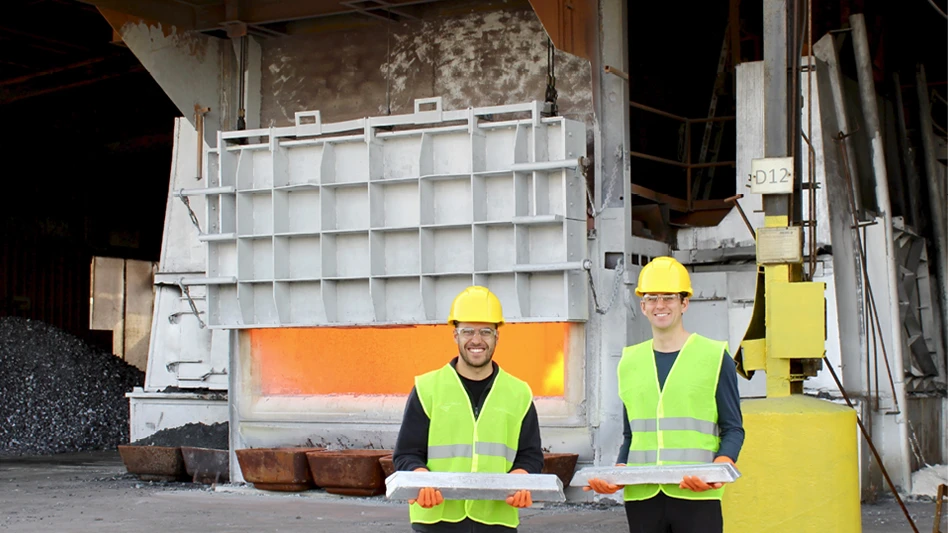

The energy and carbon impact of aluminum production in North America is at its lowest point in history, according to a life cycle assessment (LCA) report published in January 2022 by the Aluminum Association, Arlington, Virginia. Since 1991, the carbon footprint of the region’s primary aluminum production has declined 49 percent, while recycled aluminum production’s carbon footprint has declined 60 percent. Over that time, the energy needed to produce primary and secondary aluminum has dropped by 27 percent and 49 percent, respectively.
Despite these green credentials, secondary aluminum production produces dross as a byproduct. While dross is recyclable, the process results in salts and oxides that often are landfilled in the U.S. However, new technology introduced by California-based startup Hydrova holds the potential to further enhance the sustainability of aluminum recycling.
Hydrova’s patent pending separation technology, called DrossZero, recovers aluminum, salt and oxide products from dross and salt cake while generating hydrogen for clean energy use on-site. The company says its process can divert 100 percent of the 5 million tons per year of waste from secondary aluminum production that otherwise are destined for landfill while also decarbonizing aluminum and cement production.
Earlier this year, Hydrova announced a partnership with secondary aluminum producer TST Inc. to produce aluminum ingots using salt and aluminum recovered from dross, generating hydrogen during the recovery process. The achievement was welcomed by TST, which produces 3,000 metric tons of secondary aluminum ingot for the automotive industry per month through its TIMCO division and 3,000 metric tons of forging billet for the aerospace and semiconductor industries per month through its TANDEM division.
“Being in Southern California, we have to take a lead in technology that can improve the environment,” TST President and CEO Andrew G. Stein says. “We are always looking for new ideas,” particularly as the state tightens its environmental regulations, he adds.
Regarding its dross, Stein says, “In years past, we recycled on-site with rotary dross furnaces and disposed of the salt cake,” which is a byproduct of the dross recycling process. “Currently, we toll process with an Arizona facility.”
However, even the processor TST uses to recycle its dross is disposing of the salt cake, and Stein says that does not reflect the green future of secondary aluminum production.
“The secondary aluminum industry is a green industry at its heart. We use recycled aluminum to make better-than-primary aluminum with only 5 percent of the energy usage. Any technology that eliminates this waste is good for the industry, our company and the community.”
“First, we remove as much aluminum as we can, as all dross processors do—the most important thing to the aluminum recyclers is getting as much aluminum metal back as possible.” – Rostam Reifschneider, Hydrova chief technology officer
Going greener
Hydrova co-founder and CEO Julian Davis says he and Rostam Reifschneider, co-founder and chief technology officer, began working on the technology for DrossZero about three years ago as students.
Reifschneider says he and Davis have been friends since they attended high school together in San Diego. They both headed to the East Coast for college, with Davis attending Georgetown University in Washington and Reifschneider attending Massachusetts Institute of Technology (MIT) in Cambridge. Davis and Reifschneider reconnected in California in 2020 when they were sent home from university at the start of the COVID-19 pandemic.
“During COVID, we got a grant from MIT that sort of kicked off this whole thing,” Reifschneider says of Hydrova. “We were looking at hydrogen generation through the aluminum-water reaction, thinking about decarbonization of some of the hardest industries that are using a lot of natural gas.”
He adds that as they were studying the production of hydrogen using the aluminum-water reaction, they learned of the “massive waste challenge in the aluminum industry, specifically in the form of dross and salts cake, that yet has to be solved today, especially in the United States.”
Reifschneider says Hydrova’s technology is a “full end-to-end zero-waste dross recycling process, that also, of course, incorporates hydrogen production through the aluminum-water reaction, sort of recouping any aluminum that would have otherwise gone to waste that’s not recyclable and turning that into hydrogen instead, so we can further try to decarbonize the industry.”
He adds that Hydrova is lucky to be working with a company like TST. “We’re piloting our technology with them, sort of proving everything out, and are now scaling it up.”
Davis says, “By separating out the aluminum and salt from dross, Hydrova is able to put these materials straight back into the furnaces from which they came, creating a closed loop. And by producing hydrogen, we can provide a clean fuel to help decarbonize those same furnaces.”
Technically speaking

Reifschneider says Hydrova’s DrossZero technology centers around the aluminum-water reaction for hydrogen generation.
Aluminum can react with water at room temperature to form aluminum hydroxide and hydrogen. However, the reaction doesn’t normally happen because aluminum oxide naturally coats the raw metal, preventing it from coming directly into contact with water.
“There’s a chemical reaction component where we sort of encourage this reaction to happen and then turn any aluminum that’s left after aluminum recovery into hydrogen,” he explains. “And then after that, it’s primarily a separation process.
“We have sort of our secret-sauce, proprietary reaction promoter, we call it, that helps encourage the reaction to happen,” Reifschneider continues. “Aluminum really likes oxygen, so it’ll remove the oxygen from water and release the hydrogen. But, also, because it really likes oxygen, it’ll take the oxygen from the air, and it’ll form an aluminum oxide layer—it’s a microscopic sort of thin film on the outer surface of aluminum, so that’s why aluminum foil doesn’t just spontaneously react with water upon contact. But if you are to mitigate that aluminum oxide layer to bring water into actual contact with elemental aluminum, then the reaction just spontaneously proceeds from there and starts to produce hydrogen.”
With Hydrova’s technology, “First, we remove as much aluminum as we can, as all dross processors do—the most important thing to the aluminum recyclers is getting as much aluminum metal back as possible,” he says. “There’s still a little bit of aluminum left that’s sort of impossible to recover, so that’s what we use to make hydrogen.”
The process separates the high-quality salt flux that can be reused in the aluminum furnaces, eliminating the need to buy new salts. “That’s becoming increasingly important as the prices of salts, especially potassium chloride, are going up,” Reifschneider says.
The hydrogen piece

The pilot scale at which Hydrova’s DrossZero technology is operating means relatively small amounts of hydrogen are being produced and not yet being used to fuel TST’s operations, Davis says.
In the meantime, he adds, Hydrova is “bottling up” the hydrogen and using it in its demonstration lab to generate heat and operate fuel cells.
“What’s really exciting about it is hydrogen is such a versatile energy carrier that can be used to blend into natural gas furnaces,” Davis says. “It can be used as a pure fuel source itself, it can go into fuel cells, which convert that hydrogen into electricity and create electrical power for different machines.”
He says governments are introducing incentives to encourage the use of cleaner fuels such as hydrogen. California’s Cap-and-Trade Program, for instance, is part of the state’s strategy to reduce greenhouse gas (GHG) emissions. It establishes a declining limit on major sources of GHG emissions throughout California and creates an economic incentive to invest in cleaner, more efficient technologies.
In TST’s case, replacing some of the natural gas it uses with hydrogen could help the company stay within its carbon emissions limits to avoid paying a carbon tax, Davis says.
Stein says he doesn’t believe incorporating the hydrogen into TST’s production process would pose problems for the company but instead would enhance its melting operations if blended with the natural gas it currently uses.
Making industry connections

When Davis and Reifschneider first were in the process of researching the aluminum industry, Stein says all the business partners were referred to him and TST.
“TST has a long-standing tradition of being involved in the implementation of cutting-edge technology to improve the environment,” Stein says. “We started with the [Gas Research Institute], developing a ceramic heat recuperator to reduce the energy consumption of aluminum furnaces. We worked with the California Metals Coalition to host two fuel cells and four microturbines to generate electricity. We have been the host of numerous demonstration projects for new oxyfuel burners as well as traditional gas-air burners.”
Davis says TST was a natural partner for Hydrova as the largest aluminum manufacturer and recycler in California.
“They talked about just how massive of a problem dross is, and we sort of realized we might be onto something here," he adds.
Once Hydrova and TST embarked upon a more extensive pilot, Hydrova relocated its operations from San Diego to Orange County, California, which is roughly an hour away from TST’s Fontana, California, facility.
Davis says Hydrova is processing roughly 5,000 pounds of dross at a time from TST. “This is actually a representative pilot operation where we have each [piece of] equipment running in parallel,” he adds.
Stein mentions that the equipment Hydrova uses largely is readily available, which should facilitate the technology’s full-scale deployment.
Aluminum is not the only industry poised to benefit from Hydrova’s technology. The process also produces a high-quality, salt-free aluminum oxide material that can be sold into the cement industry.
Hydrova says it has formed a partnership with the inventors of Rapid Set cement, CTS Cement, Garden Grove, California, to supply salt-free aluminum oxide, which is a major ingredient in Rapid Set cement.
As far as deploying Hydrova’s technology more widely in the aluminum industry, Reifschneider says, “What we want to do is develop an end-to-end zero-waste turnkey dross recycling system and then work with the right aluminum industry partners to implement that throughout the industry as quickly as possible. So, we’ll essentially be designing, engineering, installing [and] contracting these systems for larger aluminum companies that would own them and operate them on their sites with their own people.”
Davis adds that Hydrova also is in talks with some of the largest aluminum recyclers in the world about how the technology can help them meet sustainability goals such as decarbonization and waste reduction.
Hydrova’s technology drew interest from the U.S. Environmental Protection Agency, which awarded the company a $100,000 grant in December of last year. Along with grants from MIT and the 776 Foundation, Hydrova’s co-founders say they have attracted venture capital investments from firms such as the 1517 Fund and Climate Capital.
“Our goal is to prevent millions of tons of aluminum recycling waste from going to landfill every year,” Davis says. “To accomplish this, the economic incentive must be clear, and that is why our focus is on turning this waste into high-quality, low-carbon products like TST’s alloys, hydrogen and Rapid Set cement. This unlocks a new opportunity for sustainability to be achieved profitably,” he adds.
Stein says, “My goal is that this technology becomes successful at meeting its goal of zero waste and that it becomes the defacto standard for the processing of dross from all secondary aluminum companies.”
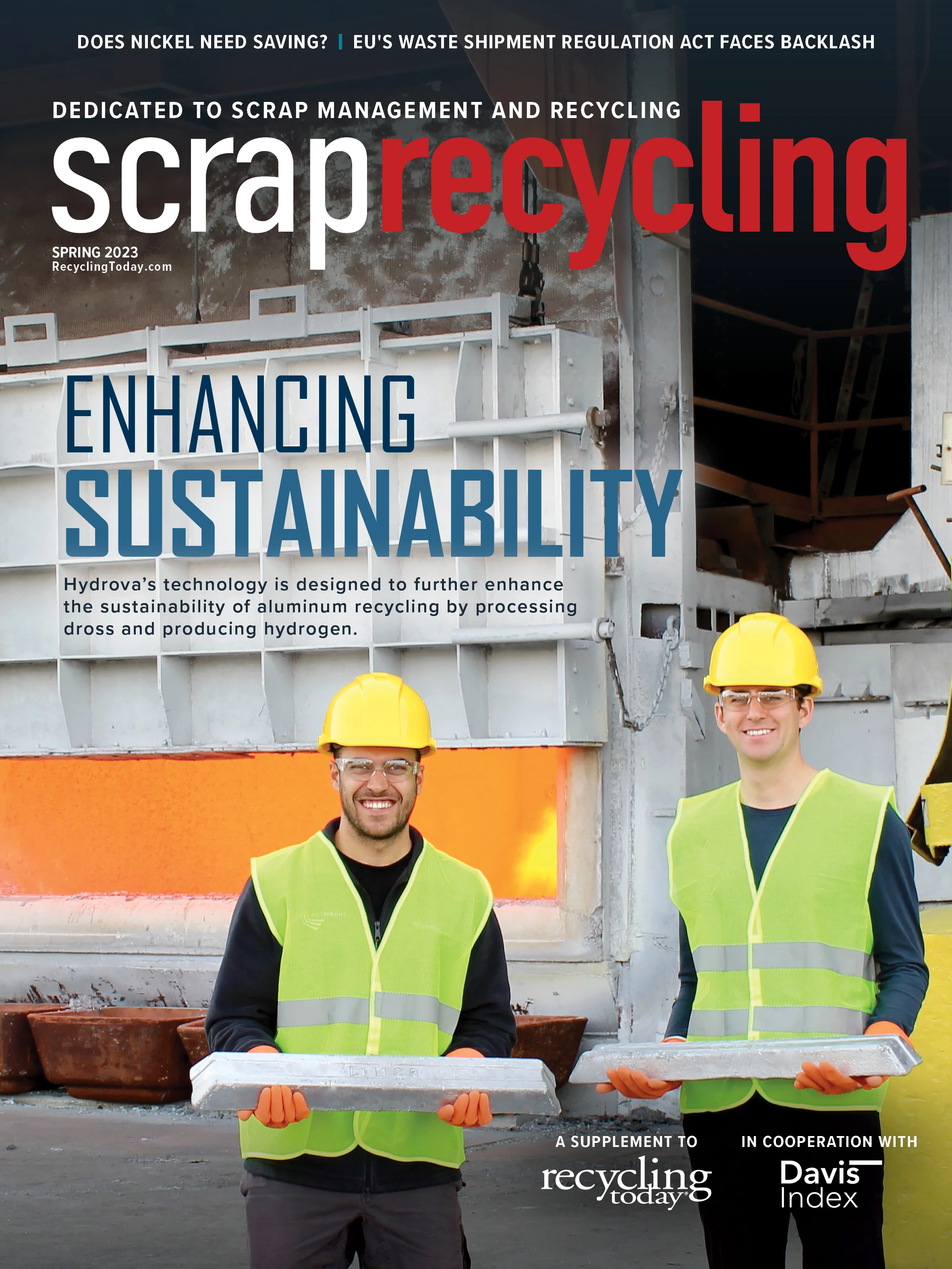
Explore the Spring 2023 Scrap Recycling Issue
Check out more from this issue and find your next story to read.
Latest from Recycling Today
- Aqua Metals secures $1.5M loan, reports operational strides
- AF&PA urges veto of NY bill
- Aluminum Association includes recycling among 2025 policy priorities
- AISI applauds waterways spending bill
- Lux Research questions hydrogen’s transportation role
- Sonoco selling thermoformed, flexible packaging business to Toppan for $1.8B
- ReMA offers Superfund informational reports
- Hyster-Yale commits to US production