Some companies thrive on challenges. Huron Valley Steel Corp., Belleville, Mich., one of the world’s largest processors of nonferrous scrap, is certainly one of them. Walking through the company’s high-tech facility for sorting the nonferrous components of automobile shredder residue (ASR) is like a visit to the future of recycling. But there is more innovative technology currently under development that one company executive says will “make what we are doing today look simplistic.”
Plenty of automobile shredding operations use eddy current separators or even flotation systems to recover aluminum and zinc alloys from ASR, but Huron Valley has taken the process much further and has developed technology to process aluminum, copper, brass, stainless steel and zinc from ASR into separate streams. To accomplish this, the company uses a combination of proprietary sorting techniques, including light and heavy media separation, eddy current separators and light imaging systems.
“We believe in collecting what someone else is throwing away,” says Leonard Fritz, president and chairman of Huron Valley. “Our strategy is to look at what we throw away, and chase the last squeak – to go for zero waste.”
The company – which is not subsidized by anybody, Fritz emphasizes – has been built from the ground up with just the hard work and determination of its many long-time employees, some of whom have been with the company for 40 years.
FERROUS BACKGROUND
Fritz is a natural entrepreneur who started in the business at age nine when he began to salvage paper, rags and bottles from landfills in the Detroit area in order to make money to buy clothes for school. A few years later, he made recovering iron and steel scrap from landfills and steel mill dumps a full-time job. “I went into business for myself when I was 15 years old in 1937,” he says.
After serving in World War II, he founded Fritz Bros. Inc. with his two brothers to recover iron from mill and foundry castoffs, and during this time got into the foundry business. In 1958, the company’s name was changed to Fritz Steel Products, and they expanded into pig iron production, but the company ran into problems.
Soon after, Fritz went into business for himself again making pig iron out of foundry discards, steel cans from incinerators and No. 2 bundles. Ron Dalton and Richard Wolanski, senior vice presidents, joined him in the late 1950s, and they formed Huron Valley Steel Corp. in 1961. In 1963, the company installed a small shredder to prepare scrap for pig iron production, modifying it for this use. From there, the Huron Valley worked with Hammermills to develop an automobile shredder, and then began shredding cars.
Around 1967, company officials decided to tackle the problem of recovering all the aluminum, stainless steel, zinc, brass and copper which automobile shredders were landfilling. Dalton had the idea to try separating the material using heavy media separation, which had never been used for metals. This showed so much potential that the company decided to devote itself to nonferrous scrap recovery.
Huron Valley began doing its own zinc refining in 1970, and its own aluminum smelting in 1978. And in 1986, the company advanced from merely separating nonferrous from non-metallics and aluminum from the heavier metals, and developed the current combination of density separation followed by eddy current separators and imaging technology.
All the company’s technological developments have been cumulative, company officials stress. “One thing led to another,” says Fritz. “It didn’t happen overnight; it was very difficult. We had many failures – they say that success has many faces, but failure only one. But having good people is key to our success.”
ASR RECOVERY
Today, Huron Valley employs almost 500 people in its operations in River Rouge, Mich.; Trenton, Mich.; Belleville, Mich.; Detroit, Mich.; Riverdale, Ill.; Anniston, Ala.; Tucson, Ariz.; and Overpelt, Belgium. All together, the company processes a billion pounds of materials a year.
The Riverdale., Ill., facility uses a flotation process to remove aluminum from ASR and then sends the rest to Belleville to be processed. The Detroit plant is a specialty facility that processes the metals from incinerator ash. The Tucson, Ariz., plant salvages old B-52s and other military equipment, and the Belgian plant has the same capabilities and capacity of the Belleville plant.
According to company officials, Huron Valley’s 35-acre Belleville plant has the capacity to handle the output of all the 200 auto shredders in North America. Because of freight costs, however, the company mainly buys ASR from about 160 of these shredders, most of which are located east of the Rocky Mountains. In total, Huron Valley handles 50 percent of the total ASR in the U.S., and 65 percent of the ASR generated east of the Rockies.
Currently, Huron Valley does little business in the western part of the U.S. But the company’s Tucson, Ariz., operation may eventually expand its scope to process materials from Los Angeles and other parts of the West Coast.
By weight, 50 percent of ASR is nonferrous metals, including aluminum, stainless steel, copper, brass, and zinc. Of that, 64 percent is aluminum. The more metal contained in the ASR the company receives, the better. To this end, Huron Valley encourages its suppliers – shredder operations – to run the material through eddy current separators before sending it to Huron Valley.
“If the shredder industry isn’t healthy, we aren’t,” says Richard Osterberg, vice president of operations. “We pay them based on recovery. We keep very detailed information on our vendors, and track them through recovery. We pay them fair market value for what they ship, based on a formula. It’s within a percentage point of what is contained in the material.”
There is a strong demand for the high quality metal scrap and ingot produced by Huron Valley. According to Dalton, 80 percent of the zinc generated by Huron Valley is sold to steel mills. Aluminum scrap is sold to smelters, and ingot is sold to die casters within a 250-mile radius. Copper and brasses are sold to smelters and brass ingot makers. Stainless is sold to stainless mills. The Riverdale, Ill., and Anniston, Ala., operations sell the aluminum they separate locally, and send the heavier metals back to Belleville for processing.
Before Huron Valley began refining zinc in-house, they were shipping it to Belgium to be refined. Refining the material makes it highly marketable, says Dalton.
“There is no real use for zinc dust now,” he says, “but anyone can use fine, primary quality zinc. In fact, a lot is still imported into the U.S. each year.”
Each year, Huron Valley sells about 160,000 tons a year of aluminum in the form of scrap and ingot, 30,000 tons of zinc, 12,000 tons of brass, 15,000 tons of stainless steel, and 5,000 tons of copper, for a grand total of roughly 225,000 tons of metal.
Thinking Big |
Although Huron Valley Steel’s focus is on nonferrous recovery, Leonard Fritz, president and chairman, remains involved in the ferrous business through a sister company, Fritz Enterprises, Taylor, Mich. This company, formed in 1973, does auto shredding and reclaiming, and is “the largest reclaimer of old dumps at steel mills in the world,” according to Fritz. Typical of the company’s practice of coming up with innovative solutions, Fritz Enterprises developed and built what Fritz says is the largest shredder/impactor in the world to process oversized steel slag at an 11-mile, 104-year-old old steel mill dump on the Lake Michigan shoreline in Gary, Ind. The machine breaks up giant 25- to 30-ton steel slag boulders into chunks that are sold to steel mills as raw material. The giant Hammermills shredder features a 148-inch circle, 1-ton hammers, and an 80-ton rotor. It is capable of generating 80 million foot pounds of force. “There is nothing like it in the world – we built it for our own operations,” says Fritz. “We figured if we could shred a can, a pail, and a car, we could shred these giant chunks. In fact, we could shred battleships with this machine.” |
A WALK THROUGH THE PLANT
How is all this metal separated? When ASR is brought to Huron Valley’s Belleville plant in one of the 40 to 50 trucks that arrive daily, it is weighed and deposited in piles in the receiving area. These are kept distinct, so the company can monitor the quality of material brought by each supplier. The material clearly differs, depending on the source – some are full of chunks of rubber and foam, others contain slightly melted metals that have been through incinerators.
Material first goes through a two-stage separation. The first wash removes very light materials such as plastics, wood and dirt, which is a waste stream.
Then fine ground iron ore (magnetite) is added to make a slurry twice the density of water. This light media separation system separates metal from nonmetal; the metal sinks and the plastics, rubber, glass and very light metal like sheet stainless floats. This stream is sent over an eddy current separator so any metal is removed.
At this point, the metals are weighed at a weigh hopper to determine the amount of metal in the load now that the nonmetallics have been removed. Suppliers are paid based on this net weight.
Next, the metals go to the heavy media plant, where ferro silicon (fused iron and silica) is used to create a heavy slurry three times the gravity of water. There, heavier metals – zinc, copper, brass and stainless steel – sink, and aluminum floats. The aluminum is washed, sized, cleaned of rock and wire and dried. Some is sold as scrap and some is sent to the company’s smelter in River Rouge, Mich. The rock is washed, sized and sold for aggregate and the wire is sold to wire choppers.
The mixed heavier metals are then sized. Materials ranging from 30 to 60 millimeters and those ranging from 20 to 30 millimeters go to the main sort. The smaller materials in the 8 to 20 millimeter size are run over a slot tumbler to remove any coins that may have been in the car’s upholstery and ended up with the ASR, and the rest is sold to countries such as Taiwan to be hand sorted. Although Huron Valley technically could sort this stream, it’s not cost-effective as it only represents 1 percent to 2 percent of the total material.
The larger materials go to the main sort, a building containing 15 eddy current separators, where the metals are concentrated. Stainless steel, which is weakly magnetic, is separated out from the stream and sold. Copper bearing material that is 70 percent copper mixed with some zinc and stainless steel – not of good enough quality to sell as copper – is also separated at this point and generally sold to copper refiners or to export markets for hand sorting.
Then the remaining zinc, copper and brass are shipped to the first imaging plant where the zinc is targeted for separation. Processing approximately 20,000 pounds an hour, the high-tech system identifies each piece of zinc on the fast-moving belt and powerful bursts of air blow them over a splitter. The copper and brass then proceed to the second imaging line to be separated in a similar fashion.
“The sum total of sortation is to expose unlike things (metals) to like stimulus and make them behave differently,” says Osterberg. “We use flotation, eddy current separators, light imaging – anything that causes metals to behave differently.”
After sortation, zinc is further processed on site. Huron Valley operates one of the few zinc refineries in North America, and claims to be the only one with the capability of producing – from zinc die cast scrap – zinc of 99.995 percent purity that is registered on the London Metal Exchange. To reach that level of purity, zinc scrap is distilled in two four-story high columns, where it is heated to temperatures up to 2000 degrees Fahrenheit. The purest material, zinc vapor, rises to the top.
Zinc distillation is a fine art, according to Osterberg. “The zinc vapor is highly explosive, so it can’t be exposed to air,” he explains. “And you can’t shut off the zinc column once it has been heated up or you would have to completely rebuild it at a cost of $250,000.”
Purified zinc is made into ingots and sold to the zinc oxide, galvanizing, die casting and brass industries.
Like all scrap processors, Huron Valley faces its share of environmental compliance issues. Air and water issues are particularly significant. “We are upstream of the Lake Huron Metropark,” says Osterberg. “We’ve spent millions of dollars in monitoring and cleaning.”
The company uses 30,000 to 50,000 gallons of water a day for dust control. This water is recovered, cleaned and reused.
Spare Change |
What happens to the change that falls out of your pocket into the nooks and crannies of your car? You can rest as-sured that most of it is re-covered rather than land-filled. Automobiles often contain a few spare coins that have fallen into the upholstery, and these coins remain in the auto shredder residue. Huron Valley re-moves the coins – except for the pennies – from the ASR, sorts them by alloy, and then sells the metal back to the U.S. Mint. |
TRACKING THE AUTO INDUSTRY
Huron Valley has a strong interest in what happens in the automotive industry. “We try to keep abreast of what’s happening in the automotive industry because if they do exotic things, we’ll see it in 8 or 10 years,” says Osterberg. “We have to be prepared. Also, we have to inform them regarding what could hurt our process.”
Over the past 10 to 15 years, the ferrous content of cars has gone down and the plastics and aluminum content has gone up. “There is more aluminum, and less zinc and copper,” says Osterberg. “There are also a lot of electronics which don’t separate easily.”
The company also watches the ferrous scrap market closely, as the nonferrous market is driven by the ferrous market. “If there is no market for ferrous, shredders won’t buy cars,” says Osterberg.
OVERSEAS EXPANSION
The principals of Huron Valley saw an opportunity for expansion in Europe, where ASR was traditionally sent through a flotation process to recover aluminum, and then the heavier metals were sent to Asia to be hand sorted. On the site of a zinc refinery in Belgium, the company is starting up a sortation plant very similar to the one in Belleville. However, environmental laws in Belgium are very strict – and the plant is right on a canal – so much of the machinery has to be redesigned to meet that country’s stringent laws.
“It’s a real education,” says Wolanski. Huron Valley did some preliminary runs in the Belgian plant in March, and is currently “on a learning curve,” with the plant’s 100 percent Belgian workforce, all of whom are first trained at the U.S. operations.
One problem doing business in Europe is the ongoing debate, centered around the Basel Convention, on which materials qualify as scrap and which qualify as waste. “An old car is not considered waste if it is sold as a car, but if it is sold as scrap it is considered waste,” says Wolanski. “This will be an ongoing issue.”
The new European plant will have the same capacity as the Belleville plant. The main difference is that most shredders in Europe already separate aluminum from ASR in flotation plants, so Huron Valley Europe just buys the heavier metals, whereas in the U.S., ASR often still contains aluminum.
When they began looking for a European site, Huron Valley was courted by a number of European companies and countries, including Germany, the Netherlands and England. They finally settled on Belgium where they had a long-term relationship with a Belgian company, Union Miniere S.A.
“We have a couple of partners in Europe – Union Miniere S.A., and Limburgse Participatie Maatschappij (LPM), a state-owned company,” says Wolanski. “Union Miniere is large and well known in the mining industry, and operates a zinc refinery.” Huron Valley owns the majority of the new venture.
Although operating in Europe presents challenges, Huron Valley executives are optimistic. “Our material sells itself,” says Wolanski. “We just have to establish a presence there.”
TECHNOLOGICAL ADVANCES
Although Huron Valley already operates an innovative nonferrous separation system, the company is not content to rest on its laurels. “We are constantly developing new technology and pushing ahead,” says Dennis Reno, marketing director for the magnetics division. “A good metaphor is computer technology – if they stopped designing chips right now, they would continue to be successful for one or two years, and then they would rapidly go downhill. You have to continually upgrade to stay competitive.”
The company’s 16-member R&D department has been actively developing technology for Huron Valley to take its next step – the ability to analyze each piece of metal by alloy. Instead of using light to separate metal by color, the new technology currently under development will use laser spectroscopy to analyze each particle as it passes on a conveyor belt at a speed of 400 to 500 feet per minute. The objective is to increase the value of the materials. “All of our science responds to the market pull,” says Wolanski.
Huron Valley’s philosophy is simple – don’t throw anything away if it is economically feasible to recover and recycle it. The company has, so far, found creative and economically feasible ways to recover a great deal of valuable material that was previously landfilled, and there are likely more innovations to come.
The author is editor of Recycling Today.
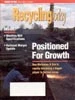
Explore the October 1997 Issue
Check out more from this issue and find your next story to read.
Latest from Recycling Today
- AF&PA report shows decrease in packaging paper shipments
- GreenMantra names new CEO
- Agilyx says Styrenyx technology reduces carbon footprint in styrene production
- SABIC’s Trucircle PE used for greenhouse roofing
- Hydro to add wire rod casthouse in Norway
- Hindalco to invest in copper, aluminum business in India
- Recycled steel price crosses $500 per ton threshold
- Smithers report looks at PCR plastic’s near-term prospects