T
he Indian steel industry is headed for some excellent times ahead. Expansion is likely to come from a revival of domestic demand, with greater acceptance of Indian steel by the domestic automobile, components and consumer goods industries.In the past, the steel industry’s fortunes in India have hinged largely on the growth in the construction and other selected industrial sectors.
Recently, the government of India announced that it has approved plans to develop private cities in India, starting with a $9 billion private sector project near the outskirts of Bangalore. Construction on the new development is scheduled to commence this fall and to be completed in phases between 2006 and 2015.
The first phase of the 6,000-acre project will include 13.59 million square meters of built-up commercial space and 35,000 residential units. The project is Asia’s largest new city development project and is expected to become the model for new city developments in India. These current developments and trends in the Indian housing industry have already brought confidence back to the steel industry.
THE PRESENT TENSE. The 1990s were a vital and important period for the Indian steel industry. The "forbidden" environment has changed drastically with the post-liberalization scenario. The successor government to the one led by the late Rajiv Gandhi has made mindful decisions to privatize the industry by removing quantitative restrictions on foreign trade, opening up the sector to the entry of private players.
The result has been a lessening in the power of MSTC, a government agency that brought most of the ferrous scrap for India’s steel industry. The last 14 years has also seen inefficient steel mills with old-fashioned technology perish.
Newly fabricated steel is a unique material in that it often contains recycled steel. Each year, millions of tons of used steel from appliances, automobiles and construction materials are recycled by steel mills. This ferrous scrap is derived from a variety of sources, including new scrap generated within steel mills, production scrap in the form of off-cuts, stampings, turnings, etc., and old scrap derived from end-of-life products. Old scrap includes heavy scrap from large construction or railway equipment and light scrap, which includes scrap steel from auto bodies, ships and railroad cars. It is collected, cleaned and processed by cutting, shredding or bailing to feed steel-making furnaces.
In India, as in many places, it is much more cost effective to use steel scrap to make new steel than to mine iron ore and then smelt it in a blast furnace. It takes about 60 percent less power to make steel from recycled materials than it does from iron ore. Steel is environmentally friendly, because it is infinitely recyclable. Transportation of scrap is another major challenge: Low mass scrap is generally shredded or bundled, while oversized material is cut to size.
The construction activity in Asia is one of the major generators of scrap steel. Another main source of scrap is retired ships and repair activities. The worldwide push on environmental awareness is expected to enhance recycling, thereby contributing to an estimated annual increase of 7 percent in steel scrap recycling. But this may not keep pace with the overall increase in steel production, resulting in a shortage of scrap in the years to come.
Scrap prices are dictated by finished steel demand and prices. As global steel output continues to grow at record levels, it is not surprising that demand for scrap remains very strong and prices therefore are high. The demand for steel has gone up further in light of the post-tsunami rehabilitation work being carried out in the affected region, plus the earthquake in Gujrat and the major economic growth in India.
Scrap prices can be unstable and can cause severe trade and industry problems for steel producers who rely on scrap as their principal raw material.
Tata Expands Eastward |
Tata Iron and Steel Co. Ltd., an integrated steelmaker based in Jamshedpur, India, has completed the acquisition of Singapore’s largest steel company, NatSteel Asia. NatSteel has operations in seven countries: Singapore, Thailand, China, Malaysia, Vietnam, the Philippines and Australia. The acquisition has increased Tata’s capacity to 6 million metric tons per year, with company plans in place to boost production to 15 million tons per year by 2010. The growth plans include the addition of a 6 million-tons-per-year integrated mill in the state of Orissa, India, that is scheduled to come online in 2008. Tata Steel will supply semi-finished steel and billets to all NatSteel manufacturing facilities. At the time of signing the agreement in August, Tata Managing Director B. Muthuraman said, "NatSteel sources scrap for producing its products. However, we will be now supplying semis to NatSteel from Tata Steel’s existing resources in India." |
With strong demand worldwide, producers have had difficulty passing higher scrap costs on to their customers, either by way of a surcharge or by adjusting base prices. The improvement in world steel prices over the last couple of years is largely attributable to economic developments in Asia.
BRIDGING THE GAP. China has developed into the largest global consumer of steel. With internal steelmaking capacities on the rise, it may soon meet its demand internally. In fact, as per reports, China’s exports of steel exceeded its imports last year. However, export and import ratios can often be misleading, and the global prices for scrap will govern the competition.
The supply-demand gap is expected to increase and this will drive steel prices upward at a time when the global steel industry is not prepared. The steel mills in India will have to remain global to stay in business.
The consequence of this sharp increase in demand for scrap metal has bolstered prices significantly, with some scrap prices rising as much as three-fold in the past few years. The U.S. Commerce Department recently reported that the value of exports of nonferrous scrap increased more than 25 percent in 2004, nearly the same in 2003, with India ranking fifth in size as a market behind China, Canada, South Korea and Taiwan.
The pace of global economic growth continues, with the International Monetary Fund estimating world output of 3 percent to 4 percent last year, but with a more pronounced expansion seen in many of the developing countries. Economic expansion last year in China was reported to be 9 percent to 10 percent, while India’s economic expansion was nearly 8 percent, with only a moderate easing anticipated for this year.
This torrid rate of growth requires the importation of a steady flow of primary commodities, as well as scrap metals, which offer more efficient feed material for the steel industry.
Steelmaking capacity in India is projected to expand rapidly throughout the next decade, from its current 35 million tons up to some 90 million tons per year. India is one of the world’s largest iron ore producers. In addition, Indian steel producers are among the lowest cost producers in the world, providing a cushion against a fall in prices.
It is estimated that the Indian steel industry could import more than 2 million tons of scrap this year for stock. More than 70 percent to 75 percent of scrap accumulated for recycling in Delhi last year, for example, was imported.
SAFER SOURCES. The availability of less expensive war scrap, principally from the former Iraqi armed forces, has made for an attractive source of added supply. However, material collected from the demolition of obsolete military facilities and equipment has often included munitions or other potentially dangerous items.
This eventuality was borne out in a fatal explosion at steel facility in Ghaziabad, a suburb of New Delhi, in 2004 that killed 12 and injured many more. The cause of the explosion was found to be live ammunition, believed to have been in the scrap metal imported from Iraq. Because of the explosion, the scrap shipments required more stringent inspections, causing delays and price hikes in the domestic market.
War scrap is usually popular because it contains copper and tank metal. Iraq war scrap is available more cheaply because it contains copper. Debris from the increased supply coming in from Iraq has made it a big source of scrap, rich in live ammunition and explosives. Most developed countries ban import of scrap from war zones; others have strict rules of entry, including third-party inspection.
Indian customs authorities recently enacted new rules requiring pre-shipment inspection certificates from approved local export agents. All inspections must declare "no war material" certificates along with the shipment. Last October, Indian customs added further safety measures, requiring inspections of all unshredded imported scrap before it leaves the port.
But even with these added legislative precautions, it remains difficult for the Indian government to protect against the possible occurrence of receiving improperly classified imported scrap. Metal scrap and war scrap from Iraq is often trans-shipped to Dubai or Iran and re-labeled before being sent on to Indian ports, thereby avoiding or bypassing the "Rules of Origin" certification requirements.
Improperly classified imports of scrap metal are not because of the absence of a strict governmental legal regime, rather they are because of the difficulty in implementation and a lack of enforcement at the local level.
The Indian government’s ability to ensure the safety of the workers in the steel mills and to enforce strict regulations for the import of scrap metal will depend on its success in promoting policies and providing adequate education at the local level.
The downside to the modified security measures and added spot inspections at already congested ports has been to further slow the flow of imports and, ostensibly, to firm already rising scrap prices. In response, the Indian government increased the number of ports for imports of scrap from 15 to 17 and has completely lifted import duties on melting scrap.
Separately, import duties on retired ships for ship breaking were lowered from 15 percent to 5 percent. India has the largest ship breaking industry in the world. High freight rates have effectively lowered the number of available ships to be scrapped, as many are kept in service to meet increased freight demand. The amount of scrap steel derived from the ship breaking industry in India has fallen to 1.2 million tons in 2004-05 from a high of 3 million tons recorded in 1998-99.
The author is a director of A-1 Specialized Services & Supplies Inc., Croydon, Pa., a recycling firm specializing in catalytic converters.
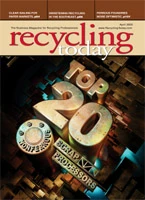
Explore the April 2005 Issue
Check out more from this issue and find your next story to read.
Latest from Recycling Today
- Fitch Ratings sees reasons for steel optimism in 2025
- P+PB adds new board members
- BlueScope, BHP & Rio Tinto select site for electric smelting furnace pilot plant
- Magnomer joins Canada Plastics Pact
- Out of touch with reality
- Electra names new CFO
- WM of Pennsylvania awarded RNG vehicle funding
- Nucor receives West Virginia funding assist