
Owners of computers and smartphones have been struggling to understand and sign off on just how much those devices get to know about them. The same dilemma increasingly faces owners of heavy equipment, such as material handling machines.
At the 2020 ConExpo-Con/Agg event, several mobile equipment makers portrayed the increasing sophistication of hardware and software included in their new machinery. The circuit boards and sensors are collecting data for many reasons, including maintenance tracking and performance monitoring.
It’s no surprise that technology is playing a larger role in any aspect of life. For recycling companies that own and operate heavy equipment, the surprises might lie in how that technology changes the way equipment is operated in the future.
Working hard and smart
Many recyclers show a preference for using customized scrap handling machinery built by manufacturers that design and specify custom handlers to load and unload scrap. However, plenty of material handlers remain on the job that were built in the same facilities and on the same platforms as excavators and handlers used in construction, mining and port applications. Even this century’s customized machines have their roots in these industries.
The largest global producers of excavators and material handlers, therefore, target much of their research and development on these larger sectors, including the use of automation and data collection.
At ConExpo, which took place in Las Vegas in March, Chicago-based Komatsu America Corp. offered a presentation on its Smart Construction services. CEO Rodney Schrader said Komatsu’s efforts to gather data via its machinery began in 2002. It has some 6,000 machines worldwide with telematics capabilities.
Komatsu has been developing services tied to its Smart Construction efforts since 2015. Schrader said every site preparation and construction job can be data-driven to “optimize decisions.”
Komatsu services include the use of drones with imaging capabilities to help map construction sites (and presumably large demolition sites) in advance of major work commencing. That data can now go from being gathered by a drone to online and smartphone access in a matter of hours, Schrader said.
One of Komatsu’s Smart Construction technology partners is South Carolina-based Moovila. That firm, in a news release issued during ConExpo, says its data tracking abilities can help offer “real-time cost analysis of any construction project, including change orders, to help retain profit margins and avoid disputes.”
“Komatsu has spearheaded major advancements in the construction industry, [and] as part of this commitment to innovation, Komatsu enlisted Moovila to help advance Komatsu’s Smart digital job site capabilities,” says Mike Psenka, president and CEO of Moovila.
Psenka says the company’s job site service “bridges process automation, project management best practices and third-party integrations to keep construction jobs on track.”
Data gathered and analyzed can help with prioritizing workflows and updating status in real-time while also working to ensure accountability on the part of stakeholders, according to the firm.
“Together, Komatsu and Moovila are transforming the way construction job sites operate, keeping everyone and everything connected while improving project execution and effectiveness,” Psenka says.
Whether such data tracking practices will make it to, say, auto shredding yards—and how long it might take to do so—is unclear. Commonly, however, equipment features introduced to the construction sector eventually make their way into other heavy equipment-dependent fields.
Mining more than minerals
Also at ConExpo 2020, Deerfield, Illinois-based Caterpillar Inc. provided updates on automation and data collection services it is researching and introducing. These services currently are configured with construction and mining sites in mind but also could spread to recycling facilities.
Three Caterpillar executives presented on how that firm says it is moving forward on equipment connectivity and autonomy. Caterpillar has “some 1 million connected assets” in place globally, said Bob De Lange, Caterpillar group president of services, distribution and digital.
At ConExpo, Caterpillar displayed several new or recently introduced technologies, including Cat Productivity, which it calls a web-based productivity management tool. Also on display was an expanded remote-control Cat Command offering designed to allow an operator to control multiple pieces of equipment from a single workstation.
De Lange told ConExpo attendees Caterpillar has 30 years of autonomy experience and has long had programmed or remote-controlled dump trucks on the job at mining sites. He said bringing that degree of autonomy to a construction or demolition site (or to a scrap yard or the waste and recycling industry more broadly) will not be easy, but it is currently testing autonomous equipment in such applications at its proving grounds in Illinois and in other parts of the world and in a pilot project it is doing with Waste Management in Denver.
Ramin Younessi, Caterpillar group president for construction industries, said he is seeing “strong interest” in autonomy from many of his customers in that segment as they continue to find skilled laborers in short supply.
Caterpillar recently released Cat Remote Services, including Remote Flash and Remote Troubleshoot, as another product featuring autonomy or remote-control capabilities. Other ConExpo displays focused on the Cat app for smartphones, VisionLink for fleet management and an augmented reality experience “to learn about getting a second life out of machines with Cat Certified Rebuild.”
Sponsored Content
Redefining Wire Processing Standards
In nonferrous wire and cable processing, SWEED balances proven performance with ongoing innovation. From standard systems to tailored solutions, we focus on efficient recovery and practical design. By continually refining our equipment and introducing new technology, we quietly shape the industry—one advancement at a time.
Sponsored Content
Redefining Wire Processing Standards
In nonferrous wire and cable processing, SWEED balances proven performance with ongoing innovation. From standard systems to tailored solutions, we focus on efficient recovery and practical design. By continually refining our equipment and introducing new technology, we quietly shape the industry—one advancement at a time.
Sponsored Content
Redefining Wire Processing Standards
In nonferrous wire and cable processing, SWEED balances proven performance with ongoing innovation. From standard systems to tailored solutions, we focus on efficient recovery and practical design. By continually refining our equipment and introducing new technology, we quietly shape the industry—one advancement at a time.
Sponsored Content
Redefining Wire Processing Standards
In nonferrous wire and cable processing, SWEED balances proven performance with ongoing innovation. From standard systems to tailored solutions, we focus on efficient recovery and practical design. By continually refining our equipment and introducing new technology, we quietly shape the industry—one advancement at a time.
Sponsored Content
Redefining Wire Processing Standards
In nonferrous wire and cable processing, SWEED balances proven performance with ongoing innovation. From standard systems to tailored solutions, we focus on efficient recovery and practical design. By continually refining our equipment and introducing new technology, we quietly shape the industry—one advancement at a time.
Sponsored Content
Redefining Wire Processing Standards
In nonferrous wire and cable processing, SWEED balances proven performance with ongoing innovation. From standard systems to tailored solutions, we focus on efficient recovery and practical design. By continually refining our equipment and introducing new technology, we quietly shape the industry—one advancement at a time.
When and if
Scrap processors and the custom scrap handler equipment makers that supply them are discussing how, when and if such technology will make it to the scrap yard. Not all yard managers express enthusiasm for excess automation or computerization, often adopting an attitude that such components and systems provide additional and potentially delicate circuit boards and wiring that could merit ongoing servicing.
But for yard managers who do want better data collection options, the Fuchs Terex brand of scrap handlers offers its Telematics system, standard on all machines, which it says “provides automated all-in-one machine management for customers to further optimize machine efficiency, control operating costs and improve uptime by alerting key individuals of upcoming service intervals and potential machine issues.”
Other scrap handler manufacturers are by no means standing still when it comes to technology. Some, including Sennebogen, are focusing on electric motor options, which could proliferate in the new decade.
Sennebogen also has been putting its R&D emphasis on safety features, such as its elevated cab technology and LED headlights.
The Liebherr USA Co. subsidiary of that Europe-based scrap handler producer says its recent $60 million investment in a new headquarters complex in Virginia has been designed in part to focus on technology upgrades.
The company, which produces a variety of heavy equipment for markets beyond the scrap recycling sector, says its new complex has been designed with “technology-laden training rooms with video conferencing capabilities and flexible workspaces for different types of working.”
Torben Reher, managing director of Liebherr USA, says, “Apart from investing in research and design for cutting-edge technology, we have a long-term focus with respect to our business and the relationships with our customers.”
Among Liebherr’s technological points of emphasis has been its patented ERC (energy recovery) system, designed to offer maximum handling capacity “while at the same time lowering overall fuel consumption,” according to the company.
As in every other facet life, technology in material handling machinery is attracting investments and attention and is likely to move forward rapidly for the foreseeable future.
Get curated news on YOUR industry.
Enter your email to receive our newsletters.
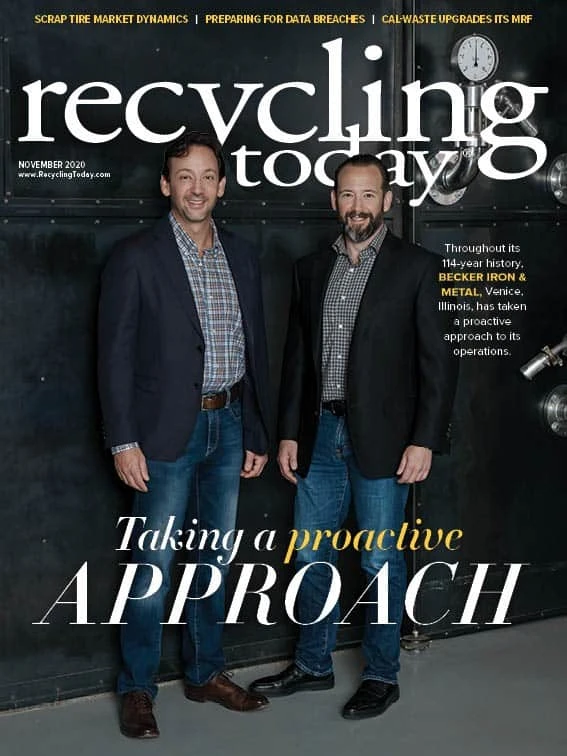
Explore the November 2020 Issue
Check out more from this issue and find your next story to read.
Latest from Recycling Today
- ReMA board to consider changes to residential dual-, single-stream MRF specifications
- Trump’s ‘liberation day’ results in retaliatory tariffs
- Commentary: Waste, CPG industries must lean into data to make sustainable packaging a reality
- DPI acquires Concept Plastics Co.
- Stadler develops second Republic Services Polymer Center
- Japanese scrap can feed its EAF sector, study finds
- IRG cancels plans for Pennsylvania PRF
- WIH Resource Group celebrates 20th anniversary