
Harsco is a well-known company in the steelmaking and ferrous scrap sectors. What might be less well-known is that the company’s history extends back to 1853 and the Harrisburg Car Manufacturing Co., a manufacturer of rail cars. Camp Hill, Pennsylvania-based Harsco Corp. has continually reinvented itself through diversification and acquisition. Its divisions are Clean Earth, which is dedicated to managing specialty hazardous and nonhazardous waste, contaminated soil and dredged material; Harsco Environmental, which has on-site mill and resource recovery services; and Harsco Rail, which focuses on railway track maintenance.
Harsco Environmental is the new name of what was previously the Metals and Minerals division. Bruce Barker, the U.K.-based director of global resource recovery at Harsco Environmental, says, “The new name is really who we have been for a number of years and is more closely aligned with our transformation into a global, market-leading environmental solutions provider. The team at Harsco Environmental is really set on expanding our industrial reach through the application of new environmental technologies and developing eco-friendly products to drive growth for our company and importantly, for our customers.”
The division says it offers solutions that are designed to maximize environmental benefits and return raw materials to production. It has developed a range of byproducts for specialized applications across industry, construction and agriculture using its expertise in minerals.
Barker says Harsco provides scrap management services at more than 150 sites in more than 30 countries. “Our primary involvement within the scrap management sector is directly with the steel mills,” he says. “Scrap management is fundamental to what we do. If somebody already has purchased scrap, we can help them optimize the value they get from it. When a customer generates scrap, we can maximize the conversion of their material into products for reuse internally or externally, depending on the customer’s preference. Importantly, we are not dumping these byproducts into landfills but rather recycling or reusing more than 70 percent of them,” Barker adds.
Barker is a metallurgical engineer with more than 30 years of global experience in the iron, steel and aluminum industries, according to the company. He shares how Harsco Environmental has evolved and where the business segment is heading.
Recycling Today (RT): How has Harsco Environmental evolved over time? How much of the company’s overall business does this segment represent and how does that compare historically?
Bruce Barker (BB): Our service portfolio at Harsco Environmental has expanded over time, with an emphasis on positive environmental impact. Currently, well over 70 percent of our services have a direct or indirect environmental benefit compared to less than 60 percent two years ago. Our business platform helps to reuse and repurpose heavy industries’ residues and minimize the amount of material going to landfills.

Historically, we were known for our “steel mill services,” and our evolution has included pioneering many byproduct recycling technologies that are now regularly used in the industry. Our division within Harsco used to be known for extracting metal from steelmaking slags and then finding solutions for the remaining mineral byproducts.
Previously, our customers’ main requirement was maximized metal recovery; but, today, we are very much focused on increasing the reuse of all metal and mineral units available for recovery. This reflects a general change to improve the efficiency of materials utilization while minimizing the environmental impact of industrial processes. We’ve made significant improvements within our original services portfolio by improving our on-site logistics and base processes. Harsco Environmental offers the widest range of on-site recycling services for the metals industry to maximize their production efficiency while minimizing the environmental impact on their own site and the surrounding communities.
In the past few decades, we’ve used the services business as a springboard to address other byproduct challenges faced by our customers. It’s opened our eyes to the need for new technologies that will address our customers’ desire to improve material utilization while minimizing the environmental impact of industrial operations. Our mission to provide environmental benefits through cost- and material-efficient process enhancements is reflective of the ongoing need by both society and industry for constant improvement in these areas.
RT: How much of your Environmental business does scrap management represent? What services does it include?
BB: While we can’t break out the percentage of our business segments for competitive reasons, we can share that there are seven main services that fall under the traditional scrap management umbrella:
- overall scrap management, which includes scrap quality analysis, loading and tracking;
- baling and shearing;
- coolant scrap production;
- shredding services;
- internal scrap collection;
- oxy cutting and lancing; and
- scrap turnings briquetting.
Harsco is involved in all aspects of scrap handling, processing, usage and tracking. There are two fundamental sources for scrap: external and internal. External scrap is material that a customer buys and brings in via road, rail and water that we help with on their site.
We use our ScrapMaster program on many sites to manage inventory and maximize the cost benefits to our customers when melting these purchased materials. Then there’s internal scrap that requires the collection of different materials from the steel plant site and their preparation for reuse, either internally or externally. This again generates the greatest economic benefit for the steel plant customer from maximizing the use of materials already in their possession.
Harsco Environmental is especially involved with preparing all forms of scrap for reuse, including the recovery of metal from slag. Also, our oxy-cutting and lancing processes allow us to recycle a wide variety of metallics by using fuel gases and oxygen to cut scrap metal of all dimensions and profiles. If there are large, off-spec steel products that are to be recycled, they must be cut into manageable sizes for remelting in the furnace.
Our metal recovery activities even involve breaking the refractory coating off used gas injection lances to recover the embedded steel pipe before cutting it to size for remelting.
All types of internally generated scrap are potential candidates for collection, upgrading and remelting.
A major environmental benefit of on-site scrap recycling is the reduced need to bring in scrap from external sources. This provides an overall cost reduction while decreasing the carbon footprint of the process as less transportation is required.
RT: Can you tell me more about your proprietary software, ScrapMaster, and how mills can benefit from this service?
BB: For steelmakers, better scrap process visibility will optimize scrap usage for benefits in cost and process control. Whether the scrap is sourced externally or internally, our ScrapMaster software system helps us monitor and control the flow of scrap from original receipt through to melting with complete traceability for quality control and cost reduction.
Incoming scrap inspection is used to record any noncompliance for automatic invoicing adjustment. Spectrographic chemical analysis is used to identify scrap contaminants as well as any valuable contained elements for optimization during scrap selection for melting.
All scrap is logged at the weighbridge prior to unloading and storage. The system is used to record the internal scrap generation points for accurate inventory control and yield monitoring within the steel- making process. It also contains records of the material weights handled at each stage and, through GPS satellite tracking, the exact location of the scrap charge basket with submeter accuracy.
Each scrap charge basket is prepared according to a recipe generated from the furnace operations personnel, and every detail of the scrap selected is recorded through each basket layer loaded. GPS tracking monitors the crane operations and exact movements of each scrap basket charged into the furnace. The program allows for monitoring and recording the entire scrap handling history.
Management reports ... help maximize process control and cost savings that are realized through lower purchase costs, improved metal purity and yield and reduced secondary metallurgy treatment costs downstream of melting.
“Least-cost” scrap charge blends facilitate an optimized scrap allocation over the entire melting schedule. Improved quality control in steel melting and decreased furnace power costs are the result. Additional benefits include reduced scrap handling and [operations and maintenance] costs, reduced assets required and improved on-site traffic management and safety conditions. ScrapMaster has been widely deployed at steel mills worldwide and is a valuable part of Harsco’s total scrap management service.
RT: Tell me more about how Harsco is helping mills manage their byproducts. How have your clients been able to benefit from these services?
BB: Our byproduct blending, pelletizing and briquetting processes enable previously landfilled, yet still valuable byproducts, to be recycled into metal production. Most metal, mineral and carbon fines can be reused when properly prepared within our engineered material recovery processes.
Although many granular byproducts can be fed directly into the sinter plant, some cannot be used “as is,” such as extremely fine baghouse dusts or materials high in residual oil or moisture. These materials have traditionally been landfilled as they are difficult to handle and cause high losses during recycling, problematic environmental emissions or inconsistencies in the sinter feed leading to inefficiencies in the sintering process. Increased sinter plant operating costs are the result.
Our blending and micropelletizing process converts the individual byproducts into a single homogenized product for sinter plant use, which eliminates these problems. As individual byproducts are blended together in designed and controlled proportions, the process ensures that a homogenous and consistent feed material is produced. The previously encountered problems associated with sintering these difficult materials are consequently eliminated. Micropelletizing essentially provides six key benefits for iron and steelmakers:
1. minimized amounts of material going to landfill;
2. conversion of multiple byproduct streams into a single homogeneous product for easy use;
3. recovery of previously lost iron, lime, magnesia and carbon units;
4. replacement of new raw material purchases by using recycled byproduct materials;
5. improvement in sinter plant productivity and thereby lowered sinter plant costs; and
6. upgraded environmental operating status of the sinter plant.
The micropelletizing process starts with a detailed physical and chemical characterization of all materials. Blast furnace (BF) and basic oxygen furnace (BOF) slurry dewatering and micron-sized dust handling technologies are combined with engineered product recipes to blend and micropelletize the byproducts into a homogeneous mix for sinter plant feed. The finished product is supplied according to the customer’s strict physical and chemical specifications. The entire micropelletizing process is controlled to minimize the variation in product quality and chemical analysis and maximize the value captured from the recycled materials.
While micropelletizing is used to consume a variety of mineral, metal and carbon-containing byproducts, on-site briquetting is mainly used to recover metals in the steelmaking process. When high iron content byproducts are briquetted for use in the BOF, they are converted directly into liquid steel thereby bypassing the sinter plant and blast furnace processes. This naturally leads to significant savings in the overall steelmaking cycle. By working directly with the steel plant operations technology personnel, each Harsco briquetting plant generates a unique, customized briquette chemistry that we manufacture on-site.
When using these briquettes as a coolant in the BOF or as a source of iron and carbon in the blast furnace, each steel plant generates significant raw material savings and environmental improvements. This is in addition to avoiding disposal of materials that still contain the valuable chemical units needed in the iron and steelmaking process.
Harsco Environmental has designed and built numerous agglomeration plants around the world for byproduct processing, using either the micropelletizing or briquetting processes according to the end-use requirements of the customer. A recent contract included both on-site micropelletizing and briquetting plants that were designed, installed and operated by Harsco Environmental. We have since been asked to increase the production capacity as these plants continue to provide significant operational savings to the customer.
These on-site byproduct processing plants improve the material utilization efficiency in the steel plant and the environmental impact of the operation. By providing specialized byproduct material handling techniques, along with our extensive history and expertise in engineered material recovery product and process designs, Harsco maximizes the conversion of our steel customer’s byproducts into process savings within a sustainable approach to environmental stewardship.
RT: How does Harsco’s acquisition of Clean Earth and Stericycle’s Environmental Solutions Business complement its Environmental service portfolio? What other areas of Harsco Environmental is the company looking to shore up through M&A activity? What organic growth opportunities exist for Harsco Environmental?
BB: Harsco’s acquisition of Stericycle’s Environmental Solutions business (ESOL) earlier [in 2020] was a significant step forward in Harsco’s ongoing transformation into a global, single-thesis environmental solutions platform. As a result of that acquisition, as well as the earlier acquisition of Clean Earth, more than 85 percent of the company’s total revenue is now expected to come from environmental solutions and services. The addition of ESOL added a highly complementary, market-leading waste management portfolio to our already strong business, significantly expanding our scale and reach.
We are focused on resuming our growth within Harsco Environmental and on integrating our recent ESOL acquisition into Clean Earth. With more than $1 billion invested in two transactions [since late 2019], we have said that we most likely will hit the “pause button” on any additional M&A in 2021.
That said, our Altek acquisition [in 2018] continues to provide synergistic opportunities for Harsco between the steel and aluminum sectors. (Altek is a U.K.-based manufacturer of products that enable aluminum producers and recyclers to manage and extract value from waste streams, reduce waste generation and improve operating productivity.)
As we improve our traditional processes and expand our global footprint, we continue to find opportunities for organic growth. In the meantime, we are proving to investors that with our single thesis platform, we remain steadfast in our commitment to deliver enhanced value to all parties.
Bruce Barker is the director of global resource recovery at Harsco Environmental, www.harsco.com/harscoenvironmental.
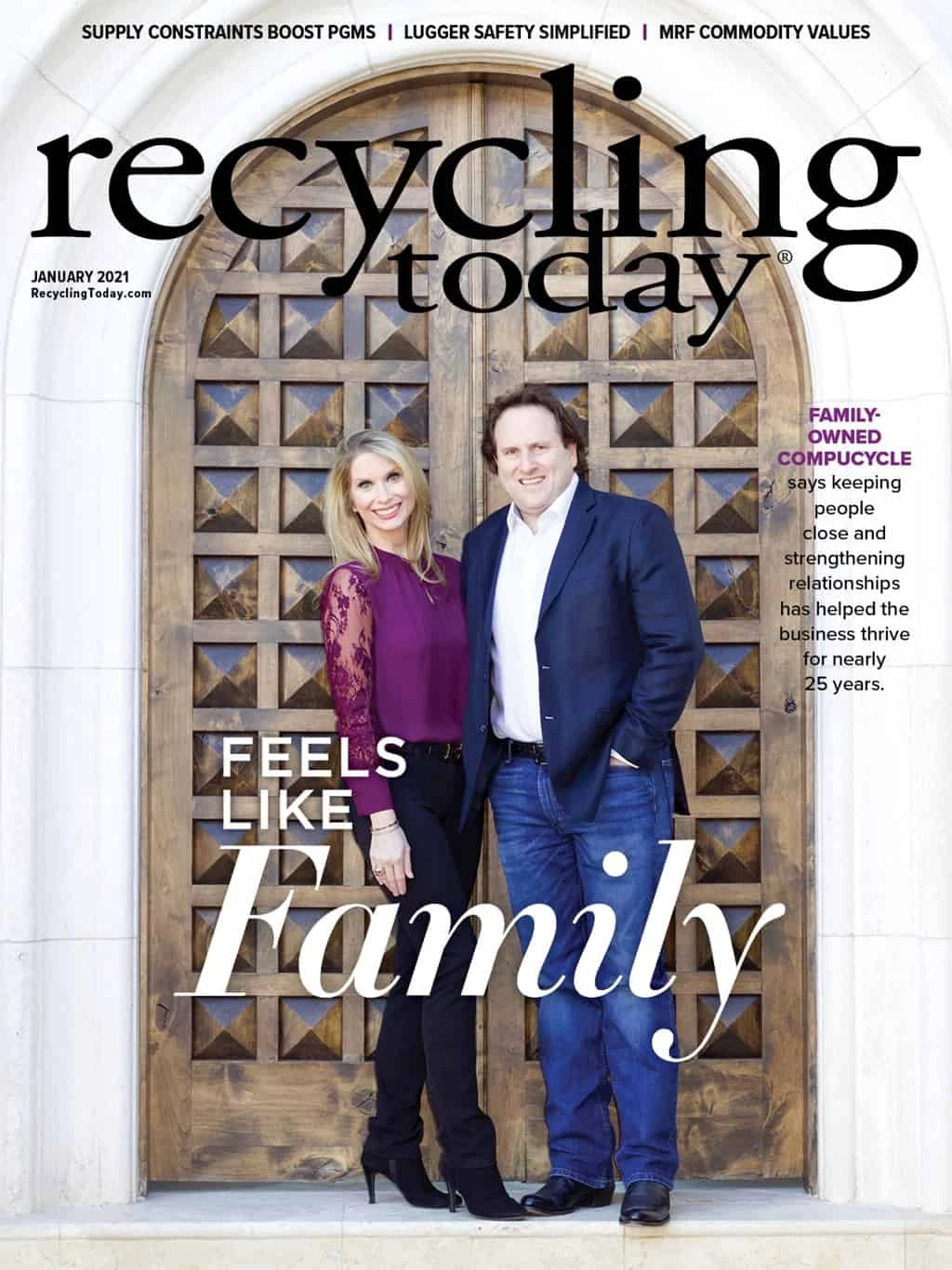
Explore the January 2021 Issue
Check out more from this issue and find your next story to read.
Latest from Recycling Today
- AF&PA report shows decrease in packaging paper shipments
- GreenMantra names new CEO
- Agilyx says Styrenyx technology reduces carbon footprint in styrene production
- SABIC’s Trucircle PE used for greenhouse roofing
- Hydro to add wire rod casthouse in Norway
- Hindalco to invest in copper, aluminum business in India
- Recycled steel price crosses $500 per ton threshold
- Smithers report looks at PCR plastic’s near-term prospects