The good news might be bad news—or it might really be good news—as dismantlers and recyclers see more hybrid and electric cars come into their yards.
One scenario has electric car recycling following the same general path that the computer dismantling business took in the late 20th century. At first, there will be a sizable number of high-value, profitable parts to recover.
However, as the industry gets its arms around the engineering challenges it faces with the alternative-fuel vehicle market—lightweighting, cheaper and more exotic materials, a reduced number of components—the easy profits from dismantling such vehicles might become harder to find.
DOWN THE ROAD
Whatever scenario plays out, it will not happen right away. It is unlikely there will be more than a trickle of electric or hybrid vehicles coming through auto yards any time soon. However, major component manufacturers are looking at third-generation products. Automotive OEMs are likely to put lightweighting in the driver’s seat, which will cause the components used in alternative-fuel cars to continue to evolve.
“We’d like to see another 15 percent of weight come out of the systems in the third generation,” says Glenn Denomme, vice president of hybrid engineering in Lear Corp.’s Electrical Power Management Systems group, Southfield, Mich. Currently, a typical battery-powered vehicle has 45 to 65 pounds of electronic components, excluding the batteries.
He says he sees advances in materials, semiconductors and cooling systems contributing to lightweighting. “Weight and cost reductions are my focuses,” Denomme says.
On top of that, several functions can be integrated into one power module. Today’s electronic cars typically plug into a wall plug. An AC-to-DC converter handles the exchange from wall to car. In the car, a second converter has to change power back from DC to AC for such components as the lights and radio. “We asked ourselves, Can we multiplex that?” Denomme says. A “yes” answer means engineers can eliminate one point of failure so the car will be more reliable, weigh less and have a smaller component footprint. That translates either to better range on the vehicle or to better efficiency for the same range.
Because most plug-in cars today are limited to a range of about 40 miles, a 10 or 15 percent jump from an improvement in one part of the package is significant.
THE OEM VIEW
Car makers love ideas like that, too. Take out some components and it leaves more space in the vehicle for passengers, cargo or other components.
Just as with computers, electric cars generate a lot of heat. Anything that adds efficiency will cut that heat output and make the vehicle simpler to design.
The people at the $2.3 billion Lear Corp. say they have given a lot of thought to the whole situation. The company is among the larger global providers of systems and components for electronic cars. It works with eight global providers, including General Motors Co. on the charging systems for the 2010 Chevrolet Volt. The company also works on the Renault Kangoo and the Daimler EV Smart.
Lear says it expects its sales of components and systems for hybrids and electric vehicles to grow by about 3.3 percent annually. That would put it at approximately 7 percent of its global electrical distribution and power management systems business by 2012.
To meet this demand, Lear has opened a new high-power systems lab at its Global Center of Excellence for Research and Development in Southfield. It joins Lear’s European hub in Valls, Spain.
NEW MATERIALS
Another area in which Denomme and his colleagues are working to achieve efficiencies involves the connectors and wiring. These eventually will be components recyclers will have to be prepared to handle.
“We are looking at alternative materials like carbon-fiber wire,” Denomme says. While dismantlers today are familiar with carbon-fiber construction in the body panels of some vehicles, this would be focused on lightweighting that 65 pounds of wiring in the car.
“If you take a carbon-fiber and clad it with copper or aluminum you cut weight,” he says.
Aluminum is not immune from weight reduction, either. “We can get rid of the aluminum in the boxes (that contain electronics),” Denomme says. Conductive plastics are lighter than aluminum and have the advantage of being molded into any shape engineers desire.
In addition, the plastics can have nano-particles of iron built into them to provide shielding for the electronics.
If the predictions of market growth by Lear Director of Global Hybrid Engineering Aftab Kahn pan out (and he terms them very conservative), there will be 3.6 percent growth in electric cars. That is equal to about 3 million vehicles.
Some market analysts are more bullish and say the market could grow by 15 percent in the next five years. That would put 12 million to 15 million electric vehicles on the road in the United States.
OEMs and component manufacturers are designing with end-of-life in mind, they say, which is good news for dismantlers and, perhaps, shredder operators.
Electronic cars are designed for 10-year service lives, longer than the typical gasoline-powered vehicle of years past. A single component—the wall-to-battery charging plug—is designed for 10,000 uses. Figuring two charges per day, that works out to a 14-year minimum life.
While much of the emphasis in the popular press focuses on cars like the Volt, for practical reasons it may be more likely to look at captive fleets for the first major market thrust. While Toyota has placed more than 2.3 million hybrid electric vehicles into service since 2000, major fleet buyers, like FedEx, are going totally electric on a test basis. FedEx, based in Memphis, Tenn., says it soon will have all-electric delivery trucks on the streets of Los Angeles. Two of the new all-electric trucks come from Navistar. These are based on a design by Modec (a subsidiary of Japan’s Mitsui with an assembly plant in the United Kingdom) already operated by FedEx, which has 10 vehicles working in London and five on order for Paris.
WORKING ON NEW CARS
The generic version of the electric car has three basic systems: the charging system, an energy-management system and a high-voltage system.
While it varies, the amperage for these cars ranges from 130 to 400. In a typical vehicle, 6.3-millimeter connectors carry 130-amp power to the car’s compressors to drive energy. Just as on today’s cars, the connections have to be small enough to fit through the dashboard panel through-hole (thus the 6.3-millimeter size). There also are 14.5-millimeter blades that carry 250-amp DC power.
The number of different standards to be met is considerable. Information that recyclers may wish to keep tabs on are the standards being developed for these vehicles. It is not a total desert. Several standards have been approved and are in use. One is the J1772 standard plug and receptacle on the vehicle.
Recyclers should be aware of the safety devices designed for those working on electric cars. One thing no dismantler wants to do is get his morning jolt from a 400-volt power train or to cut into a vehicle with “hot” power.
To prevent that from happening, electric cars are designed with safety devices. These will function for emergency first-responders, dealers or garages servicing the cars or for dismantlers.
A high voltage interlock loop will take the power from 400 volts to 60 volts in about five seconds to make the system safe to work with.
Dismantlers and shredder yards may have several years before this knowledge becomes critical for daily operations.
Published reports indicate that Detroit’s eye is on 2015 as the break-out year. In the meantime, there will be dribs and drabs of electric vehicles coming into recycling operations. However, until the world’s automakers start to produce in volume, the electric vehicle will be a curiosity in most dismantling shops and shredder yards.
Once electric cars do achieve volume, the number of pounds of material that can be recovered predictably will continue to fall. Just as with the personal computer business, what is good for the manufacturer and good for the user might not be good for the recycler as the weight of recoverable components per vehicle will drop as OEMs and component producers get better at what they do. However, as the number of electric vehicles rises into the millions, the overall weight of components available for recovery will be much greater.
The author is a contributing editor to Recycling Today and can be contacted at curt@curtharler.com.
Get curated news on YOUR industry.
Enter your email to receive our newsletters.
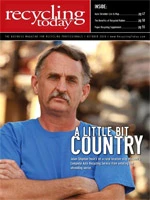
Explore the October 2010 Issue
Check out more from this issue and find your next story to read.
Latest from Recycling Today
- Toppoint Holdings expands chassis fleet
- Lego creates miniature tire recycling market
- Lux Research webinar examines chemical recycling timetables
- Plastics producer tracks pulse of wire recycling market
- Republic Services, Blue Polymers open Indianapolis recycling complex
- Altilium produces EV battery cells using recycled materials
- Brightmark enters subsidiaries of Indiana recycling facility into Chapter 11
- Freepoint Eco-Systems receives $50M loan for plastics recycling facility