
eFACTOR3 LLC has built a sterling reputation in North America for providing high-quality shredding and recycling technology to the continent’s growing plastics reprocessing sector. Thanks to a long-standing partnership with Austria-based MAS Plastic Extrusion Technology, the team at eFACTOR3 has been working with customers to install systems that use a one-step process to convert almost any type of plastic scrap to a highly marketable recycled-content pellet.

“Plastic recycling investments are escalating by both our current and prospective customers,” says Hartmut Bendfeldt, President of North Carolina-based eFACTOR3. “Customers are looking for solutions to convert their scrap into highly marketable pellets that can compete with virgin pellets on quality and price,” he continues.
In addition to its traditional plastic recycling equipment line, eFACTOR3 has broadened what it can offer its North American customers with its agreement to offer the MAS-K conical co-rotating twin-screw extruder systems that perform extruding, compounding and pelletizing in one process.
The MAS-K system features a large infeed opening, allowing it to extrude a sizable volume of product created from a wide range of plastic resins and feedstocks—whether regrind, film flakes or lower-density materials, including shredded fibers and non-woven materials.
_fmt.png)
A sophisticated continuous melt filtration system in the MAS-K allows for removal of soft contaminants, like paper, wood and other contaminants, prior to final degassing and pelletizing. The entire system features a small footprint on the shop floor, a shorter conversion cycle time and a low-carbon footprint for the recycler, thanks to the MAS-K’s ability to maintain a low melt temperature throughout the process.

It is a true UP-CYCLING System that offers great flexibility to plastic recycling and processing.
Because it combines recycling and compounding in one step, the MAS-K has proven popular in Europe, says Stefan Lehner, General Sales Manager of MAS. He cites several reasons that will be just as appealing to North American recyclers. “Operators can adjust the properties and the recipe,” he states, pointing to a versatility that will appeal to plant managers who handle polypropylene (PP), high-density polyethylene (HDPE), polyethylene terephthalate (PET), acrylonitrile butadiene styrene (ABS) and other types of plastic.
The system offers this versatility in a small footprint while also offering ease of maintenance compared with most existing extrusion-compounding processes. On the maintenance front, notes Sebastian Ward, General Sales Manager of eFACTOR3, “Anyone who has operated an extruder knows it is not if but when the time will come when you extract the screws for maintenance.”
With most existing machines, this is a daunting process that can take from six to eight hours. But Bendfeldt says of the MAS-K, “One can access the screws fairly easily by just opening up the machine and swiveling the barrel to the side and pulling the screws to the back. No need to dismantle up or downstream equipment. The entire process of pulling a set of screws takes less than an hour and a half.”
More importantly, when the machine is running, “We offer recycling and compounding in one step,” notes Lehner. “You can produce more profit all while appealing to a wider range of customers and enjoying operational flexibility.”
Bendfeldt and Ward are confident the attributes of the MAS-K system will prove popular with the growing number of companies seeking to add plastics recycling and reprocessing capacity. “The unique nature of the co-rotating, conical twin-screw extruder combined with the continuous melt filtration and cascading extruder for proper degassing drastically enhance the quality of pellets produced,” says Ward.
The lower energy requirements—up to 30 percent less—not only save money, they also allow MAS-K plant operators “to limit the amount of carbonization,” says Ward, in an era when such metrics are an increasingly important yardstick.
Lehner is excited to bring this unique MAS technology to America and sees the need for it based in part on this metric. “We have customers who get asked to provide certificates about reduction in carbon footprint. This can be necessary for pellet sales. Circular Economy is no longer just a term used by politicians—it is now a reality.”
In the wider plastics packaging and products industry, recycled-content pellets and resins also are casting off their reputation as secondary in quality, and the MAS-K is an important part of this revolution. Bendfeldt says, “With this technology, we get a top-quality material from recycled content that can compete with virgin material in many cases.”
Thus, it is not just cost savings that can impact the bottom line for MAS-K system owners, but they also can experience a boost to the top line. “Customers can demand a premium for the pellets they are making with their recycled material, and this could be from 5 to 10 cents per pound,” Bendfeldt says.
MAS and eFACTOR3 anticipate an active market in 2022 and urge recyclers with an interest in the technology to begin exploring their options immediately. The two companies are offering systems that can handle anywhere from 500 pounds to 4,500 pounds per hour of plastic scrap.
“We’re looking at oil prices of over $100 per barrel,” Ward says. “Recycled material has never been more cost-effective than it is right now. Existing customers are investing in plant expansions, and some investor-backed companies are just entering the sector. eFACTOR3 has aligned with the right partner in MAS. The innovative MAS-K product meets our rigorous quality standards, and it will meet those of our customers.”
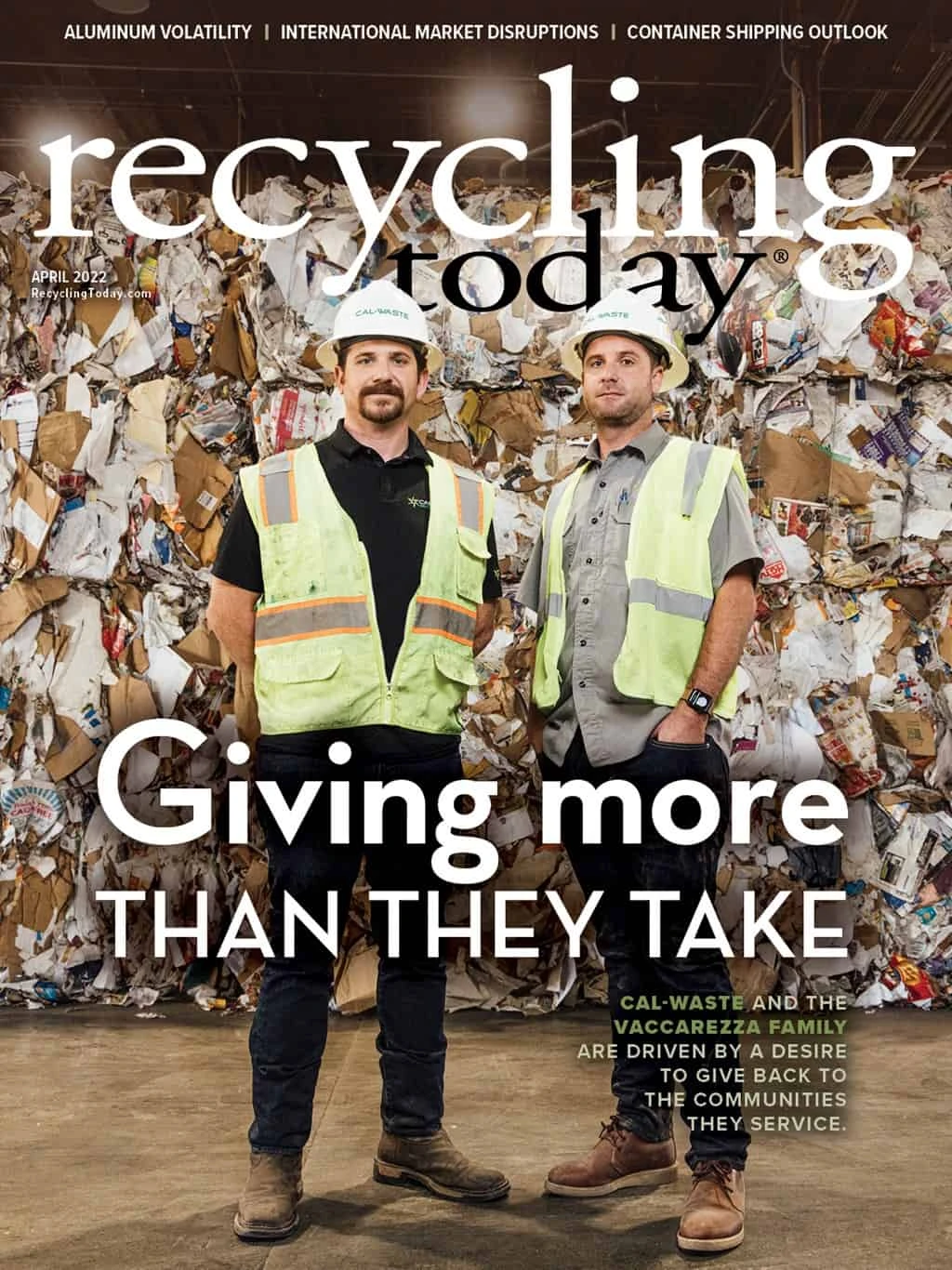
Explore the April 2022 Issue
Check out more from this issue and find your next story to read.
Latest from Recycling Today
- Fenix Parts acquires Assured Auto Parts
- PTR appoints new VP of independent hauler sales
- Updated: Grede to close Alabama foundry
- Leadpoint VP of recycling retires
- Study looks at potential impact of chemical recycling on global plastic pollution
- Foreign Pollution Fee Act addresses unfair trade practices of nonmarket economies
- GFL opens new MRF in Edmonton, Alberta
- MTM Critical Metals secures supply agreement with Dynamic Lifecycle Innovations