Barry Hunter has been involved in the scrap industry for 45 years, specializing in stainless steel and alloys. He recently started his own firm, Hunter Alloys LLC, Boonton, N.J., with an international trading base focused on high-speed steel, tool steel and stainless.
With the growing concern about the U.S. (and possibly global) economy softening, Hunter offers his views on issues facing the stainless steel scrap industry.
Has there been a change in the role of the processor in the supply chain in relation to the shipment of stainless to consumers? Please explain some of the changes that are taking place.The biggest changes are related to the growing international aspects of the industry and the limited amount of major players that has evolved. The major producers of stainless, through expansion or consolidation, have greatly increased production capacities. Today, major mills basically all have the capacity to produce more than 1 million tons.
For this production, they must turn to long-term contracted scrap supplies to ensure themselves of at least a major portion of their monthly, quarterly and yearly scrap needs. Over the years, the situation has developed where very few major international suppliers are responsible for the majority of tonnage shipped directly to the mills.
In my view, this development has ultimately benefited the smaller scrap suppliers, as major wholesale buyers dramatically compete to secure sufficient tonnages to meet these long-term commitments.
Another dramatic change is also the unbelievable amount of information that is readily available related to every aspect of our industry.
High prices for stainless and nickel have resulted in some talk about substitution. How significant an issue could this be for the processors of stainless?Years ago it would have been much more significant, but with today’s technology and available tools, ensuring the quality of received scrap has become a lot easier. The talked-about substitute factor is generally for the basic 304 or 18/8. The substitutes—201, 301, Duplex—will basically all look like the industry standard 304.
As scrap, all these items can be used to produce various grades of stainless, either by themselves or in blends. However, the nickel and chrome contents will vary and must be identified correctly as compared to the norm of 18/8. Therefore, it is the processors’ responsibility to correctly identify these substitute grades, value the material correctly and then apply material where best suited.
With the landscape for producers changing, are requirements for scrap suppliers changing?I believe the need for scrap volumes will create custom-blend products to suit individual consumers’ needs and to enhance their raw material programs. Consumers and their major supplier or suppliers will determine the best product or products to suit their scrap needs, which will be directly related to the availability of scrap. This could involve higher iron, lesser nickel, lesser chrome, copper additives, etc., while constantly expressing the need to lower the potential of harmful residuals and to increase efficiencies in handling.
Is the overall melting capacity for specialty steel increasing or decreasing?According to reports I see, especially considering China and India, it is increasing. However, what I think is more important for the future is where that capacity will be produced and how long will it take to produce the tonnage required on a yearly basis. Many times it appears that the world can produce sufficient material in nine to 10 months to satisfy a full year’s production requirement.
How do you relate the above to the availability of scrap supplies?It’s a problem. With two types of scrap—obsolete and prompt industrial—there is the strong potential for a significant downturn in the availability of scrap. With high scrap prices over the last four or five years, a huge amount of the obsolete scrap has been accounted for; that backlog is basically gone. In the United States, with automotive down, housing down and general manufacturing down, it is difficult to see any substantial growth in the availability of prompt industrial scrap.
From my perspective, volume buyers test the elasticity of the markets to determine if more scrap comes out with higher prices. In my view, any additional scrap generated though this strategy has been taken away from someone else and does not relate to increased availability. Should China and Asia continue to dominate industrial manufacturing, the scrap generated from the manufacturing process will create availability within these regions. This scrap should obviously remain within these regions for remelting. I guess if I were to project out far enough, eventually this situation might limit, or at least greatly reduce, this region’s need for imports and create some balance between supply and demand in other parts of the world. But for the short term, based on current world production, scrap availability should remain tight.
There have been a number of high-profile mergers and new players coming into the market, notably in the United States. What kind of an impact will this have on the stainless steel market?Clearly North American Stainless (NAS) has changed the domestic stainless landscape, especially once it initiated its melting operations in 2002. Since then, I feel it is safe to say NAS has become the major producer of the standard stainless grades and the major consumer of U.S. stainless steel scrap.
The other two remaining major flat-rolled producers have seemingly altered their focus and product mix instead of competing for the volumes of scrap required by NAS for their production. The expanded focus of these mills is toward specialty stainless grades, finishes and sizes with expanded alloy ranges and products.
The eventual arrival of the Thyssen Krupp’s mill in Alabama slated for 2010, with yet another 1 million-ton capacity, will pressure NAS’s scrap dominance and influence over the U.S. scrap market.
Besides the aerospace industry, how are other end markets for stainless steel holding up. Are there opportunities outside traditional markets to grow the stainless steel business?Frankly, at this time it is difficult for me to see a major need beyond "traditional markets." For the majority of scrap dealers handling stainless steel, their market will remain the wholesale processor based on logistics, relationships, price and timing. With current international mill capacity to produce about 20 million tons a year of austenitic product, just assuming an average purchase scrap need is 50 percent—which in the U.S. and Europe is significantly higher—there will always be a need for quality scrap somewhere. For those major processors willing to accept the responsibility of direct tonnage supplies to these consuming markets, they will have the pressure to secure that committed tonnage, be it monthly, quarterly or yearly. In order to supply scrap, you have to buy scrap.
Logistics is becoming a major issue for the metals industry. Why?Stainless steel scrap is an international commodity. All consumers, processors, dealers, traders, brokers, etc., wherever they are, recognize they are competing for material with other potential buying markets all over the world. For example, no longer does scrap purchased for Pittsburgh assure delivery to a domestic consuming market. Locations near container rail siding or river barges offer alternatives beyond an immediate vicinity.
Scrap from Boston to Rotterdam via 20-foot standard containers may offer a freight advantage compared to trucking material to Pittsburgh. Likewise, containers from Rotterdam to China may have a price advantage compared to shipping scrap by rail or truck to Italy. Container shipments have changed the dynamics of marketing scrap metal.
I’ll bet in the past few years the manufacturers of container loading equipment have not been able to keep up with demand for product. There is no longer a definitive domestic market when it comes to stainless scrap.
With the softening of the economy, what is the short-term (six months) outlook for stainless steel and stainless steel scrap?I frankly don’t like to project either short term or long term; I’ll leave that to the analysts and the press. For me there are just way too many variables in today’s international market place impacting stainless and stainless scrap, and for that matter all scrap. For every point there is a counter point. I prefer to deal with what is right in front of me on a day-to-day basis and share my best evaluation of that information and experience with my suppliers and consumers.
Barry Hunter is president of Hunter Alloys LLC. He can be reached at bhunter@hunteralloys.com.
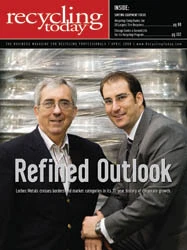
Explore the April 2008 Issue
Check out more from this issue and find your next story to read.
Latest from Recycling Today
- AF&PA report shows decrease in packaging paper shipments
- GreenMantra names new CEO
- Agilyx says Styrenyx technology reduces carbon footprint in styrene production
- SABIC’s Trucircle PE used for greenhouse roofing
- Hydro to add wire rod casthouse in Norway
- Hindalco to invest in copper, aluminum business in India
- Recycled steel price crosses $500 per ton threshold
- Smithers report looks at PCR plastic’s near-term prospects