Editor’s Note: The following feature is excerpted from the Occupational Safety and Health Administration (OSHA) publication titled Guidance for the Identification and Control of Safety and Health Hazards in Metal Scrap Recycling. The full document can be downloaded at www.osha.gov/Publications/OSHA3348-metal-scrap-recycling.pdf.
Metal scrap recycling is a large and complex industry. The variety of metals involved and the wide range of sources of metal scrap require many processing techniques. These processing techniques pose a range of safety and health hazards to employees in the industry. This section discusses a selection of those processes, the types of hazards these processes may pose to employees and measures employers and operators can implement to control or eliminate these hazards. This document does not go into detail on every process or every hazard associated with every process at a scrap yard, but rather it discusses the most common processes employed at scrap yards and provides examples of hazards related to those processes.
Recycling is a multi-step process, starting with collection and transport of raw scrap, pretreatment, melting, refining, forming and finishing. The recycling processes discussed in this document fall into these basic categories:
• Loading and unloading;
• Breaking and separating;
• Gas torch cutting;
• Non-gas torch and other cutting;
• Baling, compacting and shredding;
• Melting and baking in furnaces and ovens; and
• Applying chemical processes to recycle metals.
Each of these categories is an individual component of the recycling process and may pose a wide range of safety hazards that are common to many industrial and material handling processes. Such hazards may include flying pieces of material, exposed moving parts, fire hazards and noise hazards.
Hazardous chemical exposures to employees are most likely to result from hot processes that produce fumes (such as torching and welding or melting in furnaces) or from processes that produce dust (such as breaking, shredding and cutting). Each of these processes is discussed in detail on the following pages.
LOADING AND UNLOADING
The first step in any metal scrap recycling operation is getting the metal scrap to the recycling operation and collecting or sorting materials to be processed in groups. This may involve light or heavy trucks, stationary or mobile cranes, conveyor belts and other large and potentially hazardous equipment. Working with this equipment poses hazards typical for material handling equipment.
Employers must ensure employees use the appropriate combination of personal protective equipment (PPE), such as hard hats, sturdy boots, gloves, thick clothing and respirators (if the operation generates hazardous dust), to be adequately protected from safety and health hazards.
OSHA’s Personal Protective Equipment standards (29 CFR 1910 Subpart I) establish requirements for employers to evaluate the workplace and identify PPE needs based on actual workplace hazards (29 CFR 1910.132). These standards also establish criteria for proper selection and use of specific types of PPE, such as foot, eye or head protection.
Forklift and crane operators must be properly trained in the use of such equipment. Operators must conduct pre- or post-shift vehicle inspections depending on vehicle use. Employers must consider equipping vehicles with guarding to protect any vulnerable brake lines from incidental damage during operation (NIOSH FACE; 29 CFR 1910.178).
BREAKING AND SEPARATING PROCESSES
Size-reduction of metal scrap is a necessary component of some operations. Basic metal breaking processes often involve heavy manual labor to break up large or complex assemblies of scrap metal or to cut or break the pieces into sizes that can be fed into a furnace. Employees involved in activities of this type may be exposed to metal fumes, smoke, hot environments and hot material when working near furnaces and may come in contact with metals that present hazards through both skin contact and inhalation.
Some recycling industries use drop-ball breaking (or "tupping") to break apart the largest solid pieces of scrap metal or to initiate breaking up large assemblies. This process may create flying object hazards as the material breaks apart from the impact of the ball. Employers must ensure that employees are protected from these hazards by either performing the task remotely; placing a barrier or protective shield around the task; or using PPE, such as face and body protection.
Breaking may also create a noise hazard, requiring the employer to implement feasible engineering or administrative controls. If these controls do not sufficiently reduce the noise hazard, employers must provide appropriate hearing protection, such as earplugs, canal plugs, earmuffs or other protective devices as required by OSHA’s Occupational Noise Exposure standard, 29 CFR 1910.95.
Sorting of scrap is now commonly done using automated processes, though some metals must still be sorted by hand. When sorting metal scrap by hand, employees must wear PPE, such as gloves, if they could encounter any metal or other substance that could produce adverse health effects when in contact with skin.
Employees also must be aware of the proper first aid, medical and reporting procedures if they receive a cut or scrape.
Once an employee has started feeding material into a furnace, there is a risk of hazardous fumes from certain metals. Where exposures exceed OSHA permissible exposure limits (PELs), employers are required to implement feasible engineering controls (e.g., furnace feeding operations can be set up with local exhaust, which can circulate and vent the air near the furnaces to remove toxic fumes from the workplace). If the exposures still exceed the PELs, employees will need to wear respiratory protection to prevent inhalation of toxic fumes and dusts.
BALING, COMPACTING AND SHREDDING
Scrap metal is often compacted using balers to promote efficient melting by allowing more metal into a furnace than would be possible for a random assortment of sheeting and other scrap objects. Balers use powerful hydraulic systems to compact scrap metal. Moving parts of balers must be shielded to prevent body parts from coming in contact with machines. Car flatteners work on many of the same principles as balers and present similar safety hazards.
Balers are typically automated machines. This allows operators to stay a safe distance from the machinery, however, employees must still exercise caution when feeding raw material into a baler using a hopper or conveyor belt.
Some balers and shredders have sensors or heat detectors installed that react to human body heat and automatically stop all machine operations. For others, employees may wear magnetic or other devices on their belts that are linked to a safety interlock system.
Employees must be trained to understand the functioning and safety procedures of their equipment and must follow procedures for adequate control of hazardous energy, particularly when performing maintenance procedures on equipment (NIOSH FACE; 29 CFR 1910.147).
For all equipment where pieces of scrap metal are fed into a machine directly, or using a hopper or even via conveyor belt, employees must be trained in the proper use of the equipment. In addition, appropriate guards must be installed to prevent employees from coming into contact with hazardous moving parts of the machinery. This applies to the alligator and guillotine shears discussed above and also to other similar machines, such as rotary shears and rotary shredders. For such equipment, employees need to stay a safe distance away from working machinery and take adequate safety precautions to minimize risks. Employers must install shields to block stray pieces of metal scrap from flying out from these machines, and employees must be trained to know what materials can or cannot be fed into the machine to prevent malfunctioning.
In addition to the physical hazards associated with baling, compacting and shredding, these processes also produce significant amounts of dusts. Dust, if not controlled, can present explosion and inhalation hazards. Some ways to control these hazards include:
• Installing proper air cleaning systems on shredding machines;
• Installing explosion sensors to inject water to suppress explosions;
• Operating machinery at lower speeds to reduce dust generation;
• Introducing an inert gas to rotary shears to reduce the risk of explosion;
• Providing supplemental ventilation where needed and perhaps respiratory
protection to protect employees from exposure to hazardous dusts; and
• Using wet or semi-wet shredding processes.
Some scrap materials, such as scrap vehicles or refrigerators, may contain fuels or other materials that introduce additional hazards to the process. Operators must be sure to remove these materials before introducing the scrap to process machinery. For example, gasoline must be removed from the gas tank of scrap automobiles before compacting or shredding the automobile. In addition, chlorofluorocarbons (CFCs) and ammonia must be removed from air conditioning systems to prevent employee exposure to these irritants and to prevent the release of these gases to the atmosphere. Removal of CFCs also applies to the shredding of refrigerators.
Many of the processes described above use large amounts of electricity to operate. Employees must be aware of the potential hazards of working in high-voltage environments and should take the appropriate precautions. Additionally, all equipment power systems must be covered with non-conducting covers that require a tool to remove.
High-voltage areas must be protected to prevent access to unauthorized individuals. Employers must create a lockout/tagout program and train their employees on proper implementation of these procedures.
Get curated news on YOUR industry.
Enter your email to receive our newsletters.
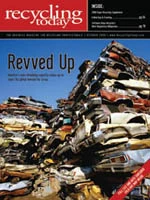
Explore the October 2008 Issue
Check out more from this issue and find your next story to read.
Latest from Recycling Today
- Nucor expects slimmer profits in early 2025
- CP Group announces new senior vice president
- APR publishes Design Guide in French
- AmSty recorded first sales of PolyRenew Styrene in 2024
- PRE says EU’s plastic recycling industry at a breaking point
- Call2Recycle Canada, Staples Professional expand partnership
- Circular Services breaks ground on north Texas MRF
- Tariff uncertainty results in choppy nonferrous scrap flows