Developing specifications for the use of recycled aggregated continues to make progress.
Various recycled materials have and are being used in new construction applications. Some materials, such as recycled asphalt pavement (RAP), have been extremely successful in achieving broad acceptance as a highway construction material.
Other materials have been less successful. In the case of RAP, most states or provinces have developed specification for its use in hot mix asphalt. Many benefits from this practice, including reduced binder content to savings in landfill space, have been appreciated.
One reason for the successful use of RAP in hot mix asphalt paving has been the concerted effort by the asphalt paving industry and state transportation departments to introduce provisions in their standard specifications to permit and to provide guidance on the use of RAP in hot mix asphalt. The absence of such specifications for other recycled materials is one reason for the lack of similar successful recycled material applications.
FORMING ALLIANCES
To provide for the development of specifications for other recycled materials, Chesner Engineering P.C., Commack, N.Y., was retained by the University of New Hampshire’s (UNH) Recycled Materials Resource Center (RMRC) and the Federal Highway Administration to prepare such specifications for publication in the American Association of State Highway and Transportation Officials (AASHTO) Materials Standards.
At publication, four standards have been prepared. These are Glass Cullet in Soil-Aggregate Base Course, Reclaimed Concrete Aggregate for Unbound Soil Aggregate Base Course, Reclaimed Concrete Aggregate for use as Course Aggregate in Portland Cement Concrete, and Coal Combustion Fly Ash for Structural Fills and Embankments. More work is planned.
Key to the success of this ongoing project is the existence of a Technical Advisory Group (TAG). The TAG is an oversight group made up of the representatives of 15 state or provincial departments of transportation. The membership represents all regions of the country and those states (or provinces) with the greatest experience in the use of recycled materials. The representatives are from California, Florida, Illinois, Maryland, Massachusetts, Michigan, Minnesota, New Hampshire, New Jersey, New York, North Carolina, Ohio, Ontario, Pennsylvania, Texas and Wisconsin. The role of the TAG is to review the draft specifications and provide input and critique of the draft specifications.
This project is known at UNH as Project 13/14. The specification development process is straightforward. Specifications from state and provincial transportation agencies where the recycled material has been or is being used are reviewed and evaluated. A phone survey of participating states is conducted and relevant literature on the recycled material is reviewed. In addition, private companies, associations and trade groups may also be contacted to supply data based on their experiences.
A draft specification is subsequently prepared with a supporting white paper. This white paper describes in detail the basis for the provisions in the specification. The specification itself is written in standard American Association of State Highway and Transportation Officials (AASHTO) format, with one notable exception. This is the use of numerous footnotes and appendices that are included in the specification to provide a mechanism to inform the engineer and potential recycler of specific properties of the recycled material that are atypical, when compared to conventional materials. As experience is gained in the use of these materials, it should be possible to delete some or all of the footnotes and appendices from the standard.
After completion of the draft, the specification and white paper are submitted to the TAG for review and comments. After receipt of these comments, the specification and white paper are editing and revised as needed and the final draft of the specification is submitted to the AASHTO Sub-Committee on Materials.
CONCRETE CONCLUSIONS
At this writing, the specification for reclaimed concrete aggregate as a base course has passed the balloting of the AASHTO Sub-Committee on Materials and will be part of the next printing of the AASHTO Standard Specifications for Materials. The reclaimed concrete aggregate for aggregate in portland cement concrete specification is under review by the Technical Section of the AASHTO Sub-committee on Materials responsible for aggregate materials. The following highlights the requirement of these two specifications:
1. Reclaimed Concrete Aggregate as Base Course:
This specification is modeled after AASHTO M147, the specification for traditional base course materials. The highlights of this standard include:
• The reclaimed concrete aggregate must be derived from crushed portland cement concrete.
• The minus No.40 sieve material shall have a Liquid Limit of less than 30 and a Plasticity Index of less than four.
• It shall have a maximum Los Angeles Wear of 50 percent.
• The reclaimed concrete aggregate may be mixed with natural soil aggregate.
• If mixing is permitted, an optimum combination ratio must be developed and blending must be by mechanical interlock, conveyor belt or other approved method.
• The gradation of the reclaimed concrete aggregate or mixture of reclaimed concrete aggregate and natural material must meet the requirements of AASHTO M147 or the specifying jurisdiction.
• Deleterious substances must be limited to a maximum of 5 percent bituminous concrete material and 5 percent brick.
• The reclaimed concrete aggregate must be substantially free of wood, metal, plaster and gypsum and free of solid waste or hazardous materials.
• The issue of soundness was specifically called out in the specification due to potential difficulties that could be encountered with the standard sulfate soundness test methods (see discussion below).
There are nine notes that are part of the specification. The following briefly outlines the substance of each note:
• Note 1 – This note cautions the user that reclaimed concrete aggregate, because of the entrained air void system present in the mortar of the concrete, exhibits higher water absorption properties than traditional soil aggregate materials. As a result the user can expect the optimum moisture content to be higher than what would be expected in a traditional granular base course.
• Note 2 – This note cautions the user that reclaimed concrete aggregate in an aqueous environment results in high alkali soil condition. The resulting pH values will be in the range of 11 to 12. Steps must be taken to prevent the transportation of high alkali liquids to surface water bodies. Similarly, metal drainage structures must also be protected.
• Note 3 – This note cautions the user as to the possibility of mineral deposit formation, known as "Tufa" that could occur in geo-textiles and soil drainage layers.
• Note 4 – In this note the user is cautioned that the void structure of base course layers may become closed as the result of mineral deposition. The permeability of the layer will be reduced accordingly.
• Note 5 – In this note the user is informed of the high degree of variability that may be expected in sodium and magnesium sulfate soundness testing.
• Note 6 – In this note the user is cautioned that hazardous and solid waste materials as defined by state regulatory agencies may be present in the reclaimed concrete aggregate.
• Note 7 – In this note the user is provided with a recommended method for validating the use of higher percentages of bituminous concrete in reclaimed concrete aggregate.
• Note 8 – In this note the user is made aware that stockpiling of the manufactured materials is a good method of performing quality control/quality assurance analysis.
• Note 9 – In this note the term "substantially free" is defined.
There are also four appendices that are part of this specification. The following briefly outlines the substance of each appendix:
• Appendix 1 – A method of performing density control is introduced. This method may be used to compensate for changes in base course compacted density that results from the presence of different natural aggregate types of reclaimed concrete aggregate.
• Appendix 2 – The phenomenon of the deposition of Tufa-like deposits is explained. The appendix also describes a test procedure for determining the potential for geo-textile clogging due to tufa deposition.
• Appendix 3 – Problems with sulfate soundness testing of reclaimed concrete aggregate are described. Four alternative test methods, with recommended acceptance criteria, to standard sulfate soundness testing are presented.
• Appendix 4 – A procedure for approving the use of higher percentages of bituminous concrete or brick in introduced. This procedure uses either California Bearing Ratio (CBR) or resilient modulus testing to determine the suitability of higher percentages.
2. Reclaimed Concrete Aggregate for Aggregate in Portland Cement Concrete:
The highlights of this standard are listed below:
• Reclaimed concrete aggregate as an aggregate must meet the gradation requirement of AASHTO M 43 or of the specifying agency.
• Blending of reclaimed concrete aggregate with other natural materials is permitted, however, blending must be accomplished by the use of mechanical interlock, conveyor belt or other approved method.
• The reclaimed concrete aggregate must meet the Los Angeles Wear requirements of a maximum of 50 percent.
• The soundness testing limitations, described above for reclaimed concrete aggregate as an unbound base course, also apply to reclaimed concrete aggregate as an aggregate.
• The reclaimed concrete aggregate must meet the reactive aggregate limitations of the specifying agency. An appendix to the specification elaborates these requirements. In parts of the country where D-cracking of concrete is a known problem, the reclaimed concrete aggregate must be tested in accordance with ASTM C 666 or equivalent.
• The flat and elongated particle requirements of the specifying jurisdiction must also be complied with.
• The presence of extraneous and deleterious materials in reclaimed concrete aggregate are limited to the following: clay lumps- maximum of 3 percent or 5 percent; chert-3 percent, 5 percent or 8 percent; cumulative clay lumps and chert- 3 percent, 5 percent or 8 percent; coal and lignite-maximum 0.5 percent; other deleterious substances consisting of adherent fines, vegetable matter, plastics, paper, plaster, gypsum, metals, fabric, wood, brick, tile, glass and bituminous material-0.3 percent maximum.[The exact requirements will depend on the service use application of the new portland cement concrete.]
• Since the portland cement concrete used to manufacture reclaimed concrete aggregate may have been subjected to deicing salts there is an additional requirement that the reclaimed concrete aggregate contain no more than 0.6 pounds per cubic yard of chloride ion.
There are six notes that are part of this specification. The following briefly outlines the substance of each note:
• Note 1 – This note recommends that quality control/quality assurance practices be initiated in addition to the requirements of this specification.
• Note 2 – The user is cautioned that reclaimed concrete aggregate will probably exhibit high water absorption properties and variations in specific gravity may occur.
• Note 3 – The user is cautioned regarding testing variables that may occur when testing the performance of sodium or magnesium sulfate soundness testing.
• Note 4 – The user is cautioned to be fully aware of the definitions and requirement of the local environment protection agency with regard to hazardous waste materials.
• Note 5 – The user is cautioned that segregation of reclaimed concrete aggregate materials may occur during stockpiling operations. Steps to mitigate this problem are recommended.
• Note 6 – The user is advised that stockpiling of reclaimed concrete aggregate material prior to use may be an effective quality control/quality acceptance procedure.
There are four appendices that are part of this specification:
• Appendix 1 – This appendix outlines quality control and quality assurance procedures that have been shown to be effective in controlling the quality of reclaimed concrete aggregate materials.
• Appendix 2 – This appendix informs the user that because of the nature of reclaimed concrete aggregate, high water absorption properties are likely. Additionally, there is a potential for variation in the specific gravity of reclaimed concrete aggregate. This is particularly true when portland cement concrete containing different aggregate types is used in the manufacture of reclaimed concrete aggregate. The appendix discusses methods of dealing with these problems.
• Appendix 3 – Problems with sulfate soundness testing of reclaimed concrete aggregate is described. Four alternative test methods, with recommended acceptance criteria, to standard sulfate soundness testing are presented.
• Appendix 4 – This appendix includes a discussion of various testing methods that are used to assess the potential reactivity of aggregate materials.
These specifications are available for viewing at the University of New Hampshire’s Recycled Materials Research center web site: http://www.rmrc.unh.edu/.
The authors are associates with Chesner Engineering, P.C., Commack, N.Y.
Get curated news on YOUR industry.
Enter your email to receive our newsletters.
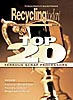
Explore the March 2002 Issue
Check out more from this issue and find your next story to read.
Latest from Recycling Today
- Circular by Shapiro releases "5 for Five" sustainability series
- Graphic Packaging set to close Ohio CRB facility
- Ameripen voices support for Maryland EPR bill
- Matalco to close Canton, Ohio, plant
- Maryland county expands curbside recycling to include electronics
- California EPS ban will be enforced
- YKK AP America introduces BetterBillet
- Fresh Perspective: Cameron Keefe