On a hot, humid summer day in 1974, I paid my first visit to the United States Metals Refining Co. in Carteret, N.J. That day not only left an indelible picture in my mind, but also marked the beginning of a long love affair with copper.
USMR, as it was known throughout the industry, was the largest secondary smelting and refining facility in the United States and a division of Amax Inc., one of the largest and most diversified natural resource organizations in the world.
In operation since 1902, USMR was 20 miles southwest of New York City, with a deep-water port on the Arthur Kill, directly across from Staten Island, N.Y. It was a landmark unlike any, punctuated by its 425-foot high smoke stack, the tallest stack east of the Mississippi. There was nothing small about the operation or its complexity. Annual production of refined copper was in the range of 180,000 metric tons; silver, 40 million troy ounces; gold, 800,000 ounces; and platinum and palladium combined, 100,000 ounces. In addition, the facility produced some 75,000 metric tons of oxygen-free copper as well as copper powder.
Having just joined a management training program within the copper division of Amax, I was sent to USMR to see the operation and to get a better understanding of the work I would be doing. What an education! Smelting; refining; blister copper; anodes; cathodes; ingots; wirebars; billets; cakes; precious metals; scrap, scrap and more scrap. It was enough to make your head spin, but there was no better place to learn the business.
That was a long time ago, and a great deal has changed since then, reflecting the ongoing evolution of our industry.
A SHIFTING CENTER
Until the late 1970s New York was the center of the universe for the copper industry. Although the mines were out West, their headquarters were mainly in Manhattan, along with the bankers, brokers, merchants and, of course, the New York Commodity Exchange.
Going just beyond the city, the copper trade was a major part of industrial activity in the Northeast. Not far from USMR, American Smelting & Refining had a plant in Perth Amboy, N.J., while Phelps Dodge produced copper at its secondary operation in Laurel Hill, Queens, N.Y.
Being on the water enabled copper producers to ship wirebars by barge to wire and cable mills located along the Hudson River, or cathode, ingot and wirebars to New York Commodity Exchange warehouses.
Not far away, the Copper Valley in Connecticut was home to the brass mill industry, while dozens of wire mills were scattered about New Jersey, Connecticut, Rhode Island, Massachusetts and upstate New York.
Of course, where goods were manufactured, scrap was generated, and, with it, a network of scrap dealers whose job was to find a home for the metal to be used again. This is one of the most important characteristics of copper—its ability to be recycled, over and over again, regaining its natural state after being refined or being used directly in the application of a different product.
Paradoxically, although the recycling of copper is essential to the industry, key sectors of it no longer exist. The advent of stringent environmental regulations, coupled with cyclical market conditions as well as outdated technology, all took a severe toll on secondary smelting and refining in the United States.
Given the importance and complexity of copper recycling to our country, and indeed to the global economy, it is important to look at long-term trends to better understand where the industry was, where it is now and what the future may hold in store.
A NEW LANDSCAPE
Typically, when discussing production and consumption of copper, the point of reference is refined metal. But this requires explanation, as the supply of refined copper is a combination of primary material, or that which is mined from ores, along with scrap, or secondary material that is recycled. Further, copper scrap can be divided into two major categories: 1.) new scrap generated in the manufacturing process or 2.) old scrap, which could result from a building being torn down, old machinery being broken down or an automobile being dismantled. Depending on the grade of metal, scrap from either category may be consumed directly in another application, such as a foundry, where strength is more critical than purity, or in a brass mill, where the copper will be alloyed with other metals. Historically, lower grades of copper scrap that were not suitable for another direct application because of impurities, contamination or even market conditions would find their way to a secondary smelting and refining operation.
As a point of reference, in 1980, 1.69 million metric tons of copper were produced in the United States, of which, 1.25 million metric tons, or 74 percent, was from primary material, while 430,000 metric tons, or 26 percent, was from scrap processed through a secondary operation. At that time, six major secondary smelting and refining facilities were operating in the country.
The early to mid-1980s was a very difficult and painful period for the copper industry, as low prices, high labor costs and strict environmental requirements reduced output of metal overall, with secondary facilities being hit particularly hard, as some companies, including USMR and the PD Laurel Hill facility, were forced to close permanently.
By 1988, market conditions improved dramatically, but the structure of the industry was markedly different. That year 1.85 million metric tons of copper were produced, but secondary sources comprised just 115,000 metric tons, or 6.2 percent of the total. 1998 saw the peak in total domestic output of refined copper at 2.49 million metric tons, but it was also the final year for secondary production, as the last two remaining facilities threw in the towel in light of the high cost of regulatory and environmental compliance.
In looking at consumption, just as we saw with production, the numbers are considerably larger when scrap is included. In 2007, domestic consumption of refined copper was 2.15 million metric tons, of which copper rod mills used 1.61 million metric tons, or 75 percent of the total, while brass mills took in 481,000 metric tons, or 22 percent. However, total copper consumption in 2007, inclusive of scrap, was 3.04 million metric tons, with rod mills representing 1.64 million metric tons, or 54 percent of the total, while brass mills used 1.15 million metric tons, or 38 percent, with the remainder going to foundries, powder plants and other sectors.
HEADING EAST
If there is any curiosity in the numbers, it is found within the global breakdown of statistics. The United States is the largest economy in the world and, until 2002, was the largest producer and consumer of copper. The equation changed that year as China surpassed the United States in both categories. How did this transition occur? Some 20 years ago China began gradually moving from a centrally planned communist economy to a market-driven, quasi-capitalistic system. With this change the country marshaled its resources toward developing an export based economy, driven by low-cost labor and production. Further, it was free of environmental restrictions that existed elsewhere, and the doors were opened for foreign companies to invest or relocate their manufacturing operations.
CHART TOPPERS |
For additional charts that accompany this feature, visit the Recycling Today Web site at www. |
Throughout the subsequent 16 years, China’s production of copper rose 525 percent to 3.5 million metric tons by 2007, with the same ratios of primary and secondary material holding fairly constant. Thus, scrap consumption for refining climbed some 966,000 metric tons, or 568 percent, to 1.14 million metric tons, which does not include scrap used for direct consumption.
Where did the metal come from? All over the world, and specifically in large part from the United States.
TO LIMIT TRADE?
Despite the nonexistence of secondary smelting and refining in the U.S., consumers nevertheless continued to demand scrap, particularly in the brass mill sector. But foreign trade changed dramatically in 2000, as exports of copper based scrap began rising exponentially to satisfy the insatiable demand of furnaces in China, among other countries. From 315,000 metric tons in 1999, total exports of copper scrap more than doubled to 689,000 metric tons by 2003, thereby causing a shortage of scrap raw materials in the United States and forcing consumers to seek help from the government to limit exports of metal.
Within the U.S., lines were sharply divided between those who sought to limit exports to make more metal available to domestic consumers and the other contingent, who believed metal should be sold to the highest bidder, regardless of where they were. Ultimately the argument for free trade prevailed, as the government took the position that limiting exports would result in retaliation by foreign countries or lead to other protectionist measures. Clearly, this was a contentious issue, but not without precedent.
In 1984, as domestic producers were struggling to survive amid low market prices and the high cost of production, they petitioned the government for assistance to stem the tide of refined imports. Their argument was that foreign producers were not held to the same standard of environmental compliance as the domestic industry and that lower-cost foreign labor was subsidized by government programs. In 1984, President Reagan rejected the producers’ request, effectively saying import restrictions were "not in the overall national economic interest."
Historically, the United States has been a net importer of refined copper and a net exporter of copper scrap. In 1995 net imports of refined copper stood at 211,000 metric tons and rose 339 percent to 926,000 metric tons by 2005. During this same period, net exports of scrap doubled from 273,000 metric tons in 1995 to 543,000 metric tons in 2005.
The obvious question is, "Why would we export a vast amount of scrap that should be recycled here?"
The simple answer is the high cost of regulatory and environmental compliance. Ten years ago we saw the closure of the last secondary smelting and refining facility in the United States; thus, there is no home for much of that material to be recycled here.
TODAY’S CHALLENGES
Today, the copper industry and, indeed, global economies are facing severe challenges. The past five years saw rapidly rising prices driven by strong fundamentals and supercharged by cheap and easy credit that fostered excessive speculative trading. Those days are gone. Markets that once embraced risk have become risk adverse, and the theory of a "Super Cycle" in commodities that would hold prices aloft for many years to come has gone bust.
Nowhere was this more apparent than in the price of copper, being as it is the bellwether of economic activity. On July 2, 2008, spot copper closed on COMEX at $4.08 per pound. By year end, the price had collapsed to a low of $1.25, off $2.83, or nearly 70 percent.
In response to the downward spiral in global economic activity, governments worldwide and their respective central bankers have been injecting trillions of dollars into the financial system in an effort to stem the slide and to reignite economic growth.
In time, the excesses of the past several years will be eliminated from the system, setting the stage for recovery, to be followed by growth and expansion once again. As for copper, it too will recover, and while we will not see resurgence in smelting and refining of secondary copper in the United States, it would not come as any surprise to learn that someone, somewhere is developing an environmentally friendly process that will make it economically feasible to recycle more metal here.
The author is president of Newport, R.I.-based J.E. Gross & Co. Inc., a metals management and consultancy firm established in 1987. He also is publisher of The Copper Journal, an industry newsletter he created in 1989. He can be reached john.gross@copperjournal.com.
Get curated news on YOUR industry.
Enter your email to receive our newsletters.
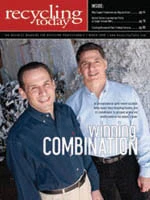
Explore the March 2009 Issue
Check out more from this issue and find your next story to read.
Latest from Recycling Today
- Astera runs into NIMBY concerns in Colorado
- ReMA opposes European efforts seeking export restrictions for recyclables
- Fresh Perspective: Raj Bagaria
- Saica announces plans for second US site
- Update: Novelis produces first aluminum coil made fully from recycled end-of-life automotive scrap
- Aimplas doubles online course offerings
- Radius to be acquired by Toyota subsidiary
- Algoma EAF to start in April