
Sterilization wrap, gowns, irrigation bottles, IV bags, basins, pitchers, trays and rigid and flexible packaging materials are, for the most part, used once and thrown away. According to data as reported in a 2010 article published by Slate, available at http://slate.me/2vURBWL, U.S. hospitals generate 6 million tons of waste per year, with plastics accounting for up to one-quarter of that total. Most of that plastic ends up in landfills or incinerators despite that 85 percent is nonhazardous and free from patient contact and contamination.
Understanding the opportunity
Given
Recyclers also stand to reap multiple benefits from recycling health care plastics. In most markets around the country, few (if any) recyclers are working to extract these rich, untapped materials from clinical settings. Because disposal of these materials represents a significant cost to hospitals, a solution that reduces that cost while offering an environmentally responsible alternative to landfill or incineration represents a very desirable alternative to current practices, and hospitals are clamoring for recyclers to partner with.
Health care plastics often are made of high-quality materials, a requirement for use in medical applications, and are designed for extremely specific uses. This results in very little variance in key characteristics, such as melt flow,
Connecting supply and demand not only helps create a closed-loop system (make, use, return) that achieves better environmental outcomes, but it also makes good business sense.
Busting the myths around health care plastics
To help recyclers embrace the possibilities that plastics from health care settings hold, we examine three popular myths that surround this material.
Myth No. 1: the ick factor. A common misconception about health care plastics is that all of it is inherently dangerous as a result of contact with biohazardous materials, medications and other unsafe materials. In reality, this stream is cleaner than municipal material—after their single uses, most health care plastics are disposed of before the patient even enters the room.
Years ago,
“A strong partnership and open communication between hospitals and recyclers are key,” says Dan Constant, president of Sustainable Solutions LLC, Gainesville, Georgia, and a consultant to Halyard Health’s Blue Renew program. “Understanding the importance of training and who is accountable for each step in the process greatly diminishes potential contamination issues,” he says.
Myth No. 2: The quantity isn’t there. While a single hospital may not generate a profitable volume of material for a recycler, many hospitals are part of larger health care systems that are interested in working together to collect sufficient volumes to make recycling economically viable. Recyclers should look to accumulate material across multiple hospitals, whether by health care system or geography, to achieve desired quantities. Studies such as the one conducted at Stanford Healthcare (See www.hprc.org/stanford-pilot-study.) have demonstrated that the quantity is there—it’s the collection that can be the challenge. However, recyclers and other service providers (document destruction, paper recyclers, linen companies and sheltered workforce programs, such as those offered by Goodwill (See http://bit.ly/2kI7wiV for a case study.), already are transporting materials to and from hospitals and have logistics in place to aggregate the volume needed for a health care plastics recycling program to make good business sense. Working with these vendors to set up backhaul systems can be key to scaling a collection program.
“Health care plastics are the last large, untapped material stream with great potential for recyclers,
Myth No. 3: There is no end market. Health care plastics lend themselves to numerous markets. High-quality polypropylene (PP) always is in demand with compounders given its relatively high value and universal applications for blending and pelletizing. PP sterilization wrap increasingly is made into many finished products, including some that are sold back into hospitals.
“Through Halyard Health’s Blue Renew program, we have created BlueCON Resin, a recycled polypropylene made of 80 percent operating room waste,” says Constant. “With this new resin, we make environmentally preferred products that hospitals use every day, including garbage cans,
Rigid plastics from the health care sector, such as pitchers, trays and packaging materials, can be processed with other
Continuing the conversation
To continue the discussion around the potential of health care plastics, the Healthcare Plastics Recycling Council (HPRC), in conjunction with the Washington-based Plastics Industry Association, is hosting a workshop at the 2017 Paper & Plastics Recycling Conference Wednesday, Oct. 11.
This workshop will help recyclers better understand material types, quality
HPRC is a private technical coalition of industry peers across the health care, recycling and waste management industries. Members include Baxter, BD, Cardinal Health, DuPont, Eastman Chemical Co., Johnson & Johnson, Medtronic, Nelipak Healthcare Packaging and Ravago Recycling Group.
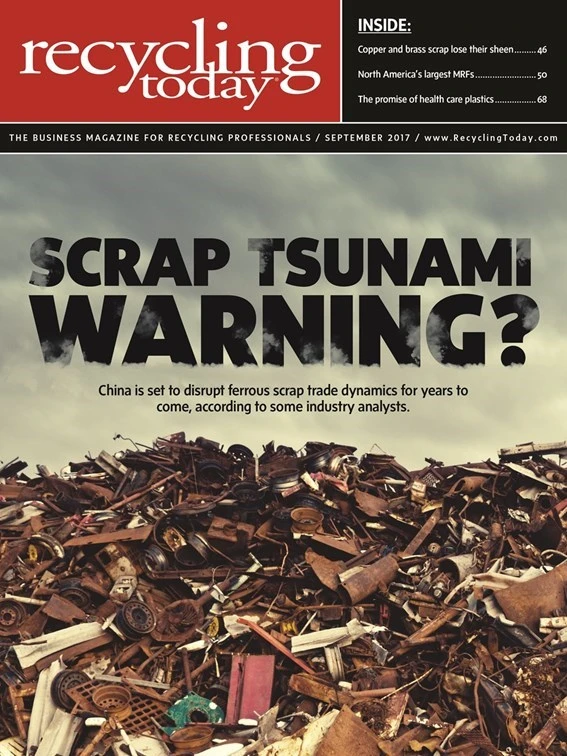
Explore the September 2017 Issue
Check out more from this issue and find your next story to read.
Latest from Recycling Today
- Aurubis CEO says its metals play vital role
- Steelmakers await impact of tariff policy
- Radius loses money, says merger on track
- Electrostatic technology vies for role in ASR sorting
- ReMA board to consider changes to residential dual-, single-stream MRF specifications
- Trump’s ‘liberation day’ results in retaliatory tariffs
- Commentary: Waste, CPG industries must lean into data to make sustainable packaging a reality
- DPI acquires Concept Plastics Co.