
A company that has revolutionized information technology has set its sights on influencing an entirely different field—recycling.
IBM Corp., Armonk, New York, is seeking partner organizations to pilot a new technology that uses a catalytic chemical process to turn end-of-life polyethylene terephthalate (PET) into a renewable resource. Called VolCat, short for “volatile catalyst,” the technology enables the recovery of the monomer bis(2-hydroxyethyl) terephthalate (BHET), which can then be used in the production of like-new PET. VolCat, IBM says, is cost-efficient, produces no waste and uses little heat. And, unlike mechanical recycling, it provides a way to derive new value from dirty and colored plastics that might otherwise be earmarked for landfills.
Polymer science is essential to advanced computing, and IBM researchers have contributed in both fields, says senior researcher Greg Breyta, who works at IBM Research-Almaden, the company’s San Jose, California-based innovation lab. “Part of this research has focused on the development of new catalysts for making these polymers. Scientists at IBM applied this expertise to the reverse problem: depolymerizing polymers such as PET, leading to the VolCat process.”
To start the process, PET bottles, containers and polyester fabrics are ground up. The ground PET then travels to a reactor, where it mixes with ethylene glycol and a chemical catalyst. With the catalyst, the reactor can depolymerize the PET in the presence of slightly elevated pressures and temperatures of about 392 degrees Fahrenheit—a lower temperature than is generally used to produce BHET. The catalyst digests and cleans the ground plastic, and contaminants are separated. The mixture is filtered, purified and cooled, resulting in a white powder—the BHET monomer. Also recovered in the process is a liquid that, along with the catalyst, is returned to the reactor.
“The catalyst is completely recovered, and there is no waste from the process, except for the impurities that are introduced by the grade of input,” Breyta says. “After [the] process unzips the PET polymer chain into monomer, and the volatile catalyst is recovered, we are able to perform subsequent cleanup steps to make the high-quality BHET monomer, which is then introduced into existing PET polymerization processes.”
IBM says the monomer can be fed directly into a polyester reactor to make new resin.
Breyta says IBM still is studying the properties of PET made from BHET recovered in the process but believes it will compete well with materials made directly from virgin monomer. While mechanical recycling can discolor or damage material properties of recycled plastics, he says that’s not likely to be the case with the VolCat approach to chemical recycling.
Breyta says used PET won’t have to be sorted or cleaned—the VolCat process works with all of it, depolymerizing the PET while separating out other materials. And, because the PET made from VolCat-recovered BHET retains its mechanical properties, chemically recycled materials can be used more extensively than materials produced by mechanical recycling. While recycled PET might make up just 10 percent of the material in a new PET product, VolCat-produced BHET could be used in greater ratios.
VolCat can depolymerize the PET with little or no effect from a wide range of impurities in the input stream. To IBM, that means there’s hope in totally transforming how plastic gets made and used. “In five years,” IBM says, “recyclers could cut out the fossil fuels and simply attach a VolCat system to the assembly line and make new plastic directly from the old.”
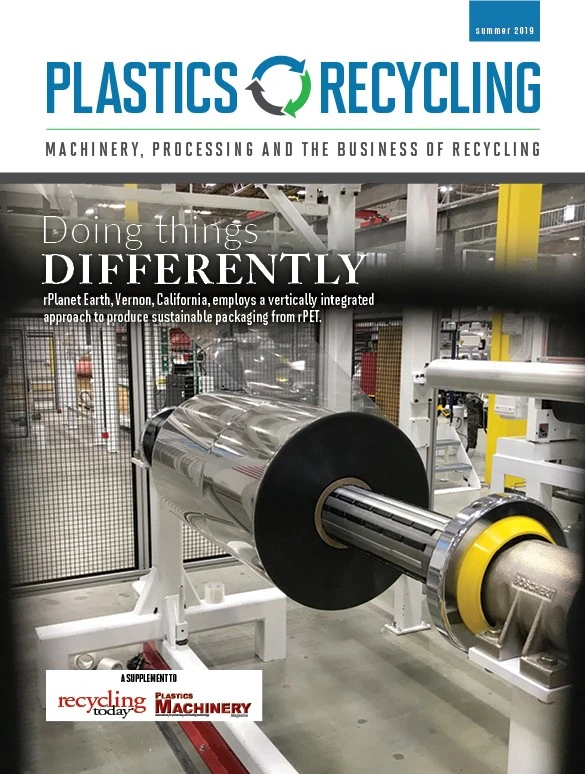
Explore the June 2019 Plastics Recycling Issue
Check out more from this issue and find your next story to read.
Latest from Recycling Today
- Fenix Parts acquires Assured Auto Parts
- PTR appoints new VP of independent hauler sales
- Updated: Grede to close Alabama foundry
- Leadpoint VP of recycling retires
- Study looks at potential impact of chemical recycling on global plastic pollution
- Foreign Pollution Fee Act addresses unfair trade practices of nonmarket economies
- GFL opens new MRF in Edmonton, Alberta
- MTM Critical Metals secures supply agreement with Dynamic Lifecycle Innovations