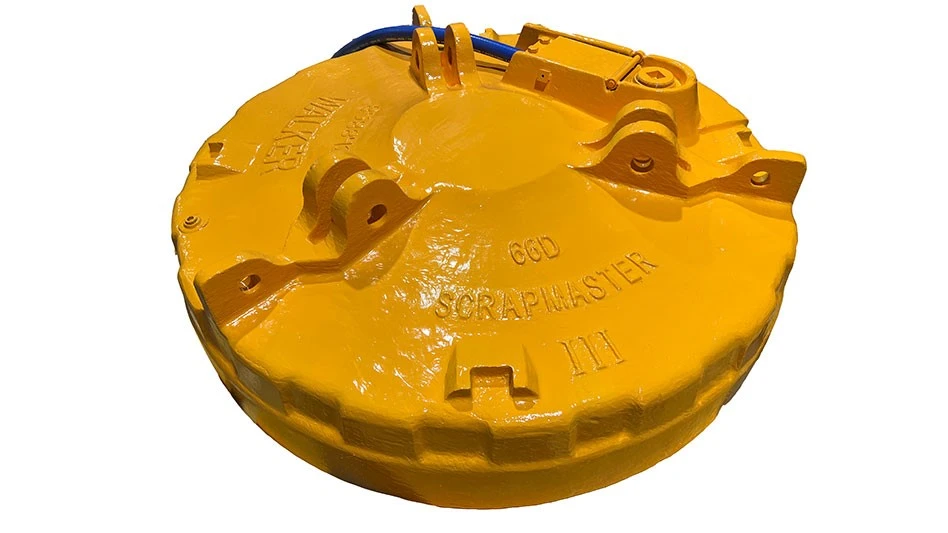


of Industrial Magnetics Inc., says IMI is working hard
to keep recyclers supplied in 2022.
Supply chain issues have been in the headlines since COVID-19 became a global economic factor in the first quarter of 2020. Dennis O’Leary, chief business development officer of Industrial Magnetics Inc. (IMI), says the magnetic equipment industry has been as hard hit as any other by such issues, especially because of its reliance on material from China.
O’Leary says the early part of this decade has involved IMI navigating “delays in receipts of raw magnet material, with largely the sole source being China, and with the related shipping, port of entry and customs delays.”
At the same time, IMI has been consolidating its production and service operations at its expanded Boyne City, Michigan, headquarters complex. That project, still underway, is allowing IMI to further integrate the Walker Magnetics product lines it acquired in early 2021.
Finding answers to difficult questions
O’Leary says IMI’s growth during the last five years, including its Walker acquisition and that of separation technology provider Javelin Equipment in 2017, prompted questions as to how IMI could best serve the wider North American and global market.
One of the foremost answers has involved consolidating IMI’s product line and people onto one corporate campus. “As part of the asset acquisition of Walker Magnetics, we moved its two facilities into our 37,000-square-foot expanded space here at headquarters in Boyne City,” says O’Leary. “This will allow us to better design, build and service the Walker brand products by centralizing it all under one roof.”
The benefits of that project have included bringing the company’s salespeople, product developers and problem solvers under one roof. Later this year, the full objective should be achieved. “We are due to complete phase two of our facility value streams in just a few short months, and that will create additional efficiencies on the manufacturing floor to properly accommodate demand for new builds and repair work,” O’Leary comments.
He is clear that wider global supply chain issues are not evaporating as of mid-2022 but adds that IMI will continue to work with customers and vendors to navigate them.
“We have worked with our vendors to create a process that scales as we grow as opposed to a knee-jerk ‘give me everything you have’ reaction,” O’Leary says about IMI’s approach to serving the market’s need for both permanent magnets and aluminum and copper magnetic coils.

Ready to serve in all markets
IMI’s capability to supply a broad product line of lifting and separation magnets used by the scrap recycling industry means magnetic and conductive metal shortages have affected it on all fronts.
Disruptions in supplying rare-earth materials from China have presented challenges in making permanent magnets, and global metals market tightness has been a hindrance when making electromagnetic products.
“On the electromagnet side of our offerings we have seen similar delays in aluminum and copper we use for coils, again due to material availability,” says O’Leary.
There is no one solution to the challenge, he adds, which is frustrating for IMI team members and channel partners. “Whether we are commissioned to repair an existing magnet or build a new one, each requires permanent magnet material or coils,” he notes.
The enduring nature of permanent magnet technology could be a mark in its favor if supply chain disruptions and materials scarcity remain the norm. O’Leary says, “Scrap and electro lifting magnets are generally ideal for these markets. Pivoting to the use of permanent lifting or separation technologies can help to bridge the supply/demand inequity.”
In the meantime, O’Leary is clear that “navigating the acquisition of a legacy brand through a global pandemic, coupled with a labor deficit and supply chain shortage, has been a challenge.” The recent stretch has at times been frustrating for IMI and its customers, he acknowledges.
Part of the frustration, however, is linked to the growing activity and demands of a healthy scrap recycling industry. O’Leary says that provides IMI with the incentive to complete its expansion project and prepare to serve a dynamic recycling sector.
A wide product horizon
The IMI acquisition and consolidation strategy has allowed it to offer a horizontal product line that can serve scrap recyclers across numerous applications.
O’Leary says IMI and its Walker and Javelin brands each had established themselves firmly in the scrap market. The brands might have shared a similar customer base, but they did so offering “vastly different products,” he notes.
Scrap recyclers who work with IMI and visit its growing Boyne City complex will witness the fabrication of lifting magnets the metals recycling industry has relied upon for as long as ferrous scrap has been handled, as well as complicated nonferrous metal sorting systems.
O’Leary’s message to the scrap market is that IMI has positioned itself to provide any magnetic solution that can help make processors more efficient and profitable. Supply chain hiccups have created delays to deploying those solutions during the last two years, but IMI is working hard to serve recyclers.
“The opportunities that lie ahead to meet the demand for the products we manufacture are encouraging, and we look forward to satisfying that demand,” O’Leary says.
Global material supply issues cannot be waved away, he adds, but IMI is doing everything in its power to prepare for circumstances as they change. O’Leary says, “There are still many barriers, as previously mentioned, but when the pendulum swings, we will be even better positioned to meet our customer and channel partner requirements.”

Explore the July 2022 Issue
Check out more from this issue and find your next story to read.
Latest from Recycling Today
- ReElement, Posco partner to develop rare earth, magnet supply chain
- Comau to take part in EU’s Reinforce project
- Sustainable packaging: How do we get there?
- ReMA accepts Lifetime Achievement nominations
- ExxonMobil will add to chemical recycling capacity
- ESAB unveils new cutting torch models
- Celsa UK assets sold to Czech investment fund
- EPA releases ‘National Strategy to Prevent Plastic Pollution’