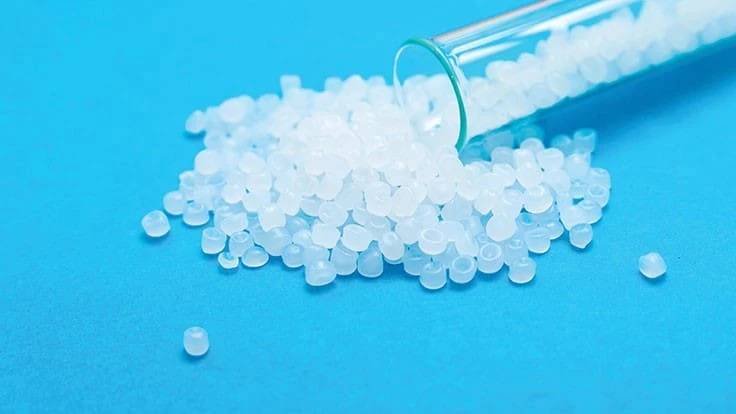
Stanislau_V | stock.adobe.com
Honeywell, headquartered in Charlotte, North Carolina, says it has commercialized a process that expands the types of plastics that can be recycled, producing feedstock that enables manufacturing recycled plastics with a lower carbon footprint.
The company’s UpCycle Process Technology uses molecular conversion, pyrolysis and contaminants management technology to convert end-of-life plastics into feedstock for the production of recycled plastics. It is suitable for colored, flexible, multilayered packaging and polystyrene. When used in conjunction with other chemical and mechanical recycling processes—along with improvements to collection and sorting—Honeywell says its UpCycle Process Technology has the potential to increase the amount global plastic recycling rate to 90 percent.
The company says recycled plastics produced via UpCycle Process Technology can result in a 57 percent reduction of carbon dioxide-equivalent (CO2e) emissions compared with the production of the same amount of virgin plastic from fossil feeds, according to a Honeywell Life Cycle Analysis published in October. The process also reduces CO2e emissions by 77 percent compared with conventional modes of handling postuse plastic, such as incineration and landfilling.
"Plastics play an important role in our society, including expanding the shelf life of food and making vehicles lighter, which reduces their emissions. Unfortunately, only a fraction of plastics today can be successfully recycled," says Vimal Kapur, president and chief executive officer of Honeywell Performance Materials and Technologies. "Honeywell's UpCycle process helps fix this problem. By broadening the types of plastic that can be recycled, UpCycle will revolutionize the plastics economy and play a critical role in improving the sustainability of many of the products we use on a daily basis."
Sacyr, a global engineering and services company headquartered in Madrid with operations in more than 20 countries worldwide, will be the first to deploy Honeywell's proprietary UpCycle Process Technology. Honeywell and Sacyr are partnering to form a joint venture where the two companies will co-own and operate a facility in Andalucía, in southern Spain, with the capacity to handle 30,000 metric tons annually of mixed plastics into Honeywell Recycled Polymer Feedstock. Production is expected to begin in 2023, Honeywell says.
Partnering with companies that have waste management experience will allow Honeywell to help close the loop within the plastics supply chain by bringing the recycling technology on-site to the collection source. The recycling plants feature a modular design, facilitating deployment and installation, according to the company.
"Our partnership with Honeywell will enable Sacyr to bring sustainable, circular solutions to market," says Domingo Jiménez, manager of Sacyr Circular. "The speed with which we can start up plants and the global viability of this solution has the potential to greatly accelerate the impact we can have on the communities we serve, the environment and society as a whole."
Honeywell's UpCycle Process Technology was created within Honeywell's Sustainable Technology Solutions (STS) group, which is part of Honeywell UOP.
Latest from Recycling Today
- Aqua Metals secures $1.5M loan, reports operational strides
- AF&PA urges veto of NY bill
- Aluminum Association includes recycling among 2025 policy priorities
- AISI applauds waterways spending bill
- Lux Research questions hydrogen’s transportation role
- Sonoco selling thermoformed, flexible packaging business to Toppan for $1.8B
- ReMA offers Superfund informational reports
- Hyster-Yale commits to US production