How many times have you checked the lubricant level or the grease points on your baler? Remember that number. Now how does that figure hold up in comparison to how many times you have performed preventive maintenance or at least a visual check of the hydraulic hoses on the same equipment?
THE CRITICAL LINK
Hydraulic hoses, along with the other systems on your equipment, need to be checked on a regular basis for abrasion, wear and tear and site damage, as a hydraulic hose failure on any piece of equipment can bring it to a standstill in seconds and can take a long time to repair. A quick visual inspection of the high pressure hoses on your baling equipment at the end of a productive day can save your operation many headaches and downtime further down the line.
But it’s not just balers that rely on hydraulics for their continued operation. For example, if you have a fleet of recycling trucks, and one of your drivers calls you midway through his route to tell you that oil is leaking from beneath the vehicle, what happens next?
Some companies send one of their own service technicians to assess and repair the problem on site. Reaching the vehicle may not be easy depending on its location and traffic. When the technician arrives and finds the reason for the oil leak is a failed hose that needs replacement, he may have to spend more time—often upwards of an hour—removing the hose and locating a hose shop or dealer for a replacement part. If he is not familiar with the local area, it may mean that he has to drive back close to where he started from to get a new hose made before driving back to the vehicle to refit it and then ultimately drive back to his office. In total, your truck could be sidelined for hours unable to complete any work.
Let’s consider this: How much time and money does a simple hose failure cost your business? Well, in the case of the leaking recycling truck above, your service technician could have spent up to four hours driving from his office, to the site, to the hose shop or dealer, to the site and back to his office, not to mention spending up to two hours on site removing and replacing the hose. In this example alone, that’s a total of six hours of your technician’s time and six hours that your truck is out of commission and unable to perform its job. This doesn’t even include other costs, such as vehicle expenses, travel time, gas or downtime that prevent the job from being completed in a timely manner.
One specific case that comes to mind involved a Pirtek franchise partner in Georgia. Mike McCarthy, who owns Pirtek Norcross and Pirtek Smyrna, works with several large recycling companies. About two years ago, a major fire nearly destroyed one of his client’s automobile shredders. Since the shredder is used daily, having it out of commission for any length of time would have been detrimental to the company’s operation, and because of its size, the shredder had to be repaired on site. Fortunately McCarthy and his team were able to drive to the site and re-hose the entire system in one weekend instead of in the two weeks another company could have taken. Two years later, McCarthy still visits this client weekly to perform maintenance that ensures the machinery remains in proper working order.
To reduce the downtime of any piece of equipment in your fleet, you can follow a number of basic steps. These include visually inspecting all of the exposed hoses on your equipment and replacing the damaged or worn hoses, especially if you dispatch baling equipment to retail or warehouse locations. If you can easily see these hoses, they are the ones that are most likely to be damaged externally and are the one most susceptible to wear.
IDENTIFYING HOSE FAILURES
There are six common hose failure scenarios. Once identified, the solutions for repair are straightforward. These common scenarios include:
1. Abrasion—The hose has failed with signs of rubbing on the outer cover.
Solution—Check to see if the hose can be rerouted. Use clamps to hold the hose or provide a hose guard on the replacement hose as an additional precaution.
2. Excessive heat—The hose cover and/or the inner tube are brittle to
the touch and have a cracked appearance. The hose is not flexible at room temperature.
Solution—Using the method known as STAMPED (which stands for size, temperature, application, medium, pressure, ends and delivery), choose a hose that has the correct temperature rating for the application and provide additional protection with heat shields or fire jackets.
3. Excessive pressure—The hose has burst cleanly with no random wire breakage or cover abrasion.
Solution—Verify the correct system operating pressure and setting. Choose a hose that meets or exceeds the pressure rating for the application.
4. End fitting blown off—The end fitting has blown off the hose either with or without the ferrule. No other external damage is evident.
Solution—Ensure the correct assembly procedures have been followed by referring to your product catalogues or by calling your service provider. Ensure that only the correct parts have been used (for example, the hose and fitting should be from the same supplier) and never mix components from different manufacturers.
5. End fitting broken off—The fitting has broken off leaving some or all of the fitting tail inside the inner tube and the ferrule attached.
Solution—The fitting has broken off as the result of an outside influence. Try to identify the source of this outside damage and eliminate it by rerouting the hose or correctly routing the hose in the case of a poor previous repair. Always use any brackets that are provided by the manufacturer.
6. Incompatible fluid—The inner tube is deteriorated and swollen. The outer cover of the hose may be peeling off.
Solution—Establish the correct hose for this application by referring to the chemical compatibility chart for guidance.
CONSIDERING HOSE SLEEVING
To protect hoses from external damage and wear, you can use or specify several different types of hose sleeves that can help to extend the life of hydraulic hoses. For example:
1. Metal Spring Guard—This form of hose protection is often used when an exposed hose may encounter a very aggressive environment. The spiral metal guard can be used in areas where the hydraulic hose may be easily damaged by external forces. The metal spring guard needs to be fitted before the hose is assembled.
2. Plastic SprinG guard—This is also used on exposed hoses but has the added advantage of being able to be fitted both after the hose has been assembled and sometimes after it is fitted to the equipment.
3. Textile Sleeving—This type of sleeving is more often used on hoses that are somewhat less exposed further inside the equipment or in places where abrasion may occur. The textile sleeving has excellent wear characteristics and can help reduce the amount of oil spillage.
Using these basic steps should help to reduce your job site downtime as the result of a hose failure.
The author is director of franchise support at Pirtek USA, Rockledge, Fla., a provider of on-site hose replacement services. More information is available online at www.pirtekusa.com.
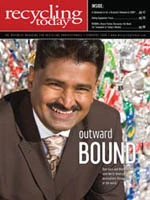
Explore the February 2009 Issue
Check out more from this issue and find your next story to read.
Latest from Recycling Today
- AF&PA report shows decrease in packaging paper shipments
- GreenMantra names new CEO
- Agilyx says Styrenyx technology reduces carbon footprint in styrene production
- SABIC’s Trucircle PE used for greenhouse roofing
- Hydro to add wire rod casthouse in Norway
- Hindalco to invest in copper, aluminum business in India
- Recycled steel price crosses $500 per ton threshold
- Smithers report looks at PCR plastic’s near-term prospects