shareholders in the Lackawanna, N.Y., project.
According to Simon, negotiations for a recyclable wood supply for the operation were conducted with Lake Front Recycling of Buffalo and other firms last year, but a contract with Lake Front was never signed.
"As soon as we put our financial structure together, we are going to negotiate with local wood-waste suppliers in the Buffalo area," he told the Buffalo News.
Ligna Recycling will be eligible for grants and tax breaks, including $27 million in financing through Erie County Industrial Development Agency bonding and other tax breaks and incentives due to its location in the Lackawanna Economic Development Zone. Construction of the Ligna facilities is expected to cost about $32 million.
JAPANESE WOOD RECYCLING LAW SPURS RESEARCH
The Japanese steelmaking conglomerate NKK Corp. has also announced that it is "exploring the possibility of employing construction-waste scrap wood to feed a power generation boiler."
The company, which has pioneered using scrap plastics as a substitute for coke in steel blast furnaces, is developing what it describes as "a circulating fluidized-bed boiler, which will use scrap wood as well as mixtures of wood and plastics as fuel, with a 31 percent power generation efficiency."
While conducting trial operations, NKK will study how to collect at least 50,000 tons of scrap wood each year in Japan—the required amount to run the power generation boiler on a commercial basis.
The project is spurred in part by new legislation in Japan on construction material recycling that will be enacted in the spring of 2002. The rules require the recycling of scrap wood at some construction sites.
CMRA BEGINS REGISTRATION
Response has been strong to the Construction Materials Recycling Association (CMRA) Annual Meeting, according to CMRA executive director William Turley. The meeting will be held next March 20 at Las Vegas’ Treasure Island Resort in conjunction with the ConExpo-Con/Agg trade show.
The CMRA meeting will feature three speakers: Byron Lord of the Federal Highway Administration on recycled material’s use in the highway environment; Terry Bauer of Green Seal Environmental on safety at C&D recycling sites; and, Paul Ruesch, U.S. EPA Region 5, on dealing with governmental regulations.
The CMRA, in cooperation with SWANA, is also offering certification programming for C&D facility operators.
For more information about the meeting, contact CMRA at (630) 548-4510 or by e-mail at turley@cdrecycling.org.
C&D Recycling Southeast Style
C&D recycling remains a regionally varied industry, with infrastructures varying widely even within the same quadrant of the U.S. That was the conclusion reached by some participants at a conference on C&D recycling sponsored by the U.S. EPA in Atlanta.
In Mississippi, there is no official designation for or definition of C&D waste, and it is regulated the same way as municipal solid waste. Florida, on the other hand, its C&D debris stream and has proactively supported the recycling of C&D materials.
Representatives from North Carolina and Georgia noted that their states had some activity and offered some initiatives to promote C&D recycling, but not to the extent that Florida does.
C&D Recycler Challenges Franchise Law
A C&D debris recycling company is challenging a California community’s franchise hauling law that restricts the flow of construction and demolition debris to recyclers.
Chip It Recycling Inc., an Oakley, Calif.-based recycler of construction and demolition materials, is appealing an order this week entered by the Contra Costa County Superior Court prohibiting Chip It from continuing any recycling activities in the City of Antioch based on Antioch’s solid waste and recycling ordinances.
Chip It is arguing that federal transportation law preempts any local regulation of the transportation of recyclable materials from commercial and industrial sites to downstream manufacturers and other recycling and reuse processing facilities. Chip It also argues that the injunction violates state of California public policy because it allows solid waste hauler Pleasant Hill Bayshore Disposal Inc to landfill substantial quantities of materials previously recycled by Chip It.
Bruce McChesney, president of Chip It, says the city’s ordinances and exclusive franchise contract with Pleasant Hill "violate common sense and public policy. The City is ignoring its duty to promote recycling, and the garbage company is just trying to increase its monopoly profits. The city shouldn’t allow [Pleasant Hill] to force developers and contractors to pay inflated garbage rates for hauling commercially valuable material to landfill."
Pleasant Hill argues that it has the exclusive right to transport loads of recyclable wood, concrete, stucco, and other construction material from construction sites and manufacturers within the City of Antioch, including cases where materials are taken directly to third-party manufacturers or processing facilities for recycling and re-use.
Several "friends of the court" briefs have been filed on behalf of one side or the other by groups such as the Association of California Recycling Industries, Californians Against Waste, California Resource Recovery Association, Grass Roots Recycling Network, Independent Recyclers Council, and the Northern California Recycling Association as well as by the California Refuse Removal Council and the Cities of Alhambra, Antioch, Camarillo, Irwindale, Palm Springs, San Jose, Signal Hill, Sunnydale, and Vacaville.
A similar appeal is pending before the Ninth Circuit Court of Appeals in an Oregon case where the United States District Court found that federal law preempted local regulation of the transportation of recyclable construction and demolition materials.
Chip It has collected and transported recyclable C&D materials, including wood, concrete, stucco, gypsum, metal, and cardboard, from commercial sites for subsequent recycling and re-use since 1987.
T. H. GLENNON ADDS SALES REP
Kriem Michel has joined T. H. Glennon, Salisbury, Mass., as sales representative for the eastern region of the U.S.
Kriem will represent the company’s line of landscape mulch colorants to the region, as well as the Mulch Color Jetä equipment, which is used to inject colorants directly into the grinder.
She comes to T. H. Glennon from the Landscape Products Group of the Coatings and Colorants Division of Bayer Corp. She has extensive experience in the wood mulch industry and over ten years in sales representing Bayer’s line of colorants.
Kriem will work from an office in New Jersey.
BTI NAMES CANADIAN DEALER
Breaker Technology Inc. (BTI), Solon, Ohio, has named Creighton Rock Drill Limited Equipment Inc. as its exclusive distributor in the province of Ontario.
The Mississauga, Ontario, company will handle the sales, service and parts for all BTI hydraulic breakers, plate compactors, pedestal breaker systems and demolition attachments.
A BTI news release credits Creighton with having "extensive experience" in the rock drilling and crusher wear parts areas, and with having a "customer driven focus."
Allied Honors Top Dealers
Allied Construction Products Inc., Cleveland, has announced its final distributor standings for 2000. The Top Distributor Award was given to Michigan CAT of Novi, Mich.
Other top Allied Distributors were:
• Scot-Gallaher Inc., Cloverdale, Va.
• Highway Equipment Co., Zelienople, Pa.
• Waukesha-Pearce Industries Inc., Houston
• Eagle Power and Equipment Corp., Montgomeryville, Pa.
• Gibson-Stewart Co., Oakwood Village, Ohio
• Wilson Equipment Co., Lexington
• Green Equipment Co., Fort Worth
• Pacific Machinery Inc., Waipahu, Hawaii
Rich Steinbrenner, North Royalton, Ohio, was named winner of Allied’s Top Gun Award which is given to the number one district manager for outstanding sales performance.
Sandvik Enters U.S. Crushing Scene
The Sandvik Group, a Swedish industrial conglomerate, has acquired some of the crushing equipment lines of the former Svedala Industri AB from Metso Corp., the Finnish company that bought Svedala.
Sandvik Rock Processing will be a new sector within the company’s Mining and Construction division. The Svedala crushing line purchased will include models such as the Hydrocone, the Eurocone, the Jawmaster and the Impactmaster. Several of the models are used by recyclers of concrete and asphalt.
The overall line of equipment offered by Sandvik will include crushers, screens and feeders, including mobile crushers and screening stations.
Sandvik has an established presence in the mining, drilling, excavating and metalworking fields. The conglomerate employs 35,000 people doing business in 130 countries.
The new Sandvik Rock Processing division currently has its North American offices in Appleton, Wisc. Nils Evert Karlsson is global president of the division, which is based in Sweden.
VOLVO, KOMATSU CONSIDER COOPERATION
Japan’s Komatsu Ltd. and Sweden’s Volvo Construction Equipment have entered into discussions to cooperate in component procurement.
According to a Volvo news release, the two companies "have initiated discussions regarding future cooperation in the production and development of construction equipment components."
The intention, according to Volvo, is to "find ways to strengthen their cost competitiveness and to increase customer satisfaction."
The two companies will not discuss cooperation in the areas of sales, service, distribution and equity participation, according to the release. "Both companies will continue to engage in business as independent competitors using their own dealer networks, brands and identities."
The brief news release does not address whether the cooperative efforts planned could lead to merger exploration talks, or whether the two companies expect to run into any anti-trust resistance with their component procurement efforts.
Bobcat Hits a Milestone
Bobcat Co. has built its 500,000 Bobcat skid-steer loader at its Gwinner, N.D., plant. This represents more skid-steers than all other brands combined, the company says. "We are excited at their tremendous growth and acceptance, and proud to have played a leading role in the development of the skid-steer loader industry," says Chuck Hoge, president, CEO of Bobcat.
Hoge attributes much of the growth in the skid-steer industry to the contribution of attachments, making the units more versatile.
MORBARK PRODUCT GUIDE RELEASED
Morbark, Winn, Mich., has released a product guide that offers information on its entire range of products for the recycling, composting, waste processing and other industries.
The glossy, full-color publication contains product specifications on tub grinders, horizontal grinders, trommel screens, mulch coloring systems, material handling equipment, chippers and all the other equipment made by the company.
Contact information for the six Morbark product support facilities located in different parts of the U.S. is also included. Those interested in receiving the guide can call Morbark at (800) 831-0042.
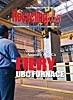
Explore the December 2001 Issue
Check out more from this issue and find your next story to read.
Latest from Recycling Today
- Altilium produces EV battery cells using recycled materials
- Brightmark enters subsidiaries of Indiana recycling facility into Chapter 11
- Freepoint Eco-Systems receives $50M loan for plastics recycling facility
- PET thermoform recycling the focus of new NAPCOR white paper
- Steel Dynamics cites favorable conditions in Q1
- Hydro starts up construction in Spain
- Green Cubes unveils forklift battery line
- Rebar association points to trade turmoil