The Rosen family has been recycling materials in southern Michigan for more than 80 years, getting its start in the competitive paper recycling and scrap metals industries.
The recycling industry has changed greatly in the course of eight decades, and the Rosen family business, now known as Great Lakes Recycling (GLR), has changed along with it in terms of processing technology and the types of materials recycled.
Great Lakes Recycling At a Glance: Principals: Ilene Bischer, Steve Rosen, Ben Rosen, Sandy Rosen and John Hawthorne Locations: No. of Employees: Equipment: Services Provided:
But along with the changes there have been some important constants in the equation. The most important one has been the way the company and its principals interact with customers and employees, putting an emphasis on showing respect and an ability to see things from the other person’s point of view.
FAMILY MATTERS
The roots of GLR trace back to 1927, when Henry Rosen started H. Rosen and Sons as a small metal, paper and rag recycling business in Detroit.
Henry guided the business through the Great Depression and was able to welcome his sons into the business in the 1940s. Ben joined the business in 1941, and his brother Burt began full-time in 1947.
"I joined GLR after high school," recalls Ben. "With my dad and with my late brother Burt, we were able to slowly grow the company. Burt handled the paper side of the business, while I handled the metal side of the business."
Not long after Ben and Burt joined the business, the company out-grew its original location in Detroit. "As we grew, we needed more room and moved from Detroit to Roseville, Mich., in 1951," says Ben. Initially, the company moved to a two-acre parcel of land in that Detroit suburb.
Ben looks back fondly on the years when he and Burt helped the business survive and thrive so it could become what it is today. "It was a great relationship, and I miss Burt to this day," he comments. "I only wish that he was here to see how the company has grown and prospered."
During the 1970s and 1980s, the third generation of Rosens joined the business in the form of Ben’s daughter Ilene Bischer and his sons Sandy and Steve Rosen.
Ilene began working for GLR in 1982 and has been a key part of the management team while also attending university classes and starting a family with four children. "Now that my four children are almost grown, I am able to be more involved with the business," she notes. "I am currently handling the IT and assisting in the accounting department."
When he was young, Sandy was not convinced he wanted to enter the family business, but his path took him almost directly there. "It was my father’s career, but I never expected it to be mine," he says. "I worked after school, weekends and summers through high school and college. I decided to take a break from school and was offered a job painting in the plant [and] I never left. When I graduated with a degree in computer science, I passed on job hunting in that field in favor of this. Business was much more fun, we grew organically and through acquisition."
While he has been engaged in the business non-stop for many years, Sandy says it has not been a static journey. "I went back to Michigan State and earned my MBA in 1998 to fill a bare spot on the wall. Passion for the environment came later. Observing all the waste in society firsthand has had a tremendous impact on me."
Steve Rosen worked part-time for GLR during his high school years, but attended both college and medical school and practiced medicine from 1977 to 2006. Even during those years, he stayed involved in the family business. "I started the industrial foam [recycling] division in the late 1990s," he remarks. "I grew up in the recycling business and always thought I might be part of the business after finishing my medical career. I continue to teach at North Oakland Medical Center and keep up my medical license. Although not life and death, the recycling industry has always been interesting and challenging in spite of being so different from medicine," he adds.
"My children began to work for the company in the 1980s, and it has truly been wonderful working side by side with them to grow our small company to be one that employs over 250 people," says Ben. "I am 85 years old now but I still come in six days a week to keep an eye on things and offer my advice as it is needed."
The advice must be sound, as additional company growth has allowed GLR to purchase adjacent and nearby parcels of land in Roseville to form a total of 12 acres.
In Roseville, GLR operates some 125,000 square feet of indoor recycling space. One building contains the company’s scrap metal recycling operations, while the other was initially set up as a paperstock plant handling commercially and industrially generated fiber.
That facility, however, was converted into Michigan’s first single-stream material recovery facility (MRF) in 1999, one step in a series of moves that have helped GLR down its path toward corporate growth and diversification.
The company has continued to grow this decade not only in Roseville but also in new locations.
NEW BRANCHES
In a light industrial park several interstate highway exits south of Detroit, GLR has built a single-stream MRF designed not only to handle large amounts of material efficiently, but also to serve as a showpiece where residents of surrounding communities can see what happens after they place something in a recycling bin.
The company’s second MRF in the Detroit area is intended to provide more complete geographic processing coverage to metro Detroit, although material also is being brought in from beyond the Detroit market. "The recycling facility will process recyclables from the entire region, including from Michigan, Ohio, Indiana and Canada," notes Sandy.
As noteworthy as the Huron Township facility is, it is only one of three new projects that is being undertaken by GLR this year.
The company, which has been offering electronics recycling services throughout this decade, will soon be doing so on a larger basis thanks to a new joint venture with Global Electric Electronics Processing (GEEP).
A joint venture GEEP Michigan plant includes a shredding system with thorough processing capabilities.
And at the other end of the Great Lakes region, GLR is involved with the construction of the company’s new MRF near Buffalo, N.Y. GLR, which already operates a facility in North Tonawanda, N.Y., is a joint venture partner with Model City, N.Y.-based Modern Corp. in building a single-stream facility to be known as Buffalo Recycling.
THE HUMAN FACTOR
The Rosens and other decision-makers at GLR have needed to put considerable thought into where and when to add plants and equipment, but even reaching such points of decision would not have been possible if people didn’t come first, they say.
"People like to deal with us," says Hawthorne, who joined the company in 2004, several years after he had met Sandy when they were fellow students in the MBA program at Michigan State University.
Regarding customer relationships, Hawthorne says, "We have a reputation for making sure each and every transaction is fair and equitable for both parties. We have grown steadily over time so we have been able to handle our growth in such a way that it keeps our customer focus strong and our relationships with our customers strong. We offer a lot of transparency to the people we do business with and take the time to put ourselves in their shoes."
Even in the course of what can be a very hectic work week, Hawthorne says thanking customers and considering their viewpoint has to be kept in mind. "We show a lot of appreciation to the people who choose to do business with us and do everything in our power to make it a good experience for them."
Providing good customer service is likelier when employees enjoy their work, a realization that has led GLR to keep a sharp eye on its workplace culture and environment. "We take our mission statement and our culture statement very seriously, unlike those that jot something down and hang it on the wall. Hundreds of hours of our people’s time went into the painstaking process of defining the mission and culture, and we believe it keeps us on the right track," says Hawthorne.
"We probably treat our staff better than the average recycler," he notes. "We have a standard benefit package that everyone from the owner to the newest hire receives. We take safety very seriously; there’s no amount of profit that would make an injury to someone worthwhile. In terms of unpleasant jobs, no one is expected to do anything that the executive team won’t do and, if there’s any doubt, we go out in the plant and do it to make sure."
Hawthorne, the Rosen family members and other managers stay in touch with frontline work though the company’s "day-in-the-life" program, which entails sales, administrative and executive team members working general labor shifts on the plant floor at various posts several times per year. "There is no other way to really know what it is like," says Hawthorne.
The program provides numerous other insights as well, according to Sandy and Ilene. "We can’t be out on the plant floor all the time, and the chances of seeing everything you need to see in a walk-through are limited," says Sandy. "But when you spend a couple of hours cutting copper or helping receive incoming scrap paper loads, you see a lot more. By being out on the dock, if I see a trailer that looks like a bomb went off inside, it makes me realize that the sales folks have to be told about that so they can talk to the customer."
In the "day-in-the-life situations," a plant employee who may otherwise have kept information to himself will often speak more freely after working side-by-side with Sandy, John or Ilene. "They feel like they don’t really have the power to make things happen," says Sandy. "There are employees who can be intimidated by us, but not when we’re standing next to them near the conveyor or sorting through loads of cardboard that come in. They see us as people and not just figureheads."
Ilene agrees, adding, "They become comfortable approaching us and telling us something that another employer may not want to hear. Ultimately, that’s good for our business."
Combining what is good for employees and customers with what is good for business will ideally remain the way GLR approaches its business. "We cannot forget we are in the service business," says Hawthorne. "We are not in the manufacturing business. The conveyors, balers and forklifts are the manufacturing base that allows us to provide the services to our customers. The people that supply us have needs and, as long as we meet or exceed those needs, we will be OK."
If its recent new facility projects and electronics joint venture are any indication, GLR should be more than just OK as it prepares to remain a vital part of the recycling industry in the Great Lakes region it calls home.
The author is editor in chief of Recycling Today and can be contacted at btaylor@gie.net.
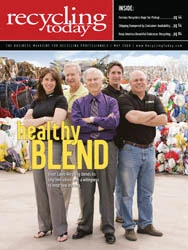
Explore the May 2009 Issue
Check out more from this issue and find your next story to read.
Latest from Recycling Today
- Nucor receives West Virginia funding assist
- Ferrous market ends 2024 in familiar rut
- Aqua Metals secures $1.5M loan, reports operational strides
- AF&PA urges veto of NY bill
- Aluminum Association includes recycling among 2025 policy priorities
- AISI applauds waterways spending bill
- Lux Research questions hydrogen’s transportation role
- Sonoco selling thermoformed, flexible packaging business to Toppan for $1.8B