
“While recycling is good for the environment,” according to the U.S. Occupational Safety and Health Administration’s (OSHA’s) website, “it can be dangerous for workers. Certain materials that are recycled or reused, such as scrap metal, electronics, batteries and used oil and other chemicals, have materials that directly pose hazards to workers.”
OSHA continues, “Collection is one of the most dangerous activities in the recycling industry. Tragically, workers have lost their lives due to being backed-over by trucks or struck by oncoming vehicles as they were exiting the trucks they were driving.”
According to the recent fatality report issued by the Solid Waste Association of North America (SWANA), Silver Spring, Maryland, the waste and recycling sectors in the U.S. and Canada recorded 22 deaths in the first month of 2019. Of those, 15 were members of the public who were killed in collisions involving collection vehicles, and eight were operators. In the first 10 days of January 2018, seven fatalities were reported. By the end of the month, that number had increased to 19. January 2019 and January 2018, respectively, hold the highest and second highest number of fatalities the industry has seen in a single month.
Incidents such as these involving collection vehicles come at a cost, according to SWANA’s data: Backing accidents involving only property damage have a minimum average cost of $7,400, while accidents involving injuries have a minimum average cost of $27,558, and accidents that result in fatalities cost $500,000 at
Accidents by nature are unplanned. But by creating strategic plans that include the integration of safety training, education and technologies, significant strides can be made to mitigate or completely avoid future incidents and collisions.
Plan to avoid
A successful safety plan should demonstrate how to avoid problematic situations and provide a detailed description of how to deal with these circumstances should they arise.
Unfortunately, many accidents are caused by human error, but even they can be managed through proper implementation of corrective and preventive safety programs.
“Have a proactive safety program in place, train your team and then train them some more,” labor lawyer John Cruickshank, a partner at Cruickshank and Alaniz, Houston, says. “Maintain the quality of your operators, maintain your equipment and keep detailed maintenance records, and your fleet will be better prepared to mitigate the risks that come with a potential accident.
“Labor law is the intersection between how the law requires an employer to manage its employees and how an employer effectively manages its employees,” he adds.
OSHA standards, Cruickshank says, set the stage for a proactive safety plan in which safety management should include properly maintaining equipment, integrating safety technologies, keeping records and providing frequent and ongoing employee training to mitigate risks and protect a company from a lawsuit.
“A lawsuit avoided is better than a lawsuit won,” Cruickshank says.
“A lawsuit avoided is better than a lawsuit won.” – John Cruickshank, Cruickshank and Alaniz
The reality is, if a company vehicle is involved in an accident, a company should expect to be sued.
SWANA calculates the average price of an accident claim involving a fleet vehicle at between $5,000 and $8,000, depending on location. Regarding workers’ compensation, the average cost of a work-related injury is $4,000 to $6,000.
Many costs are associated with accidents involving vehicles. Indirectly, a company will have to deal with lost production time, time lost in hiring and training a replacement, reduced morale, OSHA penalties, paperwork and more.
Plan to protect
To avoid the potentially insurmountable costs of an accident, a company must first protect itself and its employees. To do this, the first course of action is to identify all health and safety risks and mitigate them. Fleet safety management necessitates understanding the causes of accidents and creating a corrective plan with measurable goals and objectives.
This requires an integrated approach across the spectrum of fleet safety practices and support from the C- level down. Through this corrective plan, driver qualifications, training programs, good-conduct policies, vehicle maintenance, inspection processes and procedures, postaccident management and a reasonably comprehensive plan to adopt and implement safety technologies will mitigate, if not eliminate, employee-related health and safety issues.
In providing a safe work environment, companies must consider adopting safety technology solutions and implementation plans to combat vehicle safety issues throughout the collection and transportation process, according to “Commercial Fleet: Managing the Legal Risks of Vehicle Safety Technologies, A White Paper,” which Cruickshank co-authored with fellow attorney John Phillips. My company, Preco Electronics, sponsored the white paper.
The white paper states that a safety technology integration plan is a “blueprint for managing and improving vehicle safety but also a self-serving document intended for litigation. Its purpose is to demonstrate and persuade a jury that the company made more than reasonable efforts to integrate vehicle safety technologies where it could and made reasonable business necessity decisions where it couldn’t.”
Such plans should recognize important safety technologies, discuss the cost of the technology relative to its impact on safety, provide a comparison of what other companies in the industry are doing and outline a reasonable timeline for integration and retrofitting.
According to the white paper, the plan should be flexible and scalable, with any deviations documented.
Proximity detection technologies that are designed to prevent incidents from causing excessive downtime, injuries and fatalities can be essential for a comprehensive safety program and should be considered in a company’s safety technology integration plan.
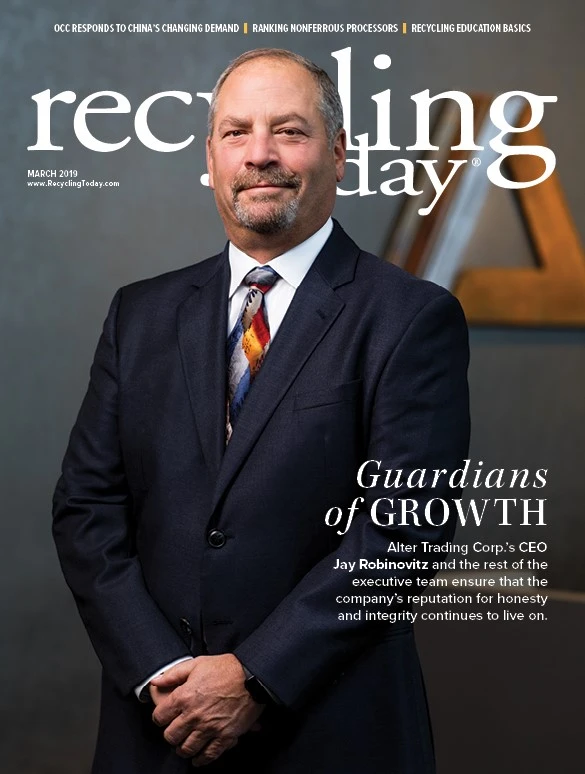
Explore the March 2019 Issue
Check out more from this issue and find your next story to read.
Latest from Recycling Today
- Athens Services terminates contract with San Marino, California
- Partners develop specialty response vehicles for LIB fires
- Sonoco cites OCC shortage for price hike in Europe
- British Steel mill’s future up in the air
- Tomra applies GAINnext AI technology to upgrade wrought aluminum scrap
- Redwood Materials partners with Isuzu Commercial Truck
- The push for more supply
- ReMA PSI Chapter adds 7 members