
When Sam Advani bought integrated electronics recycler Metech International LLC in May of 2005, the company was experiencing financial difficulties and suffering from operational inefficiencies. Under his leadership, Metech embarked on a restructuring process, streamlining its operations while further strengthening its reporting capabilities.
Before Advani entered the picture, Metech was owned by a South African group. But Metech Business Development Manager Jim Gardner prefers not to reminisce about that time, saying simply that Metech was "struggling" financially and that Advani "rescued" the company.
STARTING OVER
When Advani purchased Metech, the company already had passed through a number of hands, tracing its origin back to 1973 in Woonsocket, R.I. At that time, the company was known as Refinemet and its focus was on precious metals and tantalum recovery. Gardner says Refinemet expanded into electronics recycling by "default" in the late ’70s and early ’80s because customers like AT&T, Burroughs, DEC and IBM had large pieces of equipment that they were retiring.
In 1983, shortly after expanding into processing end-of-life electronics, Boliden, a smelting and mining company based in Stockholm, Sweden, purchased the firm and renamed it Boliden Metech. Trelleborg, which then owned Boliden, spun off the smelting operations, though it retained Metech. In 2002 Viking Investment and Asset Management, based in Johannesburg, South Africa, bought Metech.
"Metech was in somewhat of a holding pattern," Advani says of the company at the time he purchased it. "A lot of the problems were based on the physical location. It was a very inefficient plant in Mapleville (Rhode Island), and the operational costs were very high."
One of Advani’s first moves as Metech’s president and CEO was to close the Mapleville plant. He relocated the corporate offices to Worcester, Mass., and the company designed a processing line—including four shredders of different types, conveying lines and downstream separation equipment—for its new 85,000-square-foot plant.
"Right away, the operating costs dropped in half," Advani says. "You can imagine what that does for the bottom line."
As part of the restructuring, Metech discontinued receiving precious-metals-containing hazardous waste and scaled back its other local precious metals refining business that was not adding value to the company’s focus on integrated electronics recycling, Advani says.
"The real future of our business is what we call integrated recycling," he says. "We like to go into the large OEMs (original equipment manufacturers), multi-national accounts, and be able to offer everything. It’s not specifically precious metals, it’s not specifically computers; it can be the whole range of solutions."
Garner adds, "Our customers are primarily OEMs in the networking, data storage or telecommunications business who require that their equipment be dismantled and recycled, not remarketed. Therefore, remarketing of systems is a very small portion of our business."
Gardner says Metech serves OEMs in electronics-related industries, primarily, though the company is increasing its market in the non-electronic corporate area as well as in the legal, financial, medical and retail sectors.
As part of the restructuring, Metech concentrated its precious metals sampling at its Gilroy, Calif., plant. While both sites are equipped for end-of-life electronics recycling and precious metals sampling, the Gilroy plant includes thermal reduction capabilities to process a wider range of precious metals.
Although Advani did a fair amount of restructuring when he purchased the company, there is one thing he didn’t change: Metech’s detailed tracking and reporting capabilities.
DETAIL ORIENTED
Details can be a source of frustration for many businesses, but particularly in the electronics recycling industry, where downstream accountability is important.
Thanks to Metech’s start as a precious metals processor, the company already tracked all of the materials entering and exiting its plants with painstaking detail through its Accountable Resource Management program. "That was because we were sending precious-metals-containing materials we had sampled and settled/paid for to refiners and smelters and we had to compare their recoveries to ours," Gardner says. "We have continued to do the same thing with base metals, plastics, even things as mundane as cardboard. We know where everything goes and we audit everything."
When the company receives material from a customer, it is assigned a lot number that follows each of its fractions throughout Metech’s operations and then onto final consumption.
To simplify the auditing of its downstream vendors, Metech works with a select group of companies.
"In the integrated recycling industry, one of the major factors or drivers is really environmental liability and how the title passes from one step to another," Advani says. "When the material comes to us, the customer is essentially passing title of that product to us. When they do that, they also pass the environmental liability. So it benefits us to know where our products are going."
For Metech, its Accountable Resource Management program is more than a tracking system, it’s a business philosophy.
International Scope |
Metech International LLC, headquartered in Worcester, Mass., has established a presence in the Asia Pacific market by partnering with Integrated Recycling Industries Inc. (IRI), based in the Philippines, as well as by establishing its own facilities in the region. Sam Advani, president and CEO of Metech, says the companies’ cultures are a good fit. “We realized there are a lot of synergies between Metech and IRI and we had a lot of similar customers, a lot of the same customers, so we entered into a strategic partnership,” he says. “We have been very fortunate to have the right partner to start our foray into Asia Pacific.” Metech also operates a facility in Penang, Malaysia, that measures 25,000 square feet. The Penang plant, which is also ISO 9001:2000 and ISO 14001:2004 certified, is equipped for the dismantling and recycling of electronic equipment, certified destruction, component recovery and resale, segregation of nonferrous and precious metals for recycling, hard drive erasure or physical destruction and recycling of plastics. The facility can process nearly 18 millions pounds of electronics per year. The company also operates a plant in Thailand. According to Advani, Metech plans further expansion in the Asia Pacific region. “We absolutely see more growth, probably through acquisitions and franchising, most likely,” he says. “One of the things we are discussing with IRI is doing a joint venture facility under the Metech brand.” Advani adds, “In Asia we already have the largest presence of any U.S. or European recycler. I would imagine that in the next year, we are going to be looking at expanding that presence into China, possibly Vietnam; it just depends on where the market takes us. |
"Metech has developed its business and reputation around the concept of Accountable Resource Management," Gardner says. "This means we apply the highest standards of accountability and best practices to all aspects of our integrated services program."
Advani defines the four pillars of Accountable Resource Management as environmental liability protection, intellectual property protection, recovery and return of asset value and accountability and tracking of materials.
SAFELY AND SOUNDLY
Sponsored Content
Labor that Works
With 25 years of experience, Leadpoint delivers cost-effective workforce solutions tailored to your needs. We handle the recruiting, hiring, training, and onboarding to deliver stable, productive, and safety-focused teams. Our commitment to safety and quality ensures peace of mind with a reliable workforce that helps you achieve your goals.
For optimal security, Metech’s standard practice is to shred hard drives, though the company can overwrite drives using software from the Finnish company Blancco at its customers’ requests.
To further ensure the security of its operations, Metech does a criminal background check on each employee. Hourly employees are also subjected to drug testing at their pre-employment physical and if he or she is involved in an on-site accident. As part of Metech’s environmental health and safety program, processing employees receive annual physicals that include pulmonary testing as well as lead and cadmium tests twice yearly.
Shift supervisors also screen employees for metals when entering and exiting Metech’s facilities, which are equipped with alarm systems, keycard access and closed-circuit cameras.
"Security is a major concern for several reasons," Advani says. "One, we don’t want any customer intellectual property or products walking away from the plant. That could be anything from a manual to a CD to a prototype chip or circuit board." He continues, "Two, we actually have physical precious metals sitting in our plants—gold, silver, platinum, palladium, copper and rhodium—and you don’t want that walking away either, because that can be millions of dollars walking out your door."
To protect its operations and its customers, Metech also carries several million dollars’ worth of pollution liability, general and commercial liability and freight insurance. "These days, most multi-nationals require pretty high insurance coverages from their vendors, at least their large vendors," Advani says. "We usually meet and exceed those requirements."
Metech’s facilities are also ISO (International Organization for Standardization) 9001 and 14001 certified, meaning the facilities conform to ISO’s quality and environmental standards and strive to achieve continual improvement. In addition, Metech is an International Association of Electronics Recyclers Certified Electronics Recycler, a certification program tailored to the electronics recycling industry.
Non-compliance reporting plays an important role in maintaining Metech’s ISO certification. "Because we are ISO certified, we have procedures and policies in place for everything we do, and when something new comes up, we’ll create one," Advani says. "Whenever I find something that is not 100 percent inline with our policies and procedures, I call for a nonconformance report, which means that our ISO Manager Andrew McManus will investigate the issue, find out what happened, institute corrective action and then track that. We take our ISO certification very seriously and we use it as a tool to improve our business."
Metech’s five facilities process nearly 8,000 tons of electronics-related material worldwide, so such safeguards are a vital part of its operations, particularly as it looks to expand.
SEIZING OPPORTUNITIES
"There are a lot of second- and third-tier electronics recyclers that are doing very well because electronics recycling is a growth industry, but we see that as a good thing," Advani says. "We see them as future customers, feeders to us, and we’ll be the consolidator and ultimate processor," he adds.
Another area where Advani and the Metech management staff see opportunity is in partnering with asset management companies to act as their processing arm. "We work with them to construct comprehensive programs based on what they want to do. We act as the facility," Advani says. "We do a fair amount of direct business in the end-of-life arena, but we see more and more opportunities partnering with asset management companies to serve as their back end."
With Metech’s detail-oriented approach to electronics recycling, the company is sure to catch the interest of asset management firms, smaller electronics recyclers and other generators of end-of-life electronics that are seeking accountability from their electronics recyclers.
The author is managing editor of SDB magazine and can be contacted at dtoto@gie.net.
Get curated news on YOUR industry.
Enter your email to receive our newsletters.
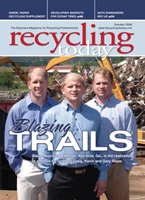
Explore the October 2006 Issue
Check out more from this issue and find your next story to read.
Latest from Recycling Today
- Recycled steel price crosses $500 per ton threshold
- Smithers report looks at PCR plastic’s near-term prospects
- Plastics association quantifies US-EU trade dispute impacts
- Nucor expects slimmer profits in early 2025
- CP Group announces new senior vice president
- APR publishes Design Guide in French
- AmSty recorded first sales of PolyRenew Styrene in 2024
- PRE says EU’s plastic recycling industry at a breaking point