Unfortunately, that “cruise control” status is not a reality. Closer looks at the quality of any program are imperative, and education programs may need to be updated to address emerging home owner recycling questions.
SEEING IT FIRST HAND
As one of the largest processors in the Midwest of residentially collected curbside recyclables, Resource Management, Naperville, Ill., is able to see first hand what people are putting into recycling bins. Resource Management receives materials from a variety of curbside programs in Illinois, Indiana, Iowa, Michigan, Missouri and Wisconsin.
Resource Management was founded by Calvin Tigchelaar in 1991, who continues to be the sole owner. The company’s business strategy is focused on efficient processing and marketing of recyclable materials and has won recognition for its quality efforts. (See the September, 1998 issue of Recycling Today, “Benchmark Your UBC Operation Against The Best”).
The company’s personnel have some interesting observations concerning the evolution of residential curbside collection programs. The computer programming industry often uses the phrase “garbage in equals garbage out.” For the recycling industry, the paraphrased version might be, “the more garbage that goes in, the more it costs to get out.” As it turns out, misinformation and changes in collection methods continue to be a challenge in the recycling industry. The good news is that simple adjustments to collection methods coupled with ongoing consumer education can increase the value of recyclable materials.
CURBSIDE COLLECTION: A LOOK BACK
A look back at the evolution of curbside collection programs helps to illustrate the causes ofcontamination that some residential curbside recycling collection programs experience.
When curbside collection began, there were specific and limited items that could be collected. These items included:
Paper Fiber:
• Newspaper (including inserts)
• Cardboard (no waxed cardboard)
• Magazines
Containers:
• Glass Bottles and Jars - (clear, brown,
green)
No window glass, dinnerware or ceramics
• Aluminum Cans
• Steel Cans
• PET soda and water bottles (#1 clear
and green plastic resin)
• HDPE milk jugs (#2 clear plastic
resin)
• HDPE detergent containers (#2 col-
ored plastic resin)
All containers were to be emptied, rinsed clean and caps and lids removed.
Route trucks used for residential collection were built with separate compartments for each material and items were separated at the curb. Earlier versions of recycling route trucks did not have any compaction, mainly to avoid glass breakage. Some later versions included a compaction compartment for paper, and some added compaction compartments for plastics.
The curbside sort collection method allowed visual inspection of all items in the recycling bin. If consumers placed non-recyclable items in the bin, the driver would leave the non-recyclable materials at the curbside, usually with a note or sticker instructing the consumer that only designated items can be collected for recycling. When recyclable materials were delivered to a Materials Recovery Facility (MRF) they were typically received and stored in separate locations to prevent cross contamination of materials. These separated materials were then successfully marketed without contamination.
COMMINGLED COLLECTION
Advancements in MRF processing technologies made it possible for curbside recycling programs to commingle materials, allowing consumers to mix all paper fiber together in one recycling bin, and all containers together in another recycling bin.
Since materials could now be separated at the MRF, it was no longer necessary to sort the materials at the curb. Haulers could simply put all paper fiber into one compartment, and all containers into another compartment. These ‘two compartment vehicles’ vastly improved the productivity of route truck drivers by spending less time at each stop. Even with the advent of commingled collection, non-recyclable materials were still left at the curb.
Soon after commingled recycling collection was initiated, manufacturers offered recycling collection vehicles with the ability to provide varying degrees of compaction to fully compress the paper fiber and partially compress the commingled containers.
Compaction options were offered by manufacturers so haulers could achieve greater payloads, thereby allowing recycling collection vehicles to pick up from more households on a single route. Varying degrees of compaction were tried to see how far commingled containers could be compacted (say, to get the air out of the bulky plastic containers) without causing excessive glass breakage.
Over time, MRF operators began to see more broken glass in recycling trucks using compaction, but experienced MRF operators were able to adjust their operations to recover and recycle the mixed broken glass; however this caused a net decrease in the value of the recovered glass
There has been a learning curve with newer recycling collection vehicles to adjust compartment sizes so that the commingled container compartment and the paper fiber compartment are fully loaded when completing a collection route. The ideal situation is for both compartments to fill completely, and the prevention of one compartment filling up before the other. Overfilling of one compartment or inefficient splitting devices can potentially cause cross contamination between compartments, where paper gets into the commingled container compartment and vice-versa. Also, if latches between compartments are not secured or working properly, this has the potential of accidentally mixing all materials together when the truck tips the material at a MRF or transfer station. These types of mishaps typically result in additional processing charges to separate paper fiber and commingled containers from each other.
TRANSFERRING TRANSFER STATION METHODS
During the early development of residential recycling programs, there were many smaller sized MRFs spread out over a geographic region. It soon became apparent that it was more economical to transport recyclable materials over longer distances to larger sized MRFs rather than continue to operate the smaller MRFs.
To achieve lower transportation costs, hauling companies began using large transfer trailers to ship bulk quantities of recyclable materials over longer distances. Many hauling companies started using some of their transfer stations to store and load bulk quantities of recyclable materials into transfer trailers.
Some MRFs discovered that transfer trailer loads from some transfer stations were contaminated with garbage or cross contaminated (paper fiber and containers mixed together). It became apparent that transfer stations can be a source of contamination for materials unless there is adequate space available to separately receive and store recyclable materials. Retaining and dividing walls are typically needed at transfer stations to prevent cross contamination between commingled containers and paper fiber, as well as preventing trash from spilling over into the piles of recyclable materials.
ADDING TO THE MIX
In an effort to expand recycling and decrease solid waste disposal, many communities began increasing the materials included in a recycling program. Paper fiber recycling was expanded beyond newspaper and cardboard to include chipboard (cereal, cake and food mix boxes), carrier stock (soda and beer carrying cartons), office paper, junk mail, and other mixed papers. There are also numerous examples of product packaging and other consumer goods that were advertised and promoted by manufacturers as recyclable materials that were subsequently added to some curbside collection programs, including:
Six-Pack Plastic Beverage Container Carrier Rings - As a result of national coverage of birds and other animals discovered with plastic six pack rings around their necks, the plastic carrier manufacturing industry promoted recycling these rings and initiated a public education campaign not to litter. Some communities continue to include these in their residential recycling program; even though the quantity by weight or volume is minuscule and markets for this material are very limited.
Aseptic Packaging and Gable Top Containers - Juice boxes made from aseptic packaging and gable top containers such as milk and juice cartons were added to curbside collection programs basedon commitments from these product manufacturers that these containers could be successfully and economically marketed as recyclable materials. Many communities continue to include these materials in their curbside programs; however, markets for these materials also remain somewhat limited.
Food Grade Polystyrene - The polystyrene industry invested $85 million to build facilities to receive and recycle post consumer polystyrene. Schools and communities were actively marketed to and convinced by the polystyrene plastics industry to include polystyrene in their recycling programs.
The National Polystyrene Recycling Company (NPRC) was established by several polystyrene manufacturers to receive and recycle post-consumer polystyrene. When the polystyrene recycling program was initiated, NPRC would send a truck to a facility and pay $140 per ton of material. NPRC has since stopped picking up polystyrene from MRFs and started charging $300 per ton. NPRC was recently sold to Elm Packaging Co., who also charges $300 per ton to recycle the material. Other companies have also attempted to take and recycle polystyrene; however, the cost of many of these alternatives are also in excess of $300 per ton.
The Illinois Department of Commerce & Community Affairs, Region 5 of the U.S. EPA, and Illinois Recycling Association have recently advised that serious consideration be given to dropping food grade polystyrene from residential curbside recycling programs due to the limited markets and extreme negative value associated with the recycling of this material.
Packaging Grade Polystyrene - A recent forum was co-sponsored by the Illinois Department of Commerce & Community Affairs, Region 5 of the U.S. EPA and the Illinois Recycling Association. The forum concluded that packaging grade polystyrene collected in a residential curbside or drop-off program is not recyclable due to incompatible grades of polystyrene and contamination during the collection process. Consumers may take this material directly to a packaging grade polystyrene recycling plant. However, this material can not be included in residential collection programs.
Plastic Containers #3 through #7 - A few markets have developed for other types of post-consumer plastic containers. Many MRFs were able to take some of these additional materials, which can include:
• #3 PVC: health & beauty aid
products, household cleaners.
• #4 LDPE: margarine tubs, frozen
desert cups, six and 12 pack rings.
• #5 PP: yogurt cups, syrup and ketchup bottles.
• #6 PS: expanded polystyrene food plates and beverage cups.
• #7: plastic narrow neck containers.
This qualified list of plastics #3 through #7 was targeted as typical plastic containers from grocery stores (with the exception of food grade expanded polystyrene), and was not necessarily intended to encompass anything else. Many consumers have mistakenly assumed that any plastic product with these resin numbers can be placed in their curbside recycling bins.
Many plastic products have an identification number stamped or embossed on the bottom or side showing the type of plastic resin used to manufacture the product. Unfortunately, many container makers have adopted a triangular chasing arrow symbol that surrounds the plastic resin identification number. Since consumers have come to understand that triangular chasing arrows mean the material is recyclable or is made from recycled material, consumers have the mistaken belief that the plastic is recyclable. This is an unfortunate and misleading practice used by some companies within the plastic industry.
Plastic Film - Plastic film consists of plastic bags, stretch wrap or pliable plastic tarps and sheets. Most home owners have become generally aware that plastic bags have the potential to be recycled. This notion is reinforced by some grocery and department store chains that allow consumers to return the plastic bags at the point of purchase. These grocery and department store chains have successfully obtained commitments from their plastic bag suppliers to recycle these plastic bags as a condition for continued purchase of new plastic bags. This practice works because the plastic bags are all the same type and have not been contaminated.
Unfortunately, some home owners have the mistaken notion that grocery and department store plastic bags can also be placed in their curbside recycling bin.
Various consumer goods may be packaged in stretch wrap to protect the product during shipping and handling. Plastic stretch wrap, rolls, sheets and tarps should not be collected in curbside programs since this material becomes contaminated in the collection process and can not be effectively identified and recovered at a MRF. The materials can potentially be recycled at a commercial level for specific types and sufficient quantities of material that are available in a clean and non-contaminated environment (such as from manufacturing or warehouse facilities).
Blue Bag Programs - When using a ‘blue bag’ recycling collection method, it should be noted that there is a reduced value of the material compared to recyclable material collected from curbside bins. This reduced value is caused by the additional cost to open the bags at the MRF, the disposal cost of the bags, and higher incidences of contamination experienced with some bagged recycling collection programs.
If consumers put non-recyclable materials into a plastic bag, haulers are often unable to identify this contamination and it is not discovered until the bags are delivered to the recycling processing facility. This circumstance is less likely to occur in curbside bin programs because the collector has a better chance to see and reject contaminated material at the curb.
DEALING WITH CONTAMINATION AT THE MRF
To some degree there is always some level of contamination in materials collected from residential curbside recycling programs. While garbage is clearly unacceptable, other items will probably continue to find their way into recycling bins, such as a plastic toy or a plastic flower pot.
Resource Management recently initiated a program with its suppliers that shows a video tape of contamination observed when processing their own materials. The video tape is made available to each supplier so they can see first hand what contamination, if any, is being collected from their residential recycling programs. The loads of recyclable materials received at the MRF are also graded based on the level of contamination observed.
A ‘Grade A’ load is relatively free of contamination, while Grades B, C, and D correspond to greater levels of observed contamination. This grading system is easy to understand, just like receiving a report card. This video tape and grading system enables the suppliers to better understand the reduced value of recyclable materials based on observed contamination, and also gives the opportunity for each supplier to determine the type and sources of contamination.
WHERE DO WE GO FROM HERE?
Resource Management has gone so far as to create a list of items that should not be included in a recycling bin. This list was generated from actual observations of non-recyclable materials being delivered to the company’s MRFs.
When it’s all said and done, residential curbside recycling remains a cost-effective and environmentally sound practice. However, residents must be continually reminded by their community regarding what can and cannot be included in their curbside bin. RT
Greg Maxwell is CEO of Resource Management, a Naperville, Illinois-based company that processes and markets recyclable materials.
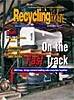
Explore the September 1999 Issue
Check out more from this issue and find your next story to read.
Latest from Recycling Today
- Reconomy brands receive platinum ratings from EcoVadis
- Sortera Technologies ‘owning and operating’ aluminum sorting solutions
- IDTechEx sees electric-powered construction equipment growth
- Global steel output recedes in November
- Fitch Ratings sees reasons for steel optimism in 2025
- P+PB adds new board members
- BlueScope, BHP & Rio Tinto select site for electric smelting furnace pilot plant
- Magnomer joins Canada Plastics Pact