For the last several decades, the consensus has been that there is a scrap tire surplus, with most states either currently or formerly having been plagued with scrap tire stockpiles. Contrarily, tire recyclers often say that an inability to guaranteesufficient supply has been a barrier to tire recycling success in some markets.

Recyclers who can figure out how to help solve each of these dilemmas are attempting to bring balance to the markets, says Marty Sergi, president of Recovery Technologies Group (RTG), Guttenberg, N.J. More importantly, Sergi is confident that solving the problems will not require several five-year plans, but says in fact steps toward a solution are well underway.
OUT OF BALANCE. Stockpiles of scrap tires—some of which have caught fire while the rest become nuisances in other ways—have helped lend an aura of undesirability to this potential secondary commodity.
Tire recycling has also had its share of participants who have promised to lift up the industry only to retreat in disappointment a few years later.
Into this arena has stepped Marty Sergi, who first got involved in tire recycling when he was CEO of the former KTI Inc., a multiple materials recycling firm that was purchased by Casella Waste Systems, Rutland, Vt., in 1999.
Sergi says the leadership team of the former KTI "took waste streams of all types and found low-cost-producer ways to take negative value trash of all types and make it into higher value commodities."
Sergi and others at KTI, "began looking at tires in the early 1990s," he says, admitting that, "of all the scrap streams, the tire stream was the most puzzling and appeared to be the most disorganized. We saw that the industry lacked integration and was operating as an undercapitalized market."
Different companies in different regions were trying to scrape by serving the nearest consumers—whether tire-derived fuel (TDF) consumers or crumb rubber consumers such as rubber mat manufacturers.
Another problem was the reliance on TDF markets, says Sergi. Using tire shreds as boiler or kiln fuel means the material will always compete with other available fuel sources as a low-cost material. "The reality is, it should be better economically for us to go to the crumb rubber stage. In every material stream, you have to get to those higher-value chains. Purely as TDF, I don’t think this industry can every be very attractive to investors. When you get to crumb, you’re making a higher-quality and higher margin product."
The barriers to implementing such an upgrade, however, were many.
A PARTNER WITH A PURPOSE. RTG’s campaign to shift from a TDF-based model for the industry to a crumb-rubber based model has hardly been a solo effort, Sergi acknowledges.
Help has come on the processing side of the equation from a Canadian company that vastly improved the cryogenic recycling process. On the market development side, meanwhile, RTG has received a valuable assist from Ford Motor Co., Dearborn, Mich., and its Worldwide Director of Environmental Outreach & Strategy Andrew G. Acho.
FIRST AND TEN |
Viewers of both pro and college football this season are bound to see some recycled crumb rubber appearing in their programming mix. RTG Inc., Guttenberg, N.J., has been a key supplier of a crumb rubber turf additive that is being applied by sports turf maintenance and supply markets in record amounts. The material has gained favor as a key part of a new synthetic material called "turf grass" that features crumb rubber as a soil substitute as its base surface and also as an additive to natural grass fields. On natural surfaces, it is added after aeration to help make the playing surface softer. According to RTG president Marty Sergi, crumb rubber has been applied as a turf additive to the playing and practice fields of a number of pro and college teams, including the NFL’s Dallas Cowboys, Denver Broncos, Detroit Lions, Jacksonville Jaguars, New York Giants and Jets and Seattle Seahawks. High-profile college programs using the material include the Michigan Wolverines and the Nebraska Cornhuskers. (Baseball’s Tampa Bay Devil Rays also use it on their baseball surface at Tropicana field.) Regarding the spring rubber surface, Detroit Lions head trainer Al Bellamy, says, "We see less joint soreness post-game and after practices. There are also fewer [ground] impact injuries." Lions punter John Jett says on some olders surfaces, it "was like playing on concrete; there was no give." |
Sergi discovered the former Recycling Technologies Inc. (RTI) of Cambridge, Ontario, Canada, in 1998 while still with KTI. RTI had developed an improved cryogenic tire recycling process using just 15 percent of the amount of liquid nitrogen used in previous methods, thus greatly reducing the expense of making crumb rubber. "Here was a process in their pilot plant that could make 15 million pounds of crumb rubber annually and work economically," notes Sergi.
"If they were making a margin on their pilot plant, why not build more plants for ourselves," Sergi says. "We did our due diligence and bought that company in late 1998, turning RTI into RTG."
The RTI process has helped RTG produce the volumes of crumb rubber it needs to sustain expanded markets. Not long after forming RTG, Sergi had the good fortune of meeting Ford Motor Co.’s Andy Acho, resulting in some vital boosts both on the end markets side of the equation and in guaranteeing a supply of tires.
Acho, in his environmental position created with a specific mandate by Ford Motor Chairman and CEO Bill Ford, was looking for a way to make sure end-of-life tires generated by Ford dealerships and at other Ford facilities were recycled responsibly. "We asked RTG to pick up tires from Ford and Lincoln-Mercury dealerships," says Acho. "We didn’t want dealers sending tires to landfills or even to go to TDF markets in case there would be instances where tires are not burned responsibly."
The supply arrangement has worked out well for both Ford and RTG. But Acho and Ford Motor Co. have gone above and beyond this arrangement by actively promoting recycled tire uses into the types of high-margin end markets that can make RTG’s dreams of moving the scrap tire market beyond TDF a reality.
ON THE GROUND. America is a sports-crazy nation, with athletic fields and golf courses covering a significant amount of acreage when totals from all 50 states are considered.
These carefully maintained surfaces are proving to be an ideal home for crumb rubber in a rapidly spreading application that RTG is capitalizing on, often with help from Ford Motor Co.
"That whole market has exploded," Sergi says of the athletic turf market for RTG. "When we started in 1998, RTI had applied crumb to one or two fields. This year, between 700 and 1,000 fields are operating with crumb rubber as part of their base. It has grown from a 5-million- pound market (annually) for crumb rubber into a nearly 200-million-pound market."
Indeed, viewers of college and pro football this season can routinely see small black bits of crumb rubber spraying up from the field as receivers drag their feet to stay in bounds or as players hit the ground hard after a tackle or dive.

Among the fields with a crumb rubber base is Ford Field in Detroit, home of the NFL’s Detroit Lions. Working directly with the Ford family, which owns the Lions, and other Lions officials, Acho and Sergi were able to convince the Lions organization of the wisdom of installing an artificial "turf grass" surface with a crumb rubber base soil substitute at both Ford Field and at the Lions’ practice facility in Allen Park, Mich.
Acho says that at a recent Ford Motor Co. and Detroit Lions event, Bill Ford referred to the recycled surface as, "Andy Acho’s crazy idea, which I love."
A grass-like surface is made from a webbed plastic material that shreds into strands that closely replicate blades of grass.
At the base of these "blades," a healthy layer of crumb rubber is applied. The crumb contributes many important qualities to the playing surface, according to Sergi and Acho. And their viewpoints are backed by professional and collegiate front office personnel, coaches, trainers and players, as organizations are converting in large numbers to this new surface, which offers the softness of natural grass and the durability and maintenance-free qualities of an artificial surface.
According to Sergi, about 300,000 pounds of crumb rubber (sometimes mixed with sand) is applied to a typical football or soccer field outfitted with the plastic turf grass. Occasionally, some new crumb rubber must be added to replace crumb lost through ongoing action, and the field can also be raked or brushed intermittently.
The fields are as durable as traditional artificial surfaces, but without the drawback of the bone jarring impacts on the joints and bones of players as they run and land on the field.
Although there are already as many as 1,000 fields sporting crumb rubber as part of their surface or base, Sergi and Acho say there is still plenty of growth left in the market. Much of the current and future growth in this market is being driven by Ford Motor Co., with its involvement spreading far beyond the Lions.
RTG has now picked up and recycled some 8 million passenger tires at Ford dealerships. And with Acho’s prodding, Ford dealerships are also promoting the availability of the crumb rubber to high schools, colleges, golf course managers, horse farm managers and municipal recreation departments throughout the U.S.
As part of its community involvement efforts, Ford has at times helped underwrite the use of the crumb rubber. "We have worked with dealers to help high schools with running tracks and with natural turf fields," says Acho.
BIGGEST MARKET YET. The exploding turf market has helped RTG reach a point where, by Sergi’s estimation, 85 percent of its output is going into what he refers to as higher-end markets, including the turf additive, molded parts, landscaping mulch and rubberized asphalt markets. With another 7 or 8 percent going into civil engineering applications, Sergi says that less than 10 percent of RTG’s output is going to the TDF market.
"Economically, we want to keep moving up that ladder away from TDF. If you can sell a product for $300 to $500 per ton instead of $50 per ton, you no longer have a waste product," Sergi says of scrap tires. "In fact, you have a product for which the generator may be able to fetch a few dollars."
Currently, RTG still charges a tipping fee for scrap tires, although Sergi says it has lowered considerably because of the booming athletic turf market. The potential of another market—colored rubber mulch produced from scrap tires—could be the factor that causes tipping fees for tires to disappear altogether.
Rubberized mulch has been sold for several years, with initial results seeming to show that consumers are not reluctant about using the product, and in fact quickly understand the advantages of a product that will last much longer on the ground.
"The problem, from our point of view, is that there has not been a company fully integrated to make this product and take it directly to major retailers," says Sergi. "That’s where we’re trying to position ourselves," he adds.
In other words, current suppliers of the material are unable to fill the types of bulk orders that would be made by national retailing giants such as Home Depot, Lowe’s or Wal-Mart.
Sergi’s mission is to develop a closed loop system in which tires collected from major retailers such as Wal-Mart or Sam’s Club are recycled into products such as rubber mulch for gardens that they can sell back to their customers.
Once again in this market, Acho and Ford Motor Co. are lending support. Rubberized mulch made with RTG’s tires can be found on the grounds of Ford’s World Headquarters in Dearborn as well at other Ford facilities.
Acho says that Ford’s role in growing the mulch market, as with the athletic turf market, is to act as a "catalyst" in the early stages. "We believe we have helped by providing financial support and jump starting key end markets with demonstration projects," he remarks.
Sergi says RTG has been designed to serve several end markets with a demand for a variety of secondary products. As each of those products gains momentum, not only will RTG’s bottom line be enhanced, but so will the nature of the entire scrap tire industry. "I think in the case of tires, tipping fees will go way down and in five to 10 years, we’ll be paying for tires."
Tire recyclers have worked for a long time for such a development. If RTG can help it become a reality, Marty Sergi will reserve a place for himself as a key figure in the history of tire recycling.
The author is editor of Recycling Today and can be contacted via e-mail at btaylor@RecyclingToday.com.
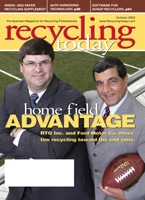
Explore the October 2003 Issue
Check out more from this issue and find your next story to read.
Latest from Recycling Today
- Nucor receives West Virginia funding assist
- Ferrous market ends 2024 in familiar rut
- Aqua Metals secures $1.5M loan, reports operational strides
- AF&PA urges veto of NY bill
- Aluminum Association includes recycling among 2025 policy priorities
- AISI applauds waterways spending bill
- Lux Research questions hydrogen’s transportation role
- Sonoco selling thermoformed, flexible packaging business to Toppan for $1.8B