
Getting compressed
During the hauling process, lightweight aluminum cans often are crushed and flattened into two-dimensional “pucks,” making it difficult to separate them effectively with
Republic Services’ St. Louis MRF Manager Brent Batliner realized small pucks of aluminum were being separated with glass at the polishing screen. Those pucks were, of course, too big for the glass screen and so were being discarded as trash. When Batliner checked the MRF’s residue line, he saw that 60 to 80 cans per minute were being trashed. Republic’s St. Louis MRF processes 300 tons per day of single-stream material, 200 tons of which are from residential collections.
Seeing results
With the installation of the MRF’s second eddy current, Republic’s St. Louis MRF has recovered an additional 15 tons per month of aluminum.
Because the second eddy current is ejecting aluminum from the MRF’s glass residue conveyor that is loaded with small pieces of debris, Batliner says he has been able to sell this material for 10 cents less per ton than the truckload per week of bales that are recovered by the MRF’s original eddy current.
But he says the investment was worth being able to recover the additional 30,000 pounds per month. The material recovered from the second eddy current separator is
“Look at your trash line and count the cans,” Batliner advises MRF operators. “We’re getting crushed cans, pieces of cans and smaller aluminum cans out of residue and into bales.”
In addition to
“Look at your trash line and count the cans. We’re getting crushed cans, pieces of cans and smaller aluminum cans out of residue and into bales.” – Brent Batliner, manager, Republic Services’ St. Louis MRF
As a result of this additional optical sorting equipment, Republic’s Seattle MRF is diverting nearly an additional truckload of UBCs per month.
As the Republic MRF in St. Louis did, the Waste Management MRF in Elkridge, Maryland, also installed a second eddy current on the glass discharge line of its sorting system. The company had identified that small, crushed UBCs could fit through the gaps in the sizing screen, ending up in the residue.
After the installation of the second eddy current, that facility saw an increased capture rate of about 15 tons per month of aluminum.
Mike Taylor, director of recycling operations at Waste Management, says, “Retrofitting the second eddy current to fit on the glass discharge line wasn’t easy, but it was worth it to capture the material.”
Aiming for high quality
With high-quality material in mind, Eureka Recycling installed several upgrades to the nonprofit’s Minneapolis MRF in 2016 to assist in better separation of paper from containers. Single-stream collection and the compaction of collected material made it increasingly challenging to keep containers out of paper grades and vice versa. Eureka’s single-stream MRF is capable of processing 75,000 tons of recyclables annually.
Kate Davenport, co-president of Eureka Recycling, says, “We saw an increasing number of flattened aluminum cans and plastic bottles in our paper, so we worked with our equipment vendor to install additional screens and ballistics as well as a bigger second eddy current. This helped to reduce the containers in our paper grades by 50 percent.”
She continues, “Because of our philosophy around high material quality, we had already made the investments in equipment to address the increased demand for material quality coming out of National Sword,” she says.
The company’s second eddy current separator, supplied by
For Eureka’s MRF and those mentioned previously, installing a second eddy current has significantly increased the amount of aluminum they capture. Aluminum’s high value means that each and every can should be correctly sorted, baled and sold.
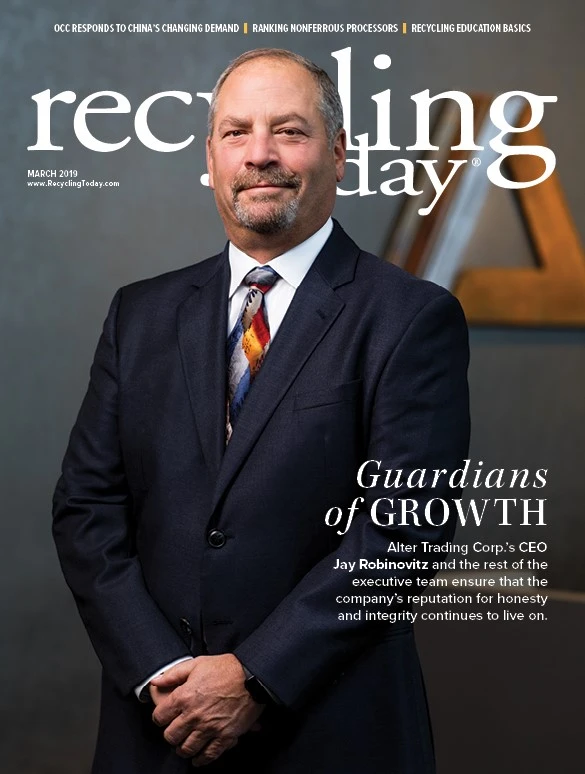
Explore the March 2019 Issue
Check out more from this issue and find your next story to read.
Latest from Recycling Today
- APR, RecyClass release partnership progress report
- Clearpoint Recycling, Enviroo sign PET supply contract
- Invista expanding ISCC Plus certification program
- Redwood partnership targets recycling of medium-format batteries
- Enfinite forms Hazardous & Specialty Waste Management Council
- Combined DRS, EPR legislation introduced in Rhode Island
- Eureka Recycling starts up newly upgraded MRF
- Reconomy Close the Gap campaign highlights need for circularity