
In comments that accompanied its 2021 third-quarter earnings report, Hilde Merete Aasheim, president and CEO of Oslo, Norway-based aluminum company Norsk Hydro ASA, said the white metal has a strong role to play in reducing global carbon emissions and supporting the green energy shift. “We see increased demand for aluminum used in customers’ solutions to curb emissions. Demand for our low-carbon aluminum offerings continues to increase, while we also are taking strong measures to reduce our own emissions.”
One of the ways Hydro is reducing its emissions is by doubling its use of postconsumer scrap by 2025. The company’s Extrusion North America division is upgrading recycling capabilities at its site in The Dalles, Oregon, allowing it to process an additional 10,000 metric tons, or 11,023 short tons, of postconsumer scrap annually and to increase overall recycled aluminum output by 27,000 metric tons, or nearly 30,000 short tons. This upgrade also will reduce energy consumption and result in lower CO2 emissions and metal costs at the site, according to the company.
Hydro’s Aluminum Metals division also will construct a recycling plant in Cassopolis, Michigan, that will produce an estimated 120,000 metric tons, or more than 132,000 short tons, of aluminum extrusion ingot per year. The aluminum produced will be used in automotive and other transportation applications and for building products, according to Hydro.
The expected investment in Michigan is estimated at $140 million, depending on final facility design, market conditions and economic development, according to the company, which plans to use direct rail service to bring supplies to the plant, lowering the overall carbon footprint of its operations.

Rooted in sustainability
Charlie Straface, president of Hydro’s Extrusion North America business unit, says the company is rooted in sustainability and green energy as a Norwegian firm that has long used hydroelectric power. He adds that under Aasheim’s leadership, Hydro began a new strategic agenda in 2019 to position the company as an industry leader based on innovation and sustainability: “Lifting profitability, driving sustainability.”
“Certainly, we’re a for-profit company and a public company, and we need to earn money for our shareholders,” Straface says. “But equally important is [that] we need to be a leader in the transition to this low-carbon circular economy. And, and at our core is aluminum, which is a really important metal in that journey.”
He adds that aluminum has been a key material for lightweighting vehicles, improving their fuel efficiency and reducing their carbon footprints as a result. In the electric vehicle (EV) market, aluminum extrusions are commonly used in battery boxes and crash protection systems. The metal also is recyclable and often made with recycled content, furthering its appeal.
Hydro’s North American Extrusion business, which has the region’s leading market share in the segment, operates 22 facilities that are supported by nine cast houses that produce aluminum billet with recycled content, Straface says.
“We believe in highly recycled products,” he continues. “Our goal is to keep driving up the recycled content of our aluminum billet.”
Hydro’s recycled content has increased from roughly 60 percent to approximately 70 percent to 75 percent.
“Our goal is both to increase our total recycled content to 80, 90 percent and then within that to continue to increase our use of postconsumer scrap,” he adds.
Hydro also plans to source the primary aluminum it uses from facilities that use hydroelectric power.
The company’s North American operations are looking to use more green energy, as well. In Cressona, Pennsylvania, home of Hydro’s largest extrusion plant, the company has signed a long-term deal to convert all the electricity used on-site to solar, he says.

Specialized focus
Using more postconsumer scrap to produce its extruded aluminum products doesn’t come without challenges, however. Straface says that compared with postindustrial scrap, postconsumer scrap “is harder to use and does require some new innovations and some more advanced technology than has existed in the past.”
Hydro has a group of employees within its Aluminum Metals division that specializes in increasing the company’s use of postconsumer scrap. “They’ve been doing all of the developmental work in Europe,” he says.
The company has three or four different kinds of technology that it’s been working with to further its ability to not only to segregate contaminants but also to sort alloys by type. Straface says, “We’ve been doing a lot of research and development and have a production-size facility in Germany.”
That facility will inform the design of Hydro’s new Michigan location. That cast house will be run by the company’s Aluminum Metals division, which also has facilities in Commerce, Texas, and Henderson, Kentucky, he says, that have a total of 400 million to 500 million pounds of annual capacity. However, Straface says, the technology and processes Hydro’s Aluminum Metals division develops eventually will be applied at the nine cast houses that supply its North American Extrusions business. Those facilities have roughly 1.6 billion pounds of capacity.
In the meantime, he says his division’s cast houses are working with scrap suppliers that have shredding capabilities and putting in bunker systems to handle different kinds of scrap.
The Dalles site is being equipped with what Straface says is a “state-of-the-art baghouse and fume collection system that will allow us to use more postconsumer scrap. But the big breakthrough is going to come from this technology that we’re running in Europe today.”
In 2020, the Oregon Department of Environmental Quality (DEQ) issued the Dalles facility a $1.3 million penalty for multiple air quality permit violations. Those violations arose in part because the facility processed unclean, coated aluminum scrap for more than a year, according to a news release from the Oregon DEQ about the penalty. The facility’s permit prohibits the melting of this material. Hydro says it has amicably resolved the matter with the DEQ.

Seeking more scrap
While the extrusion billet produced at Hydro’s nine North American remelt facilities contains 69 percent scrap on average—roughly 20 percent of which is postconsumer—scrap content varies by site and alloys produced. “I have one facility that uses 92 percent recycled content,” Straface says, while others may use 65 percent scrap. “Again, that has to do with the alloys that they need to produce. And maybe the geography of what scrap’s available. So, the cast houses are all a little different depending on fundamentally the alloys they have to produce to the markets they have to serve.”
He adds that one of Hydro’s strengths as an extrusion company is working with its customers. “The advantage of having our own cast houses is that as we develop the properties that they need for their products to work, sometimes we tweak the alloy … and we have our own cast houses where we can cast it.”
The company also believes it needs to be transparent about its scrap use, Straface says, to avoid greenwashing claims. “I think we have a really good set of processes now that truly identifies the scrap that we do receive, and we’re very confident about what we report.”
Until Hydro is ready to roll out the technology and processes it’s developing in Germany to use more postconsumer scrap, its cast houses operated under its North American Extrusion business will continue to consume aluminum wheels, electrical conductor wire and window and door frames, he says.
Regarding its goal of consuming 50 percent postconsumer scrap, Straface says, “It is Hydro’s belief that this is a great opportunity to both create a circular economy and be profitable.”
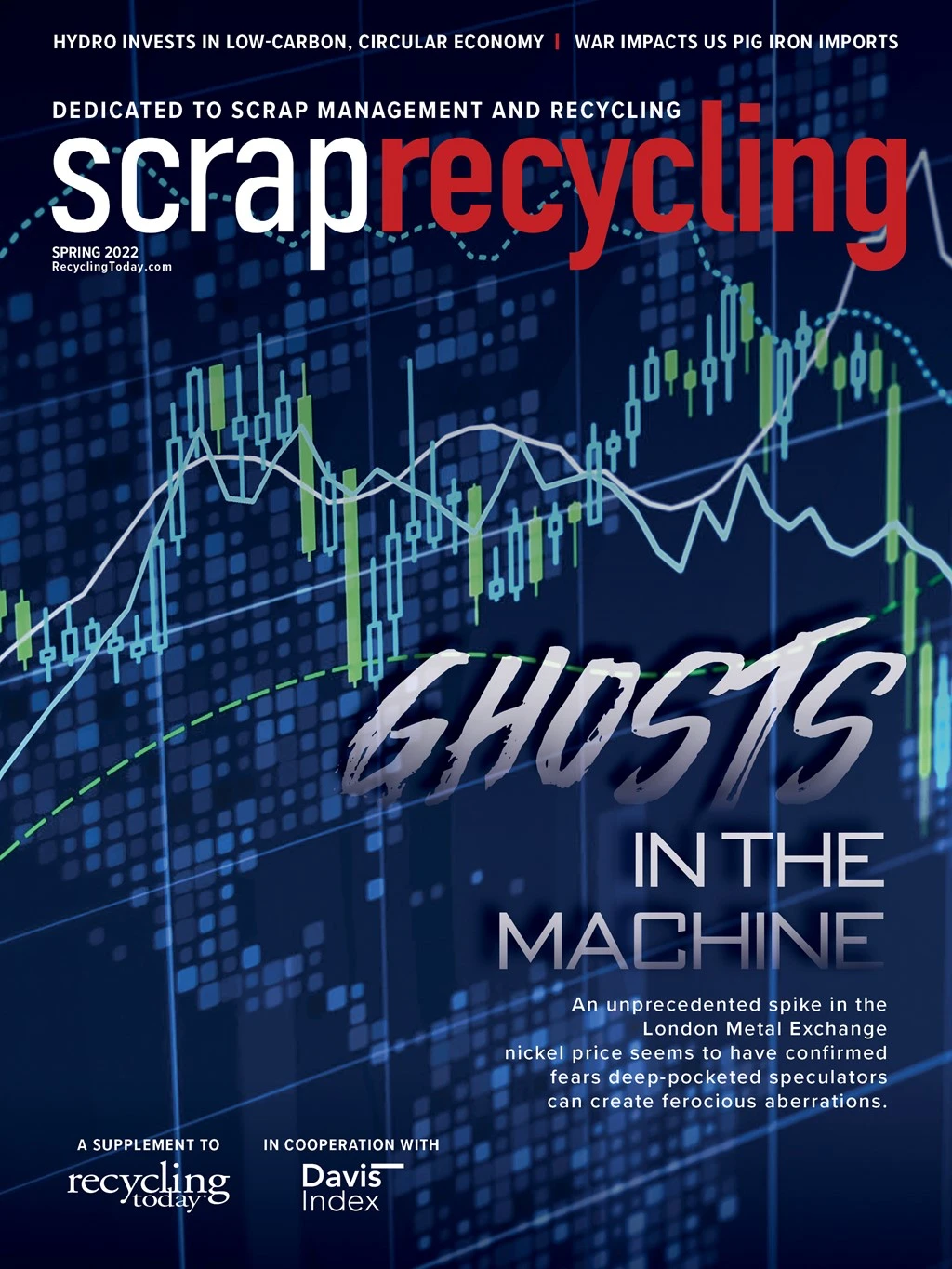
Explore the Spring 2022 Scrap Recycling Issue
Check out more from this issue and find your next story to read.
Latest from Recycling Today
- Lautenbach Recycling names business development manager
- Sebright Products partners with German waste management equipment company
- WasteExpo transitions to biennial format for enhanced experiences
- Study highlights progress, challenges in meeting PCR goals for packaging
- Washington legislature passes EPR bill
- PureCycle makes progress on use of PureFive resin in film trials
- New copper alloy achieves unprecedented high-temperature performance
- Gränges boosts profits and sales volume in Q1 2025