Aerojet Ordnance Tennessee, Jonesborough, a wholly owned subsidiary of aerospace and defense contractor Aerojet General, based in Sacramento, Calif., fabricates parts from tungsten heavy alloys and other refractory metals for defense related products, such as ammunition, warheads and electronic shielding. The company also produces components for sporting goods and other end uses, though defense accounts for about 80 percent of its business.
Tungsten heavy alloys are one of the densest metals produced. Reclaiming fabrication scrap was difficult and costly, prompting Aerojet to sell the scrap at significantly lower prices than it was worth as a recycled and reusable material.
The company uses tungsten heavy alloys for the properties they provide, including corrosion and radiation resistance, thermal and electrical conductivity and machinability. The alloys are formulated with tungsten (85 percent to 98 percent) and binders (nickel, iron, copper and other elements). Densities for tungsten heavy alloys range from 1,060 to 1,160 pounds per cubic foot (17 to 18.6 grams per cubic centimeter), which is about 2.5 times the density of steel. For example, Aerojet manufactures counterweights from the material, which can be fabricated in smaller sizes than counterweights made with other metals in light of the density of the tungsten heavy alloys.
The alloys and other refractory metals Aerojet works with are like ceramics in that they do not melt, but are compacted from powder into shapes and sintered to full density, after which they are machined and finished. Scrap is generated as a result of compaction, sawing of large blocks and other processes.
STILL RISING |
The aerospace and defense industry remains one of the healthier sectors in the global economy. Investments play a major role in the industry. Combined investments in new product and technology development and R&D activities are higher than in other sectors, according to Global Industry Analysts Inc. (GIA), San Jose, Calif. A news release from the organization notes, "Strong R&D activities are expected to transform the worldwide aerospace and defense industry through the introduction of new, advanced aircraft." The possible roll-outs that could keep machine shops (and scrap recyclers) busy include "Unmanned air cargo carriers, supersonic military and civil aircraft, hypersonic/transatmospheric vehicles, eco-friendly intercity aircraft based on fuel cells, solar powered UAV (unmanned aerial vehicle), and unmanned passenger aircraft are some of the major developments that are expected to revolutionize military, commercial and cargo aerospace industry," according to GIA. Fuel cells are expected to power a wide range of military and civilian aircraft around the world. — Brian Taylor |
DOWN TO SIZE
Aerojet has experimented with techniques to reclaim tungsten heavy alloys scrap, including using a hammer mill and manually downsizing pieces. None of the methods was efficient or produced consistently sized particles. A hammer mill’s crushing and pulverizing action isn’t effective with a material of this density and generates dust. With manual reclaim, "labor costs were prohibitive and the results uneven," says Tim Brent, project engineer. Aerojet, consequently, wound up selling the scrap to dealers.
"If we can reuse the material, it’s worth two to three times more to us than selling it as scrap," says Brent. "But we couldn’t reuse the material without an effective means of size reduction."
After testing the performance of several size-reduction machines, comparing particle sizes, consistency and economy, Aerojet decided on an SCC 15 Screen Classifying Cutter from Munson Machinery Co. Inc., Utica, N.Y. Aerojet’s engineers were aware that the machine had a successful record in similar applications. "The design is simple and stands up to the tungsten heavy alloys," says Brent.
The cutter is engineered to downsize hard materials like tungsten heavy alloys into controlled particle sizes with few fines and no heat buildup. Key to its efficiency, according to Munson, is a helical rotor with dozens of tungsten-carbide-tipped cutter heads attached to an array of interconnected parallelograms that creates a steady and even cutting action against a pair of bed knives with each turn of the rotor, yielding particle uniformity. Most cutters and granulators, by contrast, have rotors with a smaller number of angled blades that deliver scissors-like cuts. The helical rotor efficiently moves material to take full advantage of the screen area, preventing "hot-spotting."
Munson says the rotor design generates six times greater force per inch with each cut than conventional knife-type cutters of equivalent horsepower, contributing to uniform size reduction and reduced energy use.
The cutter has a 10.5-inch (26.7-centimeter) wide helical rotor with 30 knife holders, each with two chisel-shaped, tungsten-carbide-tipped cutting heads, for a total of 60 cutting tips that maintain sharpness longer than tips made of conventional tool steel, thus reducing maintenance and downtime, according to the manufacturer. The teeth slide onto each machined holder and screw into place, speeding changeover. The two proprietary hardened tool-steel bed knives are reversible, meaning that when one edge wears down, the other edge can be used. When both edges of a knife become dull, they can be resharpened.
Aerojet’s cutter has a 3-inch-by-11-inch (7.6-centimenter-by-28-centimeter) throat opening and a hopper vent that draws dust away from the work area. The average rotor speed is 2,600 rpm, which can be changed by installing different size sheaves or by using a variable speed drive.
Brent says, "After a year in operation, the cutter has not required any significant maintenance."
UP TO THE JOB
"We manually batch-feed about 100 pounds (45.4 kilograms) of scrap through the cutter per hour, although the machine can do much more than that, and remove it by hand," Brent says. Actually, the cutter "sees surges of several pounds over a matter of seconds," he notes, as feeding is intermittent. The downsized material occasionally requires fine-milling, "but in some applications we can go directly from the cutter to the compaction process," Brent adds.
Aerojet specified an abrasion-resistant interior and a special stand to accommodate containers used in moving scrap to the process machines, which Munson Machinery accommodated.
Brent says Aerojet currently does not have plans for more cutters, but if increased capacity is required, the company will add options that automate cleaning, which is currently a manual affair. "Downsizing different grades of tungsten heavy alloys raises the risk of batch contamination if the interior isn’t properly cleaned," he notes. "The cutter is easy to clean compared to other machines, but still requires labor to take off the panels and get inside."
This text was submitted on behalf of Munson Machinery, Utica, N.Y. The company can be contacted at info@munsonmachinery.com.
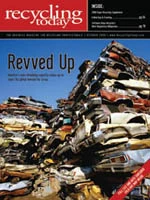
Explore the October 2008 Issue
Check out more from this issue and find your next story to read.
Latest from Recycling Today
- Agilyx says Styrenyx technology reduces carbon footprint in styrene production
- SABIC’s Trucircle PE used for greenhouse roofing
- Hydro to add wire rod casthouse in Norway
- Hindalco to invest in copper, aluminum business in India
- Recycled steel price crosses $500 per ton threshold
- Smithers report looks at PCR plastic’s near-term prospects
- Plastics association quantifies US-EU trade dispute impacts
- Nucor expects slimmer profits in early 2025