
As Recycling Today readers know, there has been a steep jump in the demand for ferrous scrap to feed steel mills throughout the world within the last few years. This has created greater demand for auto hulks, white goods and other sourpces of obsolete scrap. This hunger for scrap metal has drawn attention to the ship scrapping industry, although sometimes it’s been negative in nature.
While the high-value ferrous scrap from these vessels would be an ideal raw material for steel mills, much concern surrounds the levels of toxic material that are released into the water and air. Many critics of the ship dismantling industry also point to its predominance in developing countries such as Bangladesh and Pakistan, among others. The inherent danger associated with ship dismantling is also cited by some as a concern.
However, Bay Bridge Enterprises LLC, a Chesapeake, Va.-based ship dismantler, seeks to overcome the hysteria about dangerous conditions and to focus on the company’s environmentally compliant operations.
ACCENTING THE POSITIVE. While Bay Bridge has been in operation for only five years, its Chesapeake site has operated as a ship breaking facility since 1958. Bay Bridge is one of six U.S. salvage recyclers to get the U.S. Maritime Administration’s (MARAD) "Green Certified" designation. According to representatives from the company, Bay Bridge has never had an environmental violation, nor has the company had a time-lost worker accident in the last four years.
Bay Bridge hopes this information will help to distance it from many of the negative stories that continue to circulate about ship dismantling facilities.
Mike Dunavant, president and CEO of the firm, says the company has been actively involved in much of the decommissioning of the James River Fleet (often referred to as the Ghost Fleet). These projects bring Bay Bridge scrutiny from a number of federal and state inspectors.
While many companies would complain about the multiple inspection channels, Dunavant welcomes the scrutiny. He says he feels that the company’s reputation allows Bay Bridge to stand above many other firms that might have a less environmentally focused operation.
While acknowledging that some companies have engaged in questionable practices, Dunavant says that things have changed. "Ship breaking used to be bad, bad, bad," he says. "During the 1950s, ’60s and ’70s that was the case. However, now, environmental issues have become more intense, resulting in higher standards for ship breakers in the United States."
While MARAD is attempting to have many vessels scrapped, it isn’t an easy job. And for those companies interested in bidding on a project, the payoff could be far down the road.
Presently, only a handful of companies in the United States are capable of handling many of the large vessels that need to be scrapped by MARAD. This does not include the numerous private commercial vessels, such as tugboats and barges, that also must be dismantled.
Bay Bridge is one of a handful of domestic ship breaking firms in the Unites States that can handle Navy vessels. Other domestic ship breakers falling into this category include International Shipbreaking Ltd., ESCO Marine Inc., Marine Metals Inc. and All Star Metals LLC, all located in the Brownsville, Texas, area.
DEVELOPING A SINGLE FOCUS. While Bay Bridge has carved out a healthy niche as a dismantler of waterborne vessels, the company did not begin as a ship dismantling firm.
As Dunavant notes, Bay Bridge started as one of the largest scrap yards on the East Coast. The company had equipment and space that allowed it to handle many of the materials that traditional scrap yards handled in addition to its ship dismantling operation. However, in 2003, Bay Bridge opted to sell its processing center and equipment to Sims Group, focusing exclusively on ship dismantling.
In addition to selling its scrap operations to Australian-based Sims Group, Bay Bridge took one larger step still and sold itself to Adani Global, an India-based conglomerate. The sale, completed last June, has given Bay Bridge greater economic backing while also allowing it to remain free to conduct business without any significant changes, Dunavant says.
The result of the sale is that Bay Bridge Enterprises LLC is a wholly owned subsidiary of Adani Virginia Inc., which is owned by Adani Exports Ltd., based in India.
Dunavant estimates that perhaps as much as 95 percent or more of the material on a vessel can be marketed as ferrous scrap. He adds that the metal plate and structural steel is of superior quality. "The metal on the ship is high quality. It was milled in the 1940s, ’50s or ’60s." Dunavant adds that material of that purity is rare nowadays. The same goes for the nonferrous metal, which the company also markets.
While being able to strip high quality metal from vessels is a major plus for Bay Bridge, it proximity to Sims is such that transportation costs to the company are practically negligible. "Basically, we are talking about moving the scrap metal about 12 yards to the Sims operations," Dunavant says.
While it may sound like an easy operation, before Bay Bridge begins the time-consuming process of dismantling a vessel, it undertakes a significant number of steps that are often rigorous in scope and that include multiple parties and consultants.
NOT SUCH A SLAM DUNK. On the surface, the process seems like a no-brainer: Bid on a project, get paid for the ship and then sell the scrap metal for a high price.
However, the number of variables involved makes this task less of a slam dunk and more of a calculated risk.
While a company such as Bay Bridge will bid on a host of vessels, it may be months before it is awarded a contract.
Additionally, as many can attest, the volatile nature of the scrap industry could swing to a level that might make job far less lucrative than originally thought if scrap metal prices show a significant decline.
Before the company even puts in a bid with MARAD, it sends an asbestos team and a tank subcontractor out to the ship to determine the cost to rid the vessel of asbestos and fuel. After that Bay Bridge then sends a marine surveyor to the vessel to make sure it is seaworthy and can be towed. Then, the company seeks approval from the U.S. Coast Guard to tow the vessel to the ship-dismantling yard. After receiving approval, Bay Bridge may need to use two to three tugboats to transport the vessel to its facility.

When the vessel finally reaches the ship-scrapping site, the company still has to stay in constant contact with a number of government agencies.
Rebecca Kuntz, Bay Bridge’s environmental manager, says that the company has to file a Gantt chart with MARAD. The Gantt chart, essentially a project flow chart, gives MARAD updated information on the progression of the ship dismantling process, including the duration, the steps to be taken and any particular issues that might crop up. The company is expected to record all the steps in the process it undertakes the strip the vessel.
Kuntz says Bay Bridge welcomes the ongoing dialog with MARAD. "Every two weeks we check in, and we get daily calls (from MARAD) to find out how we are doing," she says.
In addition to constant checks with various government agencies, Bay Bridge performs daily checks of the air quality on the vessel and also brings on board a marine chemist who checks to see if it is safe to perform "hot work," Dunavant adds.
Also, Kuntz says the company has to perform detailed daily reports noting how much fuel was extracted and the extent of the scrapping. "If I tell MARAD that I have removed the super structure, it better be that way," Dunavant says.
The Virginia Department of Environmental Quality also inspects Bay Bridge’s operations regularly, and OSHA comes by at least once a month to check on the operation.
What has driven the ship breaking industry from near extinction less than 10 years ago to its growing role has been the twin pressures to scrap many of the mothballed vessels that the Maritime Administration is mandated to dispose of and the growing hunger for scrap metals.
MARAD maintains three fleets of decommissioned vessels in Virginia, Texas and California.
Heavy criticism about shipping decrepit vessels across the Atlantic or Pacific oceans to facilities in developing countries that lack rigorous environmental and safety guidelines is putting even greater pressure on MARAD to award its ship scrapping contracts to domestic firms.
According to one press report, old vessels provide as much as 5 percent of the scrap metal consumed every week. With steel mills purchasing around $100 billion in ferrous scrap per year, the dollars add up.
On the downside, while decommissioned ships are becoming more sought-after, the upswing in the global economy is resulting in more steamship lines keeping their vessels in commission for a longer period of time. According to Lloyd’s List, a U.K.-based publication covering the maritime industry, roughly 232 vessels were scrapped during the first 10 months of last year, compared to 422 ships that were scrapped during the same time in 2004.
With India becoming a growing end market for ferrous and nonferrous scrap metal, the pressure on Bay Bridge to boost its business is likely to drive the company to land more material through contracts.
For Bay Bridge, better access to the mothballed Suisan Bay fleet near Richmond, Calif., has been the driving force behind the company’s quest to open a ship breaking yard on the West Coast.
FIGHTING AN UPHILL BATTLE. Despite Bay Bridge’s clean record, perceptions are hard to overcome. While the company has encountered significant challenges in its attempt to win over a skeptical population with the benefits of a ship scrapping operation, for Bay Bridge, having easier access to a West Coast fleet of ships makes it worth the effort.
Presently, no ship dismantling firms are located on the West Coast, and Dunavant feels this represents an excellent opportunity for Bay Bridge. He estimates that during the next five years, around 62 vessels from the Suisan Bay fleet will need to be scrapped. This should give the company a minimum of 10 years of business on the existing vessels.
At the present time, the vessels are being sent to yards in Brownsville. However, locating a facility on the West Coast would sharply reduce many of the expenses associated with ship scrapping, including towing.
While Bay Bridge feels it can adequately bid on many of the decommissioned MARAD vessels, the company also expects to expand its operations on the East Coast in the near future to allow it to handle more vessels from East Coast operations. While there are plenty of MARAD vessels that are in need of scrapping, there also are a number of privately owned vessels, including tug boats, barges and other ocean-going vessels, that have outlived their usefulness and are in need of scrapping.
As pressure grows to curtail the business of sending mothballed vessels overseas to developing countries to be scrapped, the upside for domestic ship scrappers grows.
After negative publicity about the domestic ship scrapping business in the 1990s nearly destroyed the business, the demand for companies that are equipped to handle large vessels coupled with strong demand for ferrous scrap has resulted in a good outlook for this industry.
As to the public perceptions of the ship dismantling industry, Dunavant notes, "This is a dangerous job. But if trained properly and taken seriously it will be no problem."
The author is senior and Internet editor of Recycling Today and can be reached at dsandoval@gie.net.
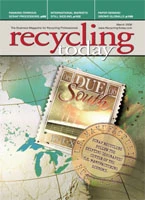
Explore the March 2006 Issue
Check out more from this issue and find your next story to read.
Latest from Recycling Today
- US ferrous market exhibits upward pricing pressure: Davis Index
- Glass Packaging Institute applauds regulation change
- Engcon adds to Tiltorotator line
- Paper recycling is focus of two January webinars
- Disruption likely for material flows in mid-January
- Blue Whale Materials to expand Oklahoma lithium-ion battery recycling plant
- CARI names new president and CEO
- Interzero revamps leadership structure