_fmt.png)
Advancing the circular economy for plastics requires transformation across the recycling system, from collection all the way to expansion of end-use markets. One of the biggest challenges facing the plastics recycling industry today is separating all of the various polymers entering the recycling stream.
Several steps throughout the supply chain play a role in the success of this separation, starting with the design of the package to consumers correctly placing items in the appropriate recycling bins to the capabilities of material recovery facilities and ultimately the actual plastics recycling plants. Each step in the supply chain is critical to generating usable feedstock for recycling.
Inseparable materials limit recycling
_fmt.png)
High-density polyethylene (HDPE) is one of the most commonly used and recycled plastics today. However, within the recycled HDPE stream, polypropylene (PP) contamination is a significant problem.
The specific challenge that PP presents for HDPE recycling is that globally, the primary method to separate plastics is by density using a sink-float process—both HDPE and PP float. When PP levels exceed approximately 10 percent in the recovered stream, the resulting recyclate becomes brittle and might not be able meet the physical demands of many applications, including blow molding and pipe. These bales generally either are downcycled to lower-value applications or landfilled. To maximize the quality of the HDPE recycling stream, reduce PP contamination and not compromise end markets, ideally the full package—the closure and the container—would be made from HDPE.
Blow-molded HDPE containers use PP closures, which have been preferred because of legacy closure designs, materials and molding technologies. Blow-molded HDPE containers are well-suited for a variety of liquids; common products in this format include shampoo, detergent bottles, automotive oils, juices and milk. However, these HDPE containers have been lightweighted significantly, while the closures have not, resulting in a greater proportion of PP to HDPE by weight.
Fortunately, new technology has been developed that enables HDPE to replace PP closures, meeting the package performance requirements on HDPE bottles while delivering a more recyclable total package.
The value of monomaterial packaging
Using HDPE instead of PP or alternative materials to make the closures on HDPE blow-molded containers provides two sustainability benefits and sets the stage for improved circularity:
The U.S. has robust recycling infrastructure for HDPE bottles, which provides the framework for a sizable supply of recycled HDPE (rHDPE), including food-contact options. The volume currently available, coupled with the potential growth of rHDPE, should provide a large and reliable stream to use in HDPE closures. By moving to HDPE in the closure, a true circular economy can be achieved as both the closure and the container can be recycled and returned for use in the same package.
Advancements enable the monomaterial capped container
Advancements across the value chain, from materials to molding technologies and designs, enable a new future where HDPE is well-suited for caps on blow-molded bottles.
Materials: On the material side, advanced HDPE resin designs and formulations provide performance characteristics that enable this leap forward in packaging sustainability. Modern resins provide exceptional environmental stress-crack resistance (ESCR) and creep-resistance performance, with bimodal resins showing the most improvement. This combination of properties not only enables the usage of HDPE in these closures but also allows for developing lighter parts that deliver on the application’s needs while also minimizing material consumption, reducing the carbon footprint as well.
In addition, HDPE designed for recycling is better positioned to support circularity. Mechanical recycling involves re-extrusion of the shredded, recovered plastics, which introduces additional heat and shear. This rigorous process can degrade the properties of the plastic. While the HDPE resins of the past only had to consider a single use, modern HDPE resins with their robust ESCR and creep resistance are more capable of incorporating higher quantities of degraded recycled content while still delivering a product that performs as well as closures made with 100 percent virgin resin.
In addition to success in converting traditional PP closures to HDPE, innovations in mold design and molding have leveraged the advantages of modern HDPE.
Thoughtful formulation of stabilizing additives further minimizes the effects of the recycled content. This allows for even higher levels of recycled content by boosting the quality of the recycling stream. Although high levels of antioxidants can be loaded into HDPE to compensate for degradation, this is not a long-term solution. Food and Drug Administration limits include active and degraded additives, and advanced additive formulations ensure the longest possible circular life of plastic while meeting regulatory limits. Through this forward thinking in design, modern HDPE is well-positioned to support a more sustainable future.
Molds and mold technology: In addition to success in converting traditional PP closures to HDPE, innovations in mold design and molding have leveraged the advantages of modern HDPE to push the limits of closures. By designing molds with the intent to accommodate for the ESCR properties of HDPE and rHDPE, a higher level of recycled content can be added successfully. The latest hot runner technology—the system that delivers the resin from the extruder to the mold—moderates resin temperature through the runner system and has been highly successful, enabling not only conversion from PP to HDPE but achievement of HDPE closures with 100 percent recycled content.
Mold designers also have succeeded in leveraging the advanced material formulations to optimize wall section and hinge performance to achieve lighter parts without a sacrifice in key performance requirements. Thoughtful use of the favorable molding characteristics of HDPE also has enabled easier demolding and simplified tool design.
Advancements in mold technologies also have benefited the carbonated soft drink segment, which often uses two-piece, mixed-material closures. Sophisticated designers have used the relative flexibility of HDPE to enable higher- performance sealing systems into robust and often groundbreaking single-piece closures. These closures reduce contamination in the HDPE stream, resulting in higher-quality recyclate overall.
An integrated Design
The goal of a monomaterial package is full recyclability. To truly close the loop and advance the circular economy, we must be able to use all the recyclate from these packages. Integration across the value chain allows the brands to design their parts with the materials in mind—both HDPE and rHDPE.
Technological innovations in resin, design and molding mean brand owners no longer need to choose between functional parts for their products and optimizing materials for the HDPE recycling stream. HDPE can be used for blow-molded container closures and is the right material for a sustainable future.
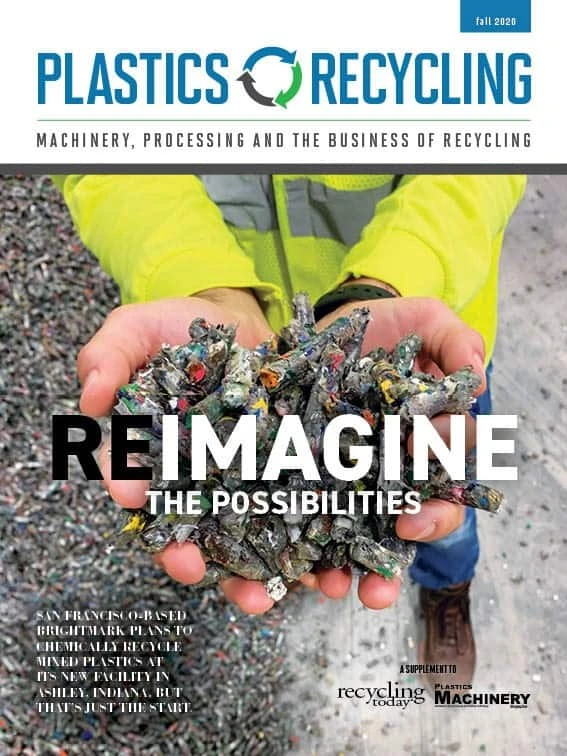
Explore the Fall 2020 Plastics Recycling Issue
Check out more from this issue and find your next story to read.
Latest from Recycling Today
- Athens Services terminates contract with San Marino, California
- Partners develop specialty response vehicles for LIB fires
- Sonoco cites OCC shortage for price hike in Europe
- British Steel mill’s future up in the air
- Tomra applies GAINnext AI technology to upgrade wrought aluminum scrap
- Redwood Materials partners with Isuzu Commercial Truck
- The push for more supply
- ReMA PSI Chapter adds 7 members